Seguridad e higiene 5’s
Summary
TLDREl método de las 5S es una herramienta clave de gestión visual, originada en Toyota en los años 60, para optimizar el entorno de trabajo y mejorar la productividad. Sus cinco etapas (clasificación, organización, limpieza, estandarización y disciplina) buscan eliminar desperdicios, mejorar la calidad y seguridad, y aumentar la eficiencia. Este ciclo continuo facilita la detección de problemas, la reducción de accidentes y mejora la satisfacción de los empleados. Su implementación ha mostrado resultados como mayor confiabilidad de los equipos y reducción de incidentes, contribuyendo al éxito organizacional.
Takeaways
- 🔧 Las 5S es una herramienta de gestión visual utilizada como punto de partida para la mejora continua en las empresas.
- 🏭 El método comenzó en Japón y fue implementado por Toyota en los años 60 para mejorar la organización y limpieza en el lugar de trabajo.
- 🛠️ Las cinco etapas de las 5S son: Clasificación, Organización, Limpieza, Estandarización y Disciplina.
- 🚗 Inicialmente fue usada en el ensamblaje de automóviles, pero ahora se ha extendido a más industrias.
- 👷 Su misión es optimizar el entorno de trabajo, facilitar la labor de los empleados y aumentar su capacidad para detectar problemas.
- 📈 La implementación de las 5S mejora la productividad, la calidad del proceso y la seguridad en el trabajo.
- 🗂️ La Clasificación consiste en identificar y eliminar materiales innecesarios para facilitar el trabajo.
- 🔍 La Organización ordena los materiales indispensables para eliminar tiempos no productivos.
- 🧹 La Limpieza no solo previene accidentes, sino que también mejora el mantenimiento de los equipos.
- ♻️ Las 5S es un ciclo continuo que requiere disciplina para mantener un lugar de trabajo ordenado y limpio.
Q & A
¿Qué es la herramienta de las 'cinco eses'?
-Es una herramienta de gestión visual fundamental utilizada habitualmente como un punto de partida para la introducción de la mejora continua en las empresas.
¿De dónde proviene el método de las 'cinco eses'?
-El método proviene de Japón, específicamente de Toyota en la década de 1960, para lograr un lugar de trabajo más limpio y organizado.
¿Cuáles son las cinco etapas del método 'cinco eses'?
-Las cinco etapas son: clasificación, organización, limpieza, estandarización y disciplina.
¿Cuál fue el propósito original del método 'cinco eses' en Toyota?
-El propósito original era mejorar la calidad y eliminar las barreras de producción efectiva en el ensamblaje de automóviles.
¿En qué otros sectores se ha utilizado el método 'cinco eses' además del automotriz?
-El método se ha utilizado en una amplia variedad de industrias, empresas y trabajos más allá del sector automotriz.
¿Qué impacto tiene la implementación del método 'cinco eses' en el lugar de trabajo?
-La implementación del método mejora la productividad del proceso, aumenta la calidad y optimiza el entorno laboral, facilitando la labor de los empleados.
¿En qué consiste la primera etapa del método, la 'clasificación'?
-Consiste en identificar y clasificar los materiales indispensables para la ejecución del proceso, eliminando los innecesarios.
¿Qué se busca lograr con la segunda etapa, la 'organización'?
-Se busca ordenar los materiales indispensables para facilitar su uso, reduciendo el tiempo improductivo y los viajes innecesarios.
¿Cómo ayuda la 'limpieza' en la mejora del entorno laboral?
-La limpieza ayuda a eliminar la suciedad y mantener el área de trabajo en buen estado, reduciendo accidentes y mejorando el rendimiento.
¿Qué implica la etapa de 'estandarización' dentro del método?
-Implica establecer reglas claras para distinguir entre situaciones normales y anormales, asegurando que las tres primeras etapas se apliquen correctamente.
¿Por qué es importante la disciplina en la implementación de las 'cinco eses'?
-La disciplina es crucial para mantener el ciclo de mejora continua, asegurando un entorno de trabajo ordenado y limpio de manera constante.
