AULA 1 - QUALIDADE E PRODUTIVIDADE
Summary
TLDRAnne, an administrative production engineer, introduces a course on quality and productivity management. The course covers the evolution of quality concepts, the competitive business environment, and the importance of quality in market competition. It introduces quality management tools like the seven basic quality tools and the ISO 9001 standards. The lecture also explains the PDCA cycle for continuous improvement and touches on the 5S methodology for workplace organization.
Takeaways
- 😀 Anne, the instructor, is an administrative engineer in production and will guide students through the course on quality and productivity.
- 📈 The course aims to meet students' expectations by focusing on quality management and its evolution over time.
- 🏭 In a competitive business environment, companies seek new materials, process acceleration, and innovative products to maintain their market share.
- 🔍 Quality is crucial for market competition, as producing quality products enhances competitiveness.
- 🚫 The goal of quality management is to optimize efforts and resources to avoid waste, such as producing defective products that lead to wasted materials and labor.
- 📚 Quality has different meanings for different people, and understanding its definition has evolved with the contributions of various quality experts.
- 📈 The concept of quality has shifted from mere inspection of finished products to a focus on process control and total quality management.
- 🛠️ The seven main quality tools include flowcharts, Pareto diagrams, cause-and-effect diagrams, histograms, check sheets, control charts, and scatter diagrams.
- 🌐 ISO 9001 is a globally recognized model for quality management systems, emphasizing continuous improvement and customer focus.
- 🔄 The PDCA cycle (Plan-Do-Check-Act) is a fundamental method for continuous improvement in quality management.
- 🧰 The 5S methodology is introduced as a way to improve organization and efficiency, starting with 'Seiri' (Sorting) and 'Seiton' (Setting in order).
Q & A
What is the main focus of the discipline 'Quality and Productivity' taught by Anne, the administrative engineer of production?
-The main focus is to understand and manage quality within an organization, ensuring that all efforts and resources used are optimized to prevent waste and enhance competitiveness in the market.
Why is the term 'competition' used in the context of quality management?
-The term 'competition' is used because it is a part of daily operations, and producing with quality increases the competitive conditions in the market.
What are the three different perspectives on what 'quality' means according to the script?
-Quality is defined as: 1) Continuous improvement by Deming, 2) Conformance to requirements by Crosby, and 3) Fitness for use by Juran.
How has the concept of quality evolved over the years as per the script?
-The concept of quality evolved from inspection of the final product, to process inspection, to the era of quality assurance with technical standards, and finally to total quality management involving the entire organization.
What is the ISO 9000 series and why is it important?
-The ISO 9000 series is a set of standards that provide guidelines and features for a quality management system. It is important because it helps organizations ensure that they meet the customer and regulatory requirements for a product or service.
What are the seven main tools of quality mentioned in the script?
-The seven main tools of quality are: Flowchart, Pareto Diagram, Cause and Effect Diagram, Histogram, Check Sheets, Control Charts, and Scatter Diagram.
What is the PDCA cycle and how does it relate to continuous improvement?
-The PDCA cycle, also known as the Deming cycle, stands for Plan, Do, Check, Act. It is a method for the continuous improvement of processes and products, and is fundamental to quality management systems.
What does the 5S methodology involve and what are its benefits?
-The 5S methodology involves a set of organizational practices aimed at creating an efficient and uncluttered work space. The practices are Sort, Set in order, Shine, Standardize, and Sustain. Its benefits include improved quality, elimination of waste, optimized use of space, prevention of breakdowns, and minimized accidents.
How does the 'Sense of Use' in the 5S methodology apply to a workplace?
-The 'Sense of Use' in the 5S methodology involves analyzing the workplace and keeping only necessary items in the right quantity, discarding what is not useful, and ensuring that items are easily accessible and used efficiently.
What is the significance of the 'Sense of Organization' in the 5S methodology?
-The 'Sense of Organization' in the 5S methodology refers to arranging the work environment so that every tool, equipment, and document has a specific place, is easily accessible, and is returned to its place after use, promoting efficiency and order.
Outlines
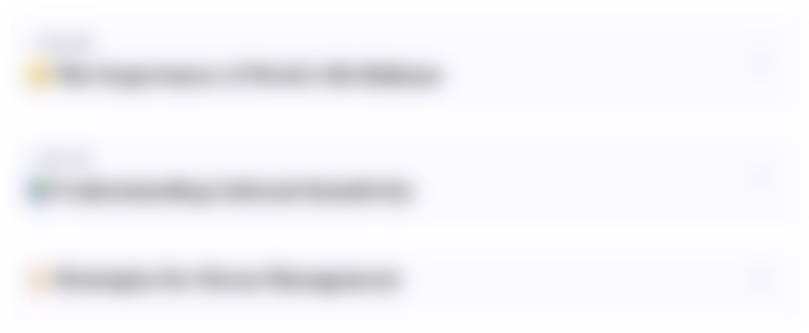
This section is available to paid users only. Please upgrade to access this part.
