Capítulo 9 Facility Layout at Wheeled Coach Ambulance
Summary
TLDRThe video highlights the unique assembly process at Wield Coach, focusing on their combination of assembly line and work cell layouts. The company custom-builds ambulances through an intricate system where various departments collaborate across workstations. Each vehicle follows a precise schedule with multiple quality checks, ensuring high standards. Over time, Wield Coach has refined its layout to reduce production time, decrease costs, and enhance quality control. Their approach to operations management demonstrates how careful planning, communication, and adaptability can optimize manufacturing processes, leading to improved efficiency and reduced work-in-process inventory.
Takeaways
- 😀 Wield Coach uses a combination of assembly line and work cell layouts to optimize its manufacturing process.
- 😀 The company's layout has evolved over time, focusing on proximity, communication, and minimizing physical distance between departments.
- 😀 Reducing the distance between workstations and encouraging face-to-face interaction improves workflow and communication.
- 😀 The assembly process is highly detailed, with different departments handling specific tasks such as painting, upholstery, and electrical wiring.
- 😀 Each vehicle is custom-built, and the assembly line is carefully scheduled to ensure efficient production and meet customer needs.
- 😀 Wield Coach has reduced its throughput time from 27 days to 19 days for large model products, significantly improving efficiency.
- 😀 The company focuses on reducing work in process and inventory costs, leading to better cost management and reduced holding costs.
- 😀 Custom-built ambulances require a flexible workforce, with employees moving across different lines depending on the day's labor needs.
- 😀 By improving throughput and inventory management, Wield Coach has achieved tighter control over quality and the manufacturing process.
- 😀 The facility layout is an example of effective operations management, with a focus on material handling, capacity, and information flow.
- 😀 Wield Coach’s manufacturing process highlights the importance of operations management techniques in achieving greater efficiency and reducing costs.
Q & A
What layout system does Wiel Coach use in its assembly process?
-Wiel Coach uses a hybrid system combining assembly lines and work cells to efficiently manage the production of custom ambulances.
How has the facility layout at Wiel Coach evolved over the years?
-The layout has evolved to optimize proximity between support functions, reduce distances between workstations, and foster better communication among teams.
Why is minimizing distance between workstations important in the Wiel Coach assembly process?
-Minimizing distance helps reduce unnecessary movement, enhances communication, and improves efficiency by allowing workers to collaborate more easily.
What are the key aspects of the assembly process at Wiel Coach?
-The assembly process involves precise scheduling with departments such as sheet metal fabrication, painting, upholstery, cabinetry, and electrical work, followed by detailed inspection and testing.
What challenges does Wiel Coach face due to custom orders?
-Custom orders create challenges in scheduling and balancing production flow, as each vehicle requires different tasks and assembly processes.
How does Wiel Coach manage labor across multiple assembly lines?
-Labor is managed across multiple lines by assigning skilled workers to different lines based on the day’s production requirements, ensuring flexibility and efficiency.
What is the significance of the five assembly stations in the main line?
-The five assembly stations ensure that each vehicle undergoes a specific sequence of tasks over eight days, with dedicated time for wiring, cabinetry, trim, inspection, and final testing.
How has Wiel Coach improved its throughput over time?
-Wiel Coach reduced its throughput time by eliminating work-in-process days, cutting the time required to produce large models from 27 to 19 days, and van models from 19 to 14 days.
What are the benefits of reducing throughput at Wiel Coach?
-Reducing throughput has led to lower holding costs, reduced inventory levels, and better control over quality, making the production process more efficient and cost-effective.
What role does the layout at Wiel Coach play in operational management?
-The layout plays a crucial role in optimizing material handling, capacity, space, and information flow, which helps reduce costs and improve manufacturing efficiency.
