Battery Management System Development in Simulink
Summary
TLDRThe video script details the design and simulation of a Battery Management System (BMS) in Simulink, focusing on its application in an electric vehicle powertrain. The BMS model is used to simulate various usage cycles and environmental conditions to evaluate the system's response to unsafe conditions, such as temperature, voltage, or current outside recommended limits. The script explains the model's components, including the battery pack with different cell configurations, the BMS ECU with monitoring and control algorithms, and the charger and inverter contactor circuitry. It also discusses the importance of accurate State of Charge (SOC) estimation and presents three methods for this purpose: Coulomb counting, Unscented Kalman Filter (UKF), and Extended Kalman Filter (EKF). The video emphasizes the need for balancing individual battery cells to prevent underutilization and the significance of active thermal management to maintain cell condition uniformity. The script concludes by highlighting the use of Simulink, Stateflow, and Control System toolboxes for designing the BMS through modeling and simulation.
Takeaways
- 🚗 The BMS model in Simulink is used for desktop simulations to evaluate the system's response to unsafe conditions such as temperature, voltage, or current outside recommended limits.
- 🔋 The model can simulate various usage cycles and environmental conditions, aiding vehicle designers in testing scenarios without damaging real batteries.
- 📊 The BMS ECU within the model has monitoring and control algorithms connected to a block representing the battery pack and its circuitry and peripherals.
- 🔌 The model includes two versions of the battery pack: a small one with six cells and a larger one with 16 modules, each containing six cells in series.
- 🔥 The thermal layout of the battery pack is asymmetrical, leading to significant temperature differences among cells, which is crucial for understanding real-life performance.
- 🔄 Each cell in the model has an equivalent circuit that includes temperature, SOC, and aging dependencies, mimicking real-life lithium chemistry behaviors.
- 🔄 The BMS algorithm includes passive balancing circuitry to maintain battery cell modules' balance and better utilize total storage capacity.
- 🔌 The model also includes charger and inverter contactor circuitry to prevent high current from damaging the battery pack during charging.
- 🔍 The BMS subsystem uses individual cell voltages and temperatures to calculate maximum allowable charge and discharge current levels for safety.
- 🔄 State of charge (SOC) estimation is crucial and is achieved through three methods: Coulomb counting, unscented Kalman filters, and extended Kalman filters, each with its merits and limitations.
- 🔧 The model allows for the assessment of SOC estimation accuracy and the effectiveness of balancing procedures, highlighting the need for active thermal management.
Q & A
What is the primary purpose of the BMS model in Simulink?
-The primary purpose of the BMS model in Simulink is to simulate desktop simulations for reproducing diverse usage cycles and environmental conditions to evaluate the system's response to potentially unsafe conditions such as temperature, voltage, or current outside the recommended limits.
How does the BMS model help in testing different scenarios without damaging real batteries?
-The BMS model allows vehicle designers to test various situations like different temperatures, state of charges, and aggressive drive cycles in simulation, which helps in understanding the system's behavior without risking damage to the real battery.
What are the two versions of the battery pack included in the model?
-The model contains two versions of the battery pack: a small one with just six cells connected in series, and a larger one with 16 modules, each module containing the six-cell series string, all connected in one parallel string.
Why is it important to model the physical domain of each cell in the battery pack?
-Modeling the physical domain of each cell, indicated by different colors (e.g., blue for electrical, orange for thermal), helps in understanding how cells exchange heat with one another and how thermal layouts can affect temperature differences among cells, which is crucial for battery performance and safety.
What role does the equivalent circuit play inside each unit cell?
-The equivalent circuit inside each unit cell, which should have a topology and parameters that mimic real-life lithium chemistry responses, is essential for providing an equivalent response to what would be observed experimentally, including dependencies on temperature, SOC, and possibly aging.
How does the BMS algorithm manage cell balancing to optimize battery utilization?
-The BMS algorithm manages cell balancing by selectively closing switches in the passive balancing circuitry, which allows cells to undergo a partial discharge to lower their voltage, maintaining the battery cell modules' balance and enabling better utilization of the total storage capacity.
