Recycling Failed 3D Prints with a DIY Filament Extruder: Artme3D
Summary
TLDRВ этом видео Stefan из CNC Kitchen рассматривает вопрос рециклинга отходов от 3D-печати, демонстрируя制作过程DIY экструзора филаментов от компании Artme. Он сравнивает его с профессиональными решениями, которые стоят в 10 раз дороже. Artme3D Mk2 - это открытая система, позволяющая пользователям создавать и восстанавливать филаменты из отходов. В видео подробно описывается процесс сборки экструзора, его функционирование и результаты экспериментов с использованием экструзора для создания новых филаментов из утилизируемого пластика. Stefan также делится своими впечатлениями о продукте и его потенциале для хобби и малого бизнеса.
Takeaways
- 🚀 В видео рассматривается возможность рециклинга отходов от 3D-печати, превращая их в новые пластины для дальнейшего использования.
- 🛠️ Введение в DIY-набор на базе экструдера филаментов Artme3D Mk2, который был куплен за 600 долларов и сравнивается с профессиональными решениями, стоимостью в 10 раз больше.
- 👨🔧 Автор Stefan из CNC Kitchen собирает экструдер из комплекта, включая настройку и прокачку всех компонентов самостоятельно.
- 🔩 Комплект включает в себя индивидуальные компоненты, а также требует распечатки пластиковых деталей 3D-принтером.
- 🔥 Процесс сборки охватывает установку барабана, нагревного блока, электроники, мотора и устройства для сушки филаментов.
- 🌡️ Экструдеры обычно состоят из винтовой системы, двигателя с высокой крутящейmoment of inertia, нагреваемого ствола и сопла для производства филамента.
- 📦 Artme3D MK2 предлагает простой в сборке и настройке дизайн, включая инновационные функции, такие как вибрационный фильтр и устройству для измерения диаметра филамента.
- 🔄 Применяется специальная лента для фильтрации и удаления загрязнений из пластика, что улучшает качество производимого филамента.
- 🌿 Рассмотрены экологические и экономические преимущества рециклинга отходов 3D-печати, а также возможность использования экструдера для создания новых продуктов.
- 🎨 Автор демонстрирует процесс рециклинга отходов, включая измельчение, выдержку, выравнивание и натяжку филамента на bobbin.
- 📏 В ходе испытаний полученный филамент проходит проверку на качество печати, демонстрируя хорошую работоспособность и отсутствие заметных неправильностей в диаметре.
- 🔧 Автор отмечает некоторые неидеальности, такие как требование дополнительной настройки и периодической уход за фильтром, но в целом остается доволен результатом и рекомендует экструдер для любителей и создателей.
Q & A
3D принтерами обычно генерируется какая отходная материал?
-3D принтерами генерируется отходная материаль в виде неудачных печатей, прототипов и отходов мультицветных печатей, которые также называются "пластиком".
Какой тип филамента можно переработать с помощью экструдера?
-С помощью экструдера можно переработать отходы мультицветных печатей, прототипы и даже "пластик", то есть отходы из промежуточных цветов.
Какой компании принадлежит разработанный экструдер?
-Экструдер разработан компанией Artme.
Какой тип ступицы используется в экструдере Artme для подачи материала?
-В экструдере Artme используется специально обработанная ступиця, которая обеспечивает более эффективное подачу и экструзию свернутых 3D-печатей.
Какой тип филамента экструдируется на Artme3D Mk2?
-Artme3D Mk2 экструдирует филамент из ПЛA, который может быть произведен из отходов, таких как свернутые 3D-печати.
Какой средний потребляемый мощностью экструдер во время работы?
-В среднем экструдер потребляет около 60Вт электроэнергии во время работы.
Какой размер филамента обычно экструдуется с помощью Artme3D Mk2?
-Обычным размером экструдуемого филамента является 1.75 мм.
Как долго занимает сверка всех компонентов экструдера Artme3D Mk2?
-Сверка всех компонентов экструдера Artme3D Mk2 занимает около 50 часов.
Какой дополнительный компонент не входит в комплект экструдера и должен быть куплен отдельно?
