Surface hardness || Hardening || Heat treatment
Summary
TLDRThe video script discusses the process of surface hardening, emphasizing its importance in various applications. It explains the need for hardening to prevent breakage under stress and demonstrates different techniques such as heat treatment, carbon and nitrogen addition. The script also covers the importance of understanding material behavior and the role of engineering in determining the depth of carbon penetration. It provides a detailed walkthrough of the hardening process, including the use of equipment like hardening machines and the significance of temperature and time in achieving the desired hardness.
Takeaways
- ๐ง Surface hardening is essential for strengthening the outer surface of components while keeping the core tough.
- ๐ก Surface hardening is necessary because hard materials can break under stress, so the process balances hardness and toughness.
- ๐ฅ Surface hardening is done through various techniques like adding carbon and nitrogen, which help increase the material's durability.
- โ๏ธ Gears and components undergo surface hardening to prevent wear and tear under high forces and friction.
- โก Heat treatment and quenching are key parts of the surface hardening process, which help to achieve the required hardness.
- ๐ ๏ธ The process involves heating the material to a high temperature (around 1550ยฐF), followed by rapid cooling in oil or other mediums.
- ๐ก๏ธ Precision in controlling temperature during surface hardening is crucial to ensure the proper penetration of carbon or nitrogen.
- โ๏ธ Different methods such as gas carburizing and nitriding are used to introduce elements into the surface, depending on the material and requirements.
- ๐ช Surface hardening increases the hardness of the outer layer without making the entire component brittle, ensuring longevity.
- ๐งช Testing of surface hardness is done using specialized machines to verify the success of the hardening process.
Q & A
What is surface hardening and why is it important?
-Surface hardening is a process of treating the surface of a material, typically metal, to make it harder. It is important because it increases the wear resistance of the surface, making it more durable while maintaining a tough core to prevent brittleness.
Why do we harden only the surface and not the entire component?
-We harden only the surface because a fully hardened component would become brittle and prone to breaking under sudden stress. The goal is to make the surface resistant to wear while keeping the core tough and flexible.
What are some methods of surface hardening mentioned in the script?
-The script mentions adding elements like carbon and nitrogen to the surface, followed by processes like quenching in oil, gas carburizing, and nitrocarburizing (adding both nitrogen and carbon).
What is the purpose of quenching after the hardening process?
-Quenching is done to rapidly cool the material after heating, locking in the hardened surface properties. This ensures that the desired hardness level is achieved without making the entire component brittle.
How does carburizing work in the surface hardening process?
-Carburizing involves heating the material in a carbon-rich environment. This allows carbon atoms to penetrate the surface, increasing its hardness while keeping the core softer and more ductile.
Why is the temperature control important during surface hardening?
-Temperature control is crucial because the material needs to be heated to specific temperatures to allow proper diffusion of elements like carbon or nitrogen. Overheating or underheating could lead to improper hardening, affecting the material's performance.
What is gas carburizing, and when is it used?
-Gas carburizing is a process where gas is used to introduce carbon into the material's surface. It is used when pack carburizing (using solid carbon sources) is not practical or efficient, offering a more controlled and uniform hardening process.
What are the potential downsides of surface hardening?
-One downside is that if the material becomes too hard, it could become brittle and prone to cracking under stress. Additionally, improper hardening could result in uneven wear or failure of the component.
What role does nitrogen play in the surface hardening process?
-Nitrogen is used in processes like nitriding and nitrocarburizing to increase hardness, wear resistance, and corrosion resistance. It diffuses into the material's surface along with carbon, forming a hard surface layer.
Why is surface hardening particularly important for gears and similar components?
-Surface hardening is essential for gears because they experience high friction and wear during operation. A hardened surface ensures the gear teeth can withstand the stress of constant motion without excessive wear, while the tough core provides resistance to breaking under heavy loads.
Outlines
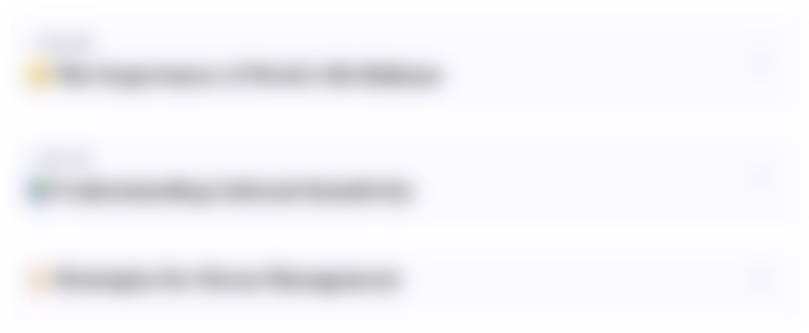
This section is available to paid users only. Please upgrade to access this part.