What is the significance of the charger and inverter contactor circuitry in the BMS model?
-The charger and inverter contactor circuitry are important for safely connecting the battery pack to a charger. They prevent excessively high current from rushing into the pack, which could potentially cause damage, by implementing a special pre-connection sequence.
How does the BMS algorithm protect the battery pack from physical damage due to temperature extremes?
-The BMS algorithm uses a lookup table with a rising or falling s-shaped profile to specify a current threshold based on temperature, modulating the allowable current delivery to avoid physical damage to the cell materials at high temperatures during charge and discharge, and at low temperatures during charge.
What are the three methods for state of charge (SOC) estimation presented in the BMS model?
-The three methods for SOC estimation presented in the BMS model are Coulomb counting, unscented Kalman filter (UKF), and extended Kalman filter (EKF). Each method has its merits and limitations and is used to estimate the SOC based on different principles and data.
How does the state machine in the BMS algorithm define the main operating states?
-The state machine in the BMS algorithm uses a state flow diagram to define the main operating states, which include standby, driving, charging, and fault states. It uses components representing states that are active or inactive depending on conditions, with code executing during entry, during, or exit from the state.
What is the importance of accurate SOC estimation in a battery management system?
-Accurate SOC estimation is crucial as it determines how much longer a vehicle can be driven before needing to recharge. It is more challenging than traditional fuel gauge design because SOC is not directly measurable; instead, other measurements are related to SOC, which requires sophisticated algorithms to estimate correctly.
How does the BMS model handle temperature differences among cells to prevent uneven degradation?
-The BMS model addresses temperature differences by showing the significant discrepancy among the hottest and coldest cells due to layout symmetry in thermal behavior. It highlights the need for active thermal management to keep thermal differences within a few degrees Celsius to prevent faster degradation of hotter cells.
What are the capabilities and limitations of Coulomb counting for SOC estimation?
-Coulomb counting is simple and has a very low computational cost, making it beneficial for SOC estimation. However, its limitations include the accumulation of current sensor error and the inability to recover from a wrong initial condition due to the lack of feedback from voltage measurements.
Why is it necessary to activate passive balancing in the BMS model?
-Passive balancing is necessary to keep individual battery cells at roughly the same state of charge. Without it, the cell with the highest SOC would limit the amount of charge that can be put into the pack, leading to underutilization of the system and reduced performance.
Outlines
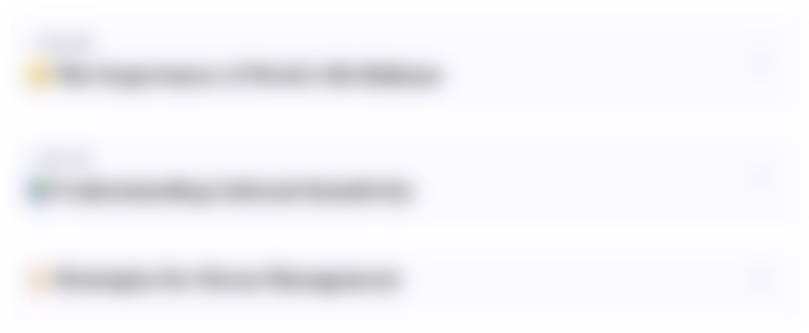
This section is available to paid users only. Please upgrade to access this part.
Upgrade NowMindmap
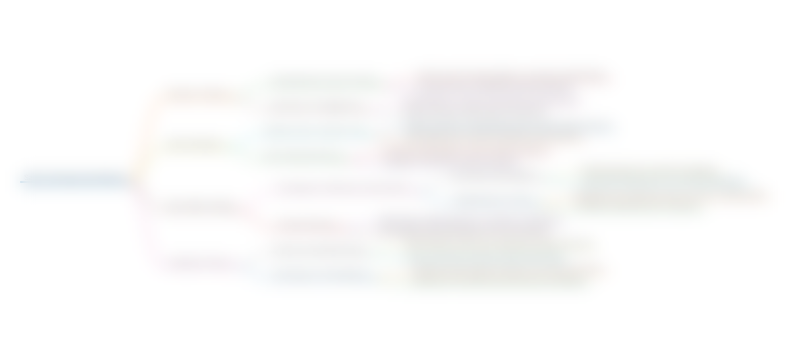
This section is available to paid users only. Please upgrade to access this part.