Outlines
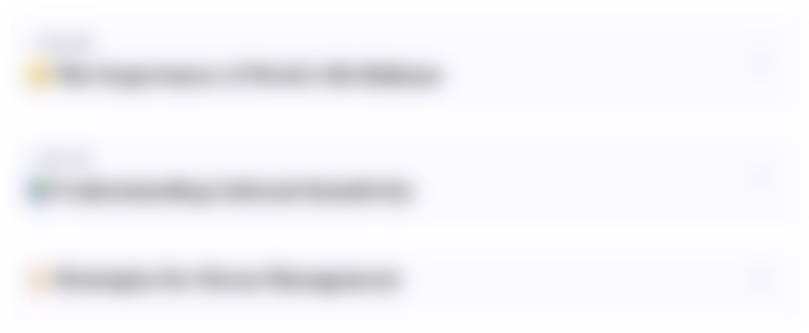
This section is available to paid users only. Please upgrade to access this part.
Upgrade NowMindmap
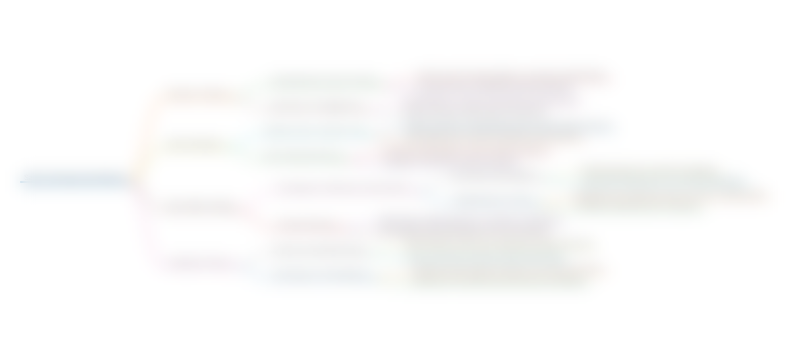
This section is available to paid users only. Please upgrade to access this part.
Upgrade NowKeywords
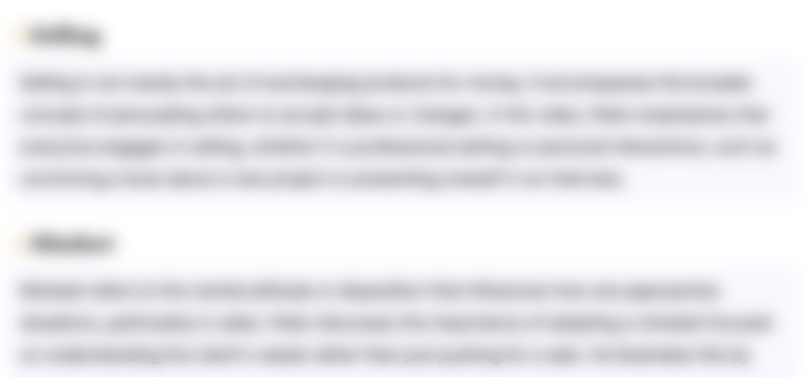
This section is available to paid users only. Please upgrade to access this part.
Upgrade NowHighlights
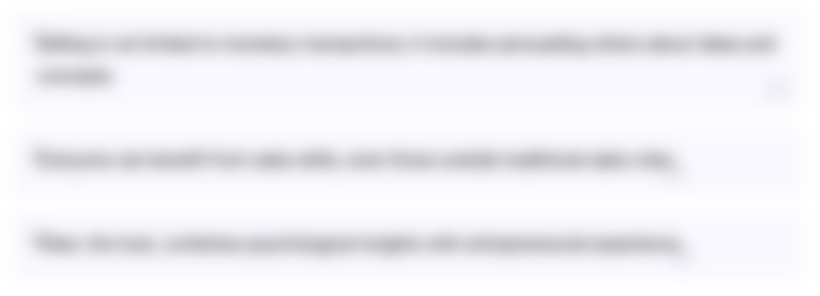
This section is available to paid users only. Please upgrade to access this part.
