Make-to-stock vs. Make-to-order (Push vs. Pull)
Summary
TLDRThis video script explains the two main types of production planning: make-to-stock and make-to-order. The make-to-stock system produces goods before demand, based on forecasts, aiming to minimize shortages but potentially increasing inventory costs. In contrast, the make-to-order system builds goods only after receiving orders, reducing inventory costs but requiring higher capacity and shorter lead times. The script also introduces push and pull systems, highlighting the advantages of just-in-time production, which minimizes waste and work-in-process inventories by synchronizing production with actual demand.
Takeaways
- π¦ The make-to-stock system builds goods before demand is realized, relying on forecasts and storing items until sold.
- β³ Make-to-stock is ideal when processing lead times are long, capacity is limited, or product variety is low, minimizing stockouts.
- π‘ The make-to-order system produces goods only after demand is realized, reducing holding costs and risks by eliminating excess inventory.
- βοΈ A service factory, like a barbershop, is always make-to-order, as services cannot be stocked in advance.
- π Make-to-stock is a 'push' system, producing and pushing inventory down the supply chain regardless of demand, while make-to-order is a 'pull' system driven by actual demand.
- βοΈ A variation of make-to-stock, known as make-to-bottleneck, synchronizes production with the bottleneck, reducing work-in-process inventory.
- π The push-pull hybrid system is used when upstream processes create low-variety parts at high capacity, while downstream processes produce high-variety finished goods.
- π A full pull system, or just-in-time system, produces only according to demand, minimizing both work-in-process and finished goods inventories.
- π The Kanban system uses signals (Kanban cards) to trigger production in a pull system, ensuring each workstation only produces what is needed by the next process.
- π§ The main weakness of a just-in-time system is low capacity utilization, but this can be addressed by redesigning processes to balance cycle times and meet demand rates.
Q & A
What is the difference between the Make to Stock and Make to Order production systems?
-The Make to Stock system produces goods before demand is realized based on capacity or forecasts, while the Make to Order system produces goods only in response to actual demand.
In what situations is the Make to Stock system ideal?
-The Make to Stock system is ideal when processing lead times are long, capacity is limited, there is little or no variety in output (such as commodity products), or the value of finished goods is very low.
What are the main advantages of using the Make to Order system?
-The main advantages of the Make to Order system are reduced holding costs and lower risk, especially when lead times are short, capacity is high, output variety is high, or the value of finished goods is high.
Why is a service factory, like a barbershop, considered a Make to Order system?
-A service factory like a barbershop is considered a Make to Order system because it cannot produce services (e.g., haircuts) in advance. Services are provided in direct response to customer demand.
What are the drawbacks of a Make to Stock system when demand is overestimated?
-When demand is overestimated in a Make to Stock system, companies face the risks of obsolescence costs and holding costs due to overstocked inventory.
How does the Push system relate to the Make to Stock system?
-The Push system is another name for the Make to Stock system, where prior processes tend to overproduce and push their outputs to the next process, often producing more than the demand rate.
What is a Pull system, and how does it relate to the Make to Order system?
-A Pull system, also known as the Make to Order system, ensures that every process only starts production when demand from the next process or the customer triggers it. This minimizes inventory and aligns production with actual demand.
What is the Push-Pull hybrid process, and in what situations is it useful?
-The Push-Pull hybrid process combines elements of both Make to Stock and Make to Order systems. Upstream processes produce based on capacity or forecasts, while downstream processes produce based on actual demand. It's useful when upstream processes handle low variety, high-capacity production, while downstream processes require more customization.
What is the Just-In-Time (JIT) system, and how does it minimize waste?
-The Just-In-Time (JIT) system, also called the Kanban system, ensures that every workstation only produces when pulled by demand from the next workstation, minimizing work-in-process and finished goods inventory, which are considered waste.
What is a major limitation of the Just-In-Time system, and how can it be overcome?
-A major limitation of the Just-In-Time system is low capacity utilization, as stations may produce less than their capacity. This can be overcome by redesigning the process so that all stations' cycle times match the demand rate (T-time), leading to balanced production.
