Hydraulic Training Series - Chapter 4 - Relief and Pressure Reducing Valves
Summary
TLDRThis presentation provides a comprehensive introduction to hydraulic relief and pressure reducing valves, essential components in hydraulic systems. It explains how relief valves protect systems by limiting maximum pressure and preventing damage, with a focus on the simple poppet-type valve and more advanced balanced piston relief valves. The pressure reducing valve is introduced as a solution for controlling pressure in specific parts of the circuit, with its own unique design. The video covers key concepts like cracking pressure, override, and the differences between the two valves, offering valuable insights for understanding and optimizing hydraulic systems.
Takeaways
- ๐ Hydraulic systems use positive displacement pumps that deliver a fixed amount of oil per cycle, which must have a designated path to prevent dangerous pressure buildup.
- ๐ Pressure relief valves are essential to prevent excessively high pressures that could damage hydraulic systems, such as rupturing lines or blowing out seals.
- ๐ A simple relief valve works by using a spring to hold a poppet in place, which opens when pressure exceeds the spring force, allowing oil to flow to the tank at a safe level.
- ๐ Cracking pressure is the minimum pressure required to unseat the poppet of a relief valve and initiate oil flow, which is a small flow compared to full pump delivery.
- ๐ Override refers to the difference between the cracking pressure and the pressure needed to pass the full pump flow through a relief valve, with larger pumps requiring more pressure to overcome override.
- ๐ A balanced piston relief valve improves on the basic relief valve design by using hydraulic pressure on both sides of a piston to reduce override, allowing it to handle higher flow rates efficiently.
- ๐ The balanced piston valve uses a small hole through the piston to balance pressures, reducing the spring load needed and minimizing override compared to a simple spring-loaded relief valve.
- ๐ Adjustable poppets in balanced piston valves allow for precise control of maximum system pressure, offering flexibility for various applications with different pressure requirements.
- ๐ Venting the relief valve by connecting it to an on/off valve or a spring-loaded poppet allows for unloading the system to save energy when not in use.
- ๐ A pressure reducing valve is used to limit pressure in specific sections of a system (e.g., a smaller clamp cylinder) while allowing the main system pressure to remain higher for other sections.
- ๐ The pressure reducing valve works by maintaining low pressure in a branch circuit using a spool and a spring. It has a balanced design with a control hole that regulates oil flow and can incorporate a check valve for reverse flow.
Q & A
What is the primary function of hydraulic relief valves?
-The primary function of hydraulic relief valves is to limit the maximum pressure within a hydraulic system to prevent damage, such as rupturing lines or blowing out seals.
What happens when a hydraulic pump's pressure exceeds the safe limits?
-When the pressure exceeds safe limits, the relief valve opens to allow oil to flow to the tank, reducing the pressure to a safe level and preventing damage to the system.
What is cracking pressure in the context of relief valves?
-Cracking pressure is the minimum pressure required to lift the poppet off its seat and allow a small amount of oil to flow through the valve. It occurs when the valve is first opened.
What is override in relation to hydraulic relief valves?
-Override refers to the difference in pressure between the cracking pressure of a relief valve and the pressure required to pass the full flow of the pump. A simple relief valve can have too much override for high-pressure systems.
How does a balanced piston relief valve work?
-A balanced piston relief valve uses hydraulic pressure along with a light spring to hold the valve closed. It has a piston with equal areas on both sides, and a balance hole allowing pressure to equalize on both sides, which reduces override and increases efficiency.
How does the design of a balanced piston valve reduce override compared to a simple relief valve?
-The balanced piston valve reduces override because it uses a light spring and hydraulic pressure to hold the valve closed. This design allows the valve to handle larger flows with minimal pressure increase, unlike a simple spring-loaded relief valve.
What is the purpose of the small hole drilled through the piston in a balanced piston relief valve?
-The small hole through the piston allows pressure to equalize between the top and bottom chambers of the piston, ensuring that the valve remains closed until the set pressure is reached.
How do pressure reducing valves differ from relief valves?
-Pressure reducing valves are normally open and close to limit the pressure in a specific branch circuit, whereas relief valves are normally closed and open to limit the overall system pressure. Pressure reducing valves also require external drainage, unlike relief valves.
What is the role of a poppet and spring in a pressure reducing valve?
-The poppet and spring in a pressure reducing valve limit the pressure in the system. The spring pushes the poppet closed when the pressure exceeds the set limit, thus reducing the pressure in the circuit.
Why might a hydraulic system need both a relief valve and a pressure reducing valve?
-A hydraulic system might need both because the relief valve limits the overall system pressure, while the pressure reducing valve can be used to control pressure in specific branches or circuits within the system, ensuring that each circuit operates within its required pressure range.
