Filament Winding | Process Explained | Polymer Matrix Composites | ENGINEERING STUDY MATERIALS
Summary
TLDRThis video explains the filament winding process used for manufacturing polymer and ceramic matrix composites. It covers the step-by-step procedure of winding continuous filament on a rotating mandrel, with the resin either applied beforehand or sprayed on the mandrel. The process is highlighted for its high fiber content and mechanical strength, with applications in gas storage, pressure vessels, and rockets. The video also discusses winding patterns, advantages, challenges, and various industrial uses, including the production of pipes and storage tanks. The process is efficient, cost-effective, and versatile, offering a range of possibilities for different shapes and materials.
Takeaways
- 😀 Filament winding is a process used to create composite materials, such as ceramic or polymer matrix composites, for applications like gas storage and pressure vessels.
- 😀 The process involves winding continuous filaments of reinforcing material onto a rotating mandrel, which can be cylindrical or custom-shaped.
- 😀 Filaments are passed through a resin bath before being wound onto the mandrel, and a tensioner ensures the filament is wound tightly and evenly.
- 😀 There are two main types of filament winding: wet filament winding, where resin is applied to the filament, and dry filament winding, where resin is sprayed directly onto the mandrel.
- 😀 The filament winding process results in parts with high fiber content (more than 70%), leading to good mechanical properties and strength.
- 😀 A filament winding machine consists of a barrel filter, arms for winding the filament, a resin bath, and a tensioner to control the filament's tension during winding.
- 😀 The winding direction significantly impacts the strength of the final product, with helical winding offering the most strength by distributing the load.
- 😀 Filament winding can be used to create a variety of products, such as pipes, rocket motors, launch tubes, and storage tanks, for both civilian and military applications.
- 😀 The filament winding process can produce both cylindrical and non-cylindrical parts with a very low scrap rate and high pressure ratings.
- 😀 While filament winding is cost-effective and efficient, it can be complex to program, and certain shapes, especially those with sharp corners, are difficult to produce.
- 😀 A common application example is the creation of spherical components for gas storage, where a wax mold is used to create the shape, which is later removed by heating.
Q & A
What is the filament winding process used for?
-The filament winding process is used to produce composite products like pressure vessels, storage tanks, pipes, and components for rocket motors. It is particularly useful for creating high-strength, high-fiber content materials.
How does the filament winding process work?
-In the filament winding process, a continuous filament of reinforcing material is wound around a rotating mandrel. The filament is either pre-impregnated with resin (wet winding) or sprayed with resin during winding (dry winding), forming layers of composite material.
What are the two main types of filament winding?
-The two main types of filament winding are wet filament winding, where the filament is soaked in resin before winding, and dry filament winding, where resin is sprayed onto the mandrel during the winding process.
What equipment is essential in the filament winding process?
-Essential equipment in filament winding includes the mandrel, resin bath, tensioner, and barrel motor. The mandrel serves as the core for winding, the resin bath impregnates the filament with resin, the tensioner controls filament tension, and the barrel motor rotates the mandrel.
How does the winding direction affect the final product?
-The winding direction impacts the strength and properties of the final composite product. For example, helical winding provides better strength compared to unidirectional winding, as it distributes forces more evenly across the material.
What are some common winding patterns used in the filament winding process?
-Common winding patterns include helical winding (where the filament is wound in a spiral), polar winding (where the filament alternates directions at the ends of the mandrel), and normal winding (with a 90-degree rotation, similar to a hoop structure).
What are the advantages of the filament winding process?
-Advantages of filament winding include high fiber content (more than 70% by volume), low scrap rate, the ability to produce both cylindrical and non-cylindrical shapes, and cost efficiency compared to other processes like tape laying.
What are the disadvantages of filament winding?
-Disadvantages of filament winding include the complexity of programming, making it difficult for intricate shapes, and the challenge of creating sharp corners or highly detailed features.
What are the applications of filament winding?
-Filament winding is used in applications such as the manufacturing of pressure vessels, storage tanks, pipes, rocket motors, and military components, all requiring strong, lightweight, and durable materials.
How is a spherical component for gas storage made using filament winding?
-To make a spherical component for gas storage, a wax mold is used as the core. Filament coated with resin is wound around the mold. After curing, the wax is melted off, leaving the resin-coated filament, which forms the final composite structure.