Outlines
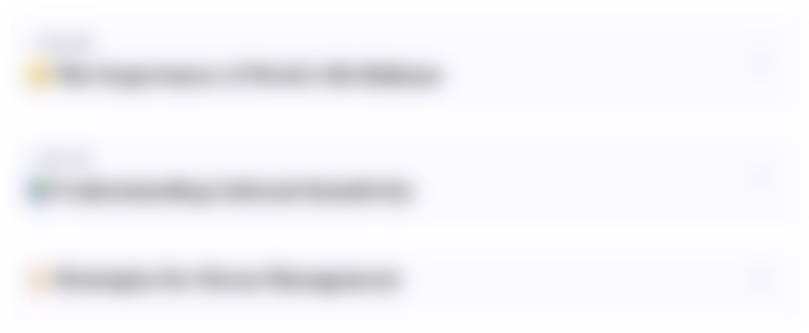
This section is available to paid users only. Please upgrade to access this part.
Upgrade NowMindmap
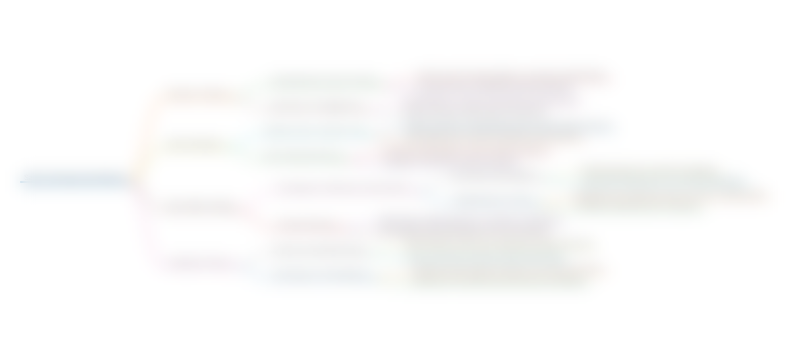
This section is available to paid users only. Please upgrade to access this part.
Upgrade NowKeywords
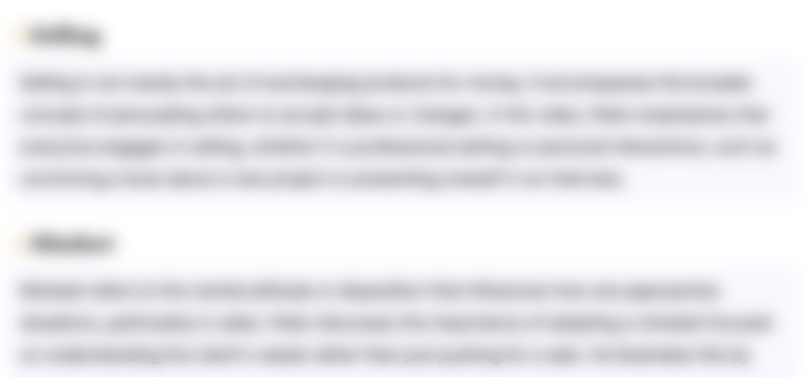
This section is available to paid users only. Please upgrade to access this part.
Upgrade NowHighlights
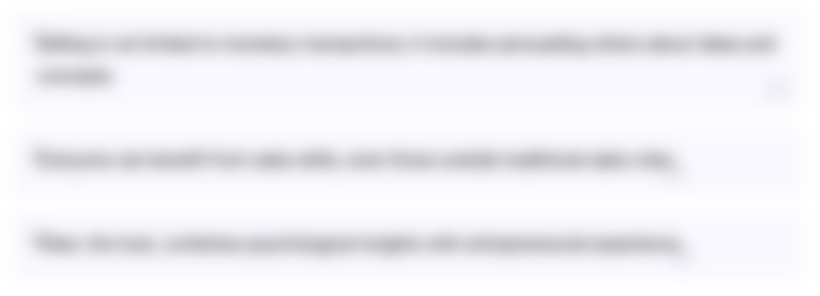
This section is available to paid users only. Please upgrade to access this part.
Upgrade NowTranscripts
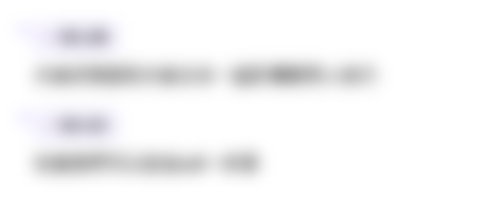
This section is available to paid users only. Please upgrade to access this part.