Outlines
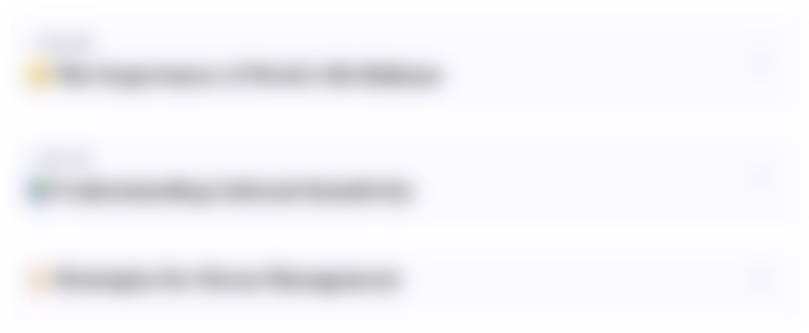
This section is available to paid users only. Please upgrade to access this part.
Upgrade NowMindmap
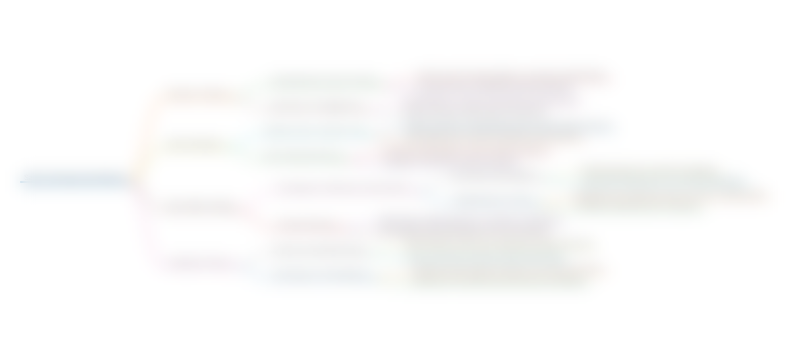
This section is available to paid users only. Please upgrade to access this part.
Upgrade NowKeywords
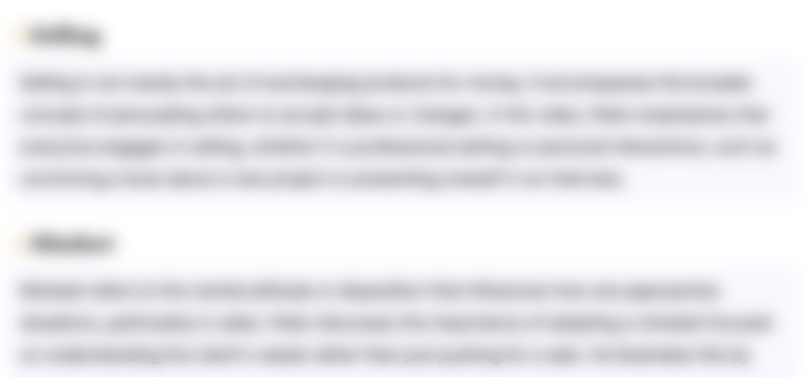
This section is available to paid users only. Please upgrade to access this part.
Upgrade NowHighlights
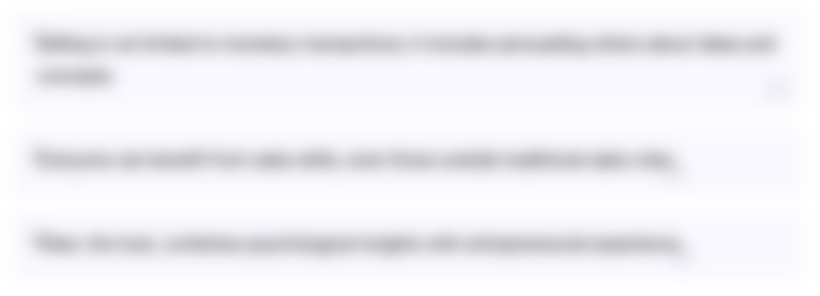
This section is available to paid users only. Please upgrade to access this part.
Upgrade NowTranscripts
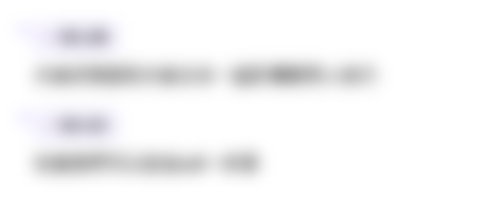
This section is available to paid users only. Please upgrade to access this part.
Upgrade NowBrowse More Related Video
5.0 / 5 (0 votes)