Extrusion Quality - Mystery issue resolved !
Summary
TLDRこの動画スクリプトでは、高品質な3Dプリンティングの理論と実際の課題について解説されています。特に、ハイエンドマシンで表面品質を維持する困難さについて焦点を当てています。スクリプトでは、時間の管理、ノズルの位置、および樹脂の量の排出が表面品質に影響を与える可能性があることが示されています。また、Extruderの精度が重要であることが強調されており、Bowden設置と直接駆動Extruderの違いも検証されています。最後に、改善されたExtruder歯車や平面ベアリングを使用した実験が行われ、それらが表面品質にどのように影響するかが詳細に説明されています。
Takeaways
- 🔍 品質の良い印刷の理論は、適切な量のプラスチックを適切な場所とタイミングで提供することです。
- 💡 高級機で高品質の印刷面を実現するのが難しい理由は、多くの要因が関与しているからです。
- 🌟 照明条件は、3Dプリンティングで作られた部品の外観に大きな影響を与えることができます。
- 📊 印刷品質の問題は、時序、ノズル位置、Z軸の揺れ、プラスチックの排出量のいずれかの要因による可能性があります。
- 🔧 時序の問題は、ソフトウェア、エクストラハーサのモーター、XおよびYの動きのタイミングによって管理されます。
- 🎯 ノズルの位置の問題は、XまたはY軸の位置、安定性、およびZ軸の揺れに関連する可能性があります。
- 🚀 ボウルデンアダプターを使用したことで、非常に高品質の印刷が得られました。これは、直接駆動エクストラハーサの過剰な直接性を示唆しています。
- 🔩 エクストラハーサのシステムを分解し、正しい根本原因を正確に特定するために、個々の要素を調査する必要があります。
- 📐 歯車や軸の精度は、エクストラハーサシステムの印刷品質に直接影響を与えるため、精密な部品が必要です。
- 🔄 フィラメントの品質と直径の一致も、エクストラハーサシステムの精度に影響を与えるため、品質の高いフィラメントを使用することが重要です。
- 🛠️ イドラーギアや軸の配置が適切でない場合、フィラメントの位置が変わり、印刷品質に影響を与える可能性があります。
Q & A
高品質の印刷を実現するために必要な要素は何ですか?
-高品質の印刷を実現するためには、適切な量のプラスチックを正確な場所とタイミングで供給することが重要です。
なぜ高級機でも表面品質を向上させることが難しいのですか?
-高級機でも表面品質を向上させることが難しいのは、印刷機のタイミング、ノズルの位置、Z軸の揺れ、プラスチックの供給量など、多くの要因が関係しているからです。これらの要因を完全にコントロールすることは困難であり、運要素も一定の影響を与えるためです。
どのような設定がFDM印刷において最悪の照明条件を作り出しますか?
-FDM印刷において最悪の照明条件は、頂部から尖锐な光が当たる状況を作り出します。これにより、レイヤーの積み重ね方や不規則な表面が明らかに見えてしまいます。
Bowden方式の印刷機がどのような利点を持ちますか?
-Bowden方式の印刷機は、長いチューブが使用されるため、ノズル内のプラスチックの圧力が安定し、表面品質が向上することが期待できます。しかし、再tractionや圧力の調整が必要なため、調整が難しい場合があります。
エクストラダーの精密度が表面品質に与える影響は何ですか?
-エクストラダーの精密度が表面品質に与える影響は大きいです。エクストラダーの歯車や軸の精度が不足していると、プラスチックの供給量にばらつきが生じ、表面に不規則なパターンが現れる可能性があります。
製造公差がエクストラダーの性能に与える影響は何ですか?
-製造公差がエクストラダーの性能に大きな影響を与えます。歯車のHub gearの軸へのオフセットやフィラメントの直径の变化など、わずかな公差もレイヤーの厚さや幅に影響を与え、最終的な表面品質に大きな違いをもたらす可能性があります。
Z軸の揺れが原因となっている場合、どのような症状が見られますか?
-Z軸の揺れが原因となっている場合、印刷物の表面に一定の間隔で繰り返し出现的する異常なパターンが見られます。これは、Z軸の揺れがフィラメントの供給位置に影響を与え、連続したレイヤーに同じエラーが現れることを意味します。
3Dプリンタのエクストラダーシステムを改善するためにどのようなアプローチを取ることができますか?
-エクストラダーシステムを改善するためには、歯車や軸の精度を向上させること、製造公差を緩和すること、またエクストラダーの設計を最適化することが有効です。また、Bowden方式のシステムと比較して、直接駆動のエクストラダーの利点と課題を検討し、適切な方法を選択することも重要です。
なぜエクストラダーの歯車や軸が表面品質に影響を与えるのですか?
-エクストラダーの歯車や軸が表面品質に影響を与えるのは、これらの部品の精度がプラスチックの供給量に直接影響を与えるからです。歯車や軸の歪みや軸の回転中心からのずれが、プラスチックの流量を変動させ、最終的に表面に不規則なパターンを生み出すことがあります。
どのようにしてエクストラダーの精度を向上させることができますか?
-エクストラダーの精度を向上させるためには、高精度な部品を使用することが効果的です。また、エクストラダーの設計を改善し、歯車や軸の一体化、軸の支えを強化することが役立ちます。さらに、製造プロセスを改善して公差を減らすことで、エクストラダーの全体的な精度を向上させることができます。
エクストラダーの調整において、PIDチューニングとは何ですか?