Upgrade NowBrowse More Related Video

(1 of 2) Decoupling Point | Make To Stock | Assemble To Order | Make To Order | Engineer To Order

Intro to Manufacturing Operations, Technology, and Processes [The Most Important Things to Know]
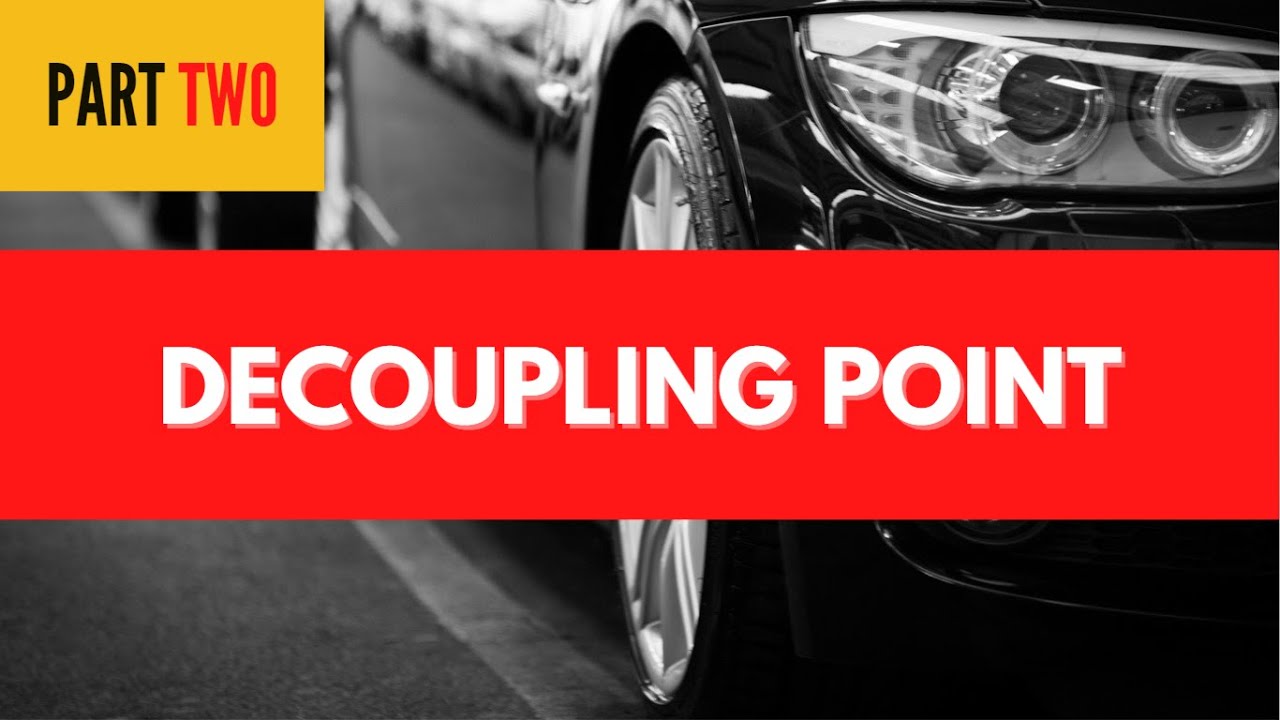