Outlines
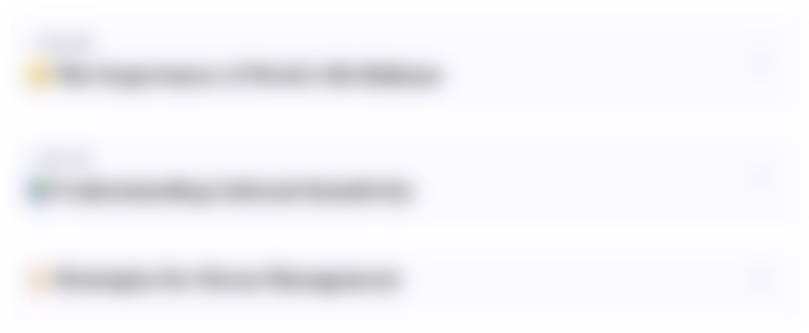
This section is available to paid users only. Please upgrade to access this part.
Upgrade NowMindmap
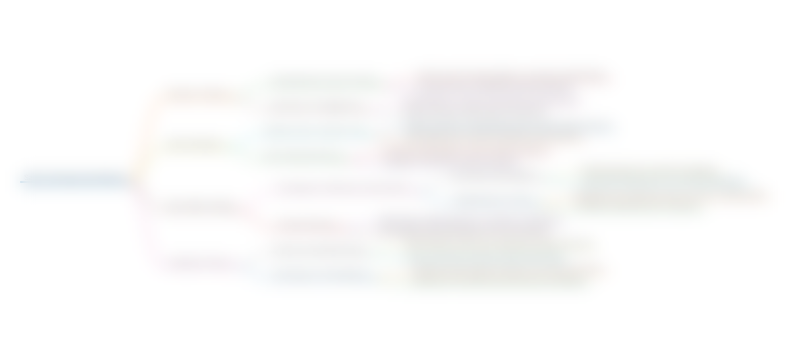
This section is available to paid users only. Please upgrade to access this part.
Upgrade NowKeywords
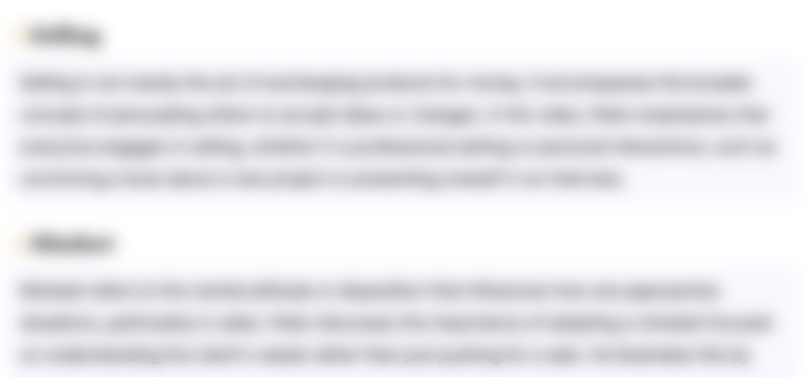
This section is available to paid users only. Please upgrade to access this part.
Upgrade NowHighlights
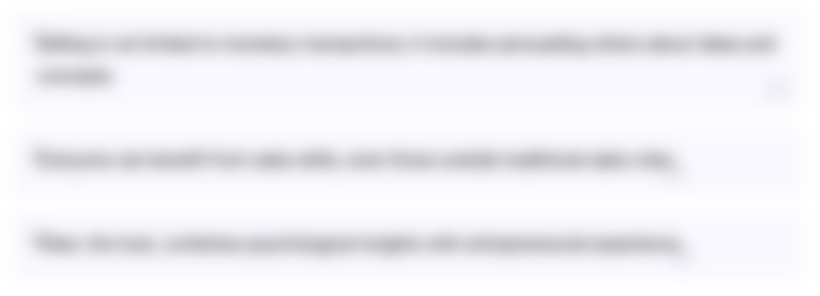
This section is available to paid users only. Please upgrade to access this part.
Upgrade NowTranscripts
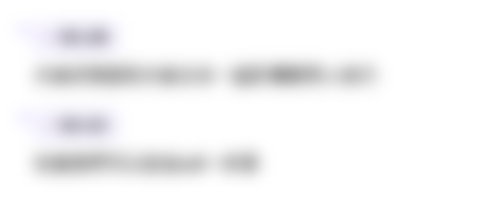
This section is available to paid users only. Please upgrade to access this part.
Upgrade NowBrowse More Related Video
5.0 / 5 (0 votes)