Multi-Warehouse Management: Solution (part 2)
Summary
TLDRIn this advanced use case, Michael explores strategies for managing inventory within a retail supply chain. He presents three approaches: a full push strategy, a full pull strategy, and a semi-automated replenishment system. The video covers how to configure these strategies using a system like ADO, including setting up warehouses, creating purchase orders, managing transit locations, and automating stock replenishment. Michael emphasizes the importance of tracking inventory movements, implementing reordering rules, and using push rules for efficient store restocking. The session concludes with recommendations for implementing these systems gradually, ensuring traceability and flexibility in operations.
Takeaways
- 😀 The use case discussed involves optimizing supply chain management in the retail industry with a focus on purchasing, distribution, and stock replenishment strategies.
- 😀 Superstar Supply Chain operates with distribution centers, stores, and suppliers, using a mix of push and pull strategies to manage stock levels and ensure product availability.
- 😀 A push strategy involves forecasting demand and pushing products from the supply chain to the stores, while a pull strategy is demand-driven, starting with customer requests and moving backward.
- 😀 Decoupling points are critical where the push and pull strategies meet, and buffer stock is needed to facilitate these transitions within the supply chain.
- 😀 In ADO, warehouses are used to represent physical locations in the supply chain, and purchase orders, receipts, and outbound operations track the movement of goods.
- 😀 For the push strategy, a manual purchase order is placed to buy products, which are received into a distribution center before being dispatched to stores via transit locations.
- 😀 The process involves multiple steps including manual order creation, receipt validation, and dispatching products to stores using custom push rules that automatically create receipts at destination warehouses.
- 😀 Automated replenishment is another approach where reordering rules maintain stock levels across different locations. These rules can be automated to avoid manual intervention in future replenishments.
- 😀 Manual replenishment gives flexibility to adjust reordering based on current stock levels, allowing for better control over ordering and restocking decisions.
- 😀 Each supply chain location, such as the distribution center and stores, can be configured with its own resupply route, either manual or automated, to streamline inventory management and ensure timely restocking.
- 😀 It is recommended to implement the strategy step-by-step, starting with manual operations, then applying routing rules, and later implementing reordering rules for a more structured and scalable solution.
Q & A
What is the core business logic behind the supply chain discussed in the script?
-The supply chain in the script is based on a typical retail industry model, with a distribution center at the core. The distribution center handles purchasing, unloading supplier trucks, and redistributing products to stores, which aim to maintain stock levels and restock shelves daily. The strategy is focused on maintaining stock at various points across the chain, from suppliers to customers.
What is the difference between a full push strategy and a full pull strategy in supply chain management?
-A full push strategy is forecast-driven, where products are pushed from the supply chain towards customers, based on predictions. In contrast, a full pull strategy is demand-driven, starting with customer requests and moving backwards in the supply chain to fulfill those needs. Typically, companies use a mix of both strategies, referred to as coupling points.
What are coupling points in the context of supply chain strategies?
-Coupling points are areas where both push and pull strategies meet in the supply chain. These points require buffer stock and typically use reordering rules to trigger and extend the pull strategy down the chain.
How are reordering rules used in supply chain management?
-Reordering rules are used to trigger resupply actions at different stock points in the supply chain. They help maintain minimum stock levels and manage the movement of goods based on predefined quantities and demand forecasts.
What is the purpose of creating sub-transit locations in the system?
-Sub-transit locations are created to differentiate between various destinations within the supply chain. These locations help track goods in transit between different warehouses and provide visibility, making it easier for operators to identify where products are headed.
What role do automated replenishments play in the supply chain?
-Automated replenishments use reordering rules to maintain adequate stock levels at different locations. They help ensure products are reordered automatically based on forecasted quantities, which simplifies inventory management.
What is the purpose of using the new operation type, 'intervals operation', in the system?
-The 'intervals operation' is used to differentiate internal transfers within the supply chain from customer deliveries. This distinction helps in better tracking and organizing operations, ensuring smoother inventory management and visibility.
How does the full push strategy work in the system?
-In a full push strategy, products are purchased and received at the distribution center. The system then uses a dispatch operation to send the goods to transit locations and stores, triggering receipts through push rules that automatically create inventory entries at the destination warehouses.
What is the significance of the replenishment rules for each stock point?
-Replenishment rules are vital for ensuring that stock levels are maintained according to the needs of each stock point (e.g., distribution center, stores). They define minimum and maximum stock levels and automate the reordering process to avoid stockouts or overstocking.
