Harga Pokok Produk Bersama & Produk Samping Dlm Akuntansi Biaya
Summary
TLDRThis video discusses the concept of joint production costs and by-products in accounting. It covers the characteristics of joint products, their shared production costs, and how to allocate these costs using various methods, such as relative sales value, physical units, and average cost methods. Additionally, the video explains how to handle by-products, which are produced alongside primary products but have lower sales value. Real-world examples are used to illustrate the calculations and decision-making processes involved in cost allocation. The goal is to provide a comprehensive understanding of joint production and its financial implications for businesses.
Takeaways
- π Joint products are two or more products produced simultaneously from the same production process, sharing common raw materials and processes.
- π By-products are secondary products generated alongside primary products but typically with lower selling value and less importance in production.
- π Joint costs refer to the costs incurred during the production of joint products, which need to be allocated between the products.
- π The split-off point is the stage in production where joint products can be separated and identified as distinct products.
- π The sales value relative method allocates joint costs based on the relative sales value of each product.
- π The physical units method allocates joint costs based on the physical quantities of the products (e.g., weight or volume).
- π The average cost method allocates joint costs based on the average cost per unit produced across all products.
- π The weighted average method allocates joint costs using the relative weight of each product in the total production output.
- π The cost allocation must consider both the direct and indirect costs associated with the production of joint products.
- π Product pricing and cost allocation methods directly impact the profitability and cost structure of each product in joint production scenarios.
- π The treatment of by-products involves allocating a portion of the joint costs to the primary product while recognizing the secondary product's lower selling price.
Q & A
What is the definition of joint costs in manufacturing?
-Joint costs are overhead costs that are incurred during the production of multiple products that are produced simultaneously from the same raw materials or processes. These costs must be allocated among the various products produced.
What is meant by 'split-off point' in the context of joint products?
-The split-off point refers to the stage in the production process where joint products become distinct and can be separated from each other, allowing them to be identified and sold individually.
What is the difference between a main product and a by-product?
-A main product is the primary focus of production, typically with a higher selling price, while a by-product is produced alongside the main product but has a lower selling price and is not the primary goal of production.
How is cost allocation determined when using the relative sales value method?