-Комплект экструдера не включает в себя 24В блок питания, который нужно отдельно приобрести.
Какой материал используется для изготовления корпуса экструдера?
-Для изготовления корпуса экструдера используются пластиковые детали, напечатанные на 3D-принтере.
Какой тип фильтра используется для очистки отходов от загрязнений при экструсии?
-Для очистки отходов от загрязнений используется фильтр растаяжки с проволочным сетчатым покрытием с отверстиями меньшими, чем диаметр насадки 3D-принтера.
Какие преимущества имеет экструдер Artme3D Mk2 перед другими DIY-решениями?
-Экструдер Artme3D Mk2 имеет преимущества в удобстве сборки, доступности компонентов, более эффективной работе специальной ступицы для подачи материала и открытости исходного кода, что позволяет пользователям внести изменения и улучшения.
Outlines
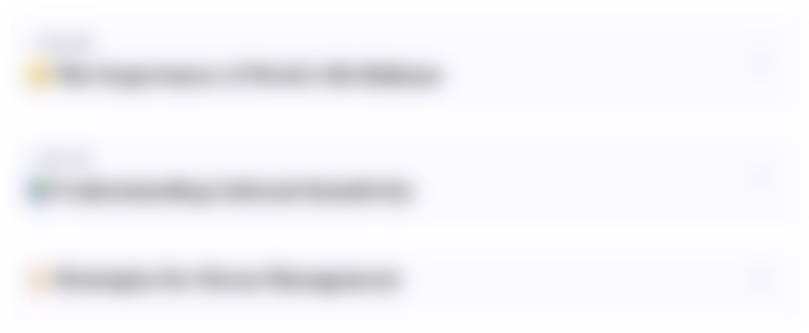
This section is available to paid users only. Please upgrade to access this part.
Upgrade NowMindmap
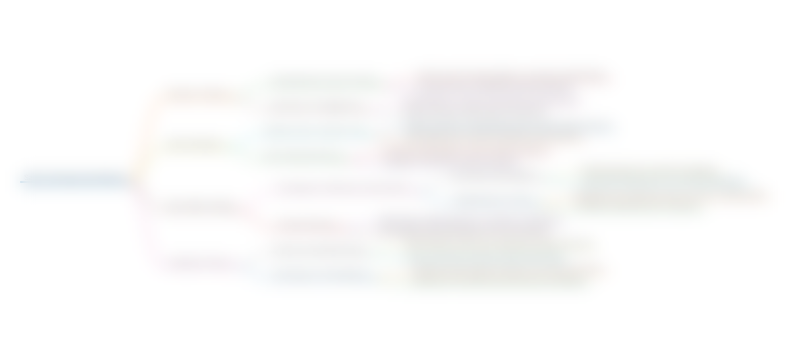
This section is available to paid users only. Please upgrade to access this part.
Upgrade NowKeywords
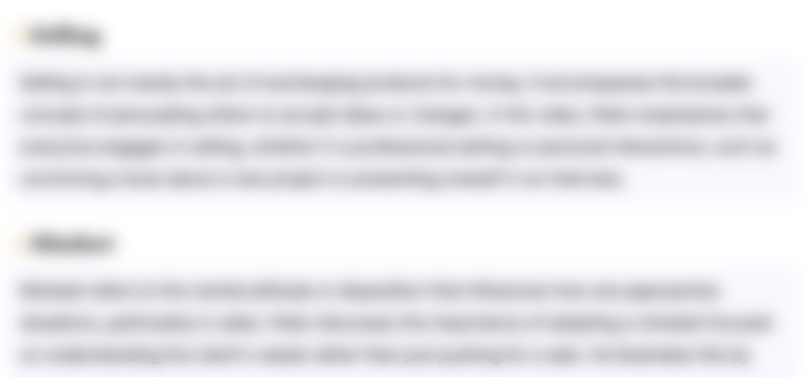
This section is available to paid users only. Please upgrade to access this part.