Upgrade NowMindmap
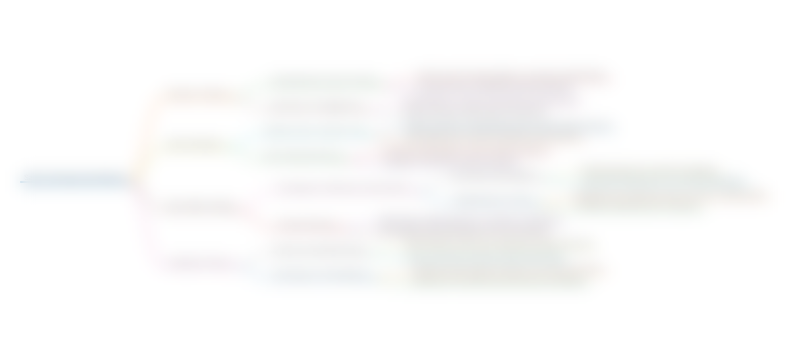
This section is available to paid users only. Please upgrade to access this part.
Upgrade NowKeywords
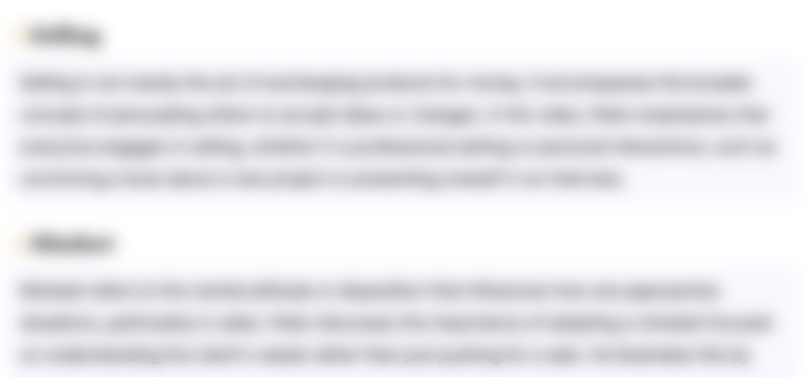
This section is available to paid users only. Please upgrade to access this part.
Upgrade NowHighlights
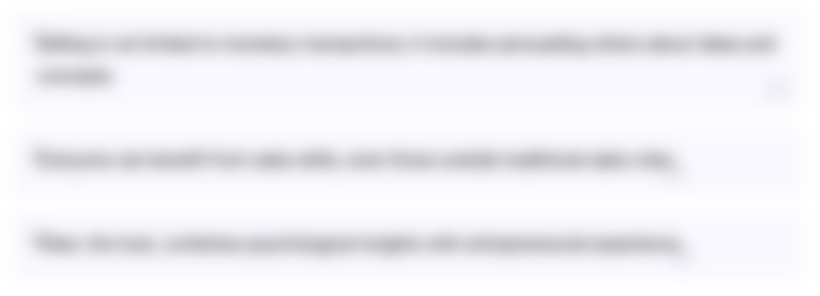
This section is available to paid users only. Please upgrade to access this part.
Upgrade NowTranscripts
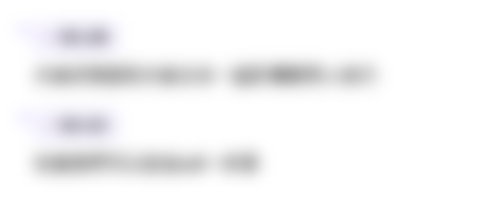
This section is available to paid users only. Please upgrade to access this part.
