Can the steel industry go green? | FT Climate Capital
Summary
TLDRThe steel industry, a major global emitter of CO2, faces significant challenges in transitioning to greener methods. At Port Talbot, the largest steelworks in the UK, efforts are underway to decarbonize using technologies like electric arc furnaces, hydrogen, and carbon capture. While these innovations show promise, they require massive investment and raise concerns about job losses. Government support, through subsidies and funding, is crucial for the transition, but unions stress the need for a gradual shift. The steel industry must act globally to reduce emissions, overcome resource limitations, and make green steel economically viable to meet climate goals.
Takeaways
- 😀 Port Talbot, the UK's largest steelworks, is at a crossroads due to the need to decarbonize and achieve net-zero emissions, as it is the largest emitter of CO2 in the country.
- 😀 Steel production globally is responsible for 7-9% of carbon emissions, and companies worldwide are working on reducing their carbon footprint, including investments in new technologies like electric arc furnaces and hydrogen.
- 😀 The transition to net-zero steel production will require massive investments. Analysts estimate that $1.4 trillion is needed to decarbonize the steel and iron industries by 2050.
- 😀 ArcelorMittal in Ghent, Belgium, has implemented a biocoal facility that converts waste wood into biocoal, which reduces the carbon footprint of blast furnaces by about 5%.
- 😀 In addition to biocoal, ArcelorMittal has developed a gas fermentation plant that uses microbes to capture CO2 from blast furnace waste gases, converting it into ethanol for use in fuels and plastics.
- 😀 Despite promising technologies, such as gas fermentation, there is still a long way to go in reducing emissions, with ArcelorMittal's Ghent plant emitting 9 million tonnes of CO2 annually, capturing only a small fraction of that.
- 😀 The shift from traditional blast furnaces to electric arc furnaces is a key step in decarbonization. However, these furnaces require high-quality scrap metal, which is in limited supply.
- 😀 Some companies are looking into 'direct reduction plants' that use hydrogen or natural gas to reduce iron ore, with green hydrogen emerging as a promising solution, as demonstrated by the Swedish start-up H2 Green Steel.
- 😀 The cost of producing green steel is higher than conventional steel, with prices around 20-30% more expensive, but customers are increasingly willing to pay a premium for green steel, particularly in industries like automotive.
- 😀 Governments are supporting the transition to green steel, with funding for new technologies in Belgium, Germany, and the UK. However, unions are concerned about job cuts, as technologies like electric arc furnaces require fewer workers.
- 😀 The steel industry has faced technological shifts before, such as the transition from open hearth furnaces to blast furnaces, and while the shift to green steel is challenging, it is achievable with the right investments and policy support.
Q & A
What is the main challenge facing the steel industry in Port Talbot, Wales?
-The main challenge is decarbonizing the steelmaking process to meet the UK’s climate targets. Port Talbot is the largest single emitter of carbon dioxide in Britain, so the plant needs to change its methods to reduce emissions significantly.
How much iron or hot metal does Port Talbot's furnace number 4 produce annually?
-Port Talbot's furnace number 4 produces about 3.2 million tonnes of hot metal per year, with each furnace making around 5,500 to 6,000 tonnes of hot metal per day.
What is the global environmental impact of the steel industry?
-The steel industry accounts for 7 to 9 percent of global carbon dioxide emissions due to its reliance on billions of tonnes of coking coal in blast furnaces.
What is ArcelorMittal’s approach to reducing carbon emissions in steel production?
-ArcelorMittal is using biocoal made from waste wood to replace a portion of the regular coking coal in blast furnaces, which reduces the carbon footprint by about 5 percent.
How does the gas fermentation plant at ArcelorMittal’s Ghent site work?
-The gas fermentation plant uses bacteria to convert waste gases from blast furnaces into ethanol. The ethanol can then be used as a fuel or for other carbon-containing products like plastics.
What are the key technologies being explored to decarbonize the steel industry?
-Key technologies include electric arc furnaces, hydrogen-based production methods, carbon capture and storage, and the use of recycled steel. Some companies are also developing direct reduction plants using natural gas and hydrogen.
What is the role of green hydrogen in steel production?
-Green hydrogen is seen as a key part of reducing emissions in steel production, as it can replace coking coal in direct reduction processes to produce steel with minimal carbon emissions.
