Managing Your Assets 06 - Managing Equipment Failures
Summary
TLDRThis video focuses on the importance of effectively managing equipment failures and downtime, emphasizing the value of remanufacturing and repair services. It highlights the benefits of using Rockwellโs remanufacturing process, which restores faulty components to like-new or better conditions, offering cost savings and extended warranties. Options like expedited repairs via a hub or priority exchanges are also discussed to minimize downtime. The video stresses the importance of trusting the repair process to ensure equipment reliability, with features like real-time tracking and analytics to manage and understand equipment failure patterns.
Takeaways
- ๐ Equipment failures are inevitable, and managing downtime efficiently is critical to minimizing costs.
- ๐ Extended downtime can be more costly than the parts being replaced, making it crucial to trust the reliability of replacement parts.
- ๐ Remanufacturing and repair services allow businesses to capitalize on their previous investments by restoring parts to like-new or better condition.
- ๐ Rockwellโs remanufacturing process ensures that repaired parts are thoroughly tested and upgraded, often including firmware and safety performance improvements.
- ๐ Remanufactured parts from Rockwell are often 50% cheaper than buying new parts and come with a one-year warranty.
- ๐ There are three repair service options: Economy Repair (2-week turnaround), Hub Service (3-5 day turnaround), and Priority Exchange (next-day shipping).
- ๐ The Hub Service allows businesses to bypass repair time by sending in a failed part and receiving a pre-repaired part, with an 18-month warranty.
- ๐ Priority Exchange guarantees next-day delivery of a working part, with a 24-month warranty, ensuring fast repairs for critical components.
- ๐ Tracking repairs through the 'My Equipment' page makes it easy to monitor the status of orders and understand where parts are in the repair process.
- ๐ The 'My Equipment' page also provides analytics on common failures, helping businesses identify frequent issues and improve asset management.
Q & A
Why is managing equipment failures important?
-Managing equipment failures is crucial because downtime can be costly. If a replacement part doesn't work, it extends downtime, which becomes more expensive than the cost of the component itself.
What role does remanufacturing and repair play in equipment management?
-Remanufacturing and repair allow businesses to capitalize on parts they've already purchased. By restoring parts to like-new or better conditions, they can save money while ensuring that the equipment remains reliable and functional.
How does Rockwell ensure the quality of its repaired parts?
-Rockwell has in-depth knowledge of the parts they manufacture, ensuring repairs meet high standards. Their repair process includes checking for weak spots, upgrading firmware, and implementing changes that improve performance and safety.
What are the advantages of using Rockwellโs remanufacturing and repair services?
-The primary advantages include cost savings (up to 50% less than buying new parts), improved parts with the latest upgrades and firmware, and a one-year warranty similar to new products.
What is the typical turnaround time for Rockwellโs economy repair service?
-The economy repair service typically takes about two weeks, ensuring that the repaired part is like-new or better, with all necessary updates applied.
What is the benefit of using Rockwell's repair hub service?
-The repair hub allows businesses to receive pre-repaired parts within 3-5 days, eliminating the wait time for repairs, while still offering an 18-month warranty.
How does Rockwell handle urgent part replacements?
-For critical parts, Rockwell offers a priority exchange service. This involves next-day shipping for the part, ensuring minimal downtime, along with a 24-month warranty on the repaired component.
How can customers track their repairs with Rockwell?
-Customers can track their repairs through Rockwell's online system, which provides real-time updates on the status of their parts throughout the repair process.
What insights can Rockwellโs repair tracking system provide?
-The repair tracking system can offer valuable analytics on commonly failed parts, allowing businesses to identify recurring issues and better manage their assets.
Why is it important to trust the repair process when dealing with equipment failures?
-Trusting the repair process is essential because a failed repair can lead to further downtime. By ensuring that repairs are done correctly and efficiently, businesses minimize the risk of ongoing failures and avoid extended operational disruptions.
