Supervisor Safety Tip: Machine Guarding
Summary
TLDRIn this informative video, Jill, Chief Safety Officer at Vivid Learning Systems and former OSHA inspector, demonstrates key aspects of machine guarding assessments. Filmed at the Monterey Bay Aquarium, Jill walks through different types of hazards like point of operation, in-running nip points, rotating parts, and flying chips or sparks, providing real-world examples. She explains the importance of proper guarding, such as using chip shields and securing rotating shafts, to protect workers from injuries. Jill also emphasizes the need for safety audits and the risks posed by homemade tools that employees sometimes create to bypass broken or inadequate safety measures.
Takeaways
- 😀 Identifying hazards in machine guarding requires assessing the point of operation, rotating parts, nip points, and risks like flying chips or sparks.
- 😀 Ensure that any machine guarding is designed to prevent access to hazardous points, preventing workers from reaching over, under, or around guards.
- 😀 The point of operation is a key area to assess, as workers may be exposed to hazards when interacting with machinery.
- 😀 In-running nip points are dangerous areas where rotating parts can pull in workers, clothing, or hair. Adequate guarding is essential here.
- 😀 Rotating parts, like pulleys and belts, must be guarded to prevent entanglement, which can lead to serious injury.
- 😀 Flying chips or sparks are common hazards in metalworking machines, requiring shields and appropriate personal protective equipment (PPE) like safety glasses and face shields.
- 😀 When guarding rotating shafts, ensure that the guard fully encloses the rotating parts to protect workers from getting caught.
- 😀 Expanded metal guards are effective for protecting belt drive systems. Consider painting these guards flat black to improve visibility during inspections.
- 😀 Always check for homemade tools or modifications that employees may use to bypass machine guards or address malfunctions. These can introduce new risks.
- 😀 Safety professionals should conduct regular hazard assessments to identify risks and ensure that guards are sufficient to protect workers.
- 😀 Safety is everyone’s responsibility—employees should be encouraged to report hazards and safety concerns to help maintain a safe working environment.
Q & A
What are the main types of hazards Jill focuses on during a machine guarding assessment?
-Jill focuses on four main types of hazards: point of operation, in-running nip points, rotating parts, and flying chips or sparks.
What does 'point of operation' refer to in machine guarding?
-The point of operation refers to the area where the work actually takes place, such as where materials are fed into the machine, which can pose a hazard if not properly guarded.
Why is it important to check if a guard allows access to the point of operation?
-It’s crucial because if a guard allows workers to reach over, around, under, or through, it may not be adequate and could lead to serious injury by exposing workers to moving parts or hazards.
What is an 'in-running nip point,' and why is it dangerous?
-An in-running nip point is where two parts of machinery move toward each other, such as rollers or belts. These points are dangerous because they can pull in clothing, hair, or body parts, potentially causing injury.
How does Jill recommend addressing the hazard of flying chips and sparks in a metalworking environment?
-Jill recommends using a chip shield to cover the point of operation, along with personal protective equipment (PPE) like safety glasses, face shields, and long sleeves to protect workers from flying chips and sparks.
What is the purpose of a guard in machinery?
-The purpose of a guard is to prevent workers from accessing hazardous areas of a machine, reducing the risk of injury from moving parts, sharp objects, or flying materials.
What are some common signs that workers might be bypassing machine guards?
-Common signs include the use of homemade tools such as long sticks, curved hooks, or objects with duct tape, which are often created by employees to bypass a broken or ineffective guard.
What is the significance of using expanded metal guards, and why does Jill suggest painting them flat black?
-Expanded metal guards are effective for protecting machinery while still allowing visibility. Jill suggests painting them flat black because it makes them easier to see through, which helps operators during inspections or adjustments.
Why does Jill emphasize checking for rotating parts in machinery during a safety audit?
-Jill emphasizes checking for rotating parts because they can pose a serious risk of injury if not properly guarded. Parts like belts or pulleys can catch clothing or body parts, potentially leading to accidents.