How does H2 Green Steel plan to scale up its production?
-H2 Green Steel plans to use green hydrogen and hydropower from the region in Sweden to produce steel. The plant aims to produce 2.5 million tonnes of steel in its first phase, with plans to ramp up to 5 million tonnes.
What are the economic implications of transitioning to green steel production?
-Green steel production is estimated to be 20 to 30 percent more expensive than traditional steel due to the cost of green hydrogen and electrification. However, customers, especially in industries like automotive, are willing to pay the premium for greener products.
How are governments supporting the steel industry's transition to green production methods?
-Several European governments are providing financial support for green steel initiatives. For example, Belgium, Germany, and the UK are backing projects like electric arc furnaces and direct reduction plants with subsidies and funding.
What are the concerns of unions regarding the transition to green steel?
-Unions are concerned about potential job losses during the transition, especially with the shift to electric arc furnaces, which could reduce employment. They advocate for a gradual transition to ensure workers and communities are supported.
Is the steel industry on track to meet its net-zero climate targets?
-Overall, the steel industry is not on track to meet its net-zero climate targets, as progress has been slower than needed. Governments need to remove subsidies for conventional, emissions-intensive methods and shift support to green steel technologies.
Outlines
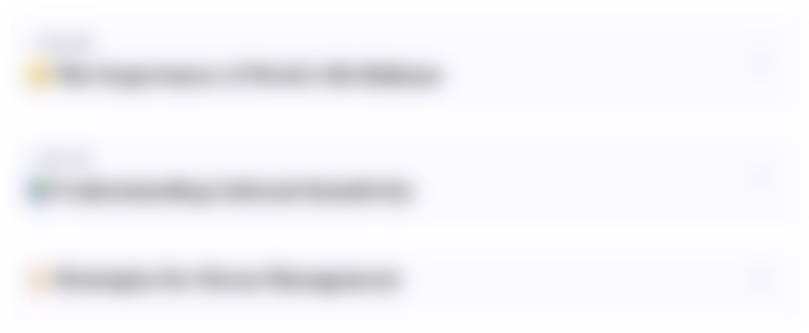
This section is available to paid users only. Please upgrade to access this part.
Upgrade NowMindmap
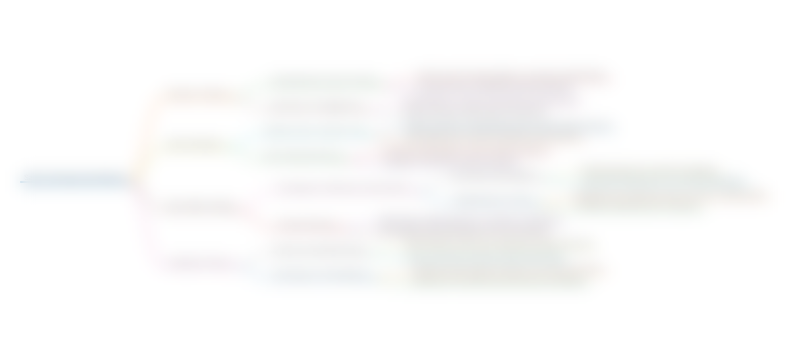
This section is available to paid users only. Please upgrade to access this part.
Upgrade NowKeywords
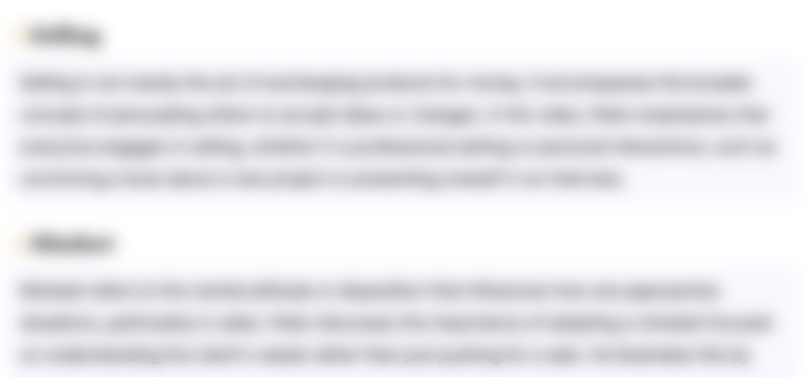
This section is available to paid users only. Please upgrade to access this part.
