Part 2, Pabrik asam sulfat: Proses Produksi dari bahan baku sulfur Belerang
Summary
TLDRThis video explains the complex process of sulfuric acid production, covering various methods like sulfur burning, metal gas reactions, and oil refinery waste. It details the stages from sulfur melting and burning to catalytic conversion and absorption, highlighting key equipment such as furnaces, converters, and absorbers. Emphasis is placed on temperature control, heat recovery, and minimizing water content in the absorption process to avoid corrosion. The video also discusses energy efficiency and the use of steam for process heating and power generation. The goal is to provide a comprehensive understanding of industrial sulfuric acid production.
Takeaways
- 😀 Sulfur is first melted at 140°C, then combusted at 150°C in a furnace to produce sulfur dioxide (SO2).
- 😀 Heat from the combustion process is recovered through a heat recovery boiler to generate steam for heating and power generation.
- 😀 Metal of gas (sulfur concentrate with pyrite) contains sulfur that reacts with oxygen to form SO2 in the converter.
- 😀 The catalytic converter uses a high temperature of 400-600°C for the exothermic reaction between SO2 and oxygen to form sulfur trioxide (SO3).
- 😀 The heat from the catalytic converter's reaction is recovered by heat exchangers and used in other processes or to generate steam.
- 😀 The sulfur trioxide gas is absorbed into concentrated sulfuric acid (98.5%), with minimal water content (only 1.5%).
- 😀 Double contact absorbers are used in the sulfuric acid production process to ensure efficient SO3 absorption.
- 😀 Excessive water in the absorption process is avoided as it can lead to corrosion and inefficient production of sulfuric acid.
- 😀 The sulfuric acid formed in the absorber is cooled before being transferred to storage tanks.
- 😀 The overall process is designed for heat recovery, efficient use of energy, and minimizing operational costs, including preventing corrosion with low water content in the system.
- 😀 The script mentions different types of equipment such as converters, absorbers, and furnaces, highlighting their roles in sulfuric acid production.
Q & A
What are the main sources of sulfur used in sulfuric acid production?
-The main sources of sulfur for sulfuric acid production include elemental sulfur, metal ores containing sulfur (such as pyrite), and waste gases from oil refineries.
Why is sulfur first melted before combustion in the production process?
-Sulfur is melted before combustion to make it easier to handle and burn efficiently. This is done at a temperature of around 140°C to ensure smooth combustion.
How does the heat recovery system contribute to the sulfuric acid production process?
-The heat recovery system captures the heat produced during the combustion of sulfur and sulfur-containing gases. This heat is used to generate steam, which can be used for process heating or to generate electricity through steam turbines.
What is the role of the catalytic converter in sulfuric acid production?
-The catalytic converter facilitates the oxidation of sulfur dioxide (SO2) to sulfur trioxide (SO3) by introducing oxygen and using a catalyst. This reaction is exothermic, meaning it generates heat, which is then recovered.
Why is the temperature in the catalytic converter kept between 400°C and 600°C?
-The temperature range of 400°C to 600°C is optimal for the efficiency of the catalyst used in the catalytic converter. This ensures that the oxidation reaction of SO2 to SO3 occurs at maximum efficiency.
What is the function of the double contact absorber in the process?
-The double contact absorber is used to absorb sulfur trioxide (SO3) into concentrated sulfuric acid (98.5%). The SO3 reacts with water in the acid to form sulfuric acid. The double contact design improves absorption efficiency.
Why is pure sulfuric acid (98.5%) used in the absorption process instead of water?
-Pure sulfuric acid (98.5%) is used because it minimizes the risk of sulfuric acid mist formation and avoids excessive water vapor, which could complicate the condensation process. The low water content prevents corrosion and inefficiency in the equipment.
What is the significance of controlling the amount of water in the sulfuric acid absorption process?
-Controlling the water content is crucial because excess water could result in the formation of sulfuric acid mist, which is challenging and costly to condense. Too much water could also lead to corrosion in the equipment.
How is the heat produced in the catalytic converter managed?
-The heat produced in the catalytic converter is managed by using heat exchangers to recover the thermal energy. This heat is then used to generate steam, which can be utilized in other parts of the process or for power generation.
Why is the process of cooling sulfuric acid necessary before storage?
-Cooling sulfuric acid before storage is necessary to prevent excessive pressure buildup and ensure safe handling and storage. The heat from the acid is dissipated in cooling units before transferring it to storage tanks.
