Example: when to use BPM (Business Process Management)
Summary
TLDRJohn, the CEO of a multinational textile factory, faces declining income and rising costs, compounded by inefficient internal administration and excessive documentation. The story follows Paul, a long-time wholesale customer, as he navigates a convoluted order process fraught with delays and poor communication. Despite placing an order, Paul's frustration grows as he encounters a lack of updates and missed deadlines, ultimately jeopardizing their business relationship. This scenario highlights the critical need for streamlined processes and effective communication, suggesting that without an automated system, businesses risk significant productivity losses.
Takeaways
- 📉 John's textile factory is facing declining income while costs and performance times are increasing.
- 💸 Excessive borrowing from banks indicates financial instability within the company.
- 🗃️ Inefficient internal administration is leading to an overwhelming amount of documentation.
- 🔍 The company struggles with understanding its operational problems, hindering effective solutions.
- 📦 The sales and supply chain process involves several stages, from order placement to delivery.
- 👔 Paul, a long-time customer, experiences delays and communication issues with his orders.
- 📅 Communication breakdowns between departments result in significant delays in order fulfillment.
- 🔄 The production process is slowed due to low order volumes, leading to inefficient machinery use.
- ⚠️ Lack of internal and external communication is a critical issue impacting customer satisfaction.
- 🚀 Implementing an automated business process management system could enhance efficiency and productivity.
Q & A
What is the main issue that John, the CEO of Tex Factory, is facing?
-John is experiencing a decline in income while costs and performance times are increasing, leading to the need to borrow money from the bank.
What specific problem is causing excessive documentation within Tex Factory?
-The excessive documentation is a result of inefficient internal administration, which complicates the management processes.
How does Paul, the wholesale clothing business owner, place an order with Tex Factory?
-Paul consults the Tex Factory's product catalog, selects the items and sizes, and then sends an email to Tex Factory requesting the cost and delivery time.
What complication arises after Matt, the sales manager, returns from vacation?
-Matt discovers that one of the products Paul requested has been discontinued, potentially due to not receiving the latest catalog.
What is the role of the warehouse manager in the ordering process?
-The warehouse manager checks the stock availability for the requested items and informs Matt about the items that are in stock and those that need to be manufactured.
What challenge does the production manager face when contacted by Matt?
-The production manager must contact two factories in different countries to initiate production, which complicates the timeline for fulfilling the order.
What does Paul experience after placing his order, and how does it affect his business?
-Paul experiences delays and a lack of communication regarding his order status, leading to financial losses and a decision not to continue working with Tex Factory.
What are some key issues highlighted in Tex Factory's process management?
-Key issues include a lack of internal and external communication, information delocalization, the use of isolated programs, lack of process control, and excessive time spent managing tasks.
What does the script suggest as a solution to Tex Factory's inefficiencies?
-The script suggests implementing a technological solution, such as an advanced software portal, to automate business processes and improve productivity.
How do the identified problems in Tex Factory's management affect businesses of different sizes and sectors?
-The problems multiply with a higher number of daily processes, impacting businesses of all sizes and sectors by increasing errors, costs, and reducing productivity.
Outlines
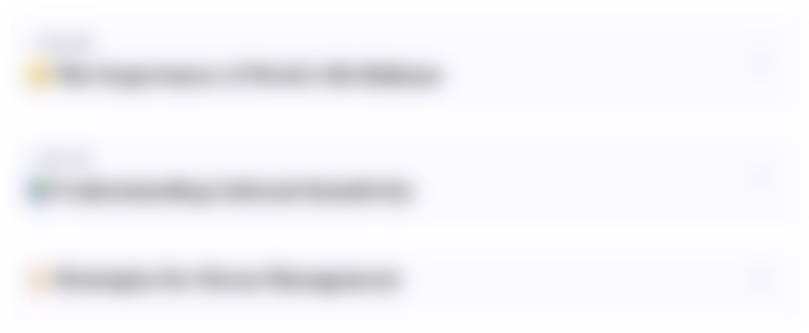
This section is available to paid users only. Please upgrade to access this part.
