WSPS Safety Snippets - Control Workplace Chemical Hazards
Summary
TLDRThis video emphasizes the importance of properly managing chemical hazards in the workplace. It outlines key strategies such as identifying and understanding the chemicals in use, reducing hazardous material use, maintaining proper ventilation and equipment, and ensuring staff practice good hygiene. The video also highlights the necessity of using personal protective equipment and limiting the areas where chemicals are handled. Overall, it provides practical tips to reduce the risk of chemical exposure and ensure a safer working environment.
Takeaways
- 😀 Know what chemicals are present in your workplace and understand their associated hazards.
- 😀 Eliminate or reduce the use of hazardous materials wherever possible to improve safety.
- 😀 Maintain proper ventilation and dust capture systems to reduce airborne chemical exposure.
- 😀 Train employees to practice good personal hygiene, like washing hands, to minimize ingestion of harmful substances.
- 😀 Ensure good housekeeping and equipment maintenance to prevent chemical exposure and accidental release.
- 😀 Limit the area where chemicals are used to control and contain potential hazards.
- 😀 Use personal protective equipment (PPE) such as respirators, gloves, and eye protection when needed.
- 😀 Educate staff on the importance of chemical safety practices to reduce workplace risks.
- 😀 Regularly review safety protocols and procedures to ensure they are up-to-date and effective.
- 😀 Visit WSPS.CA for more tips and information on controlling chemical hazards in your workplace.
Q & A
What is the importance of controlling chemical hazards in the workplace?
-Controlling chemical hazards is essential for ensuring the safety and health of workers. Improper handling of chemicals can lead to harmful exposure, accidents, or long-term health issues. Implementing safety measures can reduce these risks and improve overall productivity.
How can employers identify chemical hazards in the workplace?
-Employers can identify chemical hazards by maintaining an inventory of chemicals and understanding their associated risks. This includes reading safety data sheets (SDS), labeling chemicals properly, and staying informed about the potential dangers of each substance used in the workplace.
What are some ways to eliminate or reduce hazardous materials in the workplace?
-One way to reduce hazardous materials is to substitute less dangerous chemicals when possible. Employers can also consider redesigning processes to minimize chemical usage or implement safer alternatives, thereby reducing overall exposure.
Why is proper ventilation important for controlling chemical hazards?
-Proper ventilation helps to minimize the accumulation of airborne chemicals, which can be harmful if inhaled. Ventilation systems, such as exhaust fans or fume hoods, are crucial in reducing exposure to toxic fumes and preventing respiratory issues.
What role does personal hygiene play in controlling chemical exposure?
-Good personal hygiene, such as washing hands frequently, is vital in preventing accidental ingestion of hazardous substances. It reduces the likelihood of chemicals being transferred from hands to mouth or face, which can cause harm.
What is meant by 'good housekeeping' in the context of chemical safety?
-Good housekeeping refers to maintaining a clean and organized work environment. This includes regularly cleaning up spills, storing chemicals properly, and ensuring that safety equipment is in good working order. It minimizes the chance of accidental exposure to harmful substances.
How does equipment maintenance contribute to chemical safety?
-Proper equipment maintenance ensures that safety devices, such as ventilation systems and chemical storage units, are functioning correctly. This minimizes the risk of equipment failure that could lead to chemical spills, leaks, or exposures.
Why should the area where chemicals are used be limited?
-Limiting the area where chemicals are used helps to contain potential hazards and reduce the risk of accidental exposure to workers not directly involved in handling chemicals. It also makes it easier to implement targeted safety measures in confined spaces.
What types of personal protective equipment (PPE) might be necessary for chemical safety?
-Personal protective equipment (PPE) may include items such as respirators, gloves, goggles, and protective clothing. The specific type of PPE required depends on the chemical being used and the level of exposure risk.
How can employers ensure that staff are adequately trained on chemical safety?
-Employers can provide training sessions that cover safe chemical handling, emergency procedures, and the proper use of PPE. Regular refresher courses and hands-on practice can ensure that employees are always prepared to work safely around chemicals.
