Strategi Proses Produksi
Summary
TLDRThis lecture delves into production management strategies, focusing on process design and customization. It explores Dell's use of mass customization for competitive advantage, offering personalized computers quickly and cost-effectively. The script also examines various production strategies—process-focused, repetitive-focused, product-focused, and mass customization—each suited for different manufacturing needs. In addition, it highlights strategies used in the service sector, such as separation, modularization, automation, and scheduling, to improve efficiency and customer satisfaction. The lecture offers insights into the flexibility, cost control, and challenges associated with each strategy, providing a comprehensive guide for effective production management.
Takeaways
- 😀 Dell's direct-to-consumer sales model and mass customization strategy have helped it achieve competitive advantage by eliminating distribution channels and reducing costs.
- 😀 The definition of **production process strategy**: A company's approach to transforming resources into goods or services that meet customer specifications within cost and managerial constraints.
- 😀 There are four main types of production process strategies: process-focused, repeat-focused, product-focused, and mass-customization.
- 😀 **Process-focused strategy** is ideal for low-volume, high-variety production. It organizes facilities around specific processes to cater to customized products, as seen in job shops and workshops.
- 😀 **Repeat-focused strategy** involves modular production, where components or modules are pre-assembled and then combined into finished products, common in industries like automobile manufacturing.
- 😀 **Product-focused strategy** is suited for high-volume, low-variety production, as seen in continuous processes like cement, glass, and paper manufacturing. It requires high fixed costs but low variable costs.
- 😀 **Mass-customization strategy** enables companies to produce customized products quickly and at low cost, ensuring efficiency while meeting individual customer demands.
- 😀 In the service industry, process strategies include **separation**, **modularization**, **automation**, **scheduling**, and **training** to improve efficiency and better serve customer needs.
- 😀 **Separation strategy** involves segmenting customer interactions, such as having different service personnel for account opening, credit processing, and cashiering in a bank, to streamline processes.
- 😀 **Automation** and **scheduling** strategies help businesses reduce human labor and improve service delivery, such as in automated teller machines (ATMs) or scheduled flight ticket sales.
- 😀 The production process also requires good management of **pre-production**, **quality control**, and **distribution** to ensure products reach consumers in optimal condition, as illustrated in the food industry and manufacturing processes.
Q & A
What is the primary focus of the lecture in the provided transcript?
-The primary focus of the lecture is on different production process strategies, including process focus, repetitive focus, product focus, and mass customization, as well as their implications for manufacturing and service industries.
How does Dell Computer implement mass customization in its production process?
-Dell Computer uses mass customization by allowing customers to configure personal computers according to their preferences, which are then produced on-demand with low cost and quick turnaround times. This approach eliminates the need for a distribution chain and reduces the final product cost.
What are the key characteristics of a 'process focus' production strategy?
-A process focus strategy is organized around processes rather than specific products. It is typically used in environments with low production volume but high variety, like job shops or specialized manufacturing facilities. It provides flexibility in production but is less efficient in terms of cost per unit.
What are some industries where 'repetitive focus' production strategies are commonly used?
-Repetitive focus strategies are commonly used in industries where products are assembled using predefined modules or components, such as the automotive industry (e.g., car manufacturing) and the household appliance industry (e.g., washing machines, refrigerators).
What distinguishes a 'product focus' strategy from other production strategies?
-A product focus strategy centers around high-volume, low-variety production. Facilities are organized around producing large quantities of a single product or a small group of similar products. This strategy is seen in industries like glass manufacturing, cement production, and paper mills.
What are the main benefits of a mass customization strategy?
-The benefits of mass customization include the ability to provide highly personalized products quickly and efficiently, meeting specific customer demands without sacrificing the economies of scale typically associated with mass production.
What are the advantages and disadvantages of 'process focus' in manufacturing?
-Advantages of process focus include high flexibility and the ability to produce a variety of products. However, disadvantages include higher variable costs, the need for highly skilled labor, and difficulty in planning and controlling production due to the variety of processes involved.
What role does customer feedback play in Dell's manufacturing strategy?
-Customer feedback plays a critical role in Dell's strategy by allowing the company to rapidly adjust its production based on demand and customer preferences. This helps Dell stay competitive and responsive to market changes.
How does 'mass customization' differ from traditional mass production?
-Mass customization differs from traditional mass production by allowing customers to personalize their products while still maintaining the efficiency of mass production techniques. In traditional mass production, products are made in large volumes with little to no customization.
What are the key strategies to improve service process efficiency, as discussed in the lecture?
-The key strategies to improve service process efficiency include separation of tasks, modularization, automation, scheduling, and employee training. These techniques help streamline service delivery and accommodate customer needs more effectively.
