KOMPOSIT HYBRID SERAT SABUT KELAPA DAN SERAT LIDAH MERTUA BERMATRIK POLYESTER, M Zia Ulhaq F1C015053
Summary
TLDRThis video discusses the final project by Muhammad Zia ulhaq, which explores the hybrid composite material made from coconut coir fiber and snake plant (Sansevieria trifasciata) fiber, using a polyester matrix. The study examines how variations in the fiber composition affect the tensile strength and impact resistance of the composite. Through various tests, it was found that the optimal strength and elongation occurred at a 15% coconut coir and 15% snake plant fiber ratio. Additionally, the research reveals the impact toughness increases with a higher proportion of coir fiber, highlighting the potential of these natural fibers in sustainable composite materials for manufacturing applications.
Takeaways
- 😀 Hybrid composites of coconut fiber (sabut kelapa) and snake plant fiber (lidah mertua) are studied for their tensile and impact strength when embedded in polyester resin.
- 😀 Natural fibers, such as coconut fiber and snake plant fiber, are being explored as sustainable reinforcement materials in composite materials.
- 😀 The production process for the fibers involves soaking, extracting, washing, and drying both coconut fiber and snake plant fiber before using them in the composite.
- 😀 Alkalization with NaOH (6%) for 2 hours is applied to the fibers to treat them and enhance their properties for use in the composite.
- 😀 After alkali treatment, the fibers are cut into 10mm lengths to facilitate their use in composite molding.
- 😀 The composite creation process includes weighing the fibers, mixing them, and then pouring polyester resin mixed with a catalyst into molds.
- 😀 Tensile tests are conducted in a physics laboratory to measure the strength of the hybrid composites, with varying fiber volume fractions (SK and SM).
- 😀 The optimal tensile strength was observed in the composite with a 15% coconut fiber and 15% snake plant fiber ratio, reaching 48.90 MPa.
- 😀 Impact tests are carried out to assess the toughness of the composites, revealing that a higher coconut fiber content increases impact resistance.
- 😀 The study concludes that increasing coconut fiber content in the hybrid composite significantly improves both tensile and impact strength compared to a higher snake plant fiber proportion.
Q & A
What is the main objective of the final project presented in the transcript?
-The main objective of the final project is to study the tensile strength and impact resistance of hybrid composites made from coconut fiber (sabut kelapa) and snake plant fiber (lidah mertua) embedded in a polyester matrix.
Why is there a growing interest in composite materials in the modern industry?
-Composite materials are increasingly being developed in modern industries due to their environmental benefits and recyclability, which align with current technological demands for sustainable manufacturing.
What are hybrid composites, and what makes them significant in this study?
-Hybrid composites are made from two or more different types of reinforcement or matrix materials. In this study, the hybrid composite is created using natural fibers like coconut and snake plant fibers, which are combined with polyester resin, offering a unique balance of strength and environmental friendliness.
What are the key differences between coconut fiber and snake plant fiber in terms of their properties?
-Coconut fiber (sabut kelapa) has a higher tensile strength compared to snake plant fiber (lidah mertua), which has lower tensile strength but offers higher elasticity, making it more suitable for certain composite applications.
How were the fibers from the coconut and snake plant prepared for use in the composite?
-The fibers were first cleaned and then subjected to soaking processes. The coconut fibers were soaked for about seven days, and the snake plant fibers were soaked for 25 days to facilitate easier extraction. After extraction, the fibers were washed and dried before being processed further.
What chemical treatment was applied to the fibers before composite fabrication?
-The fibers were treated with an alkali solution (NaOH, 6%) for two hours, which is known as the alkali treatment. This treatment helps to improve the bonding between the natural fibers and the polyester resin by removing impurities and increasing the fiber's surface roughness.
What method was used to prepare the composite materials for testing?
-After preparing the fibers, the next step involved measuring the exact amounts of fiber and polyester resin based on volume fraction calculations. The fibers were placed into silicone molds, and polyester resin mixed with a catalyst was poured over them. The molds were then pressed and allowed to cure.
What type of tests were performed on the hybrid composite materials, and why?
-Two tests were performed on the hybrid composite materials: tensile strength testing to assess how much force the composites could withstand before breaking, and impact testing to evaluate their toughness and ability to absorb energy under impact.
What did the tensile strength testing reveal about the composite's performance?
-The tensile strength testing showed that the composite with a 15% coconut fiber and 15% snake plant fiber ratio exhibited the highest tensile strength (48.90 MPa), while the lowest strength was observed in the composite with a 5% coconut fiber and 25% snake plant fiber ratio (33.45 MPa).
What was the impact testing outcome, and how did it vary with different fiber compositions?
-The impact testing revealed that composites with a higher percentage of coconut fiber showed better impact resistance. The highest impact resistance (0.00386 Joule/mm²) was found in the composite with 25% coconut fiber and 5% snake plant fiber, while the lowest (0.00179 Joule/mm²) was in the composite with 5% coconut fiber and 25% snake plant fiber.