Outlines
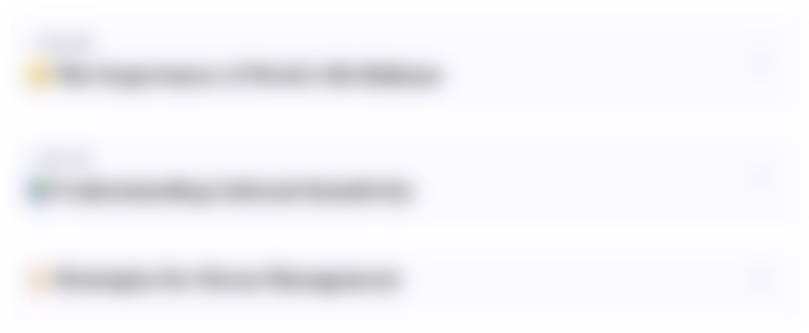
This section is available to paid users only. Please upgrade to access this part.
Upgrade NowMindmap
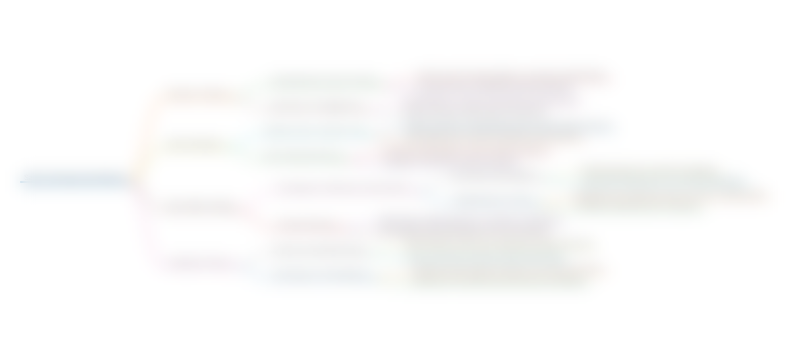
This section is available to paid users only. Please upgrade to access this part.
Upgrade NowKeywords
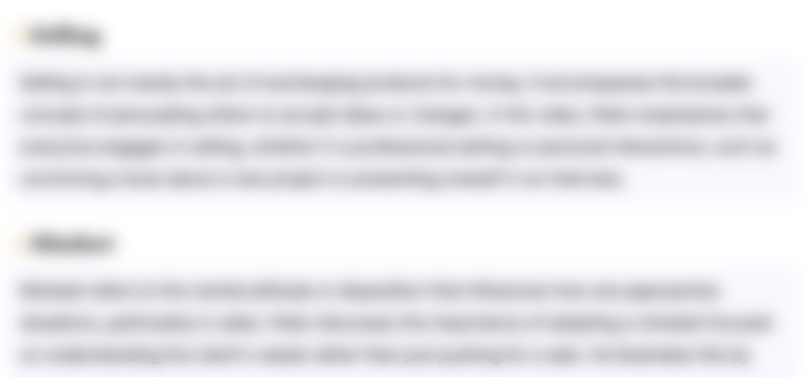
This section is available to paid users only. Please upgrade to access this part.
Upgrade NowHighlights
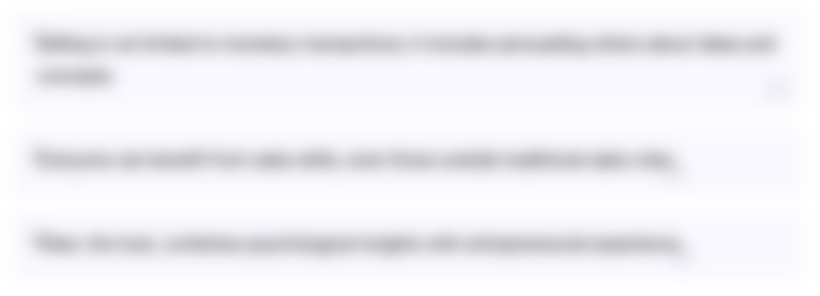
This section is available to paid users only. Please upgrade to access this part.
Upgrade NowTranscripts
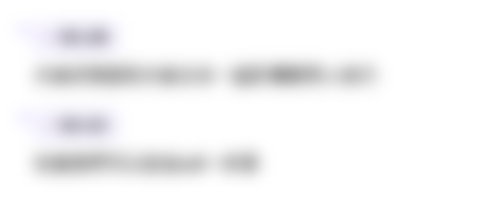
This section is available to paid users only. Please upgrade to access this part.
Upgrade Now5.0 / 5 (0 votes)