Outlines
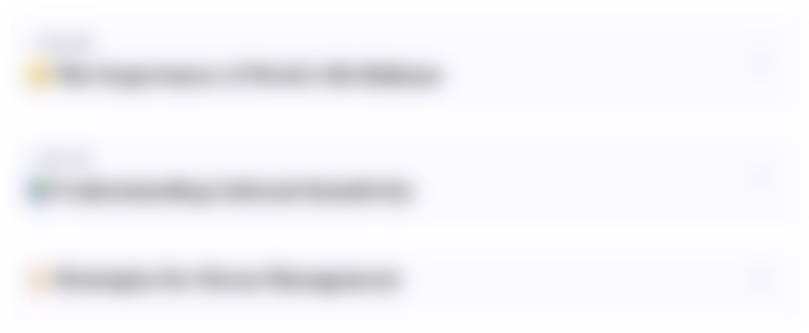
This section is available to paid users only. Please upgrade to access this part.
Upgrade NowMindmap
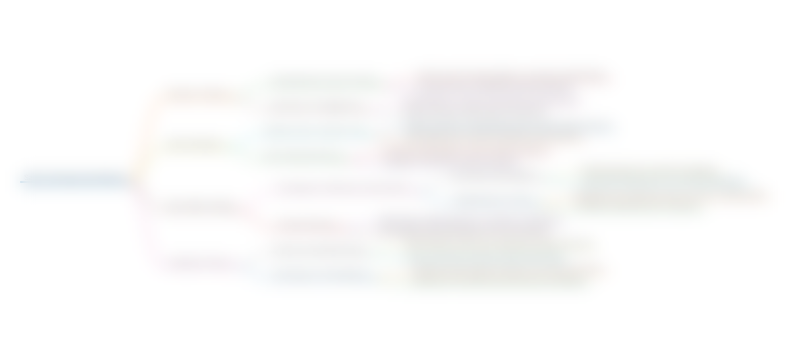
This section is available to paid users only. Please upgrade to access this part.
Upgrade NowKeywords
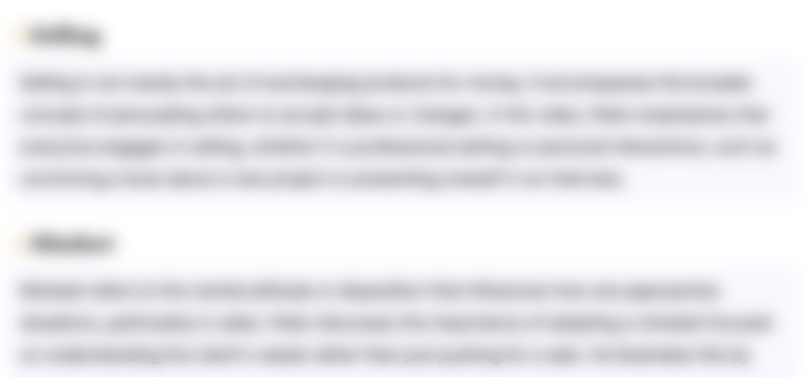
This section is available to paid users only. Please upgrade to access this part.
Upgrade NowHighlights
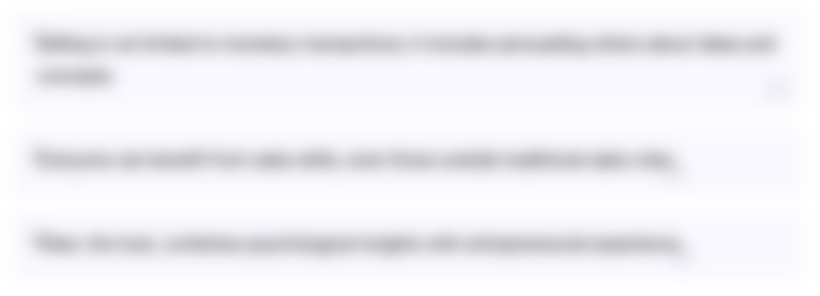
This section is available to paid users only. Please upgrade to access this part.
Upgrade NowTranscripts
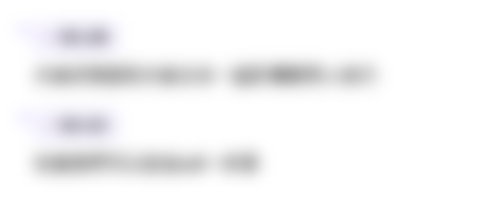
This section is available to paid users only. Please upgrade to access this part.
Upgrade NowBrowse More Related Video

Part 3, Pabrik asam sulfat: Proses Produksi dari bahan baku gas dari proses metalurgi.