Upgrade NowMindmap
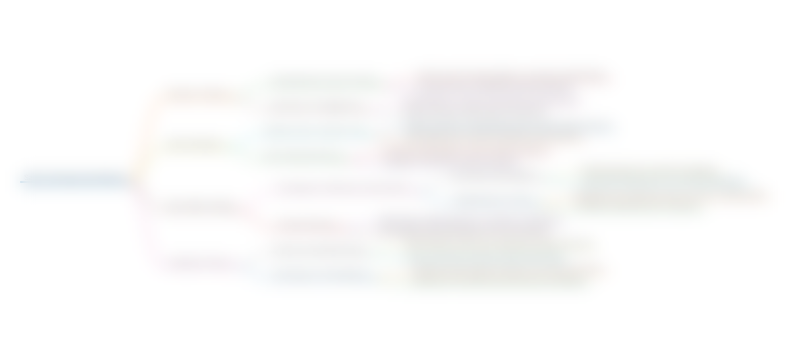
This section is available to paid users only. Please upgrade to access this part.
Upgrade NowKeywords
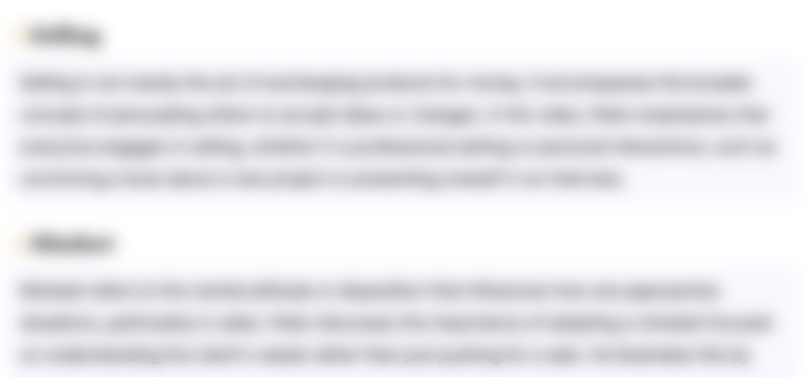
This section is available to paid users only. Please upgrade to access this part.
Upgrade NowHighlights
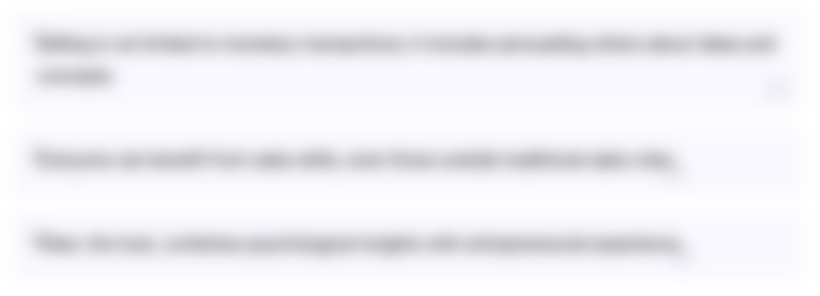
This section is available to paid users only. Please upgrade to access this part.
Upgrade NowTranscripts
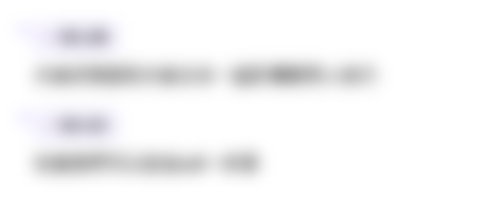
This section is available to paid users only. Please upgrade to access this part.