Upgrade NowBrowse More Related Video

The Indoor Environment: Animal Production Systems (ABE162-01.01)

Distinction between Production and Productivity I A Level and IB Economics

EDISS video series: Software Quality course at AAU
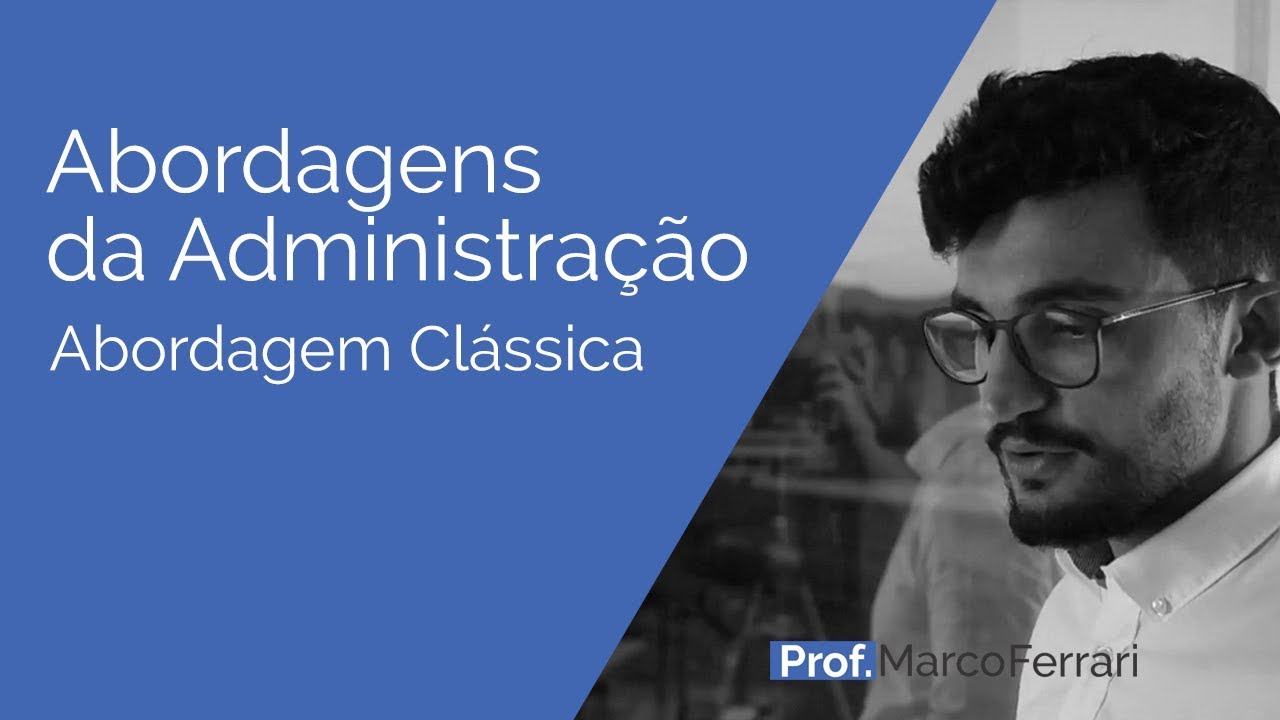
Abordagens da Administração - Abordagem Clássica
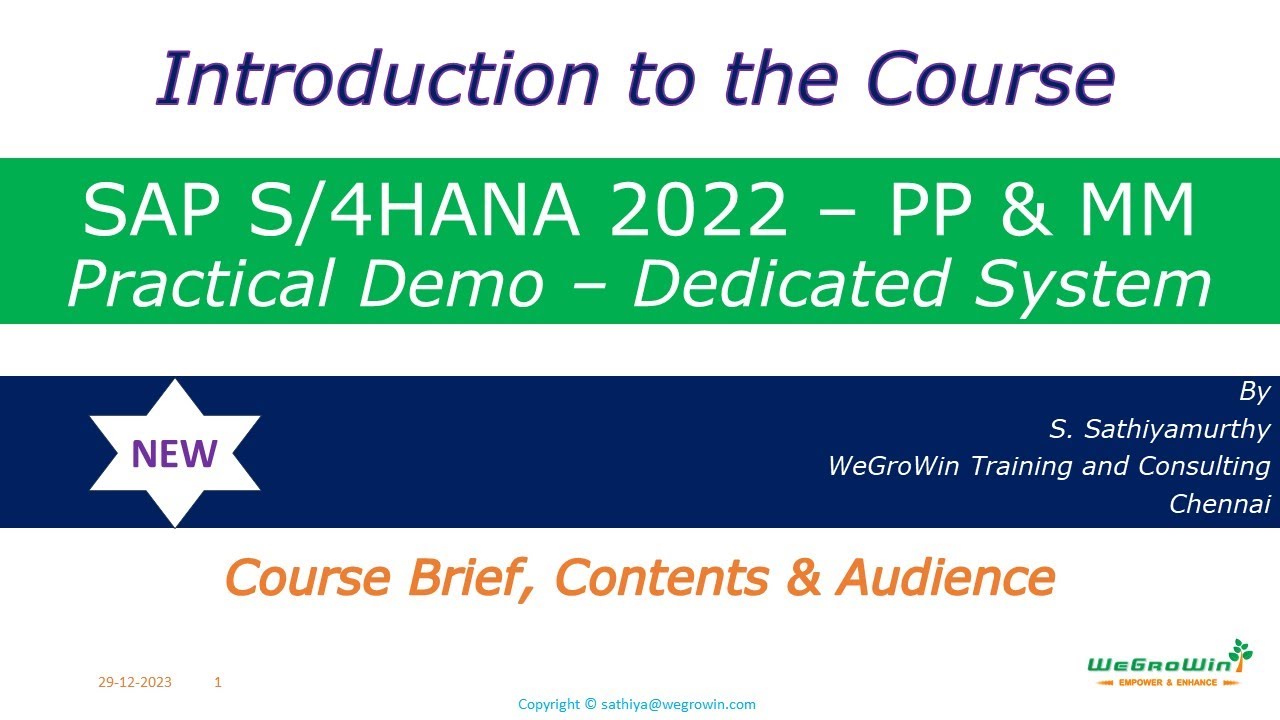
03-00 SAP S/4HANA PP MM Course with Demo - Introduction

Pendahuluan | Kuliah Silvikultur
5.0 / 5 (0 votes)