-In the relative sales value method, joint costs are allocated to products based on their proportionate share of total sales value. The sales value of each product is calculated by multiplying the unit price by the quantity produced, and the total cost is distributed accordingly.
What role does the quantity and sales price of each product play in cost allocation?
-The quantity and sales price of each product help determine its share of the total joint cost. Products with higher sales prices and quantities typically bear a larger portion of the joint costs.
What are some characteristics of by-products?
-By-products are secondary products with a relatively low sales value compared to the main product. They are produced in smaller quantities and may require additional processing. By-products are not the primary focus of production.
What are the methods used to allocate joint costs in accounting?
-The four methods for allocating joint costs are: (1) relative sales value method, (2) physical units method, (3) average cost per unit method, and (4) weighted average cost method.
How does the physical units method work in joint cost allocation?
-In the physical units method, joint costs are allocated based on the physical quantities of each product produced, such as weight, volume, or number of units, ensuring the allocation reflects the proportion of each product's physical output.
Why is the allocation of joint costs important in management accounting?
-Allocating joint costs accurately is crucial for determining the profitability of each product, making informed pricing decisions, and ensuring that financial reporting reflects the true cost structure of the manufacturing process.
What is the impact of the split-off point on cost allocation?
-The split-off point is critical in cost allocation because it is the stage where products become separable. The allocation of joint costs is done based on the value of each product at the split-off point, and further costs incurred after this stage must be considered separately.
Outlines
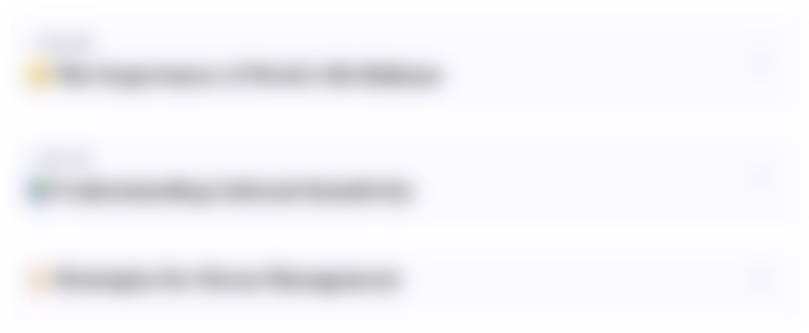
This section is available to paid users only. Please upgrade to access this part.
Upgrade NowMindmap
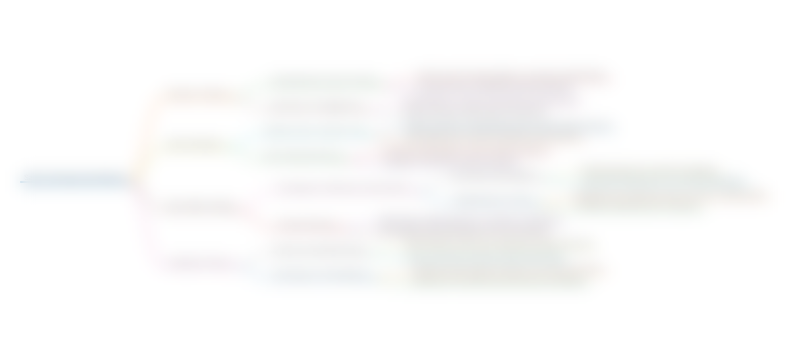
This section is available to paid users only. Please upgrade to access this part.
Upgrade NowKeywords
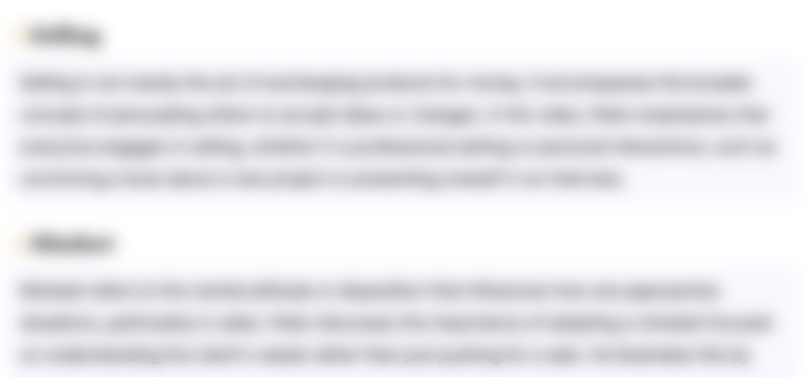
This section is available to paid users only. Please upgrade to access this part.
Upgrade NowHighlights
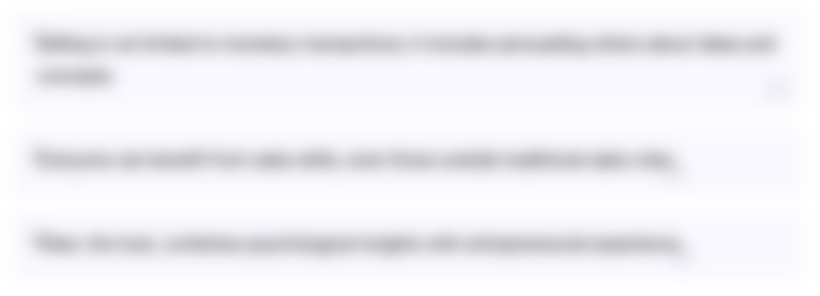
This section is available to paid users only. Please upgrade to access this part.
Upgrade NowTranscripts
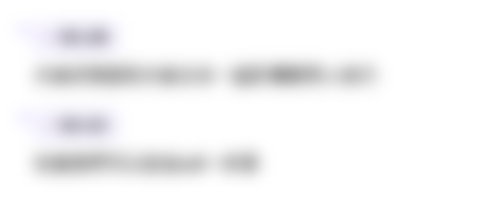
This section is available to paid users only. Please upgrade to access this part.
Upgrade NowBrowse More Related Video

Perhitungan Biaya Produk Sampingan (By Product) | Akuntansi Biaya

VIDEO TERBAIK - PENYUSUNAN LAPORAN BIAYA PRODUKSI - Metode Rata Rata dan FIFO - AKUNTANSI BIAYA

Biaya Tenaga Kerja Dlm Akuntansi Biaya

Biaya Produksi (Bagian 1) : Konsep Biaya dalam Ekonomi

Microeconomics Unit 3 COMPLETE Summary - Production & Perfect Competition

Biaya Produksi (Bagian 5) : Produksi dengan 2 Output
5.0 / 5 (0 votes)