-PIDチューニングは、エクストラダーのホットエンドの温度制御を最適化するプロセスです。PID(比例・積分・微分)コントローラーは、温度エラーを最小限に抑えるために、加热期、保温期、および冷却期の時間を調整します。これにより、プラスチックの熔融状態を安定させ、表面品質を向上させることができます。
エクストラダーシステムのトラブルシューティングにおいて、フィラメントの品質はどのよう影響を与えるのですか?
-エクストラダーシステムのトラブルシューティングにおいて、フィラメントの品質は重要な要素です。フィラメントの直径が均一でない場合や、品質が低い場合は、流量の変化を引き起こし、表面品質に影響を与える可能性があります。したがって、高品質なフィラメントを選択し、管理することで、エクストラダーシステムのトラブルシューティングが容易になります。
Outlines
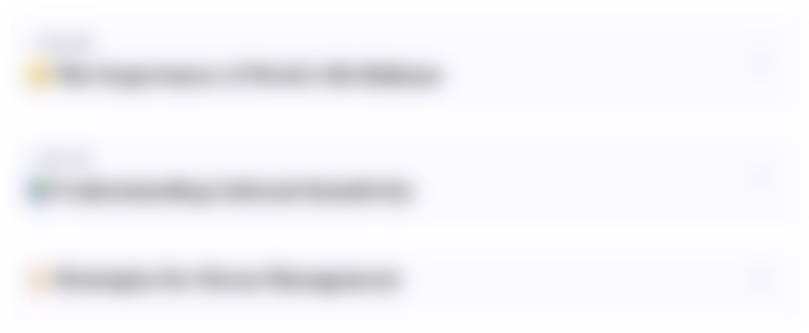
This section is available to paid users only. Please upgrade to access this part.
Upgrade NowMindmap
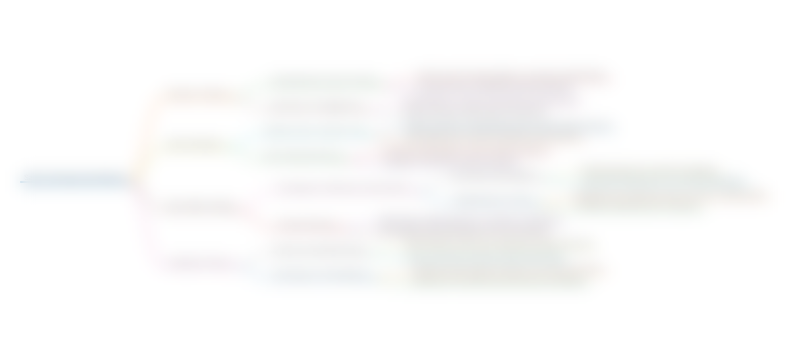
This section is available to paid users only. Please upgrade to access this part.
Upgrade NowKeywords
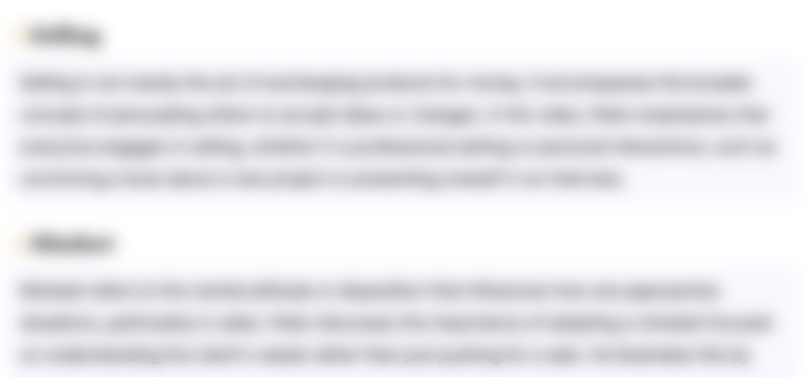
This section is available to paid users only. Please upgrade to access this part.
Upgrade NowHighlights
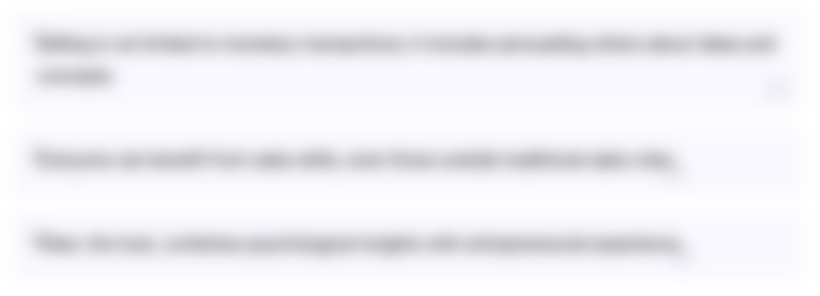
This section is available to paid users only. Please upgrade to access this part.
Upgrade NowTranscripts
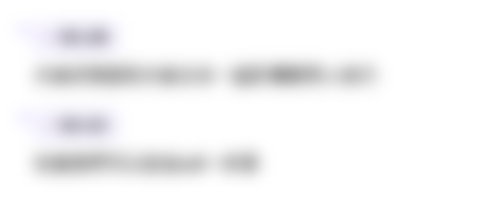
This section is available to paid users only. Please upgrade to access this part.
Upgrade Now5.0 / 5 (0 votes)