Upgrade NowKeywords
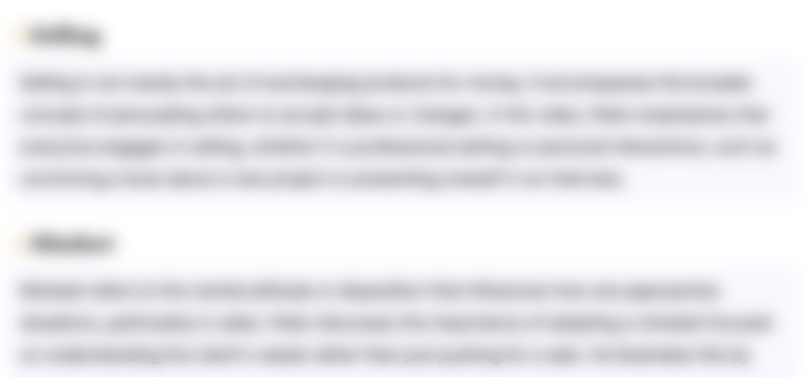
This section is available to paid users only. Please upgrade to access this part.
Upgrade NowHighlights
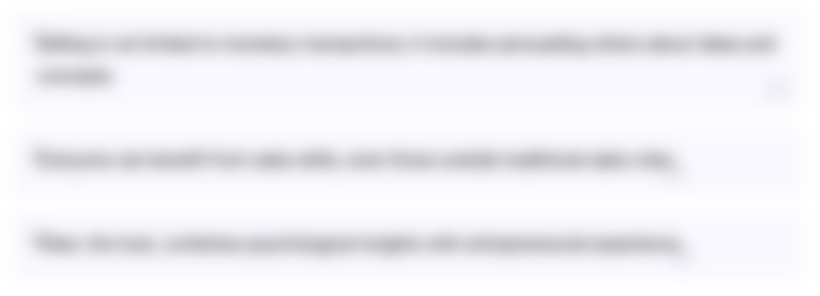
This section is available to paid users only. Please upgrade to access this part.
Upgrade NowTranscripts
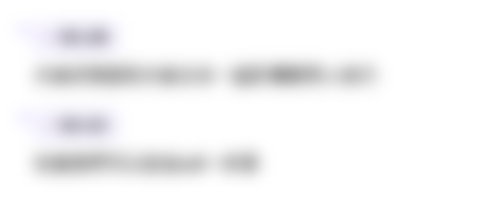
