Shell Molding - Expandable Mold Casting Processes
Summary
TLDRIn this tutorial on shell molding, a specialized metal casting process, the speaker explains the step-by-step procedure involved in creating a thin shell mold using sand and thermosetting resin. Developed in the 1940s, shell molding offers advantages like smoother surfaces, better dimensional accuracy, and reduced need for machining, making it ideal for large-scale production. However, it is more expensive compared to traditional sand casting and is not cost-effective for small quantities. Examples of parts produced through shell molding include gears and camshafts. The tutorial provides a clear overview of both the process and its pros and cons.
Takeaways
- 😀 Shell molding is an expandable mold casting process that involves using a thin shell mold made of sand and thermosetting resin.
- 😀 It was developed in Germany during the early 1940s as a method to improve casting accuracy and surface finish.
- 😀 The process begins by heating a match plate or Köppen drag metal pattern and placing it over sand mixed with thermosetting resin.
- 😀 The mold is formed by inverting the box so that the sand and resin mix partially cures on the hot pattern, forming a hard shell.
- 😀 After the initial cure, the mold is repositioned to remove any uncured particles before the shell is further hardened in an oven.
- 😀 Once fully cured, the shell mold is stripped from the pattern, leaving a high-precision mold cavity.
- 😀 The two halves of the shell mold are assembled and supported by sand or metal shot in a box for pouring molten metal.
- 😀 The final casting is obtained after pouring and removing the sprue, producing a smooth and accurate part.
- 😀 The advantages of shell molding include smoother surfaces, better dimensional accuracy, reduced need for machining, and suitability for mass production.
- 😀 Disadvantages include the higher cost of metal patterns and the process being less cost-effective for small-scale production.
- 😀 Shell molding is commonly used to cast parts like gears and camshafts, where precision and smooth finishes are crucial.
Q & A
What is shell molding?
-Shell molding is a casting process where a thin shell mold is created using sand mixed with a thermosetting resin binder. The mold is formed by heating a metal pattern and allowing the sand-resin mixture to cure around it.
When was shell molding developed and where?
-Shell molding was developed in Germany in the early 1940s.
What are the main differences between shell molding and sand casting?
-The main differences between shell molding and sand casting lie in the composition of the mold material, the method of making the mold, and the way the pattern is made. Shell molding uses a sand-resin mixture, while sand casting typically uses green sand.
What is the first step in the shell molding process?
-The first step involves heating a metal pattern (often a match plate or Köppen drag pattern) and placing it over a box containing sand mixed with thermosetting resin.
What happens during the second step of shell molding?
-In the second step, the box is inverted, allowing the sand and resin mixture to fall onto the hot pattern. This causes a layer of the mixture to partially cure, forming a hard shell around the pattern.
Why is the sand shell heated in an oven during the fourth step?
-The sand shell is heated in an oven to complete the curing process, ensuring that the shell becomes fully hardened and stable before the mold is used for casting.
What is the purpose of assembling the two halves of the shell mold in step six?
-The two halves of the shell mold are assembled and supported by sand or metal shot to prepare the mold for pouring the molten metal into it. This ensures that the mold remains stable during the casting process.
What are the advantages of shell molding?
-Shell molding offers several advantages, including smoother mold surfaces, better flow of molten metal, improved surface finish on the casting, good dimensional accuracy, minimal need for machining, mold collapse ability to prevent cracking, and the ability to be mechanized for mass production.
What is the main disadvantage of shell molding?
-The main disadvantage of shell molding is the higher cost of the metal pattern compared to greensand molds, which makes it less cost-effective for small-scale production.
What types of parts are commonly produced using shell molding?
-Shell molding is commonly used for parts that require high precision and smooth surface finishes, such as gears and camshafts.