Upgrade NowBrowse More Related Video

Surface hardening of steel | flame, induction, laser beam, case hardening and nitriding
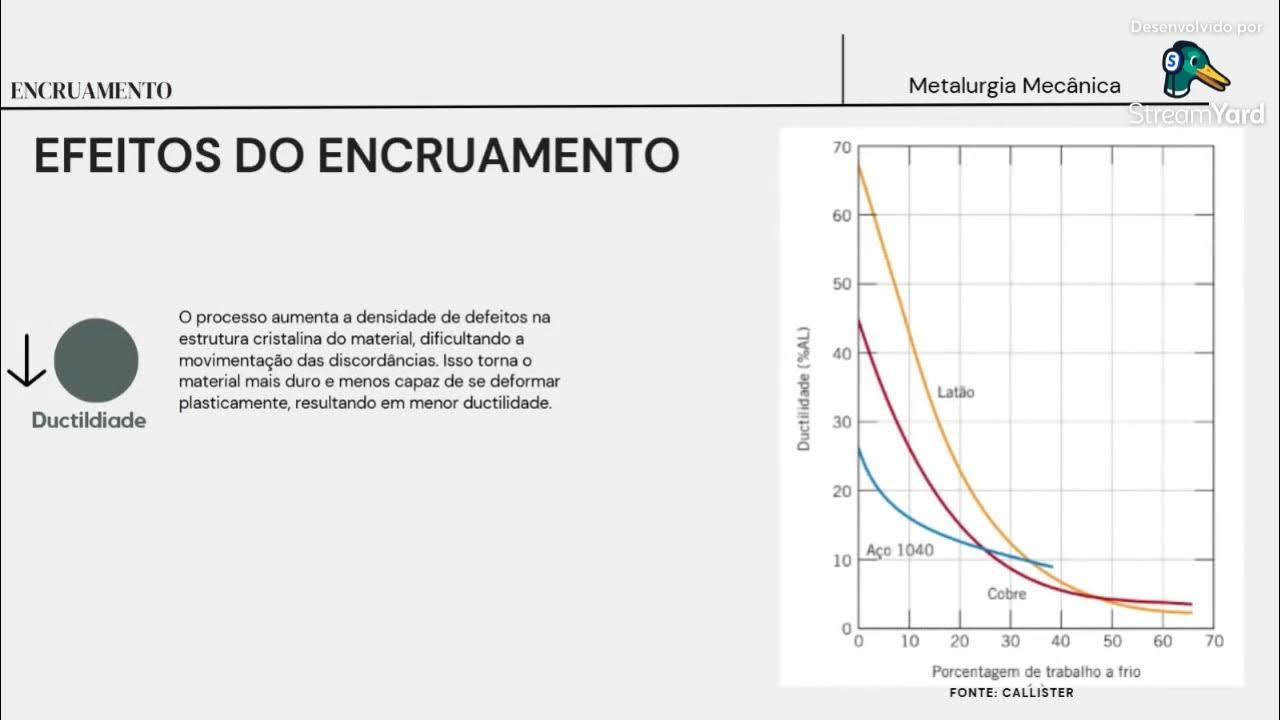
Pitch sobre Encruamento
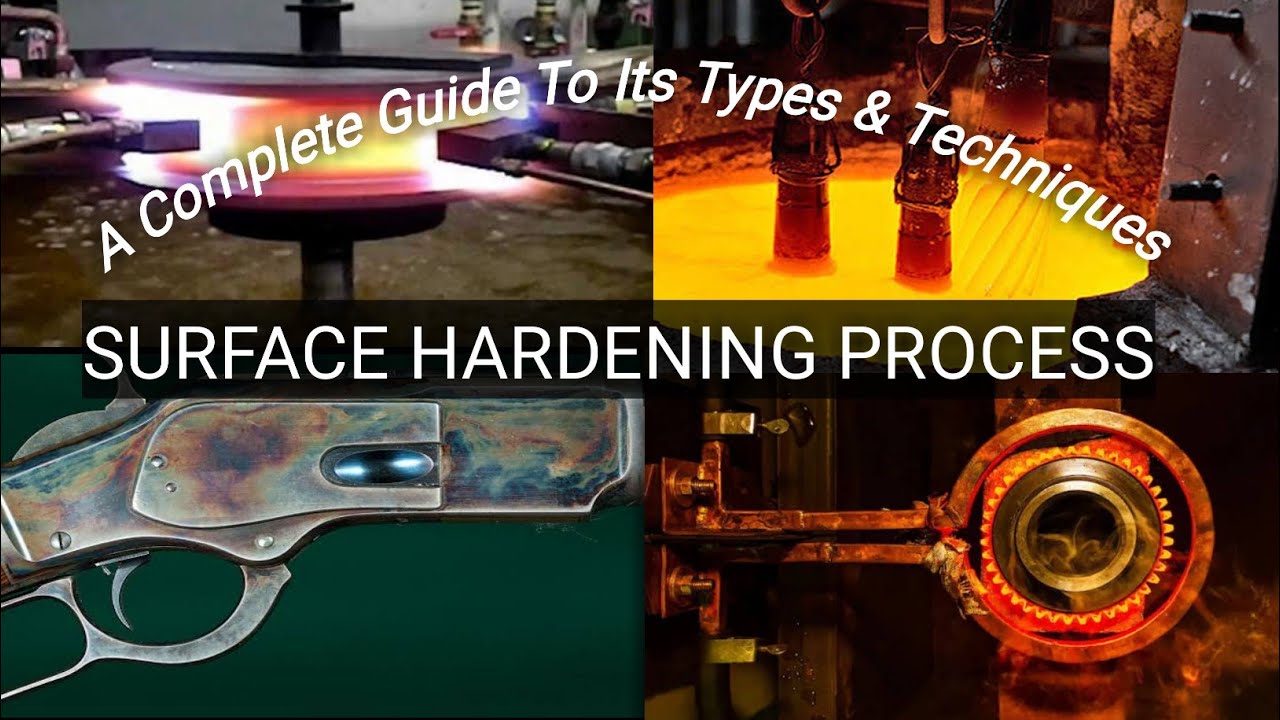
Surface Hardening Process | A Complete Guide To Its Types and Techniques.