3 Ways to Make Sulfur Dioxide Gas

Kimia Industri - Proses Pembuatan Asam Sulfat (Bag 1. Pendahuluan)
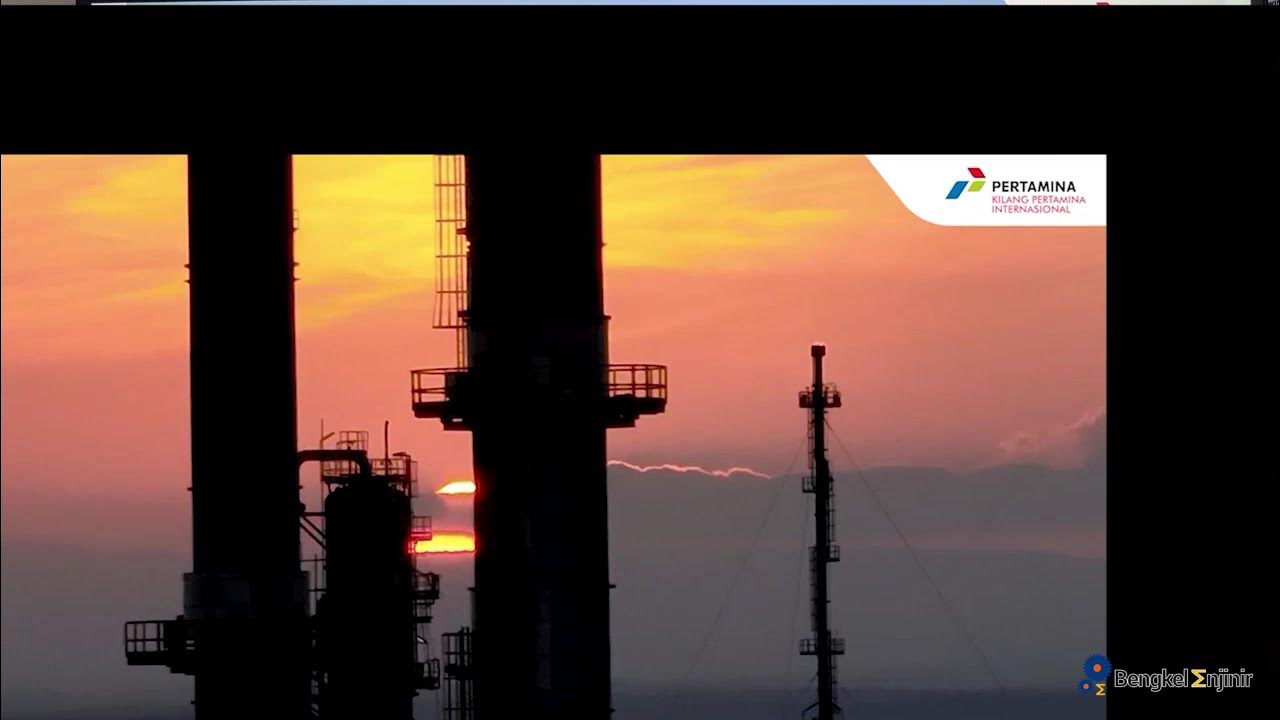
Part 4, Pabrik Asam sulfat: Proses Produksi dari bahan baku Spent Acid-limbah Kilang minyak.