What is Jill’s general approach when conducting a machine guarding assessment?
-Jill's approach involves identifying hazards like the point of operation, nip points, rotating parts, and flying chips or sparks. She then evaluates whether guards are present and adequate, ensuring that workers cannot reach exposed hazards.
Outlines
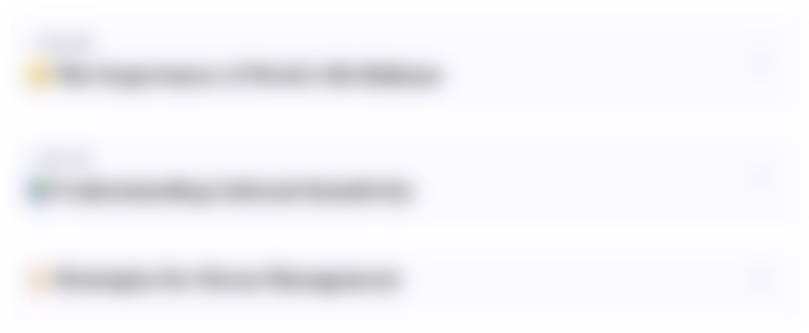
This section is available to paid users only. Please upgrade to access this part.
Upgrade NowMindmap
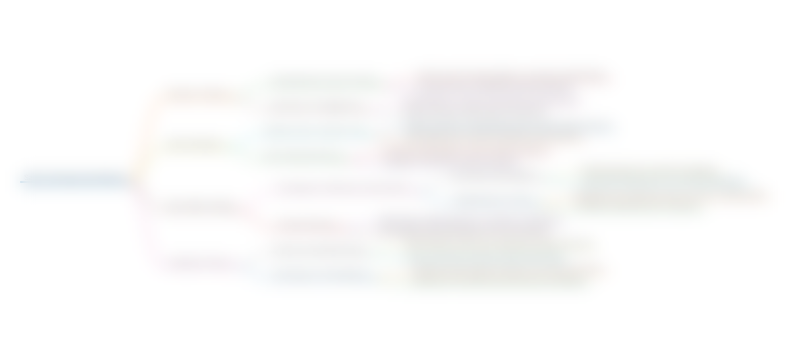
This section is available to paid users only. Please upgrade to access this part.
Upgrade NowKeywords
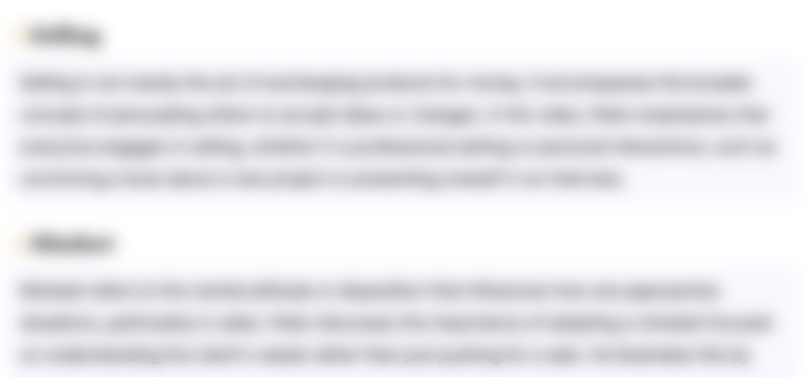
This section is available to paid users only. Please upgrade to access this part.
Upgrade NowHighlights
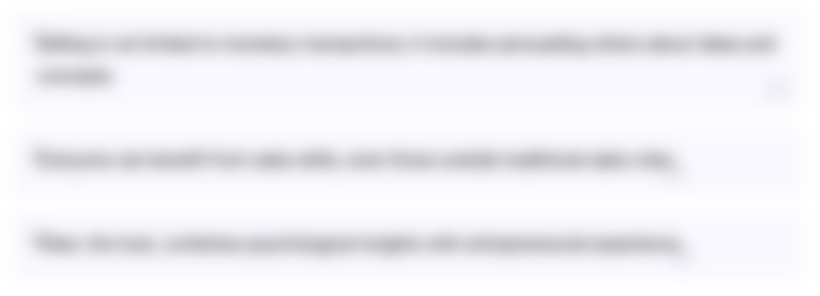
This section is available to paid users only. Please upgrade to access this part.