Outlines
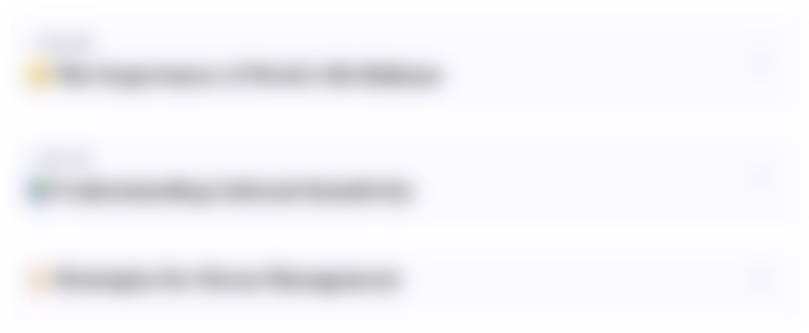
This section is available to paid users only. Please upgrade to access this part.
Upgrade NowMindmap
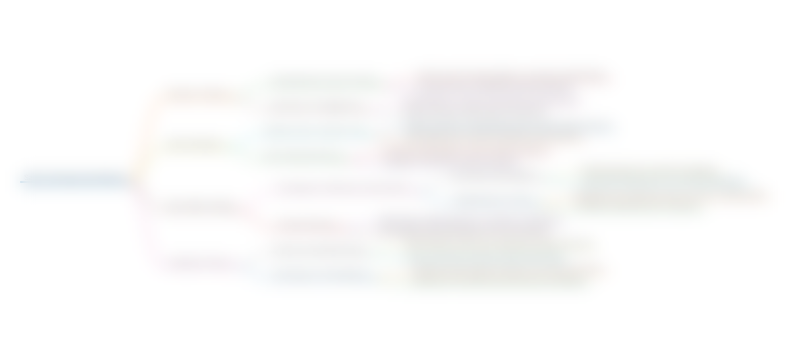
This section is available to paid users only. Please upgrade to access this part.
Upgrade NowKeywords
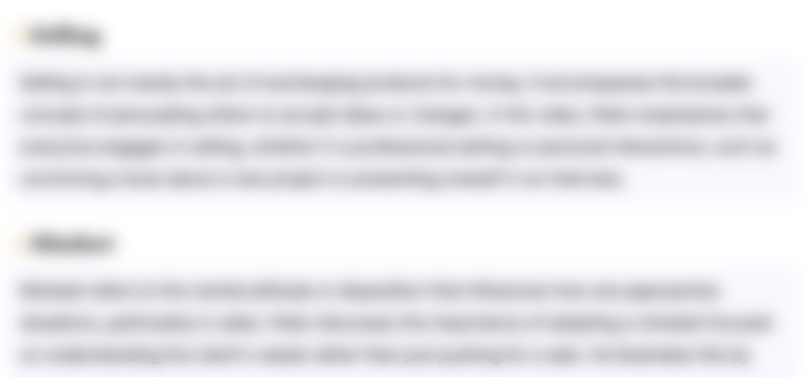
This section is available to paid users only. Please upgrade to access this part.
Upgrade NowHighlights
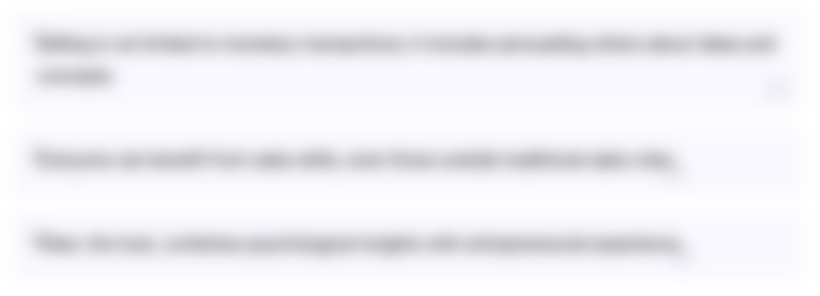
This section is available to paid users only. Please upgrade to access this part.
Upgrade NowTranscripts
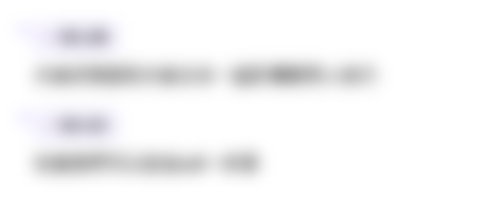
This section is available to paid users only. Please upgrade to access this part.
Upgrade Now5.0 / 5 (0 votes)