A Students Guide on How to Pass a Bend Test
Summary
TLDRThis video from well.com offers a comprehensive guide on preparing a plate for a weld test, emphasizing the importance of proper preparation. It covers the creation of a bend test fixture with a pneumatic system, detailing the process from marking and cutting test samples to grinding and blending techniques. The tutorial adheres to the 2015 edition of the code book, focusing on welder qualification for groove welds on 3/8-inch plates. It illustrates how to perform both face and root bends, highlighting the significance of maintaining weld integrity and plate flatness for successful testing.
Takeaways
- 🔧 The video focuses on preparing a plate for a weld test, emphasizing the importance of preparation in ensuring a successful test outcome.
- 🛠️ A pneumatic system is used for the bend test fixture, which is crucial for the testing procedure.
- ⚙️ The video provides a step-by-step guide on how to set up the plate for a guided bend test after visual inspection.
- 📏 It is crucial to cut test samples from specific places on the plate to avoid failing the test due to improper preparation.
- 📖 The video references the 2015 edition of the code book, specifically page 159, for welder or welder operator qualification.
- 🔩 The backing strip is used for repeatability and faster welding, and its removal is part of the sample preparation process.
- 💻 The host demonstrates how to mark and cut the test plate, ensuring the samples are taken from the correct locations for accurate testing.
- ✂️ The video explains the necessity of grinding and blending the samples to prepare them for bending, including tips for achieving the best results.
- 🔬 The bend test is conducted to check for weld quality, with the video detailing how to perform both face and root bends.
- 📚 The importance of understanding welding codes, such as D11, is highlighted for welders to ensure their qualifications and adherence to industry standards.
Q & A
What is the main focus of the video?
-The main focus of the video is to demonstrate the process of preparing a plate for a weld test, including the steps for cutting and grinding samples, and performing a guided bend test.
Why is preparation important in weld testing?
-Preparation is crucial in weld testing because it can determine whether a weld passes or fails the test. Proper preparation includes correct placement of welds, managing the heat of the plate during welding, and ensuring the samples are cut and ground accurately according to specifications.
What are the consequences of incorrect sample preparation?
-Incorrect sample preparation can lead to a failed weld test, even if the weld itself looks good. This can happen if samples are not cut from the correct locations, are not prepped in the right way, or if the grinding is not done properly.
What is the significance of the backing strip in the weld test?
-The backing strip is significant because it provides a more repeatable and faster weld. It's typically left in place in the field for structural integrity and can be used for conditions like moment connections or beam to beam column splices.
How should the backing strip be removed for testing?
-The backing strip should be removed after the samples are cut out, by grinding it down to bare metal without cutting into the parent metal, to ensure the sample maintains the required thickness for the bend test.
What are the dimensions required for the test plate and the backing strip?
-The test plate should have at least six inches of material, and the backing strip should be at least 3/8 by 2 inches as per the code book referenced in the video.
Why is it important to mark the center line on the test plate?
-Marking the center line on the test plate is important because all dimensions for cutting and grinding the samples are measured from this line, ensuring accuracy and consistency in the preparation process.
What are the specific locations from which the face and root samples should be taken?
-The face and root samples should be taken one inch or 25 millimeters from the center line, and then an additional one and a half inches from that one-inch point on either side of the center line.
How should the edges of the test samples be prepared before bending?
-The edges should be ground down to be nice and flat, maintaining the required width and thickness. The corners can be radiused up to an eighth of an inch to prevent stress concentration during the bend test.
What is the purpose of blending the weld area and how should it be done?
-Blending the weld area is done to ensure a smooth transition and to avoid introducing stress concentrations that could lead to failure during the bend test. The grinding striations should run parallel to the width of the plate, not perpendicular.
What are the requirements for the bend test after the samples are prepared?
-After preparation, one root bend and one face bend are required for the weld test. The bend test is performed using a specific fixture, and the samples must be bent without causing any cracks or discontinuities that exceed the allowable limits.