Upgrade NowTranscripts
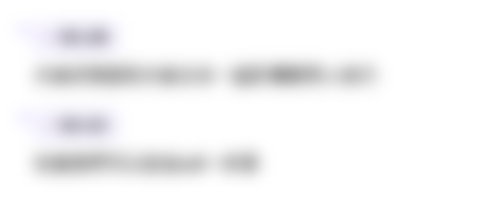
This section is available to paid users only. Please upgrade to access this part.
Upgrade NowBrowse More Related Video
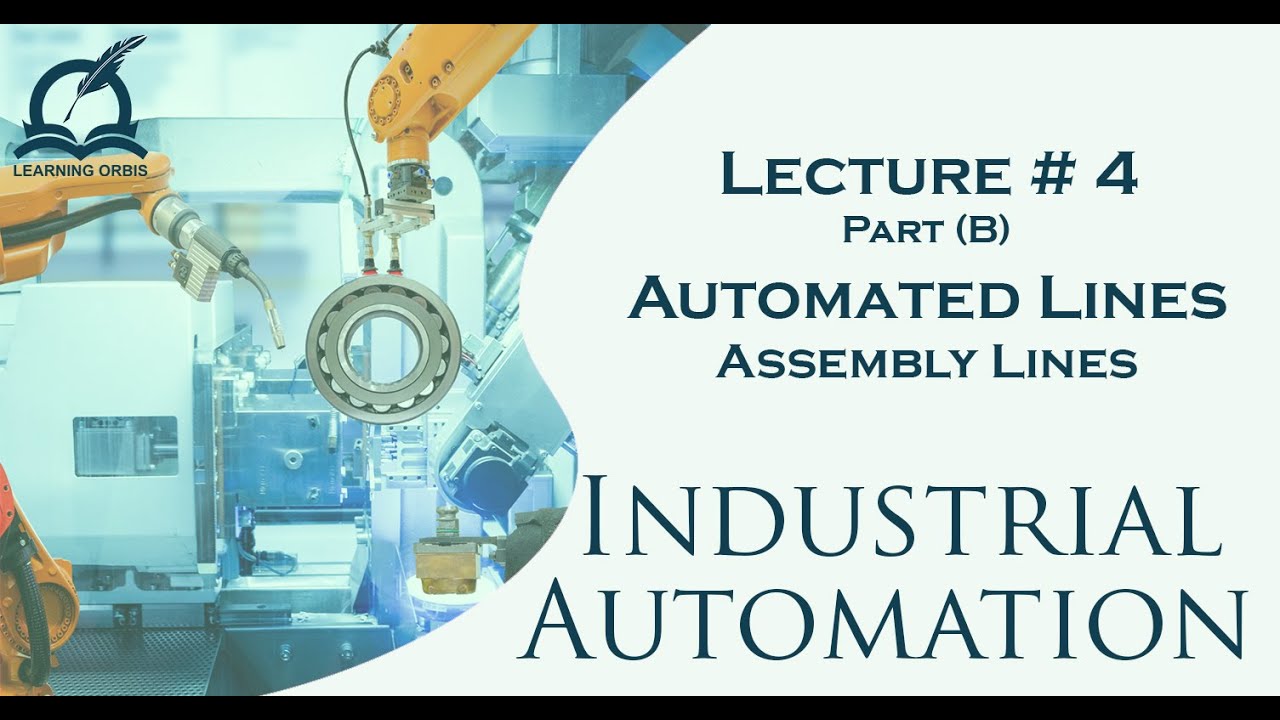
Automated Industrial Lines | Assembly Lines
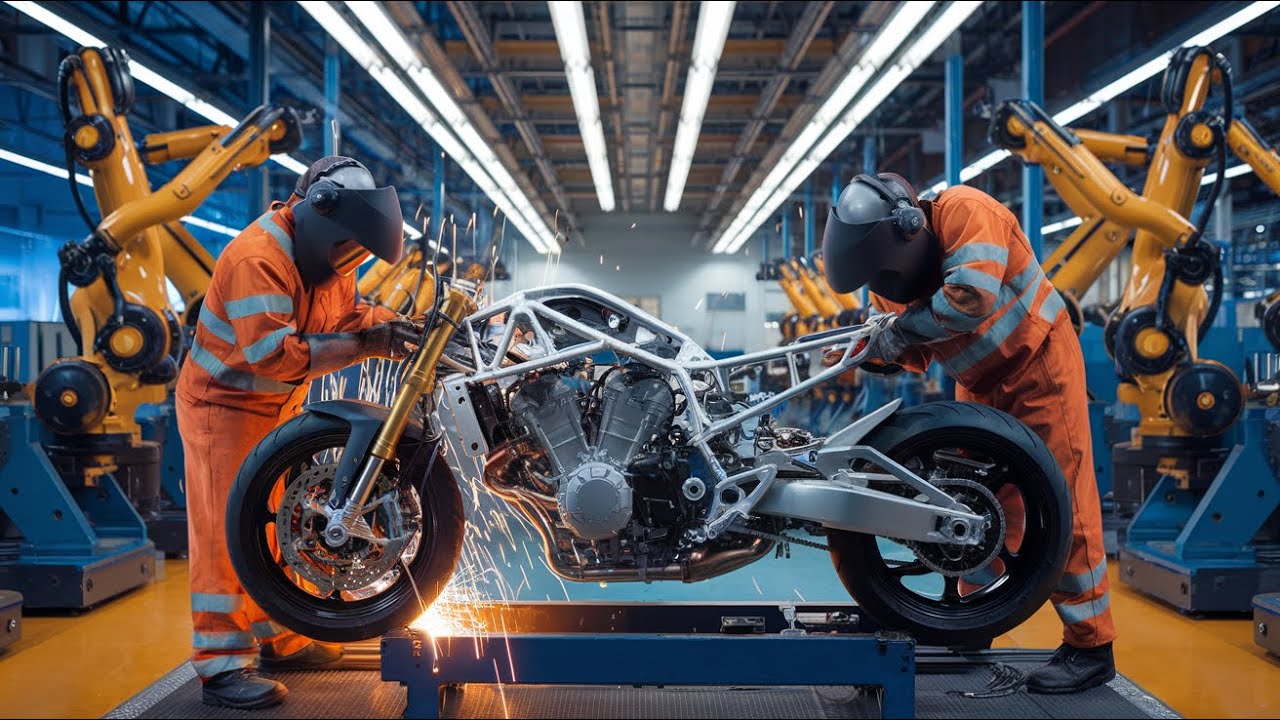
How MotorCycles Are REALLY Made
