HOW IT WORKS: Aircraft Flush Riveting
Summary
TLDRThis script outlines various methods for flush riveting in aircraft construction to minimize drag and achieve higher speeds. It details the counter sync method for thicker sheets, double dimpling for thinner sheets, pre-dimpling for specific thickness combinations, and a combination of pre-dimpling and counter syncing for sheets with varying thicknesses. The importance of accurate angles and flushness to reduce turbulence is emphasized.
Takeaways
- βοΈ Reducing turbulence and drag is crucial for increasing airplane speeds.
- π© Flush riveting eliminates the drag caused by the heads of ordinary rivets.
- π¨ The choice of flush riveting method depends on the thickness of the material.
- π For sheets over 40,000 thickness, counter sinking is the preferred method.
- πΉ Drilling a hole with a size corresponding to the rivet is the initial step in riveting.
- π© Counter sinking uses a special tool with a 100Β° cutting angle for flush riveting.
- π© The rivet length is determined by adding 1.5 times the rivet's diameter to the material thickness.
- π§ A vibrating air gun with a flush rivet set is used for driving the rivet.
- π© The finished rivet should have a head size 1.3 times the rivet's diameter and 0.5 times in height.
- π Flushness is critical and must be within plus or minus 2,000 of the rivet diameter.
- π© Double dimpling is used for thinner sheets where the total thickness is 40,000 or less.
- π© Pre-dimpling is used when the top sheet is thin and the total thickness of both sheets is over 40,000 but under 90,000.
- π© A combination of pre-dimpling and counter sinking is used for sheets with varying thicknesses that do not fit other methods.
Q & A
What is the main purpose of flush riveting in aircraft construction?
-The main purpose of flush riveting in aircraft construction is to reduce turbulence and drag by ensuring that the rivet heads are flush with the surface of the airplane, which aids in achieving higher speeds.
What is the significance of using a rivet with a flush head in aviation?
-Using a rivet with a flush head is significant in aviation because it eliminates the drag caused by the protruding head of ordinary rivets, thus contributing to higher aircraft speeds and improved aerodynamics.
What is the recommended method for flush riveting when the sheets are of 40,000 thickness or greater?
-For sheets of 40,000 thickness or greater, the recommended method for flush riveting is the counter sync method, which involves drilling a hole, counter syncing with a special tool, and then inserting and driving the rivet.
What is the correct hole size for a 1/8 inch diameter rivet?
-The correct hole size for a 1/8 inch diameter rivet is a number 30 hole.
Why is it important not to counter sync through the first sheet if specific approval has not been obtained?
-It is important not to counter sync through the first sheet without specific approval to prevent potential structural weaknesses or damage to the material, which could compromise the integrity of the aircraft.
What is the purpose of using a vibrating type air gun with a flush rivet set during the riveting process?
-A vibrating type air gun with a flush rivet set is used to ensure that the rivet is driven uniformly and accurately, forming a flush head that is consistent with the surface of the material.
What is the 'double dimple' method and when is it used?
-The 'double dimple' method is used for flush riveting thin sheets when the total thickness of the sheets is 40,000 or less. It involves dimming both sheets before inserting the rivet to achieve a flush finish.
How does the 'pre-dimpling' method differ from the 'double dimple' method?
-The 'pre-dimpling' method is used when the top sheet is too thin to counter sync and the bottom sheet is too thick to dimple. It involves separately dimming the top sheet and counter sinking the bottom sheet before riveting.
What is the purpose of using a special dimpling set with an adjusted angle and depth?
-A special dimpling set with an adjusted angle and depth is used to ensure that the dimples formed in the sheets are precise and consistent, which is crucial for the proper seating and flushness of the rivet head.
Why is it crucial for the rivet to be driven straight during the flush riveting process?
-It is crucial for the rivet to be driven straight during the flush riveting process to prevent clinching or offset, which could cause the dimpled edge to crack or fail, compromising the structural integrity of the riveted joint.
What is the combined counter sync and dimpling method, and when is it used?
-The combined counter sync and dimpling method is used when the top sheet is too thin to be counter sunk and the bottom sheet is too thick to be dimpled. The top sheet is dimpled, and the bottom sheet is counter sunk to achieve a flush rivet head.
