PowerFlex 525 Safe Torque Off Function
Summary
TLDRThis video explains the Safe Torque Off (STO) feature in the PowerFlex 525 variable frequency drive, which ensures safety by immediately halting motor motion without removing power from the drive. STO integrates into safety control systems and complies with several safety standards, such as EN ISO 13849 and IEC 61508. The video demonstrates how to configure STO by connecting the drive to a safety circuit, ensuring proper wiring, and testing safety channels. The setup includes both coast-to-stop and controlled stop actions, showcasing the effective functionality of Safe Torque Off in industrial applications.
Takeaways
- 😀 Safe Torque Off (STO) is a feature in variable frequency drives that removes torque from the motor when activated, ensuring safety during operation.
- 😀 STO works by removing torque without cutting power to the drive, making it a reliable way to halt motion without turning off the entire system.
- 😀 This feature integrates into safety control systems and requires thorough risk assessments and periodic testing to ensure its effectiveness throughout the machine's life cycle.
- 😀 Safe Torque Off meets the safety standards required for systems, including EN ISO 13849, IEC 61508, and EN 61800-5-2.
- 😀 When setting up a drive for Safe Torque Off, always use copper wire with an insulation rating of 600 volts or greater and ensure that control wires are kept at least 1 foot apart from power wires.
- 😀 The PowerFlex 525 drive requires connection to a safety circuit to enable Safe Torque Off functionality, specifically involving safety terminals and the removal of protective jumpers.
- 😀 Safe Torque Off is activated when both safety inputs, S1 and S2, are connected, and if either loses power, the control circuit is disabled.
- 😀 For compliance with EN ISO 13849, both safety channels must be deactivated for the drive to operate safely.
- 😀 A demonstration shows how Safe Torque Off works by coasting to a stop when 24V DC is removed from the control terminals, halting the motor.
- 😀 Another demonstration shows controlled stop action with a delay, where the motor ramps down before Safe Torque Off is activated after a set delay time.
Q & A
What is Safe Torque Off (STTO) and why is it important?
-Safe Torque Off (STTO) is a safety feature in variable frequency drives like the PowerFlex 525 that immediately removes torque from the motor when activated. It is crucial because it ensures that the motor halts safely without removing power from the drive, which is essential for meeting safety standards and providing a safe operational environment.
Which safety standards does the STTO function comply with?
-The STTO function complies with several important safety standards, including EN ISO 13849 (Category 3, PL d), EN 62061, IEC 61508, and EN 61800-5-2. These standards are crucial for ensuring the system's safety and reliability throughout its lifecycle.
What precautions should be taken when setting up Safe Torque Off on the PowerFlex 525?
-When setting up STTO on the PowerFlex 525, it's important to use copper wire with an insulation rating of 600 volts or greater. Additionally, control wires should be kept at least 1 foot away from power wires to prevent interference and ensure proper functioning of the safety system.
How does Safe Torque Off work in the event of a safety input failure?
-If either of the safety inputs (Safety 1 or Safety 2) loses power, the gate control circuit is disabled, which activates the Safe Torque Off function. Both safety channels must be deactivated for safe operation, ensuring that the motor torque is removed without risking uncontrolled motion.
What is the difference between Coast-to-Stop and Controlled Stop actions in the context of STTO?
-Coast-to-Stop occurs when the Safe Torque Off function is activated, causing the motor to coast to a stop naturally. In contrast, Controlled Stop involves using a Master Safety Relay (MSR) with a delayed output, which gradually ramps down the motor power before activating STTO, ensuring a smoother, more controlled stop.
Why is periodic testing of the STTO feature necessary?
-Periodic testing is necessary to ensure that the Safe Torque Off function continues to work effectively and in compliance with safety standards throughout the machine's lifecycle. Regular testing helps identify any potential issues and maintains the reliability of the safety system.
What is the role of the Master Safety Relay (MSR) in the STTO setup?
-The Master Safety Relay (MSR) plays a key role in the STTO setup by providing dual-channel output and enabling controlled stop actions. It removes power from the safety terminals, thereby activating the Safe Torque Off function and ensuring a smooth, safe shutdown of the motor.
What happens when both safety inputs (Safety 1 and Safety 2) are activated?
-When both Safety 1 and Safety 2 inputs are activated, the drive's gate control circuit is enabled, and the Safe Torque Off function is deactivated, allowing the motor to operate normally. If either input loses power, the Safe Torque Off function is triggered, stopping the motor's motion.
