Digital Twins for Automobile Manufacturing | Digital Manufacturing & Industry 4.0 Case Study by VB
Summary
TLDRThe automobile industry faces significant challenges due to rising demand and global supply chain disruptions, especially from the semiconductor shortage. Phoebe's digital twin models, powered by Industry 4.0 technologies, offer a solution by integrating robotics, data modeling, and digitalization into manufacturing processes. These digital twins enable car manufacturers to optimize production, address raw material availability, and improve quality assurance. By providing real-time insights into people, processes, machines, and materials, Phoebe helps streamline production and meet the demands of a rapidly evolving market.
Takeaways
- 😀 Digital twins can revolutionize the automobile manufacturing process by integrating people, processes, machines, and materials into digital models for accurate emulation.
- 😀 Phoebe digital twin models are specifically designed for car manufacturers to streamline production and improve efficiency.
- 😀 The automobile industry faces significant challenges, particularly due to the ongoing semiconductor shortage, which has impacted the global supply chain.
- 😀 Global disruptions in the semiconductor industry are expected to continue, further affecting the automobile manufacturing sector.
- 😀 Industry 4.0 solutions, like digital twins, offer innovative ways to address global challenges in automobile manufacturing, especially in production optimization and supply chain management.
- 😀 Digital twins help in continuous training of integrated robotics and data models, ensuring the consistent quality of automotive products.
- 😀 The integration of robotics with digital twins helps in automating production and improving delivery estimation by considering raw material availability and production demands.
- 😀 With digital twins, manufacturers can better manage production timelines, ensuring accurate estimations of delivery even amidst supply chain disruptions.
- 😀 The need for digitalization in automobile production is growing as manufacturers must cope with increasing demand and supply chain complexities.
- 😀 By using digital twins, automobile manufacturers can enhance decision-making, reduce inefficiencies, and ensure smoother operations in an increasingly complex industry landscape.
Q & A
What is the main challenge faced by automobile manufacturers in recent years?
-The main challenge faced by automobile manufacturers is a significant gap in the supply chain, especially due to the global chip shortage, which has disrupted production.
How can the automobile industry adopt digital manufacturing technologies?
-The automobile industry can adopt digital manufacturing by integrating digital twins, robotics, and data models to enhance production efficiency, quality control, and overall operations.
What are digital twins in the context of automobile manufacturing?