Outlines
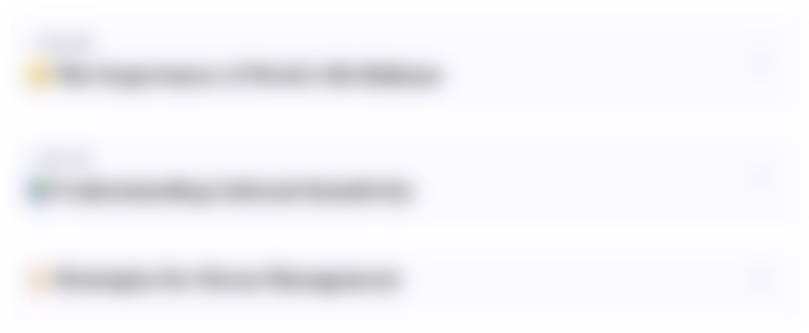
This section is available to paid users only. Please upgrade to access this part.
Upgrade NowMindmap
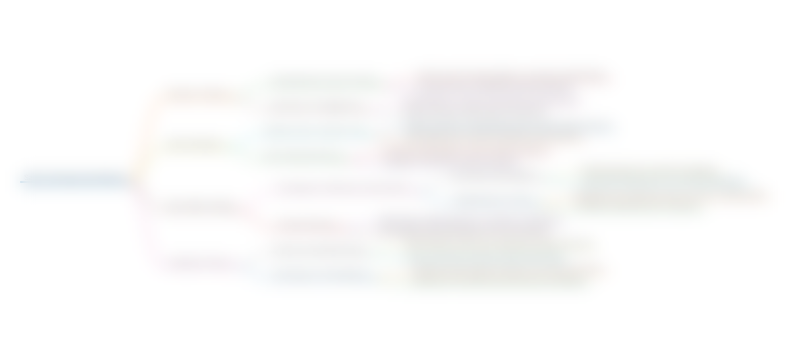
This section is available to paid users only. Please upgrade to access this part.
Upgrade NowKeywords
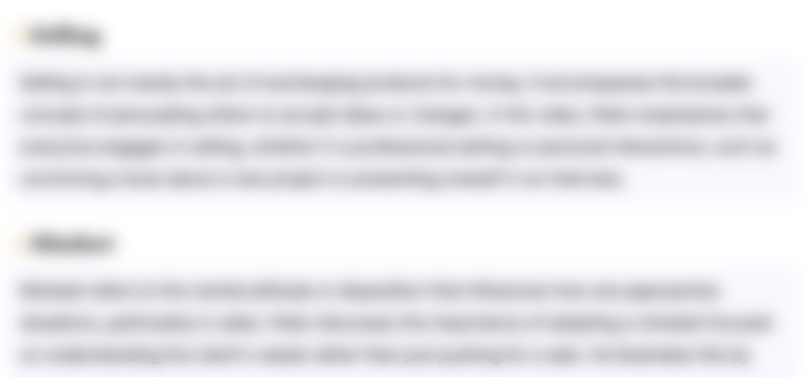
This section is available to paid users only. Please upgrade to access this part.
Upgrade NowHighlights
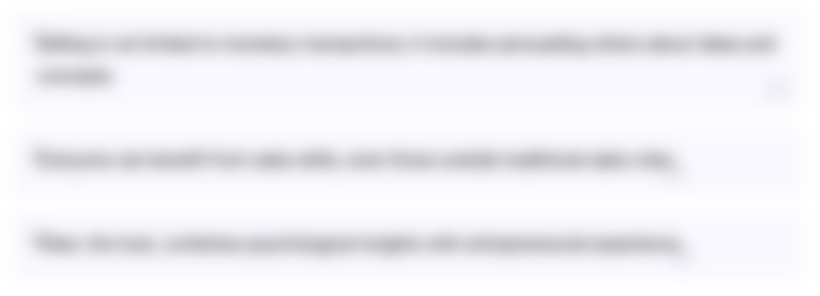
This section is available to paid users only. Please upgrade to access this part.
Upgrade NowTranscripts
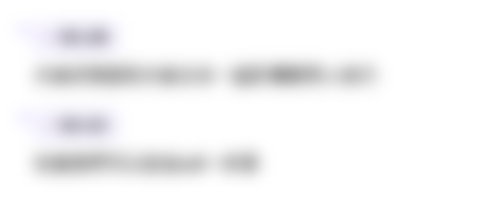
This section is available to paid users only. Please upgrade to access this part.
Upgrade NowBrowse More Related Video
5.0 / 5 (0 votes)