3 5s Orientation Part 2
Summary
TLDRThe training video outlines the implementation of the 5S methodology (Sort, Set in Order, Shine, Standardize, Sustain) in a workplace setting. It emphasizes the importance of self-discipline, responsibility, and maintaining a clean, organized workspace to ensure consistent, high-quality results. Employees are encouraged to follow standardized guidelines, akin to following a recipe, to achieve optimal outcomes. Practical tasks include organizing and cleaning workstations, using before, during, and after photos to track progress. The system also incorporates regular inspections, incentives, and an award system to motivate employees and reinforce the standards of 5S.
Takeaways
- 😀 5S methodology involves five key principles: Sort, Set in Order, Shine, Standardize, and Sustain, aimed at creating a clean, organized, and efficient workspace.
- 😀 Employees are encouraged to take responsibility for cleaning and organizing their own workstations to ensure a cleaner and more efficient workspace.
- 😀 Regular inspections and maintenance of tools, machines, and equipment are essential to prevent contamination and ensure proper functioning in the workplace.
- 😀 The process of Standardizing involves creating clear guidelines and instructions to ensure uniformity and consistency in work processes and product quality.
- 😀 Shitsuke (self-discipline) is a core principle of the 5S methodology, encouraging employees to maintain high standards without needing constant reminders.
- 😀 Supervisors and 5S champions play an important role in ensuring 5S principles are consistently followed and in conducting inspections to identify areas for improvement.
- 😀 An awarding system can be implemented to motivate employees by recognizing and rewarding those who adhere to 5S principles and maintain a clean, organized workspace.
- 😀 Practical daily applications of the 5S methodology include documenting and uploading photos of employees' progress in maintaining their work areas using tools like Google Drive.
- 😀 The 'before, during, and after' approach helps demonstrate the effectiveness of 5S in organizing and cleaning workstations and encourages continuous improvement.
- 😀 5S principles are not only applicable in the workplace but can also be implemented at home, improving personal responsibility and the overall organization of one's living space.
Q & A
What is the main purpose of the '5S' system in the workplace?
-The main purpose of the '5S' system is to improve efficiency, cleanliness, and organization in the workplace by focusing on sorting, organizing, cleaning, standardizing, and maintaining self-discipline.
What does the first 'S' in the '5S' system stand for, and what is its importance?
-The first 'S' stands for 'Seiri,' which means 'Sort.' It involves removing unnecessary items from the workspace to ensure that only essential tools and materials are kept, leading to a cleaner and more efficient environment.
How does 'Seiton' (the second 'S') contribute to workplace efficiency?
-'Seiton' means 'Set in order.' This step ensures that all tools and materials are organized and easily accessible, minimizing time wasted looking for things and improving overall workflow.
What role does 'Seiso' (the third 'S') play in workplace cleanliness?
-'Seiso' means 'Shine' and focuses on regular cleaning and maintenance of tools, machines, and the workspace. This ensures that the workplace remains tidy, safe, and conducive to efficient work.
Why is standardization (the fourth 'S') important in the 5S system?
-Standardization ('Seiketsu') is crucial because it establishes clear guidelines and procedures that ensure all employees follow the same practices for cleanliness, organization, and maintenance, leading to consistent results across the workplace.
What does the final 'S' (Shitsuke) represent, and how is it implemented?
-The final 'S' stands for 'Shitsuke,' meaning 'Sustain.' It emphasizes self-discipline and the commitment to maintaining the 5S practices consistently without needing constant reminders or supervision.
How does the 5S system encourage employee involvement?
-The 5S system encourages employee involvement through practices like self-discipline and regular inspections, where employees are responsible for maintaining their own workstations and following the guidelines set by the company.
How does the concept of self-discipline ('Shitsuke') apply to employees in the company?
-Self-discipline ('Shitsuke') applies to employees by requiring them to consistently follow 5S practices, such as wearing the proper uniform, keeping workstations organized, and ensuring cleanliness, all without being reminded by supervisors.
What is the purpose of the '5S committee' and '5S champion' within a company?
-The '5S committee' and '5S champion' are responsible for monitoring the implementation of 5S practices within the workplace. They conduct inspections, identify areas for improvement, and ensure that the system is being followed consistently.
What role does the 'awarding system' play in motivating employees to adhere to 5S practices?
-The 'awarding system' provides recognition and incentives for employees who consistently follow 5S practices. This serves as a motivation for them to take responsibility and contribute to maintaining a clean and organized workplace.