Upgrade NowHighlights
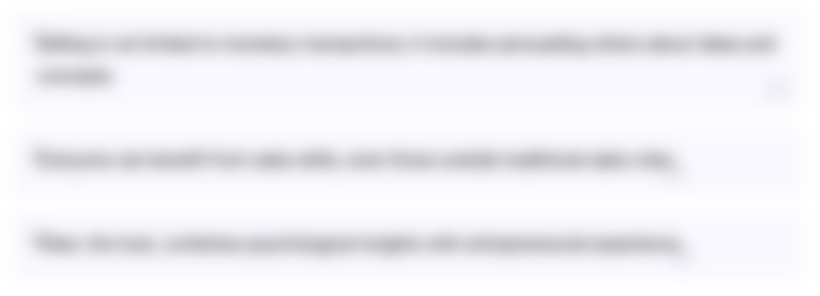
This section is available to paid users only. Please upgrade to access this part.
Upgrade NowTranscripts
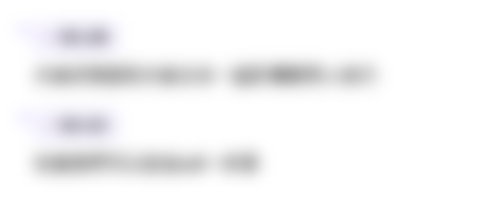
This section is available to paid users only. Please upgrade to access this part.
Upgrade NowBrowse More Related Video

Новая квартира от ПИК в Москве за 15 миллионов. Тест-драйв.
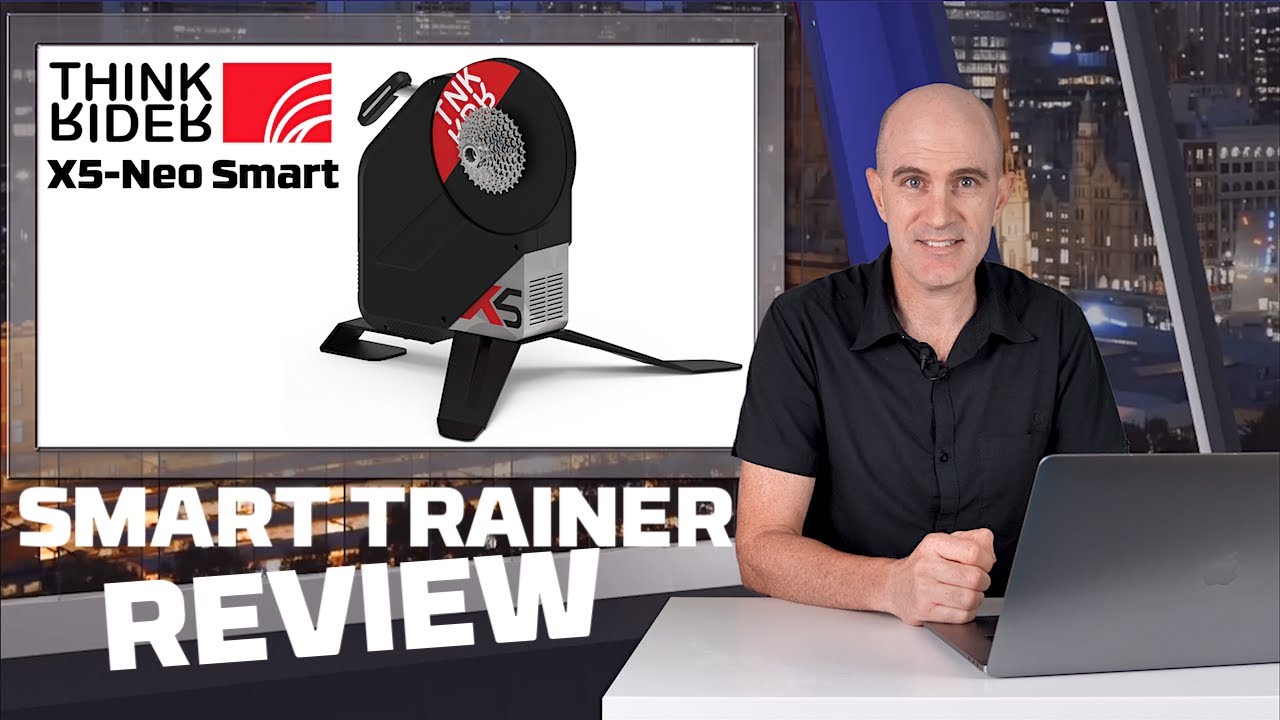
ThinkRider X5-Neo Smart Cycle Trainer: Details // Ride Review

9. Співіснування управлінських культур у великій організації.