Introduction to Surface Treatment
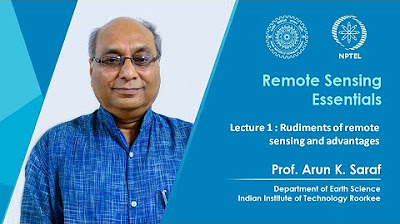
Lecture 1 : Rudiments of Remote Sensing and Advantages
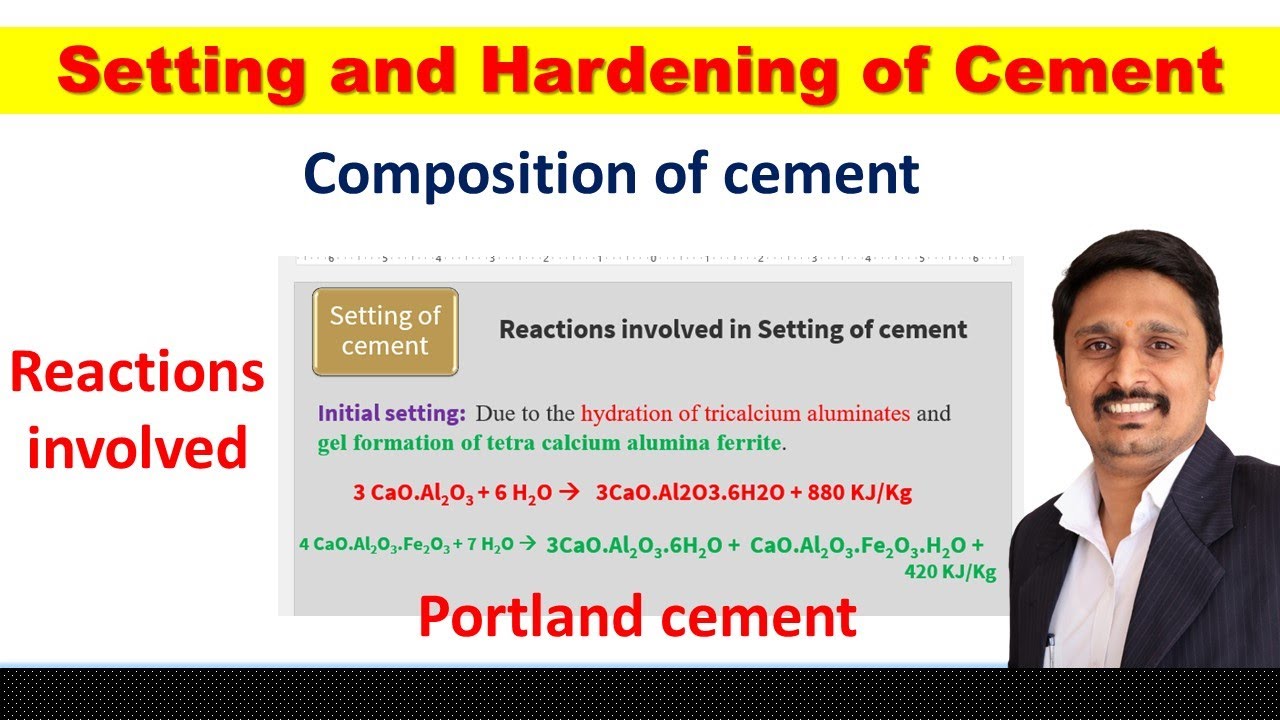
cement | composition | setting and hardening | reactions involved in setting and hardening
5.0 / 5 (0 votes)