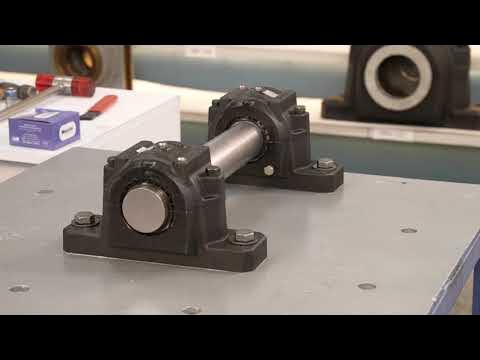
Masta Bearing Housing Assembly video of snl 511 30 1 24

Process Selection - A Review of Continuous Flow, Assembly Line, Batch Flow and Job Shop
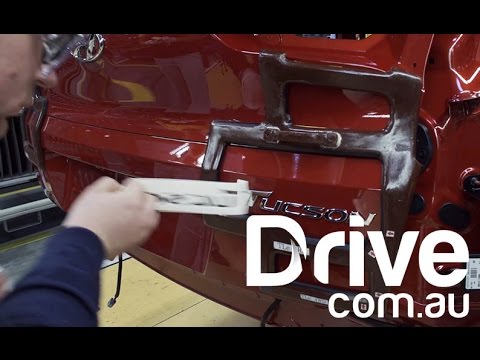
How to build a car: Inside Hyundai's Czech plant | Drive.com.au

24. OCR A Level (H046-H446) SLR5 - 1.2 Translators
5.0 / 5 (0 votes)