Upgrade NowMindmap
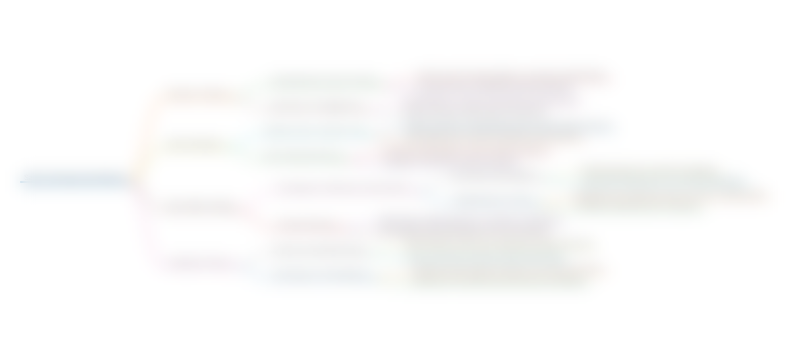
This section is available to paid users only. Please upgrade to access this part.
Upgrade NowKeywords
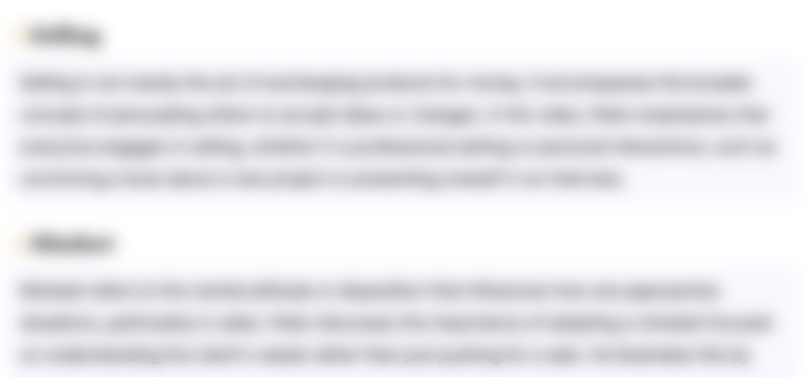
This section is available to paid users only. Please upgrade to access this part.
Upgrade NowHighlights
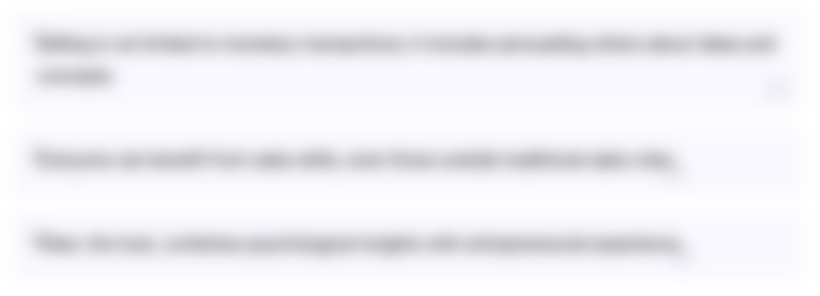
This section is available to paid users only. Please upgrade to access this part.
Upgrade NowTranscripts
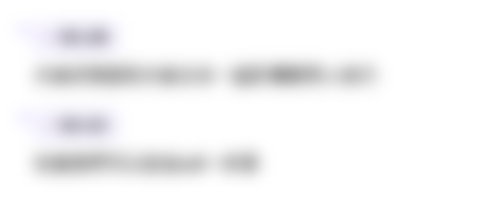
This section is available to paid users only. Please upgrade to access this part.