What are the safety wiring requirements for the PowerFlex 525 when configuring Safe Torque Off?
-The wiring for Safe Torque Off on the PowerFlex 525 requires copper wire with an insulation rating of 600 volts or higher. Additionally, control wires must be kept separated from power wires by at least 1 foot to ensure that the safety function operates correctly and without interference.
How can users verify the correct functioning of the Safe Torque Off system?
-Users can verify the proper functioning of the Safe Torque Off system by checking that both Safety 1 and Safety 2 inputs are operational and testing the system using the Coast-to-Stop and Controlled Stop actions. Both safety channels must be deactivated for proper safe operation.
Outlines
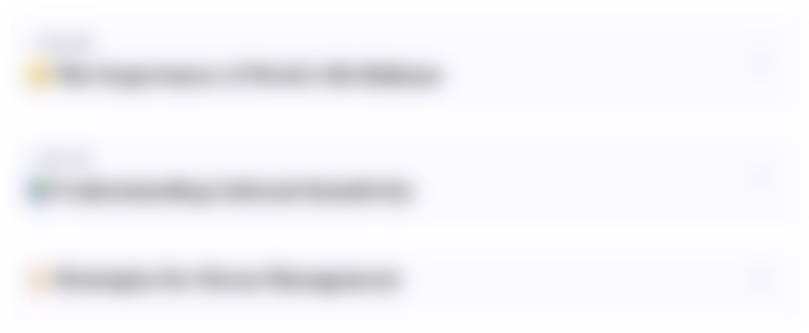
This section is available to paid users only. Please upgrade to access this part.
Upgrade NowMindmap
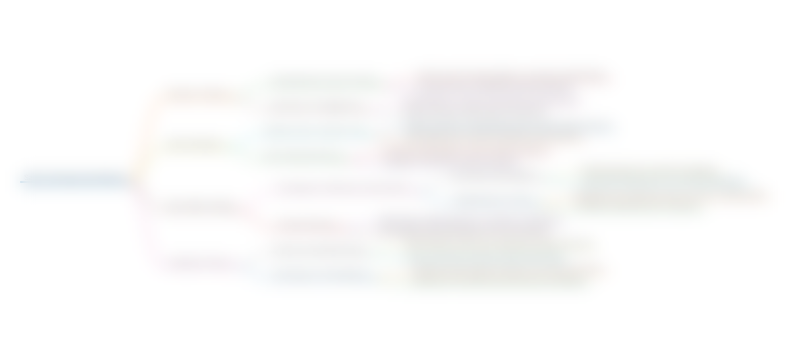
This section is available to paid users only. Please upgrade to access this part.
Upgrade NowKeywords
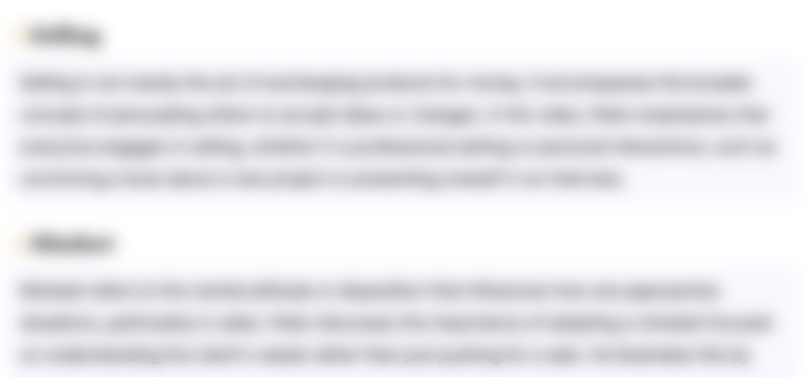
This section is available to paid users only. Please upgrade to access this part.
Upgrade NowHighlights
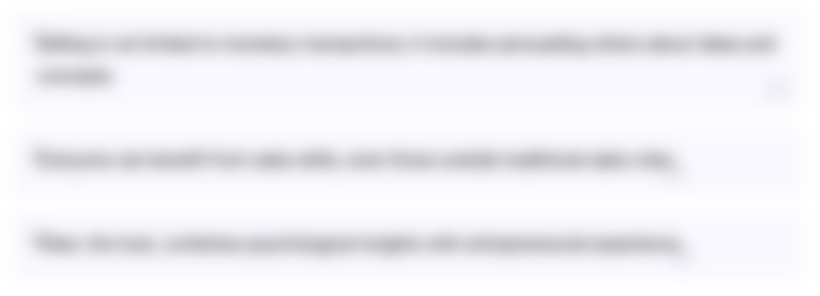
This section is available to paid users only. Please upgrade to access this part.