-Digital twins are virtual models that represent the entire production process, including people, processes, machines, and materials. These models simulate real-world conditions for accurate emulation and optimization.
What role does Phoebe's digital twin models play in the automobile industry?
-Phoebe's digital twin models are specifically designed for car makers to improve manufacturing processes. These models integrate robotics and data to ensure product quality and streamline production.
What are the key benefits of using digital twins in automobile manufacturing?
-Digital twins help enhance accuracy in production planning, optimize resource utilization, improve product quality, and address supply chain disruptions by providing real-time data and simulations.
What are the global challenges that can be addressed by industry 4.0 solutions?
-Industry 4.0 solutions, like digital twins, can help address global challenges such as supply chain shortages, production inefficiencies, and the ongoing semiconductor shortage affecting multiple industries, including automotive.
How does the integration of robotics and data models benefit automobile manufacturing?
-Integrating robotics and data models allows for continuous quality training, precise delivery estimates, and efficient coordination between raw material availability and production demands.
What is the significance of continuous training for digital twins in automobile manufacturing?
-Continuous training ensures that digital twins remain up-to-date with real-time data, helping to improve product quality and production accuracy, thus preventing potential errors or inefficiencies.
Why is the availability of raw materials crucial in digital twin-based production?
-The availability of raw materials is a key factor in accurate production estimation. Digital twins allow manufacturers to simulate real-world scenarios, helping to better predict supply needs and avoid production delays.
What is the role of human labor in the digital twin model for automobile manufacturing?
-In the digital twin model, human labor is integrated with automated processes to ensure accurate production planning, efficient resource allocation, and real-time decision-making, complementing robotic systems.
Outlines
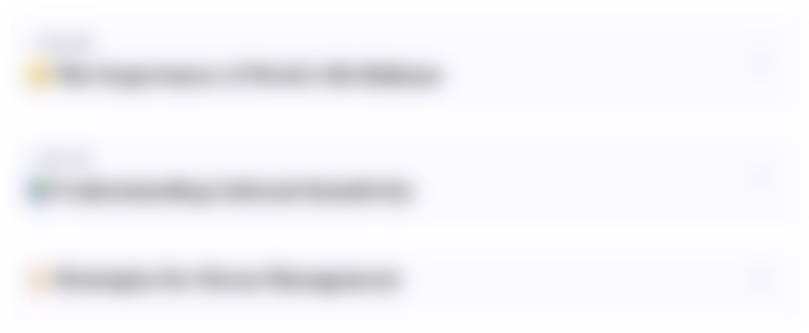
This section is available to paid users only. Please upgrade to access this part.
Upgrade NowMindmap
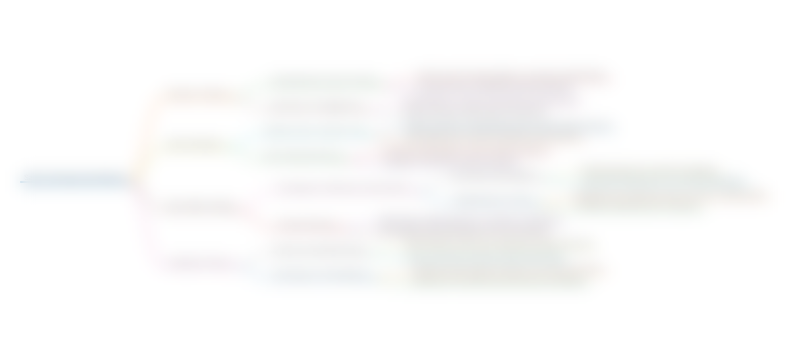
This section is available to paid users only. Please upgrade to access this part.
Upgrade NowKeywords
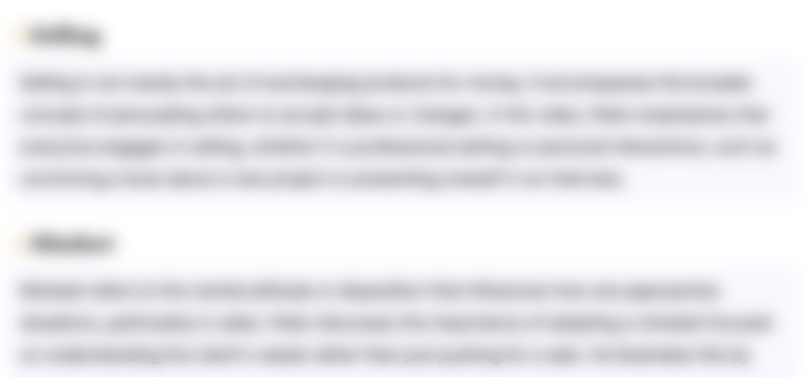
This section is available to paid users only. Please upgrade to access this part.
Upgrade NowHighlights
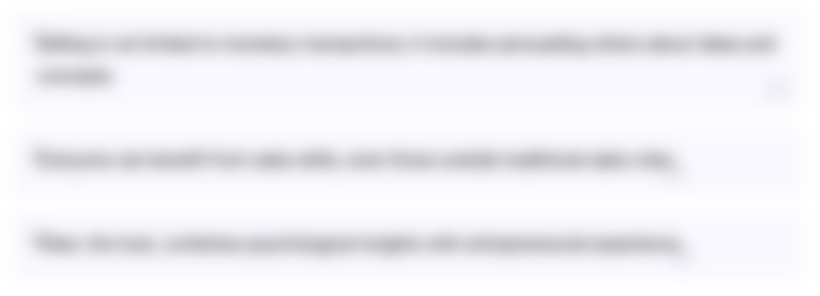
This section is available to paid users only. Please upgrade to access this part.
Upgrade NowTranscripts
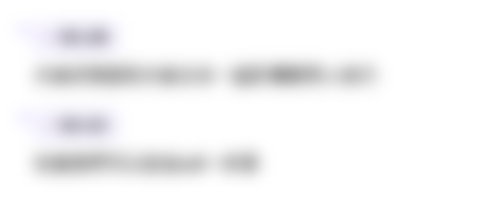
This section is available to paid users only. Please upgrade to access this part.
Upgrade NowBrowse More Related Video