What are the advantages of using manual versus automated replenishment rules?
-Manual replenishment rules offer flexibility, allowing users to adjust replenishment based on real-time needs or specific orders. Automated replenishment rules simplify inventory management by automatically ordering goods based on forecasted demand and predefined criteria, reducing human error and saving time.
Outlines
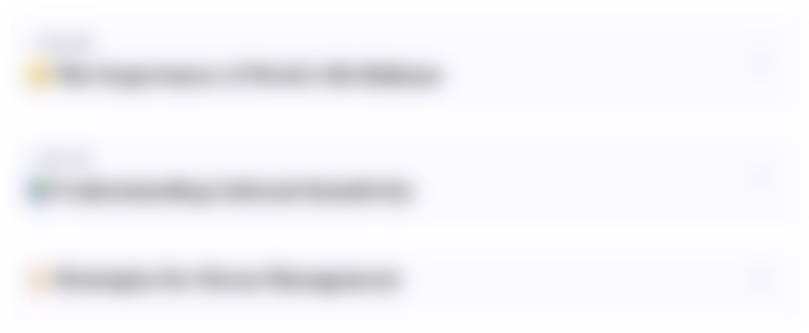
This section is available to paid users only. Please upgrade to access this part.
Upgrade NowMindmap
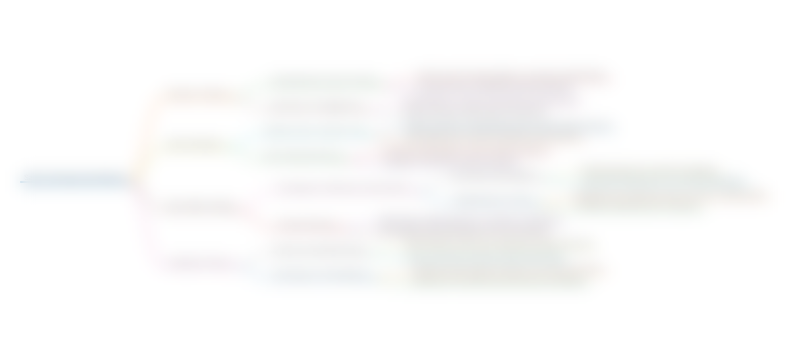
This section is available to paid users only. Please upgrade to access this part.
Upgrade NowKeywords
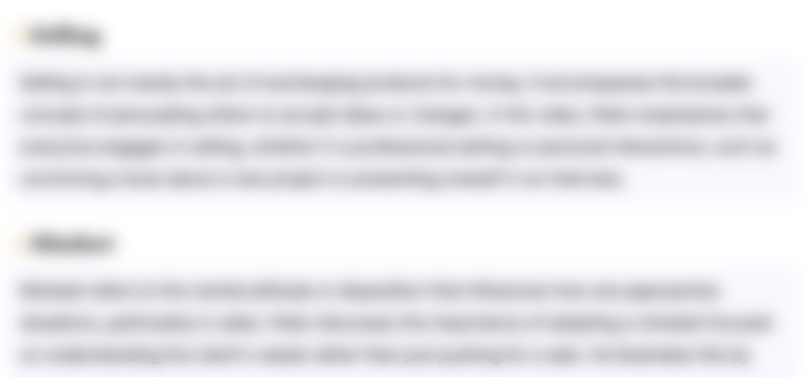
This section is available to paid users only. Please upgrade to access this part.
Upgrade NowHighlights
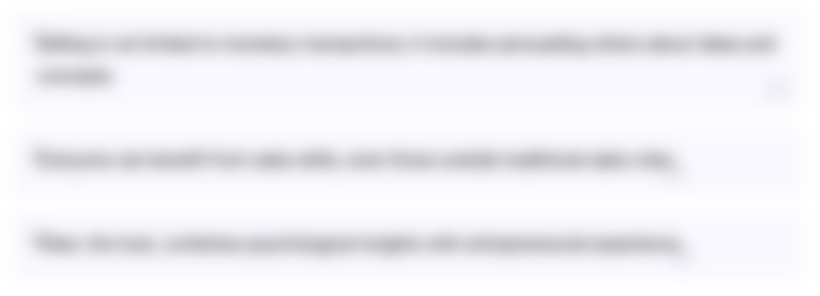
This section is available to paid users only. Please upgrade to access this part.