Upgrade NowTranscripts
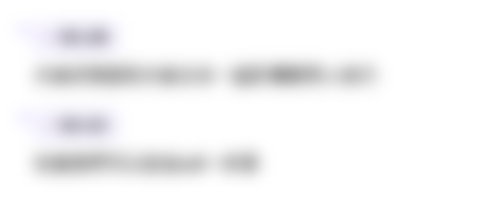
This section is available to paid users only. Please upgrade to access this part.
Upgrade NowBrowse More Related Video
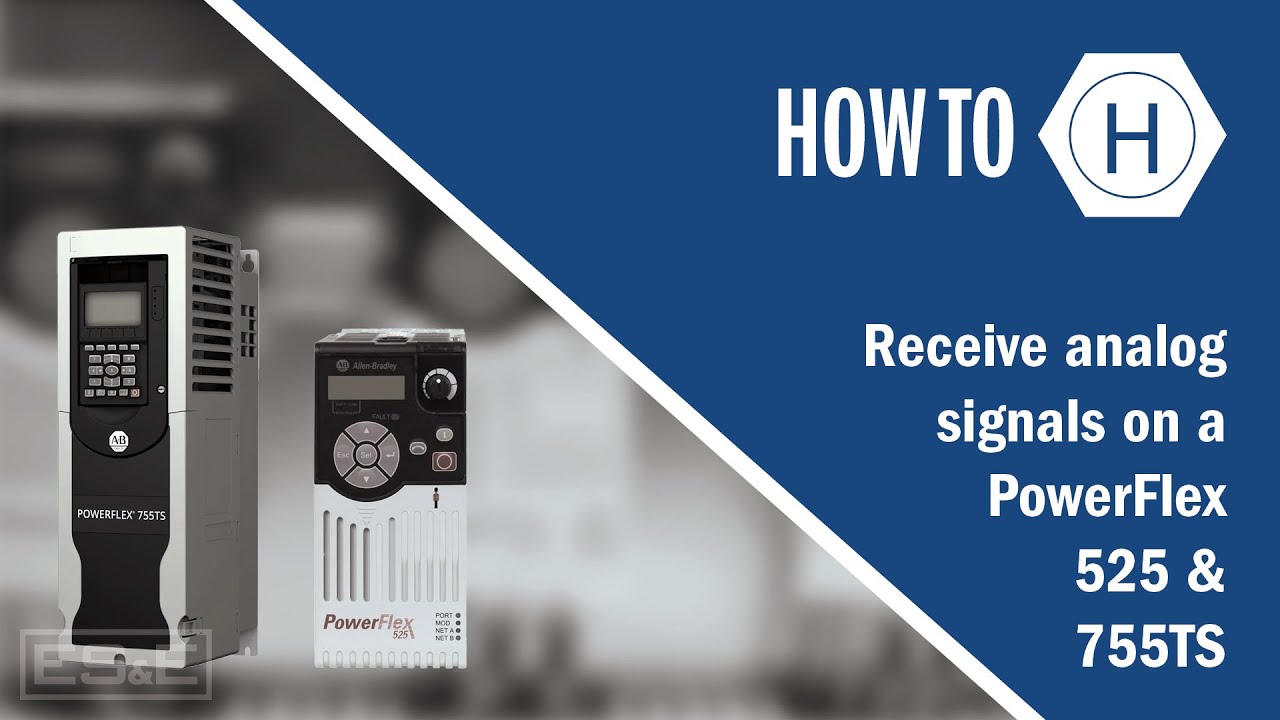
