6 Best Safety Stock Formulas: Calculation & Examples in Excel (Full TUTORIAL)
Summary
TLDRIn this video, the speaker discusses effective inventory management strategies, emphasizing the importance of aligning safety stock levels with service level targets. They highlight the limitations of using a blanket 90% service target, advocating for a more nuanced approach that considers demand profiles and seasonality through methods like ABC-XYZ classification. The speaker recommends starting with simpler models for low-volume items and stresses the necessity of high-quality data for more complex analyses. Ultimately, viewers are encouraged to download accompanying tools, track their performance, and refine their strategies for optimal inventory levels.
Takeaways
- ๐ Understanding that a 90% service level is a mathematical average, not a guarantee of performance.
- ๐ Acknowledging the limitations of normal distribution models for low sales and the impact of seasonality on inventory risk.
- ๐ Utilizing ABC classification to set varied service targets based on product importance and sales variability.
- ๐ Considering alternative methods for safety stock calculations, like binomial and Poisson distributions, while keeping it simple.
- ๐พ Emphasizing the importance of high-quality data over complex methodologies for effective inventory management.
- ๐ Regular performance tracking is essential for adjusting safety stock levels and maintaining a balance between service level and inventory costs.
- ๐๏ธ Implementing an action plan: download tools, select appropriate methods, and compare safety stock values for optimization.
- ๐ Recommending continuous calculation of performance deviations to ensure effective inventory management.
- ๐งโ๐ซ Encouraging viewers to subscribe for more resources, tools, and workshops focused on inventory optimization.
- ๐ Highlighting the need for proactive inventory management to reduce shortages and improve cash flow.
Q & A
What is the main focus of the video?
-The video primarily focuses on optimizing safety stock and inventory levels through various methodologies and data analysis.
Why is a 90% service level not always realistic?
-A 90% service level often does not account for unforeseen events that can impact service delivery, making it essential to simulate and track actual performance.
What challenges exist when using normal distribution for demand forecasting?
-Normal distribution may not be suitable for products with very low sales volumes or for those experiencing significant seasonal fluctuations, leading to potential underestimation of extreme sales scenarios.
What is ABC classification in inventory management?
-ABC classification categorizes inventory into three groups: A, B, and C, based on importance and sales volume, allowing for tailored service levels for different products.
How can machine learning improve inventory management?
-Machine learning can simulate different models and tailor classifications for each item, enhancing inventory optimization and reducing manual effort, although companies need to first ensure data quality.
What is the recommended approach for businesses with low inventory volumes?
-For businesses with low volumes, simpler methods like the average or min-max can be effective, whereas businesses with higher volumes may benefit from using normal distribution.
Why is data quality crucial in selecting inventory management methods?
-Data quality is vital because unreliable data can lead to ineffective inventory management, making it difficult to accurately assess lead times and forecast demand.
What action plan does the speaker suggest for improving safety stock management?
-The speaker suggests downloading relevant Excel tools, selecting the appropriate inventory method, comparing results with current safety stock values, and regularly tracking performance using key performance indicators (KPIs).
What does the speaker mean by the balance point between service level and inventory level?
-The balance point refers to finding an optimal trade-off where service levels meet customer demand without excessively increasing inventory costs.
What additional resources does the speaker offer for further learning?
-The speaker encourages viewers to subscribe for more educational content, offers workshops, KPIs, and tools designed to help master inventory management.
Outlines
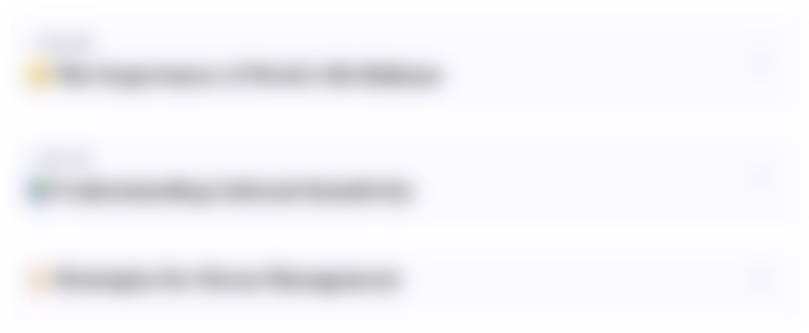
This section is available to paid users only. Please upgrade to access this part.