This section is available to paid users only. Please upgrade to access this part.
Upgrade NowBrowse More Related Video

Part 1: Introduction to Testing Battery Management System (BMS) Software
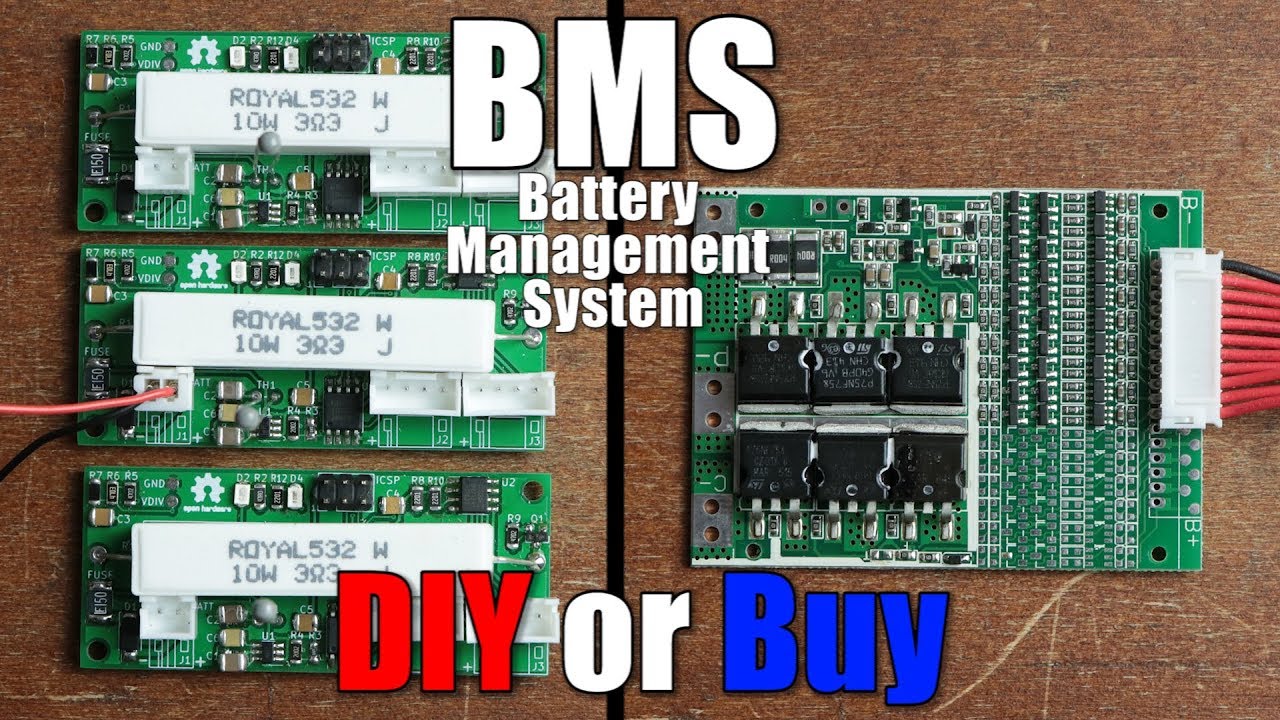
BMS (Battery Management System) || DIY or Buy || Properly protecting Li-Ion/Li-Po Battery Packs