Receive Analog Signals on a PowerFlex 525 & 755TS

Understanding 755TS Part Numbers

LRS vs VFD| What is Liquid Resistance Starter| What is VFD| Function of VFD| Motor Starting Method
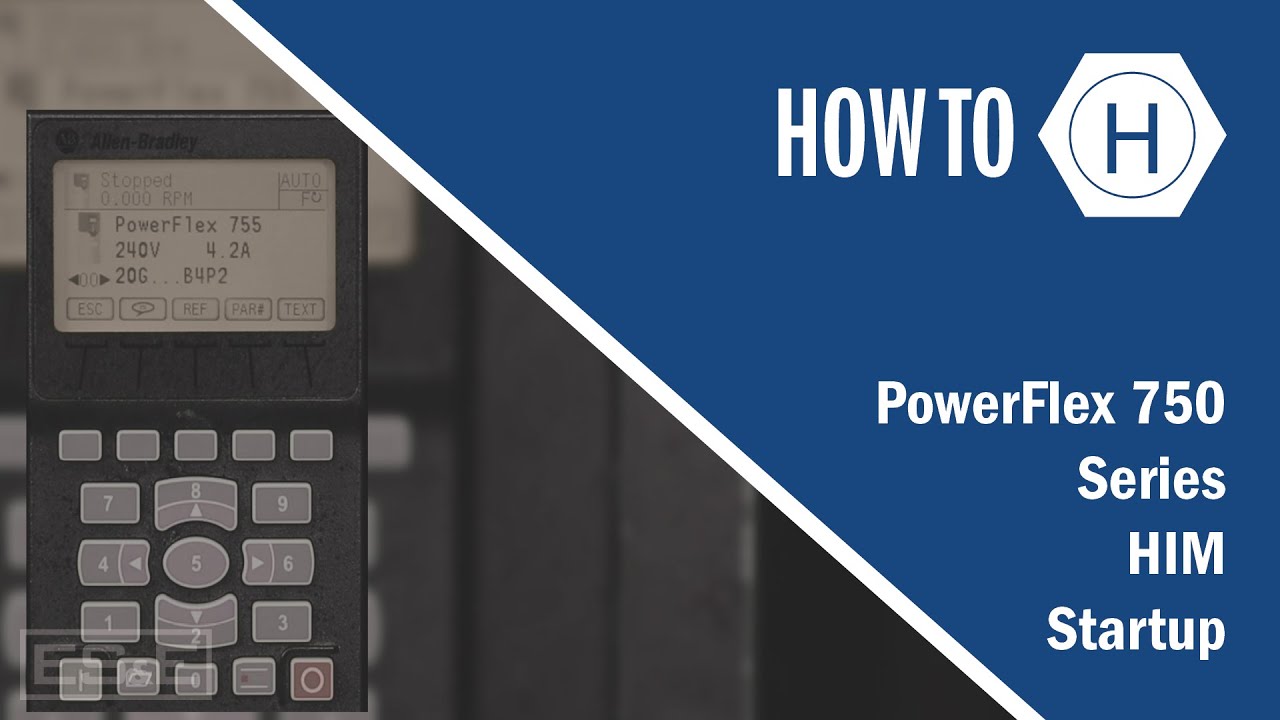