Upgrade NowBrowse More Related Video

Sritex, Prabowo, dan Masa Depan Industri Tekstil Kita

Why living in Australia is now ABSURD
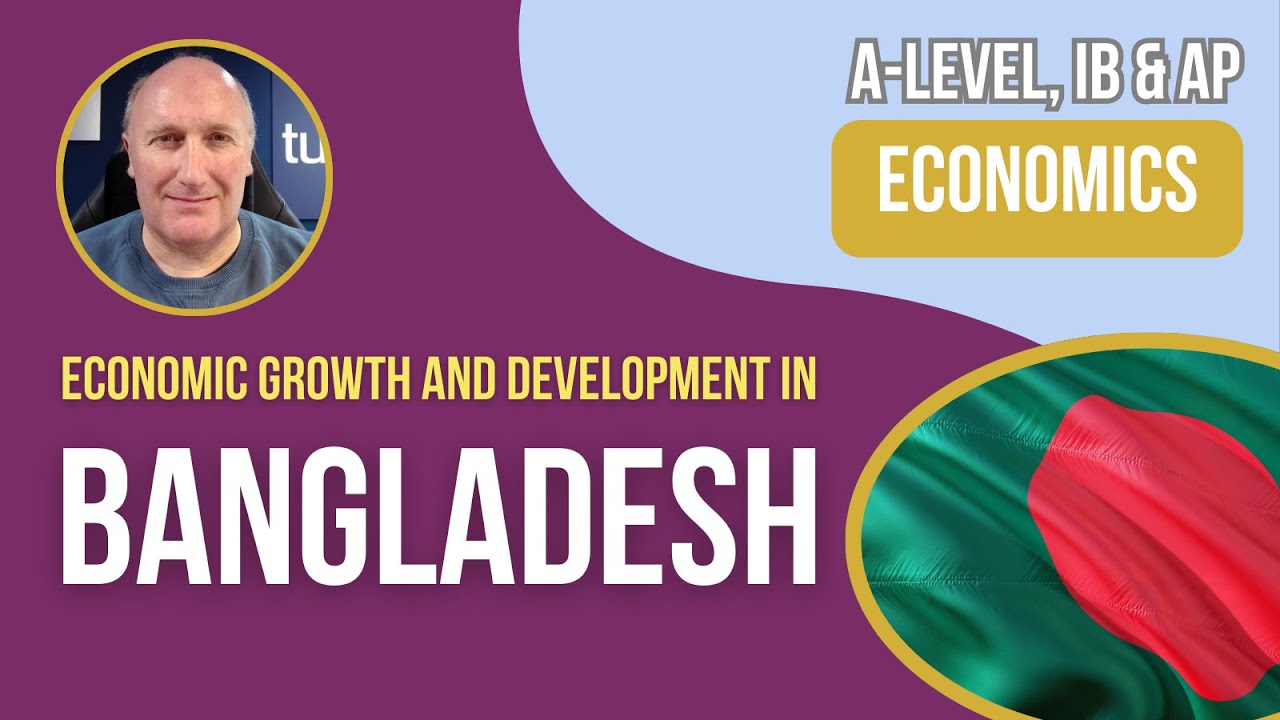
Growth and Development in Bangladesh I A-Level, AP & IB Economics
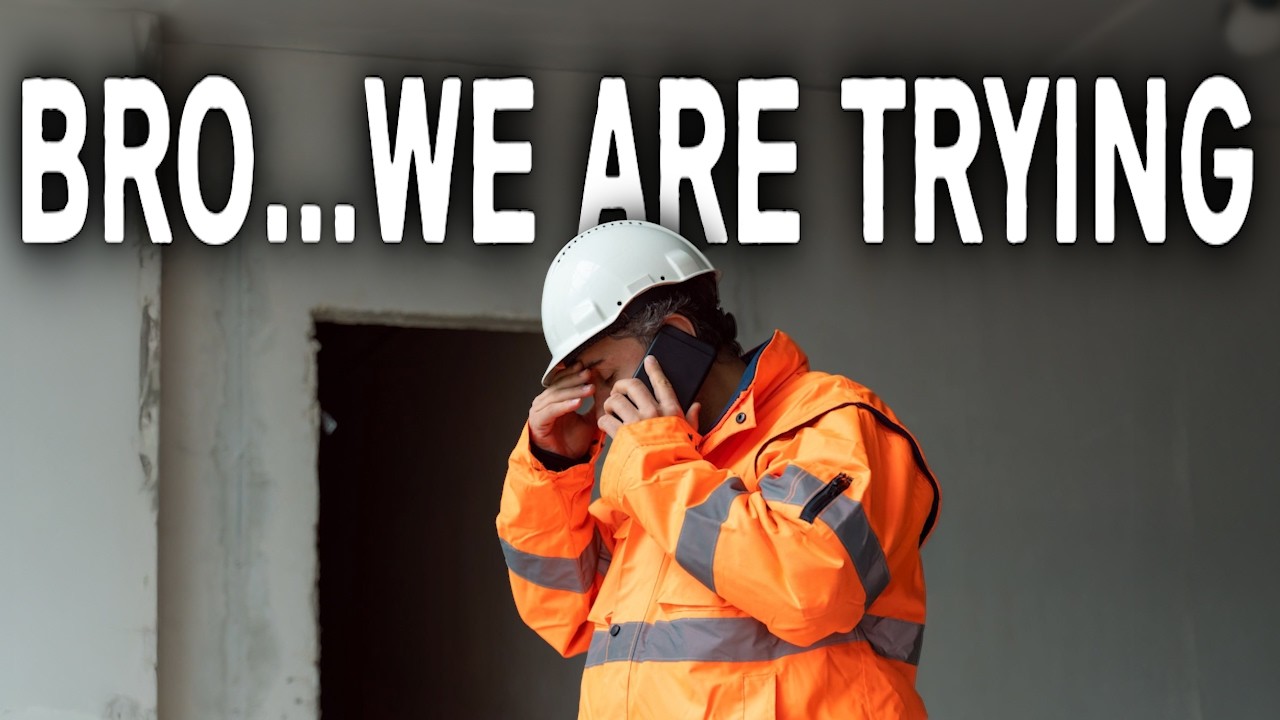
jUsT BUiLd MorE hOusEs!!