Outlines
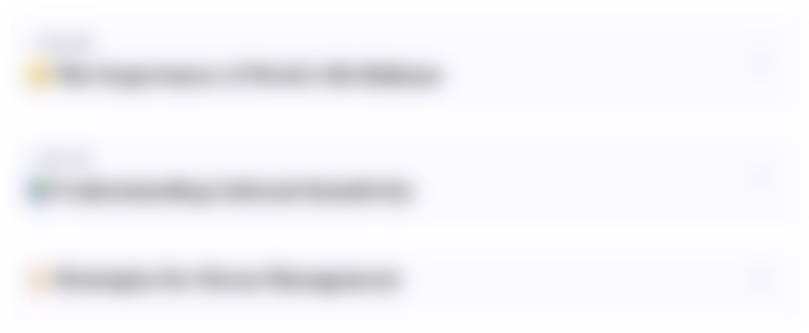
This section is available to paid users only. Please upgrade to access this part.
Upgrade NowMindmap
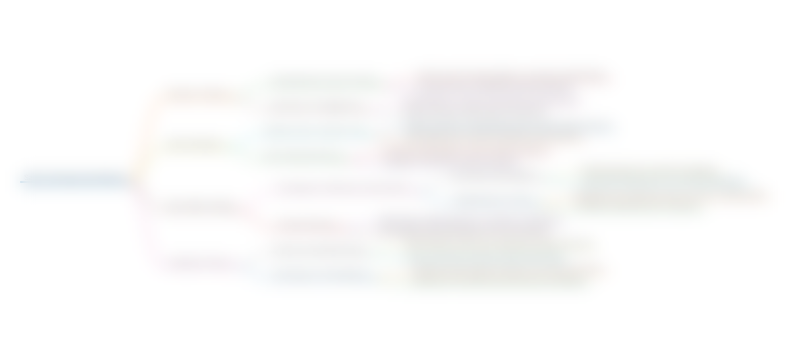
This section is available to paid users only. Please upgrade to access this part.
Upgrade NowKeywords
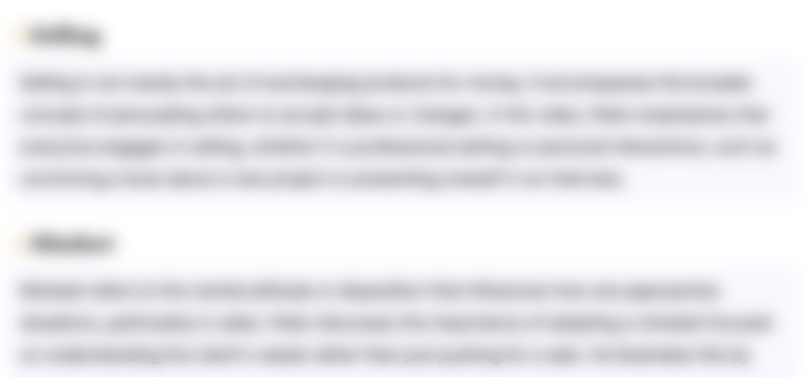
This section is available to paid users only. Please upgrade to access this part.
Upgrade NowHighlights
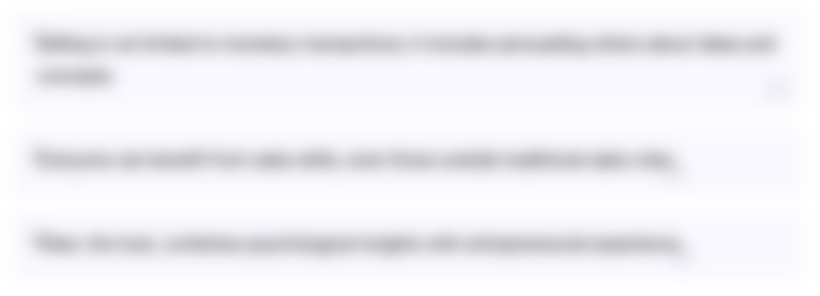
This section is available to paid users only. Please upgrade to access this part.
Upgrade NowTranscripts
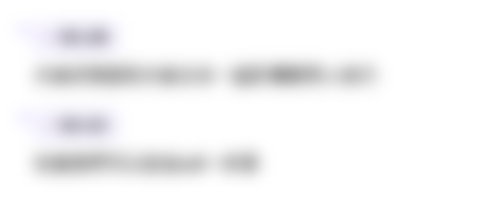
This section is available to paid users only. Please upgrade to access this part.
Upgrade NowBrowse More Related Video

Hyperloop - The Future of Travel?