PowerFlex 750 Series HIM Startup
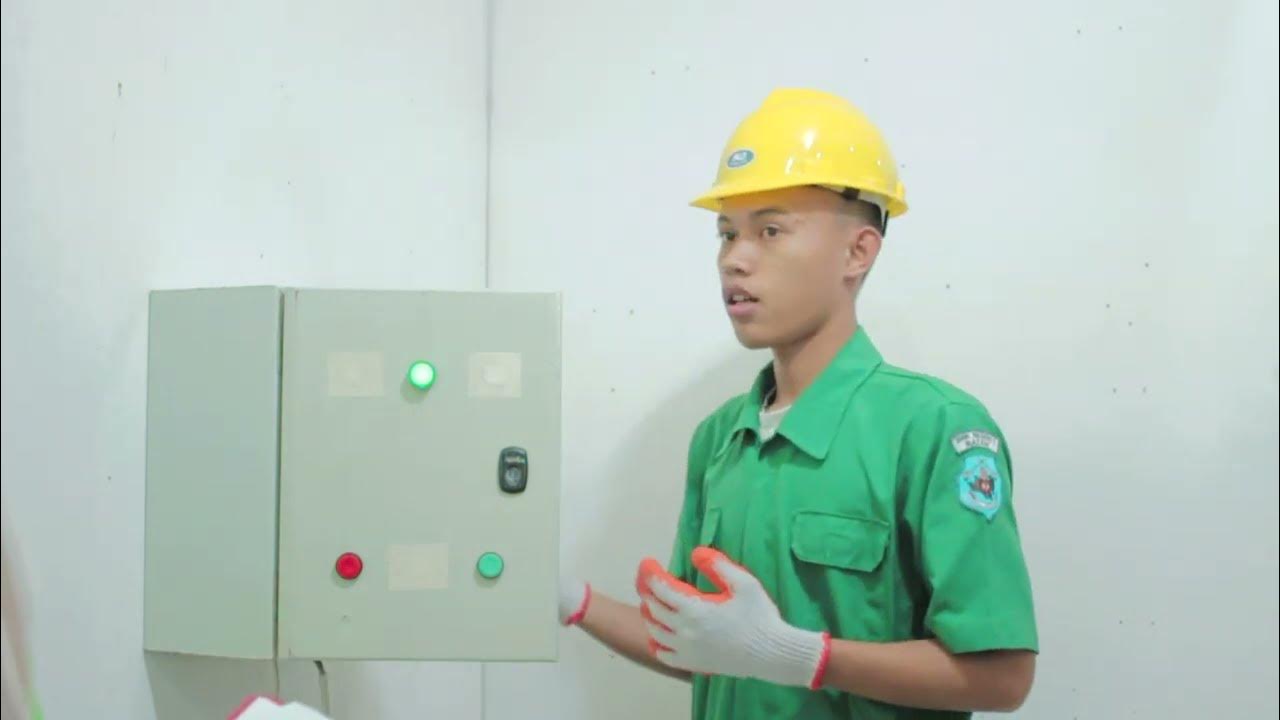
Video Pembelajaran Mengoperasikan Sistem Elektronik
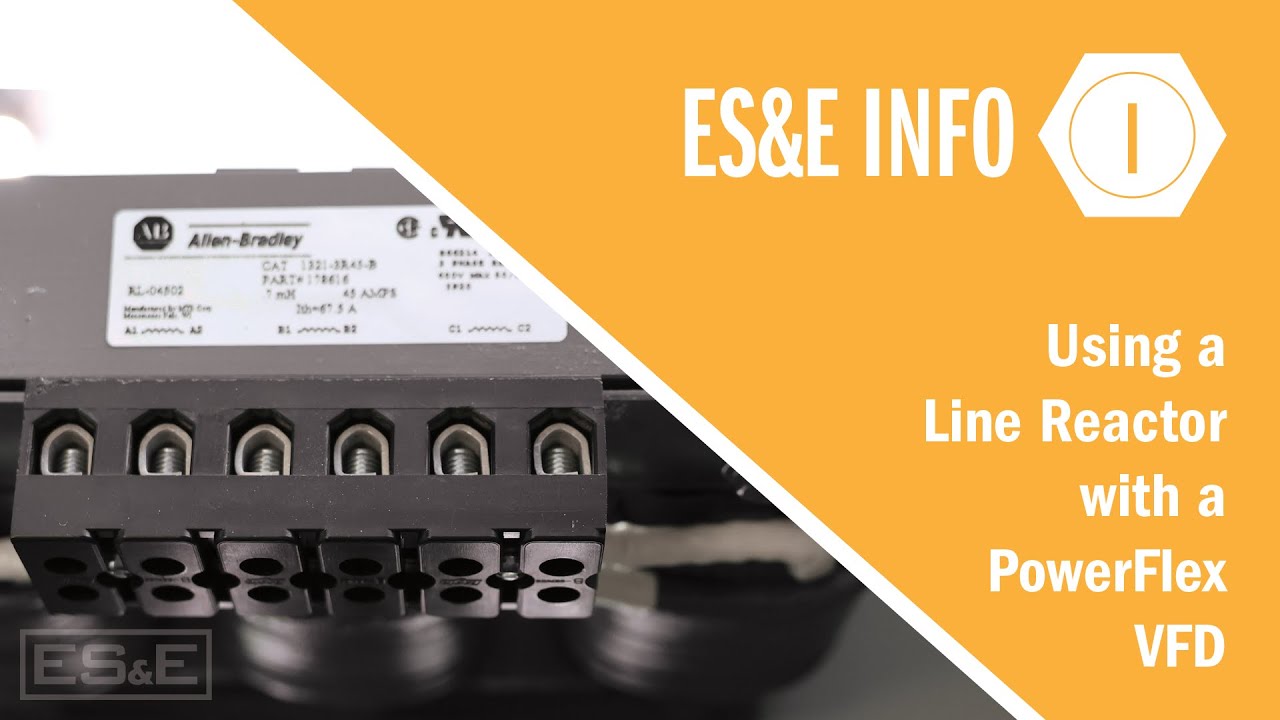
Using a Line Reactor with a PowerFlex VFD
5.0 / 5 (0 votes)