Upgrade NowHighlights
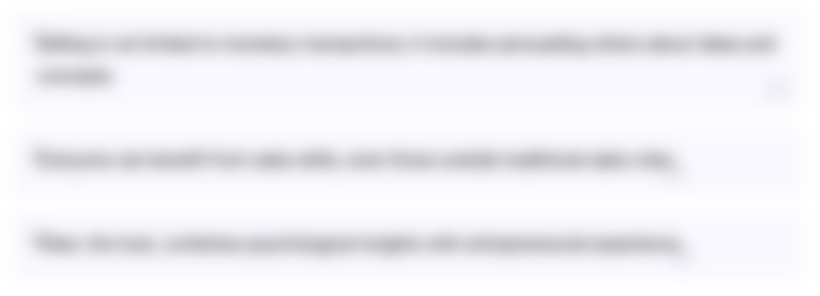
This section is available to paid users only. Please upgrade to access this part.
Upgrade NowTranscripts
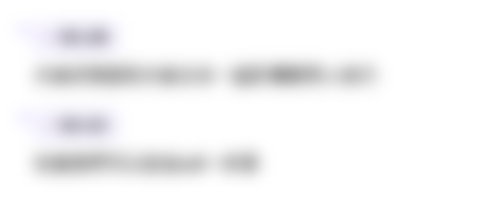
This section is available to paid users only. Please upgrade to access this part.
Upgrade NowBrowse More Related Video

Decarbonising steel making with new technologies