Upgrade NowMindmap
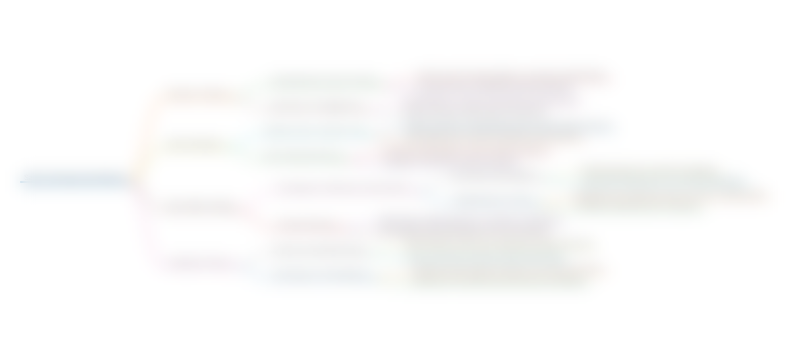
This section is available to paid users only. Please upgrade to access this part.
Upgrade NowKeywords
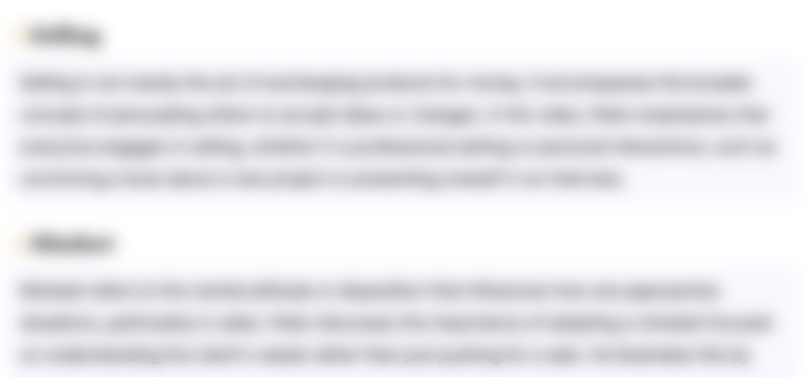
This section is available to paid users only. Please upgrade to access this part.
Upgrade NowHighlights
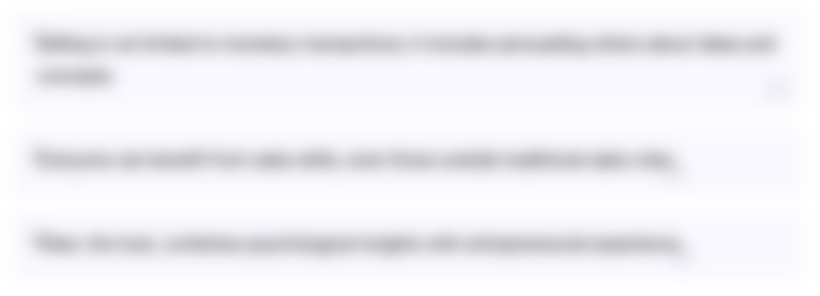
This section is available to paid users only. Please upgrade to access this part.
Upgrade NowTranscripts
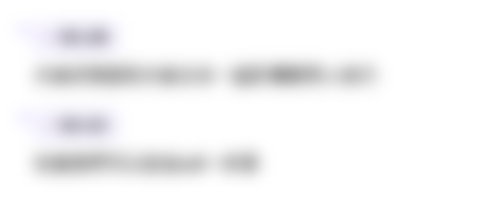
This section is available to paid users only. Please upgrade to access this part.
Upgrade Now5.0 / 5 (0 votes)