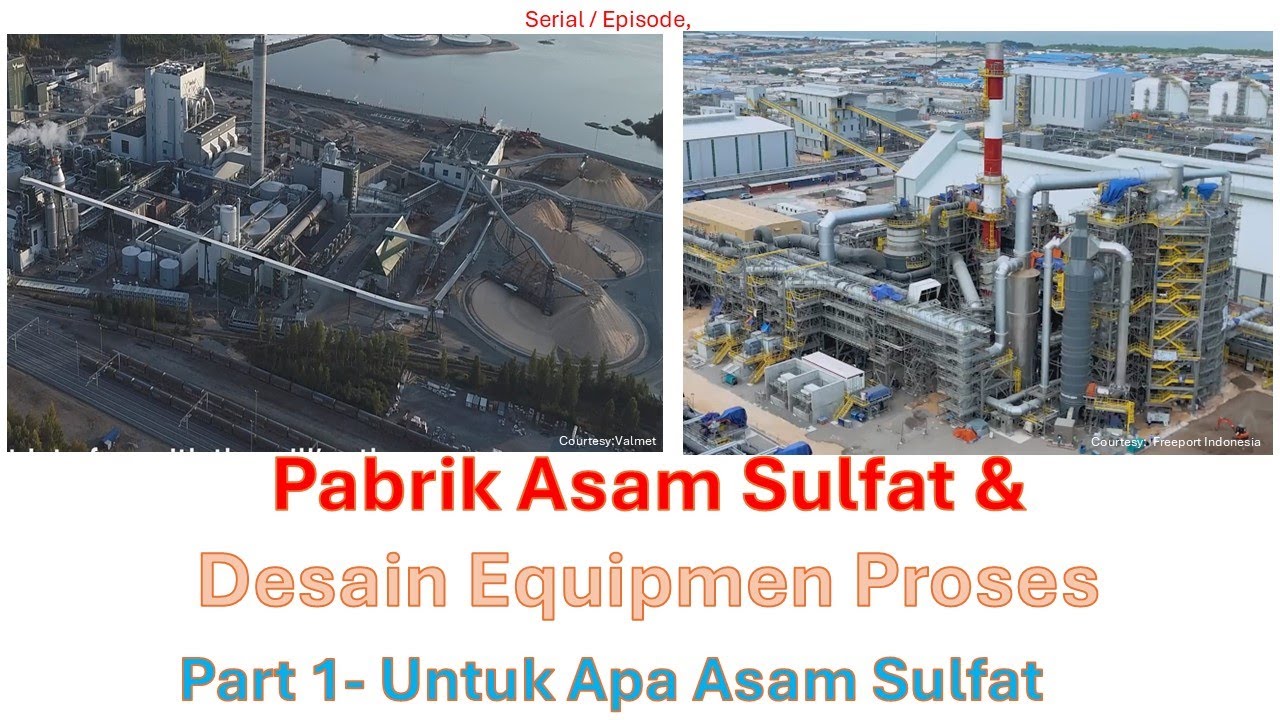
Part 1, Pabrik asam sulfat, Untuk Apa asam sulfat dipakai, dan industri yang konsumsi paling besar.
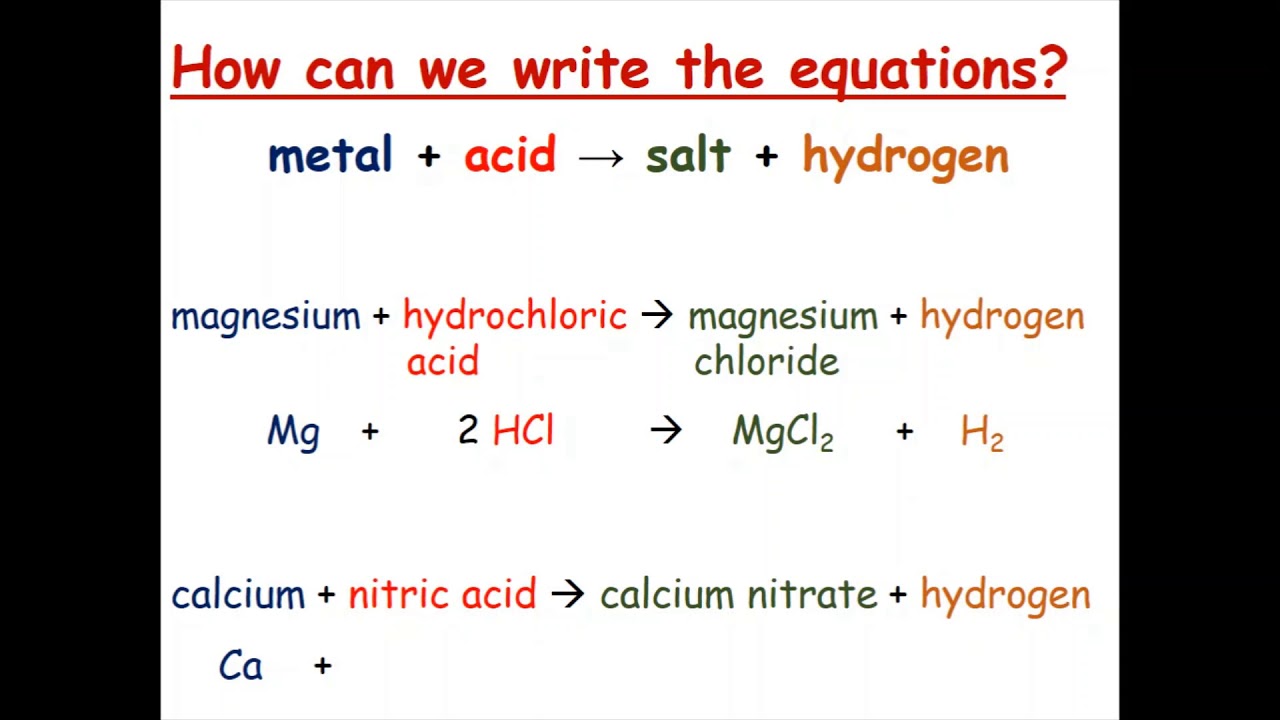
Reactions between Metals and Acids
5.0 / 5 (0 votes)