Can I fit Tesla Batteries in my Electric Hummer?! - Battery Box Build
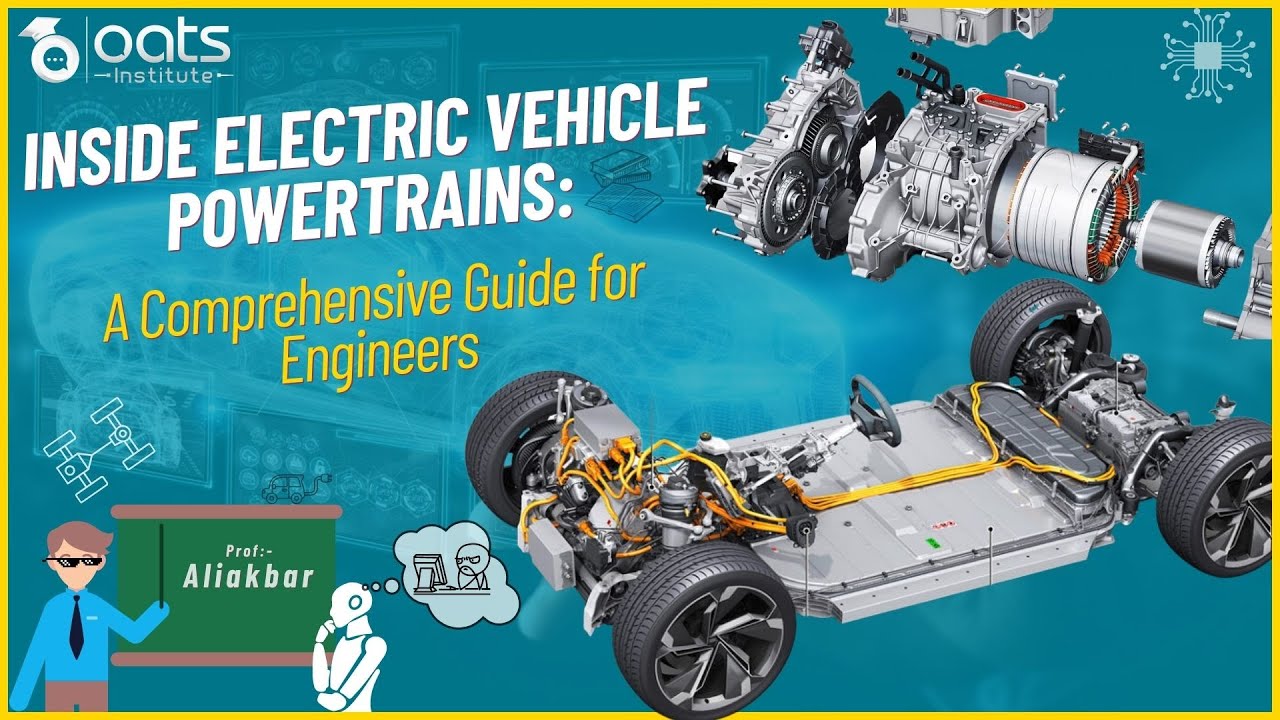
Inside Electric Vehicle Powertrains: A Comprehensive Guide for Engineers
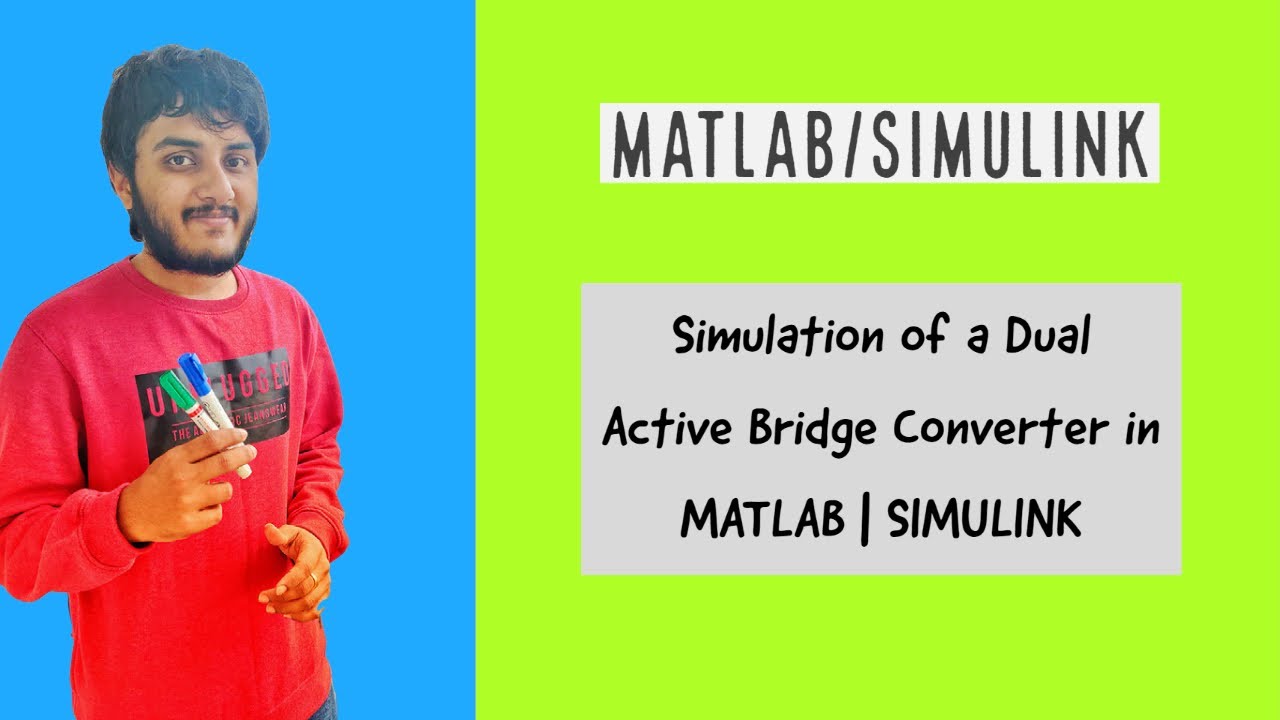
Simulation of a Dual Active Bridge Converter in MATLAB | SIMULINK

Make your own LED Battery Level Indicator
5.0 / 5 (0 votes)