(2 of 2) Decoupling Point | Make To Stock | Assemble To Order | Make To Order | Engineer To Order

Production Strategy
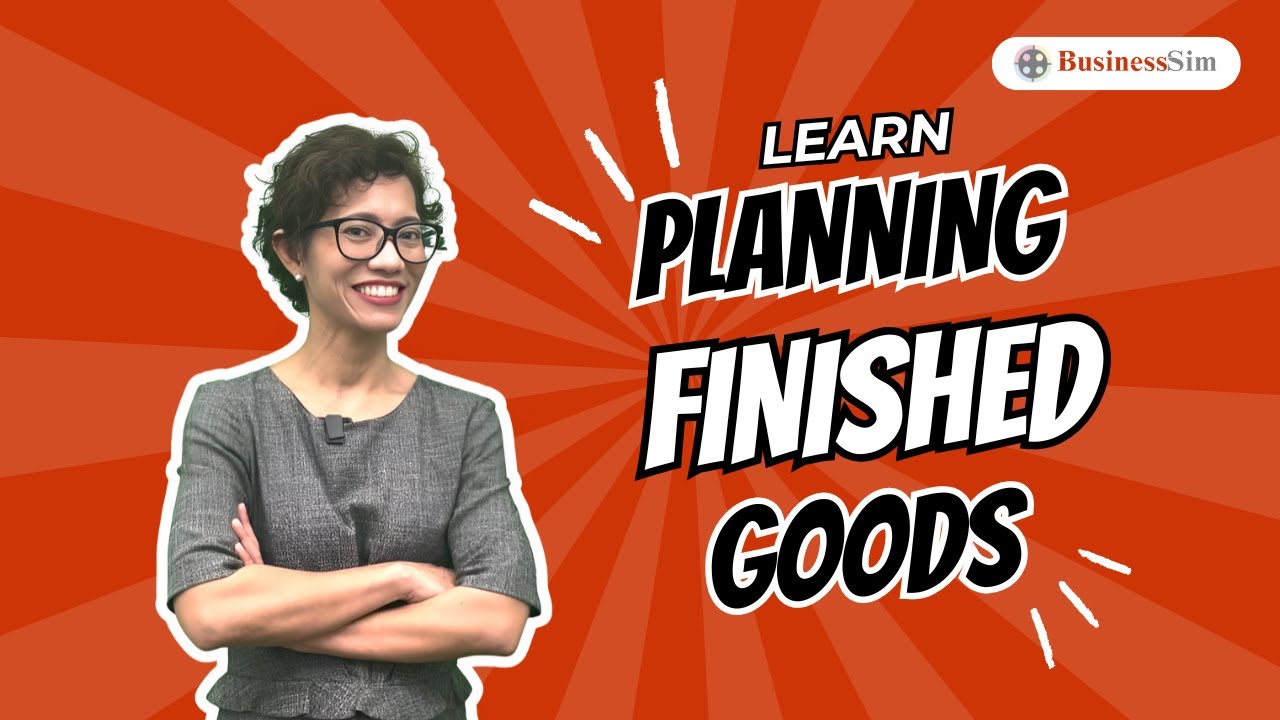
Production | Mastering Finished Goods Planning in Business Simulation
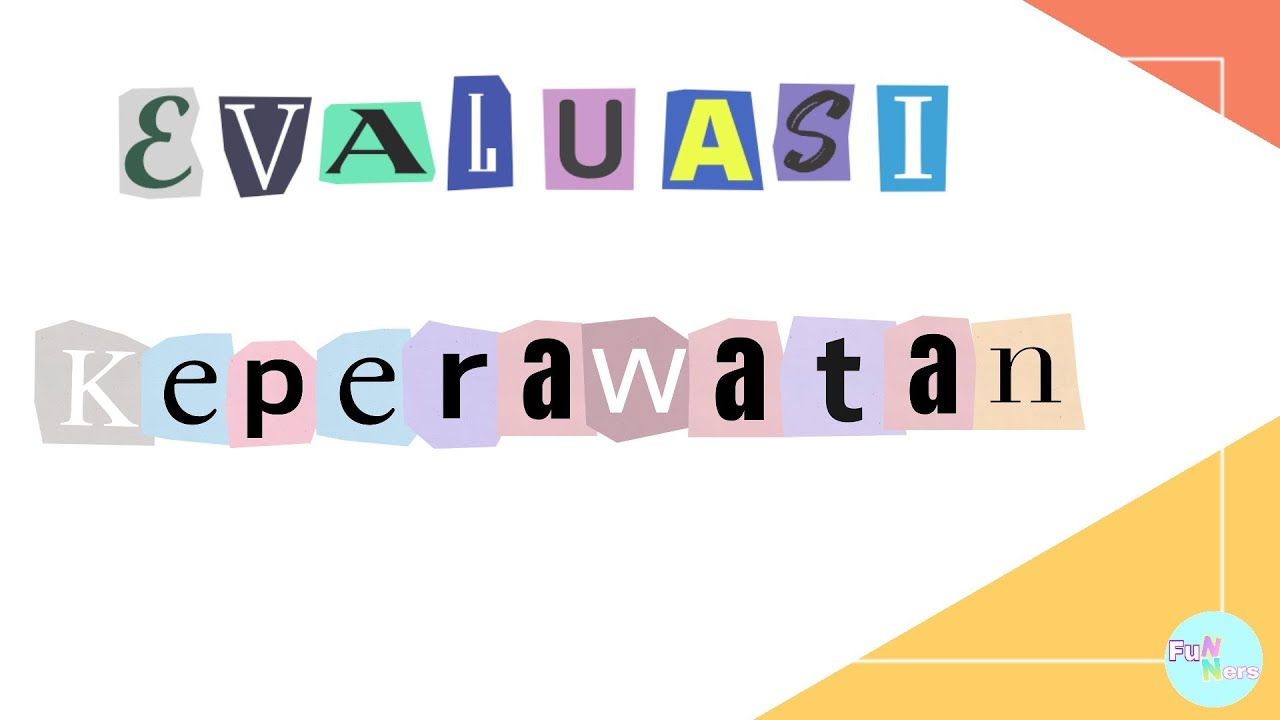
Evaluasi Keperawatan (Nursing Evaluation)
5.0 / 5 (0 votes)