Upgrade NowTranscripts
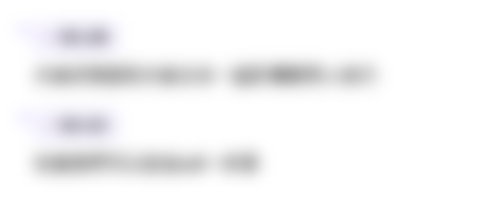
This section is available to paid users only. Please upgrade to access this part.
Upgrade NowBrowse More Related Video

American Eagle Outfitters' Supply Chain Innovation Award Competition Case Study

Business Case: Multi-Warehouse Inventory Management

Introduction to PAR Inventory Management by Trident Edge Consulting
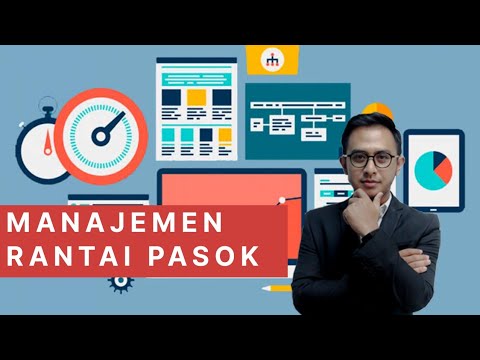
Manajemen Produksi - Ep.13 Supply Chain Management/Manajemen Rantai Pasok

Walmart - Supply Chain Management System
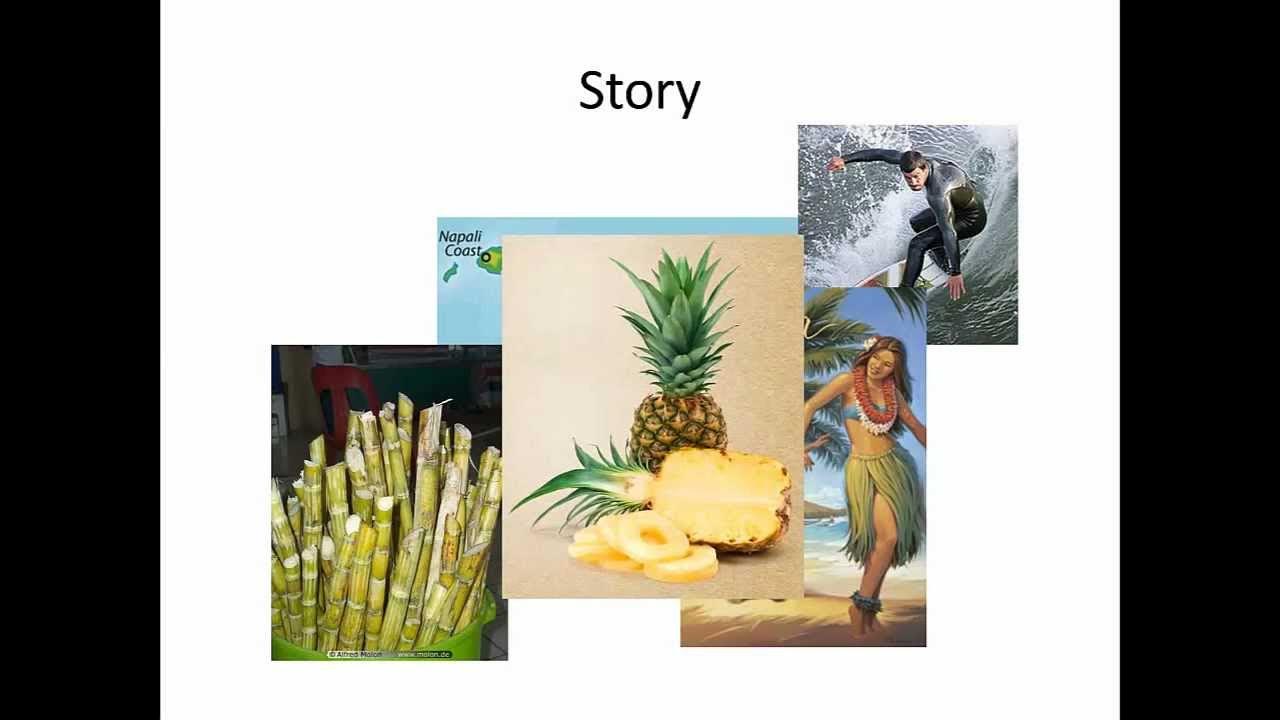
Introduction to Supply Chain Management, Transportation
5.0 / 5 (0 votes)