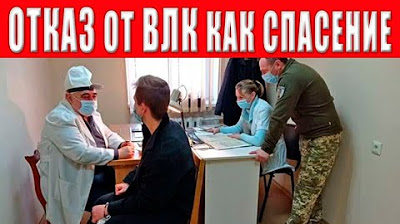
Последствия отказа от прохождения ВЛК - тюремный срок, огромный штраф! Что решил суд?
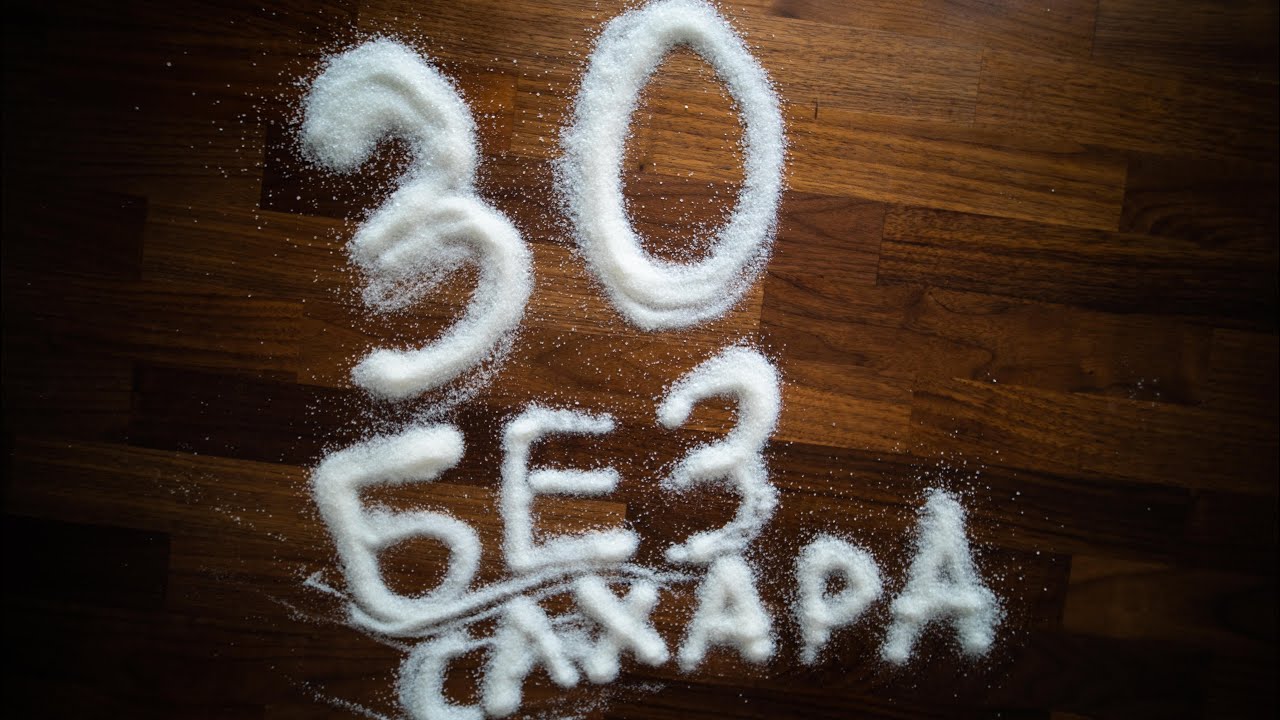
Я отказался от сахара на 30 дней

Allophone - Varianten von Phonemen
5.0 / 5 (0 votes)