Tyre Construction - Wheels & Tyres - Airframes & Aircraft Systems #20
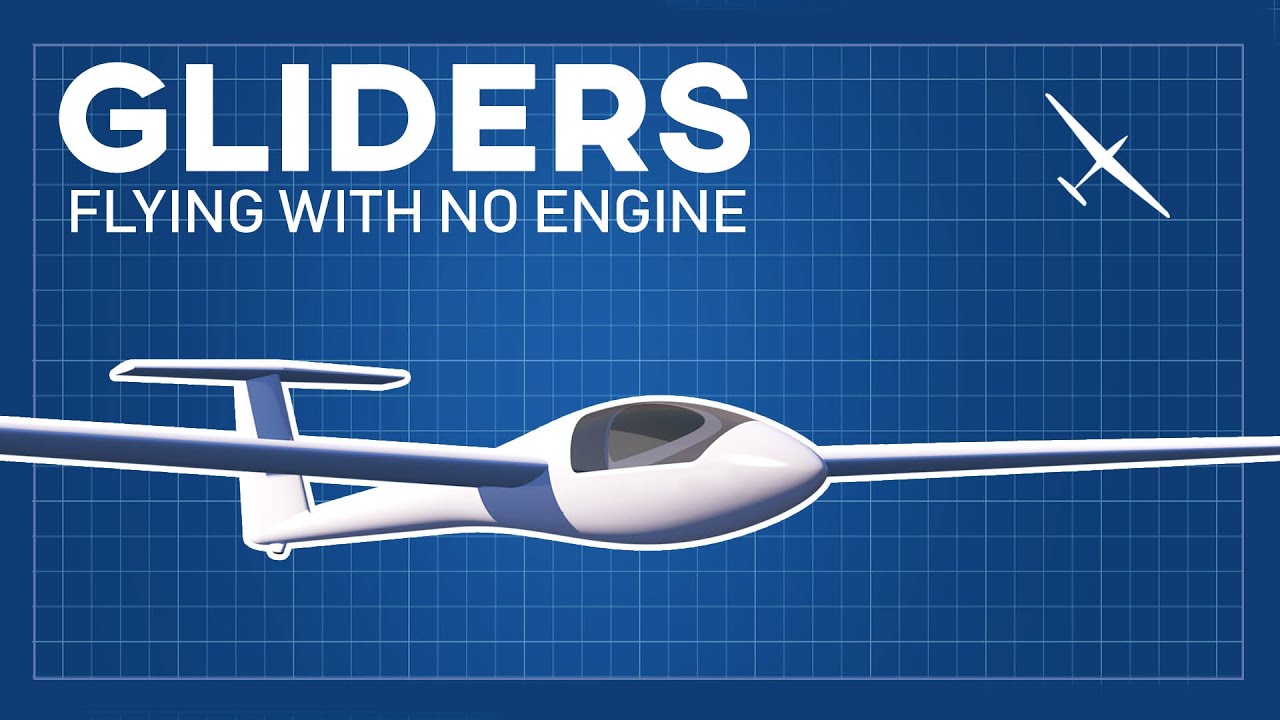
How can gliders fly without propulsion | The most complete explanation

Aerodynamic Balance - Flight Controls - Airframes & Aircraft Systems #29