Upgrade NowTranscripts
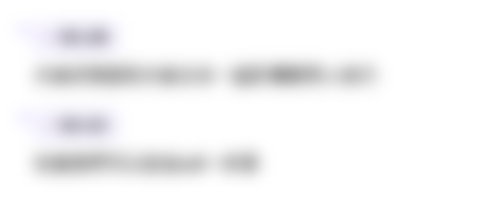
This section is available to paid users only. Please upgrade to access this part.
Upgrade NowBrowse More Related Video
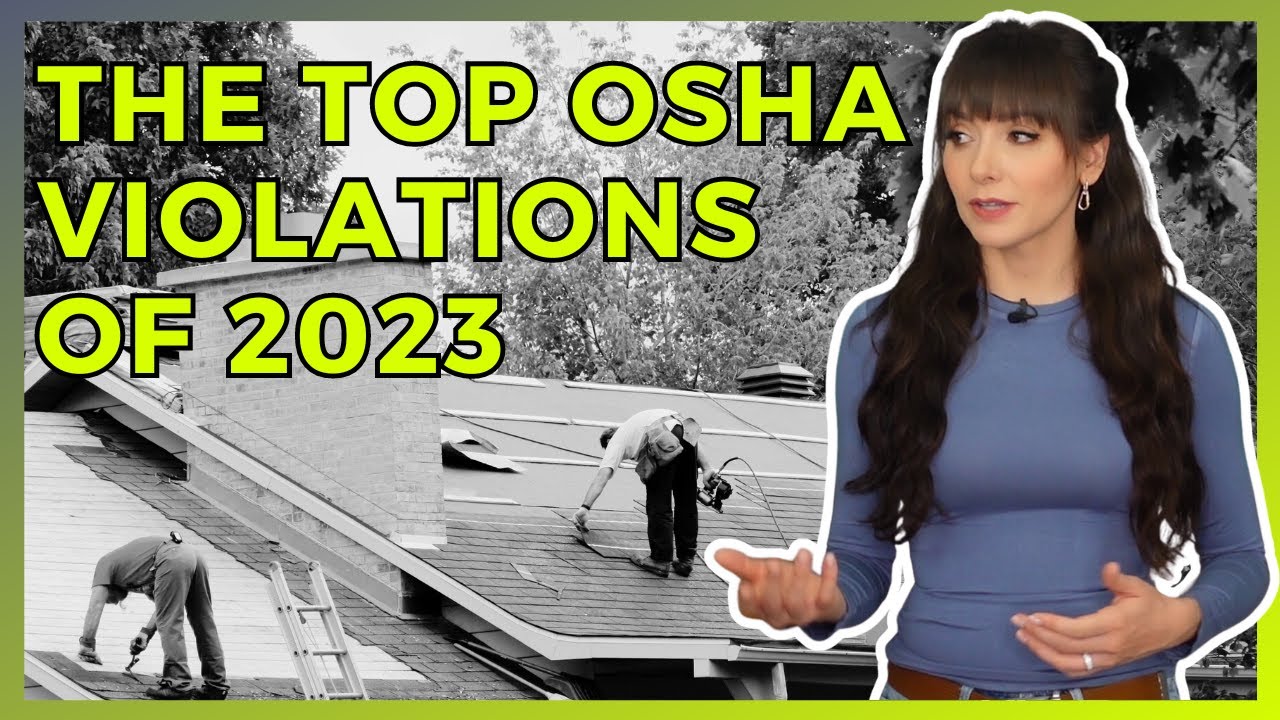
Top 10 OSHA Violations of 2023 | And how to prevent similar citations.