Outlines
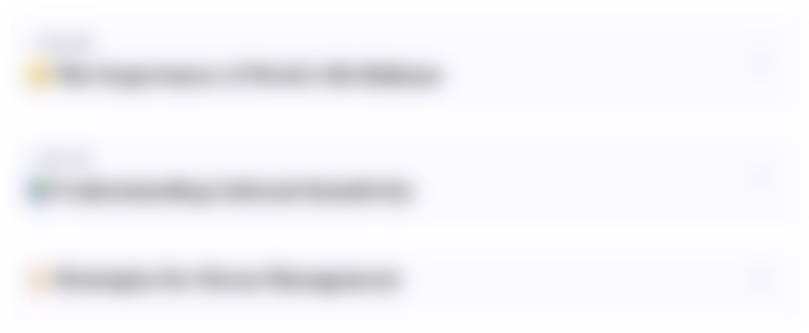
This section is available to paid users only. Please upgrade to access this part.
Upgrade NowMindmap
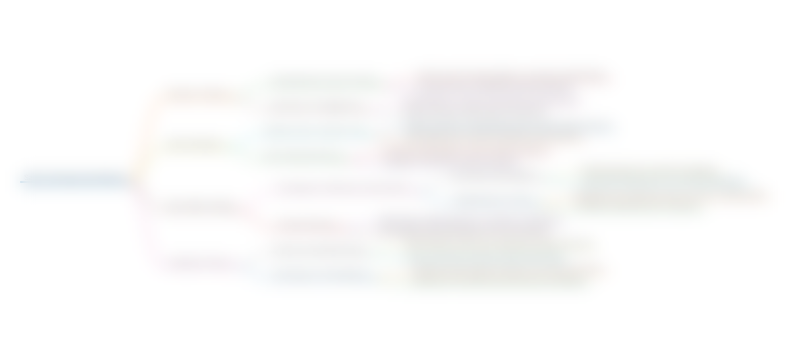
This section is available to paid users only. Please upgrade to access this part.
Upgrade NowKeywords
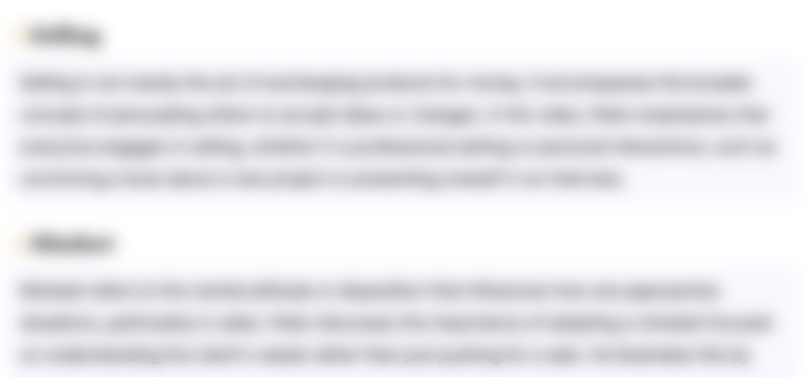
This section is available to paid users only. Please upgrade to access this part.
Upgrade NowHighlights
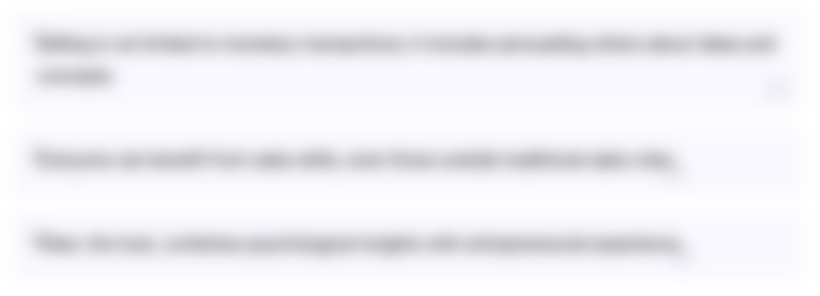
This section is available to paid users only. Please upgrade to access this part.
Upgrade NowTranscripts
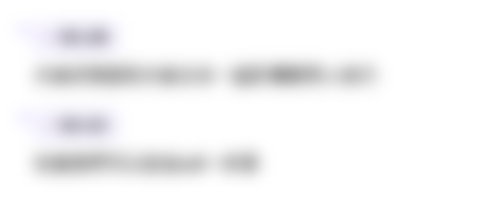
This section is available to paid users only. Please upgrade to access this part.