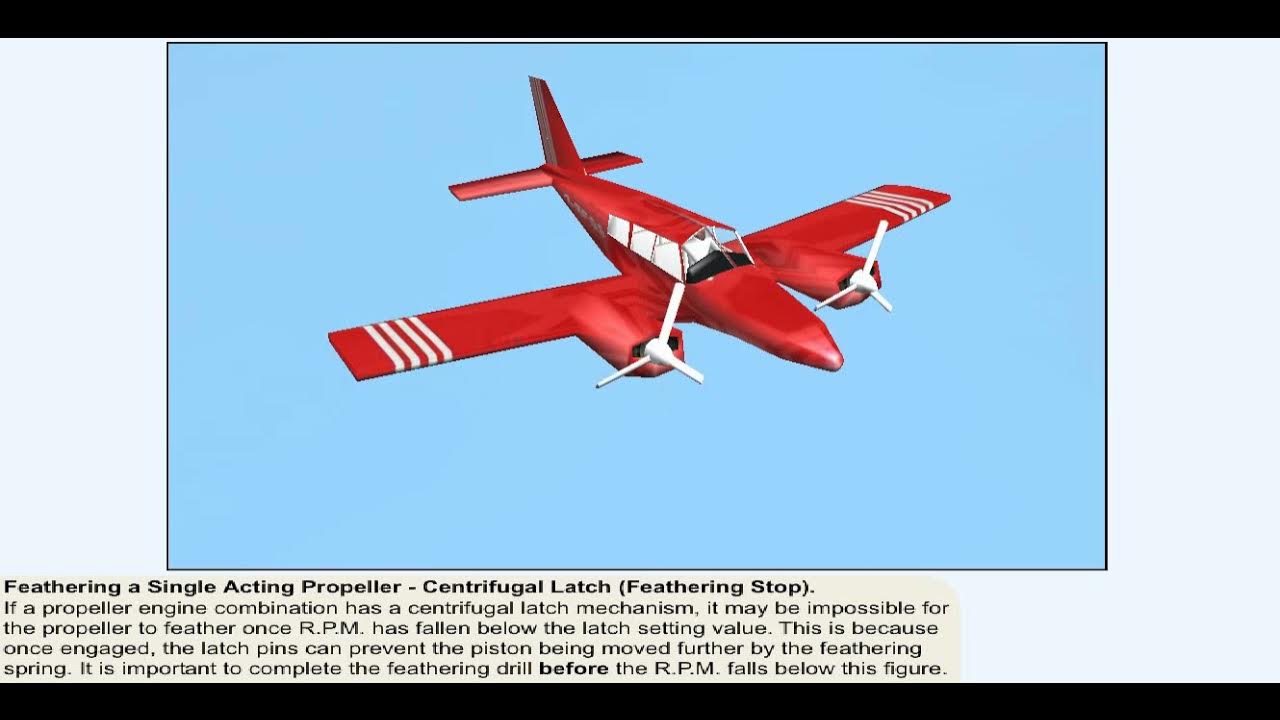
Feathering propeller and reversible pitch propeller
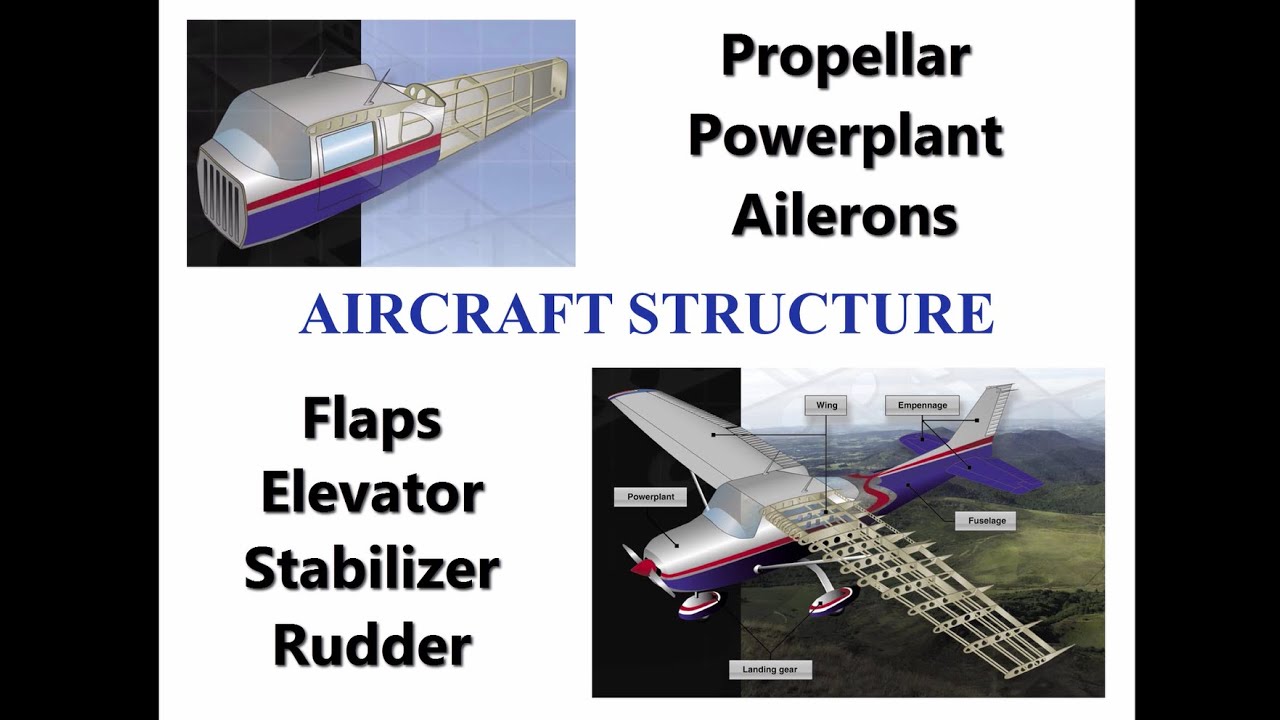
Private Pilot Tutorial 2: Aircraft Structure
5.0 / 5 (0 votes)