Outlines
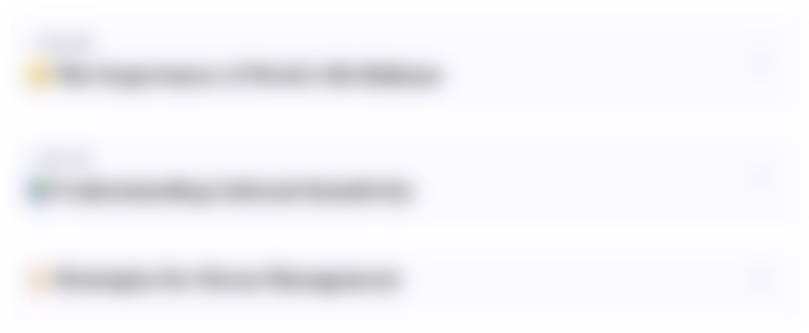
This section is available to paid users only. Please upgrade to access this part.
Upgrade NowMindmap
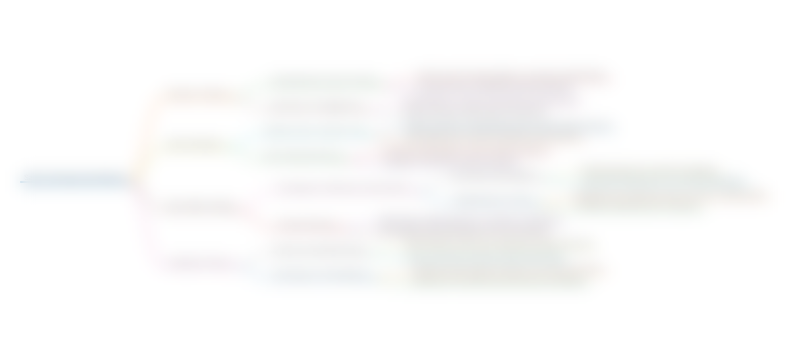
This section is available to paid users only. Please upgrade to access this part.
Upgrade NowKeywords
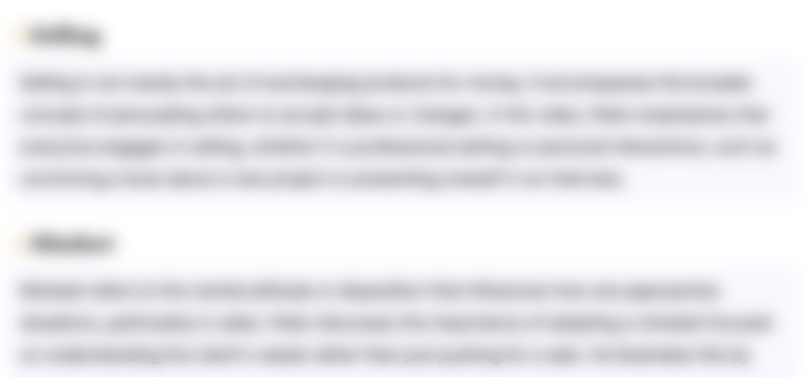
This section is available to paid users only. Please upgrade to access this part.
Upgrade NowHighlights
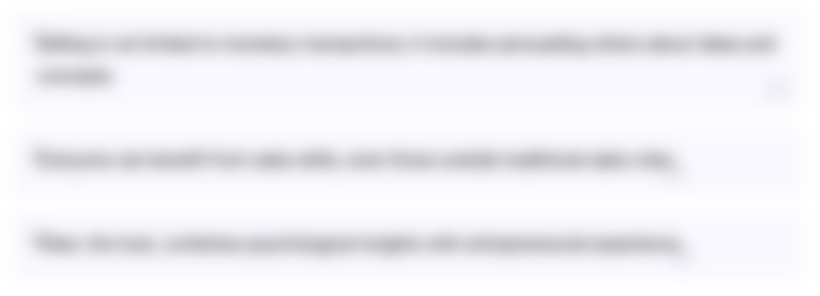
This section is available to paid users only. Please upgrade to access this part.
Upgrade NowTranscripts
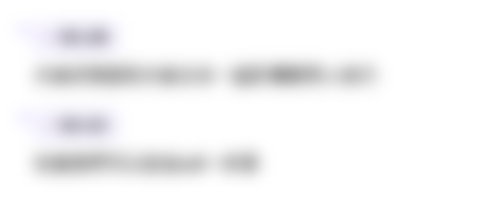
This section is available to paid users only. Please upgrade to access this part.
Upgrade Now5.0 / 5 (0 votes)