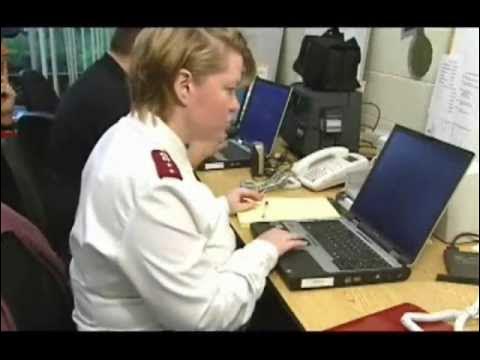
Incident Command System: Positions & Responsibilities

24 ORAS WEEKEND ONLINE EXCLUSIVE AUGUST 04, 2024: Mga apektadong residente ng baha sa Nueva...

Safety: The Fundamentals of On-Site OSHA Inspections
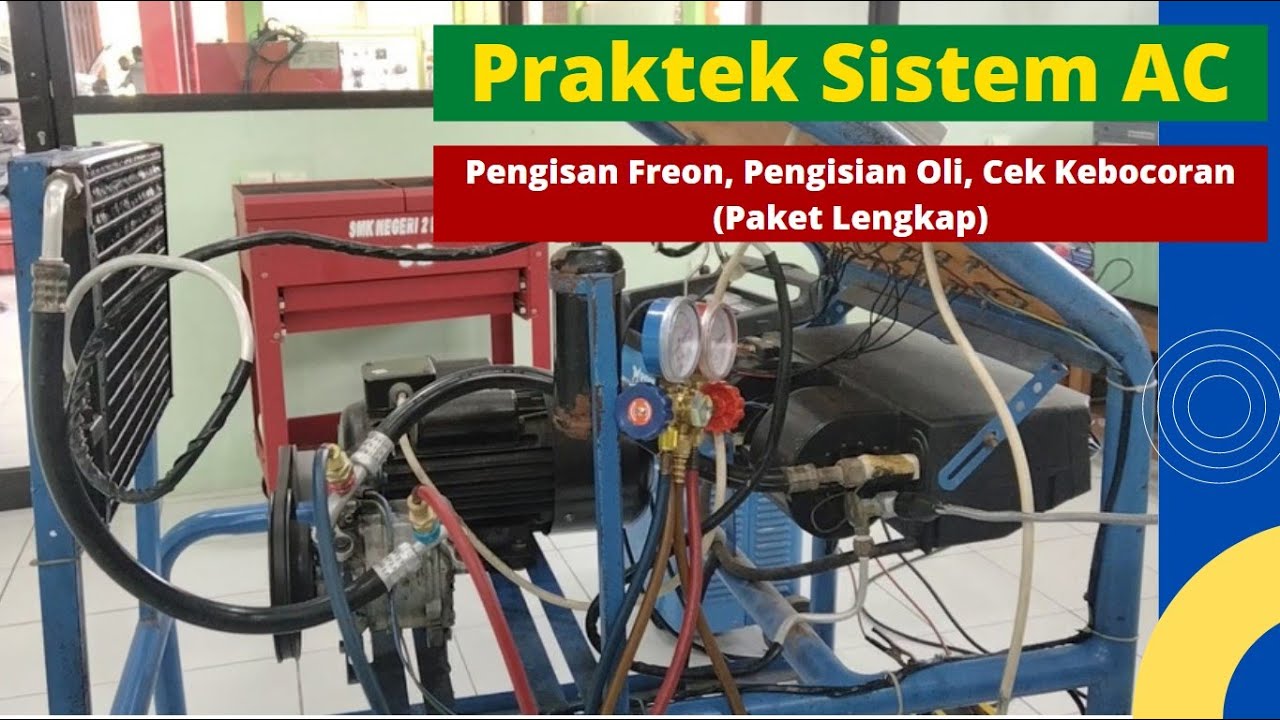
Praktek Sistem AC II Cara Mengganti Refrigerant (Freon) II Cara Mengisi Oli Pada Sistem AC

Intro to OSHA from SafetyVideos.com
5.0 / 5 (0 votes)