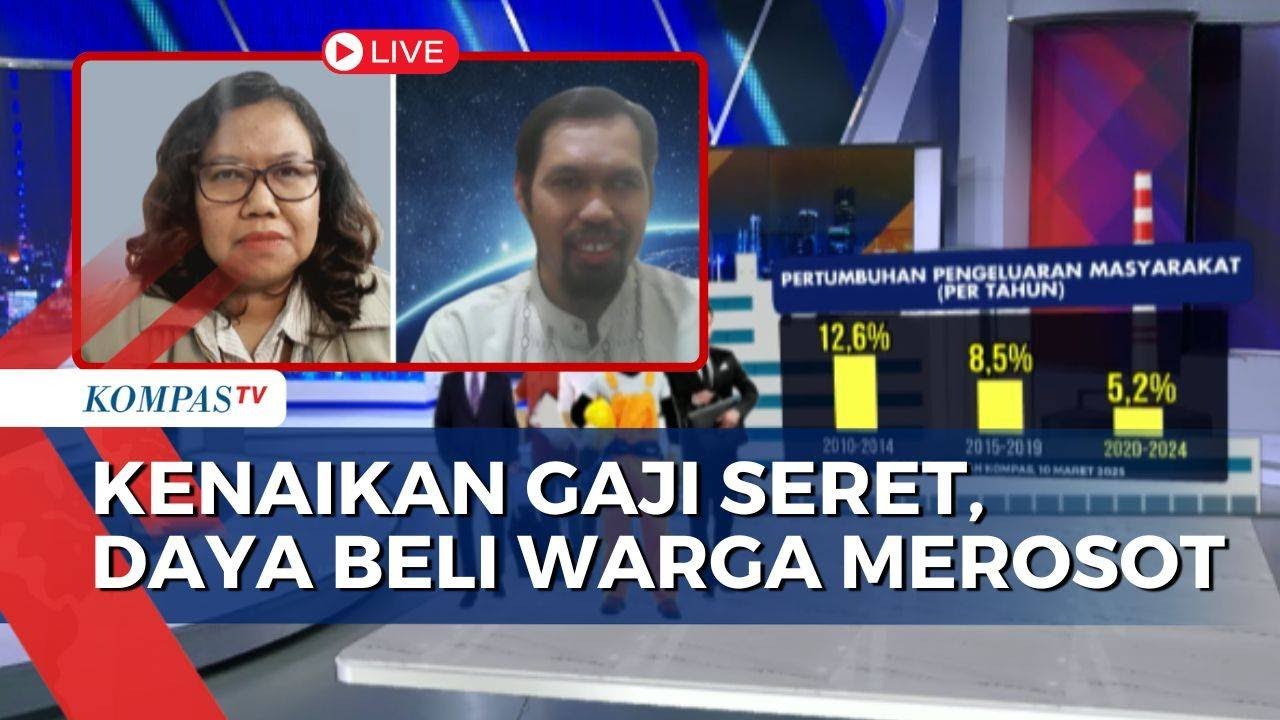
Kenaikan Gaji Seret dan Daya Beli Warga Turun, Apakah Ini Jadi 'Alarm' Perekonomian Nasional?

DAMPAK PUPUK KIMIA dan KESUBURAN TANAH
5.0 / 5 (0 votes)