Outlines
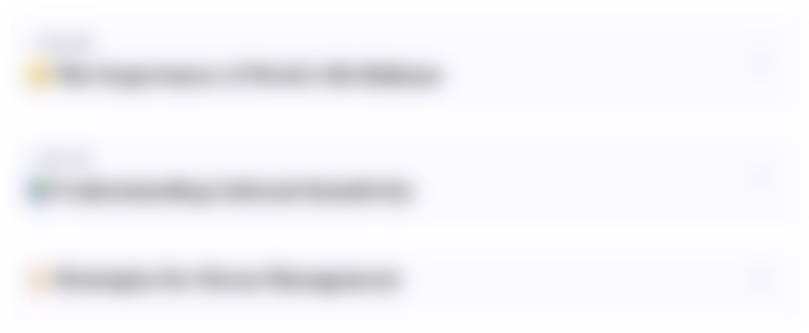
This section is available to paid users only. Please upgrade to access this part.
Upgrade NowMindmap
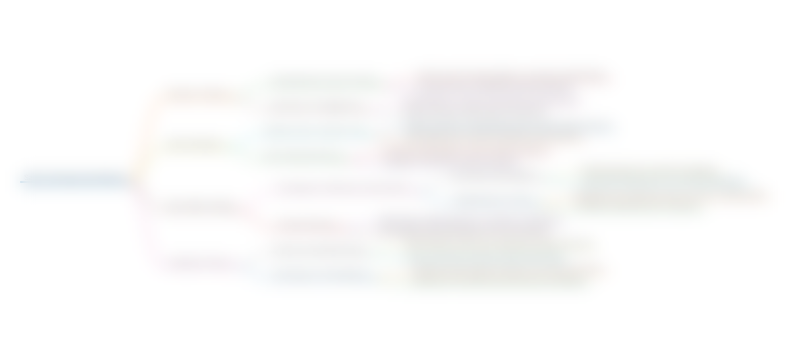
This section is available to paid users only. Please upgrade to access this part.
Upgrade NowKeywords
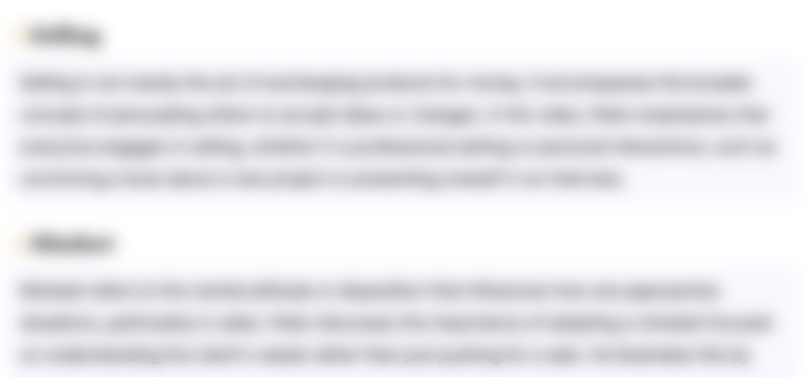
This section is available to paid users only. Please upgrade to access this part.
Upgrade NowHighlights
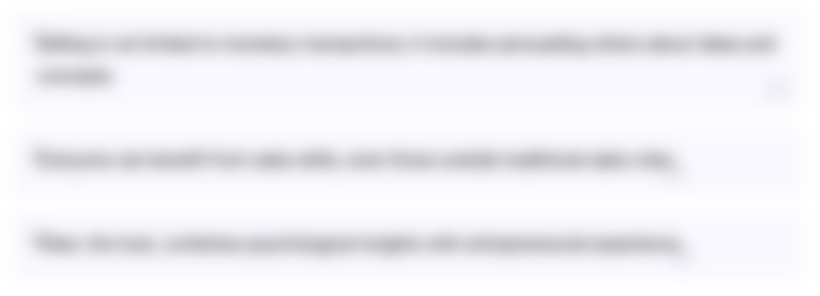
This section is available to paid users only. Please upgrade to access this part.
Upgrade NowTranscripts
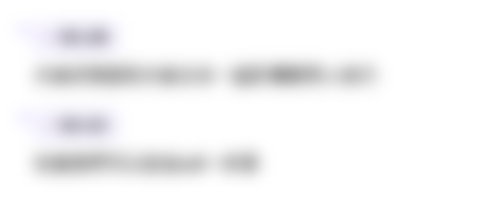
This section is available to paid users only. Please upgrade to access this part.
Upgrade NowBrowse More Related Video
5.0 / 5 (0 votes)