What conclusions were drawn regarding the performance of the hybrid composites based on the test results?
-The study concluded that the optimal hybrid composite ratio for tensile strength was 15% coconut fiber and 15% snake plant fiber, while for impact resistance, higher coconut fiber content provided better results. The study also noted that increasing the amount of coconut fiber improved both tensile strength and impact resistance, while snake plant fiber contributed more to elasticity.
Outlines
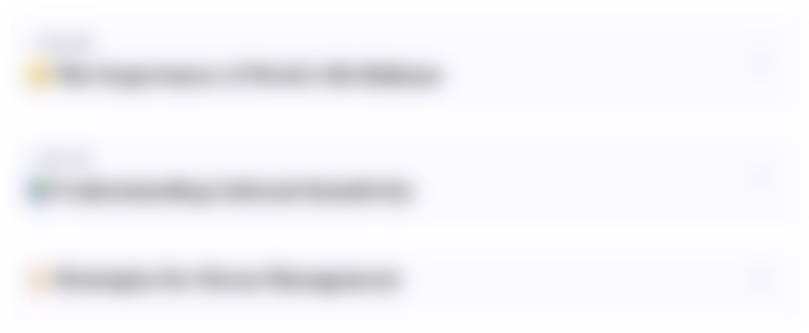
This section is available to paid users only. Please upgrade to access this part.
Upgrade NowMindmap
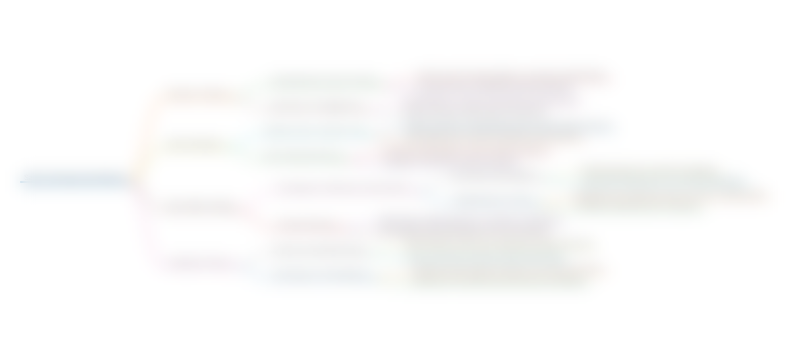
This section is available to paid users only. Please upgrade to access this part.
Upgrade NowKeywords
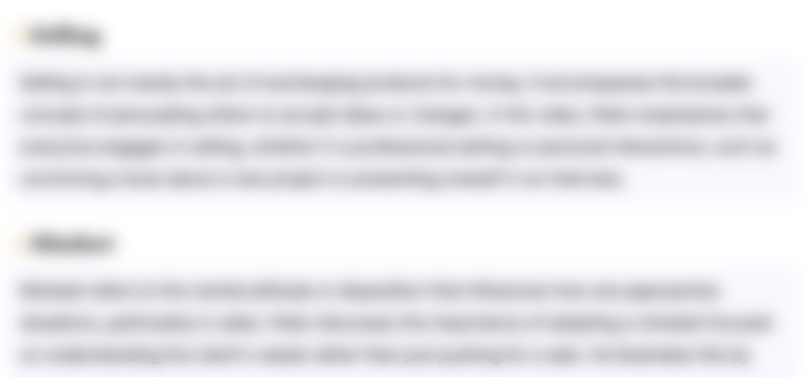
This section is available to paid users only. Please upgrade to access this part.
Upgrade NowHighlights
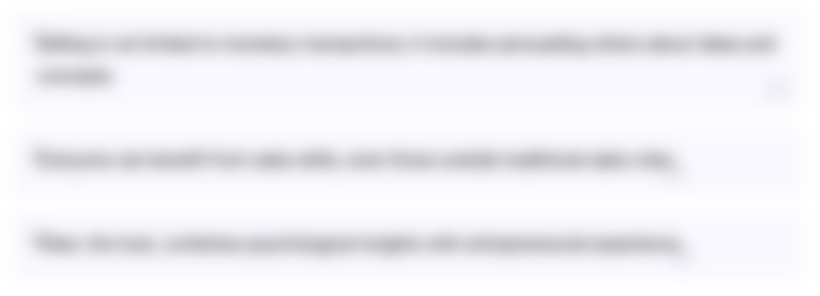
This section is available to paid users only. Please upgrade to access this part.
Upgrade NowTranscripts
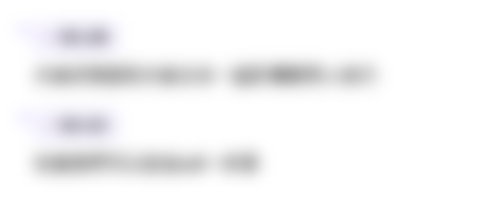
This section is available to paid users only. Please upgrade to access this part.
Upgrade NowBrowse More Related Video
5.0 / 5 (0 votes)