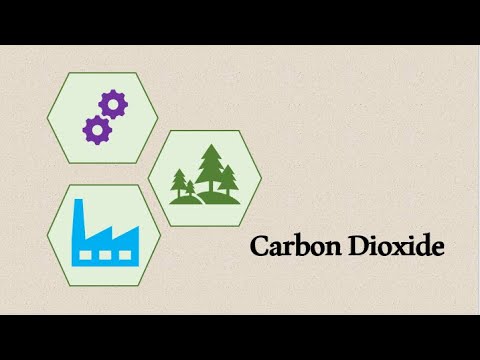
Let's Talk Global Warming Episode 2: Carbon Dioxide
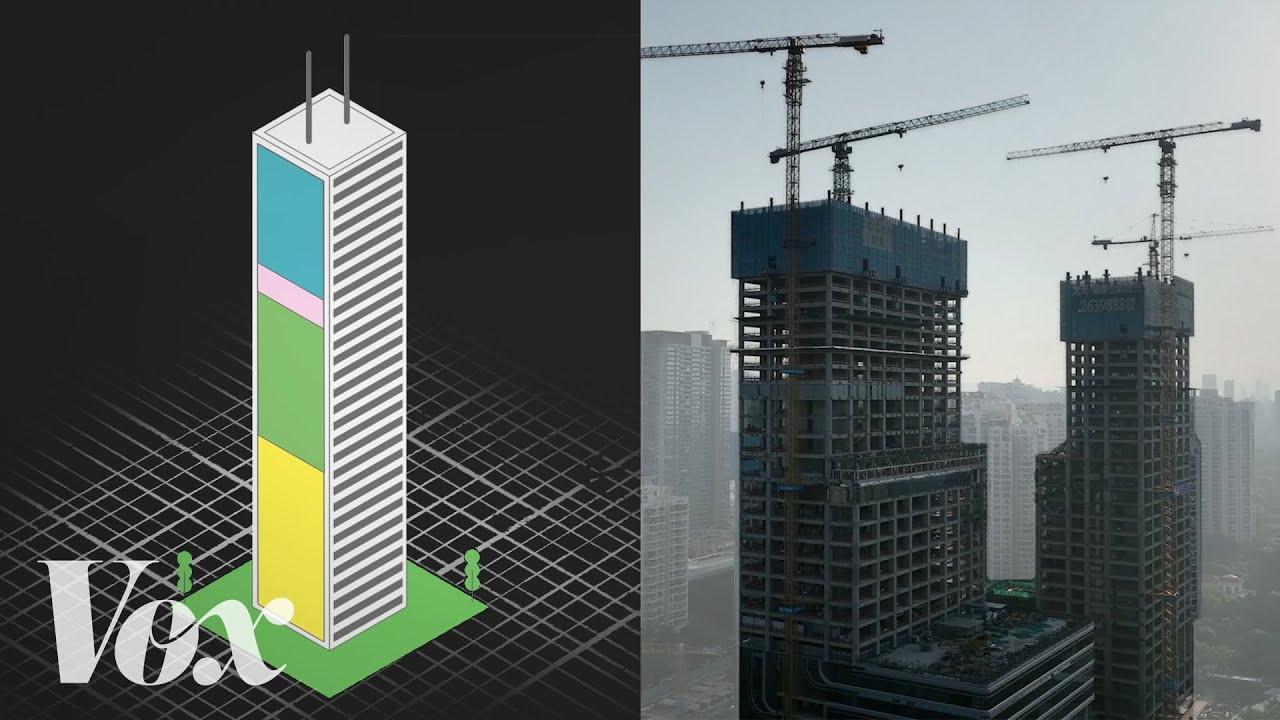
The big problem with cement, and how to fix it
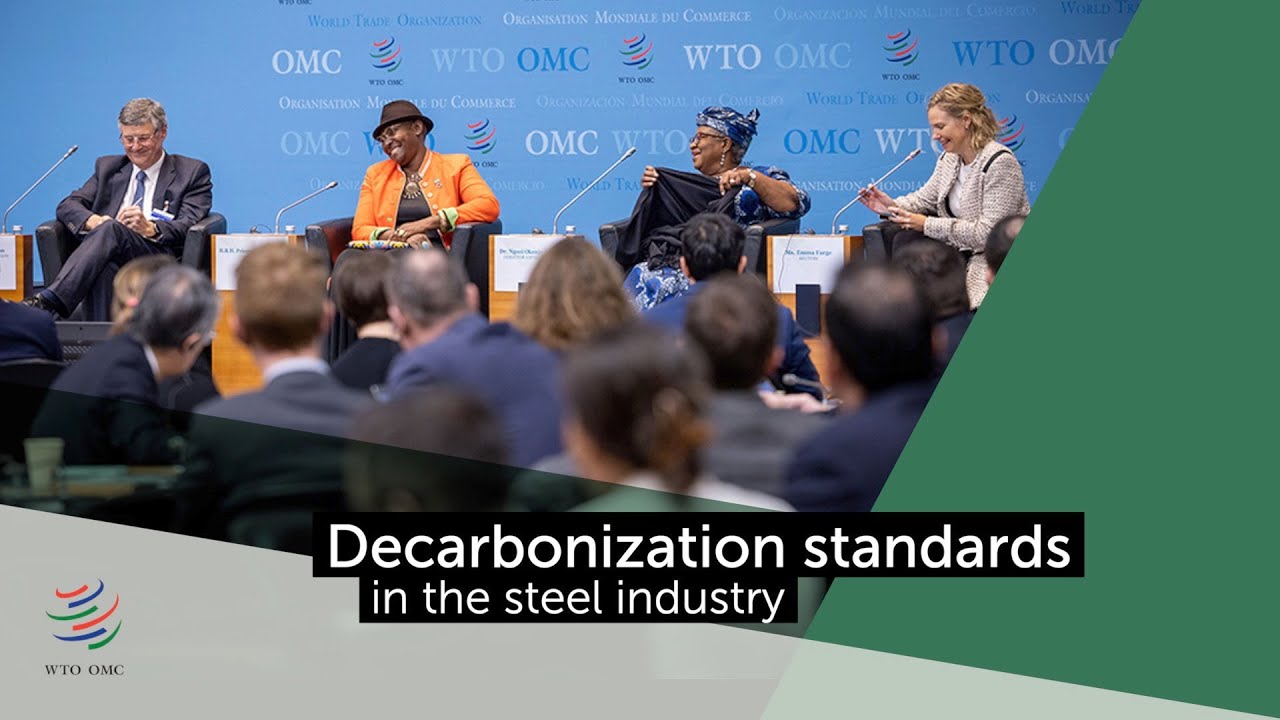
Decarbonization standards in the steel industry

How China's Happy Accident Could Change the Future

Five biggest environmental issues in India in 2023 | WION Climate Tracker
5.0 / 5 (0 votes)