Upgrade NowBrowse More Related Video
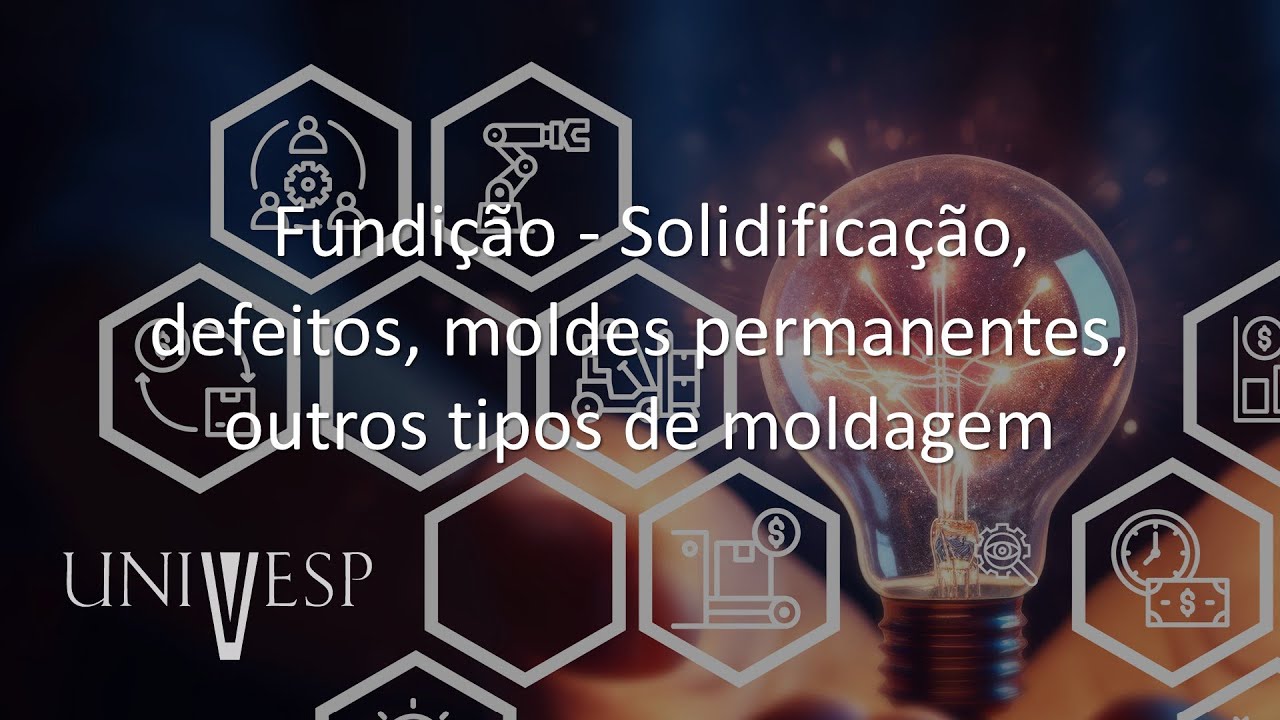
Materiais e Processos de Fabricação para Engenharia de Produção - Fundição - Solidificação, defeitos
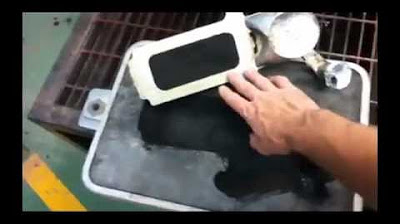
Sand Casting

What Are The Common Types Of Metal Casting Process In Engineering and Industry?

Sand Casting

Pembuatan produk bahan komposit | Asbak dari resin epoxy dan serbuk kayu

PENGECORAN LOGAM | Praktikum MK Teknologi Manufaktur
5.0 / 5 (0 votes)