China's economic situation is 'still mixed,' UOB says
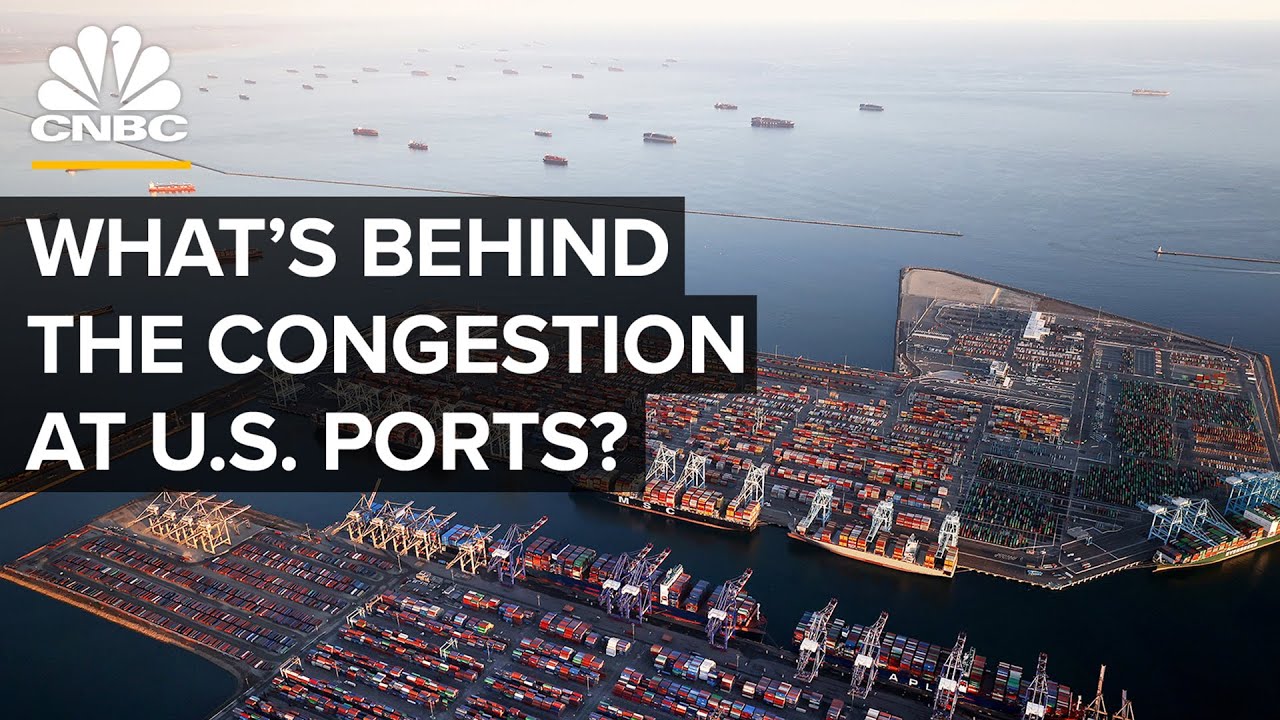
Why U.S. Ports Are Some Of The Least Efficient In The World

Why Global Supply Chains May Never Be the Same | WSJ Documentary

Vietnam's Economy: The Microchip Miracle

The Canadian Housing Market is About to Flip...

Why Everything Is On Sale: The Bullwhip Effect | WSJ
5.0 / 5 (0 votes)