Outlines
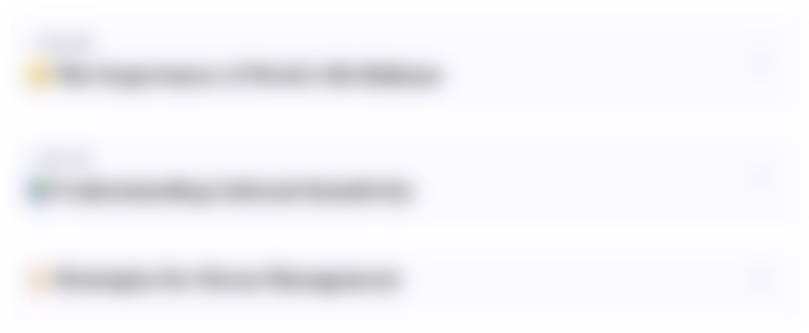
This section is available to paid users only. Please upgrade to access this part.
Upgrade NowMindmap
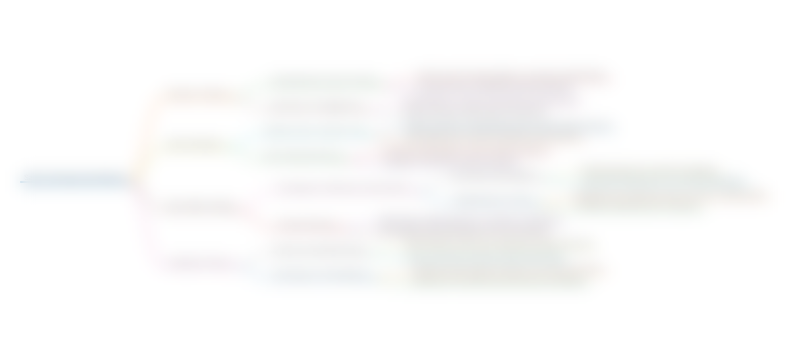
This section is available to paid users only. Please upgrade to access this part.
Upgrade NowKeywords
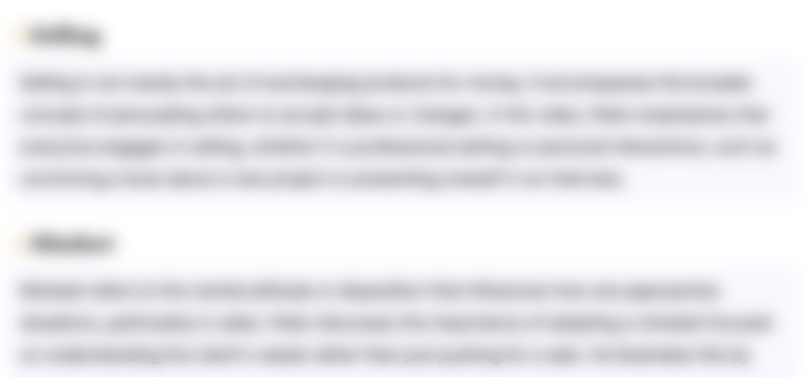
This section is available to paid users only. Please upgrade to access this part.
Upgrade NowHighlights
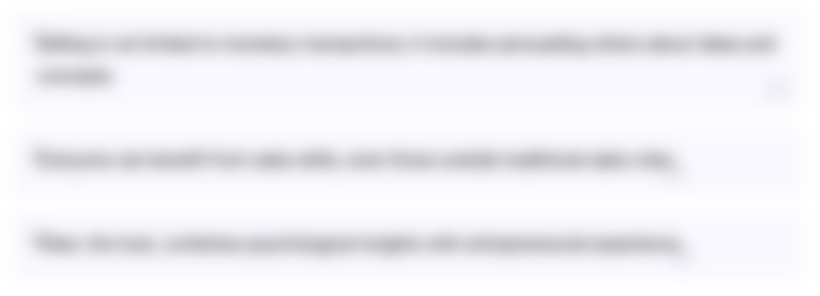
This section is available to paid users only. Please upgrade to access this part.
Upgrade NowTranscripts
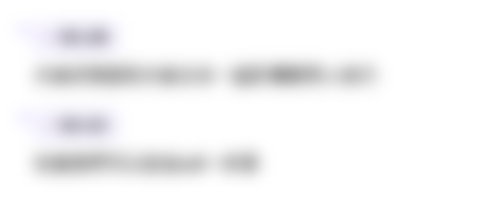
This section is available to paid users only. Please upgrade to access this part.
Upgrade Now5.0 / 5 (0 votes)