Manufacturing of a Particleboard
Summary
TLDRThis video explains the distinctive process of laboratory-scale manufacturing of particle boards in preparation for industrial production. The process involves chipping the input material, drying, and sorting it based on chip size, which impacts board strength. Chips are mixed with bonding agents, spread manually or by machine, and pre-pressed to remove air for efficient heating. The final hot pressing at around 200°C produces particle boards with properties comparable to those from industrial production. After cooling, further processing such as sanding and coating can be done.
Takeaways
- 🔬 The laboratory-scale manufacture of particle board is crucial for testing recipes and settings before industrial production.
- 🌲 The type of wood species used as input material affects the properties of the final particle board.
- 🔄 The first step in the process involves chipping the wood, which is then dried and sorted by size.
- 📏 The dimensions of the chips are critical for the board's strength and other properties.
- 🔄 Chips are mixed with bonding agents and additives in a blender, with recipes typically kept confidential.
- ⏰ Machine spreading of chips offers a significant time advantage, especially with reactive adhesives, compared to manual spreading.
- 🛠 Manual spreading allows for more flexibility in handling variable formats or chip geometries.
- 🔧 Pre-pressing is essential to remove air from the chip mat, ensuring faster and more thorough heating during hot pressing.
- 🔥 In the hot pressing process, the pre-pressed chip mat is transformed into a finished particle board at approximately 200 degrees Celsius.
- 🏭 The properties of particle boards produced in the laboratory match those of industrial-scale production, allowing for accurate testing and quality control.
- ✅ After cooling and conditioning, the particle board can undergo further processing such as sanding and coating.
Q & A
What is the first step in the laboratory-scale manufacture of particle boards?
-The first step is chipping the input material, regardless of the wood species, followed by drying and sorting the chips.
How does chip size affect the properties of the particle board?
-The dimensions of the chips significantly impact the strength and other properties of the final particle board.
What is the role of the blender in particle board production?
-In the blender, the wood chips are mixed with bonding agents and additives to form the recipe for the particle board.
Why are recipes for particle board production typically confidential?
-These recipes contain proprietary blends of bonding agents and additives that are crucial to the strength and properties of the final product.
What are the two methods of spreading the chips after blending, and how do they differ?
-The two methods are spreading by machine and spreading manually. Machine spreading is faster, especially with reactive adhesives, while manual spreading allows for more flexibility in adjusting formats or chip geometries.
What is the purpose of pre-pressing the chip mat?
-Pre-pressing removes air from the chip mat, allowing it to heat up faster during hot pressing, and provides stability for further processing without using a spreading frame.
At what temperature is the chip mat pressed into a finished particle board during hot pressing?
-The chip mat is pressed at about 200 degrees Celsius in the final hot pressing process.
How do particle boards produced in the laboratory compare to those made on an industrial scale?
-The properties of the particle boards produced in the laboratory correspond to those of boards made on an industrial scale, ensuring consistency in quality.
What steps are taken after the hot pressing of the particle board?
-After hot pressing, the particle board undergoes cooling and conditioning, followed by further processing like sanding and coating.
Why is machine spreading particularly advantageous when applying reactive adhesives?
-Machine spreading saves time, which is crucial when using reactive adhesives that may require precise and quick application.
Outlines
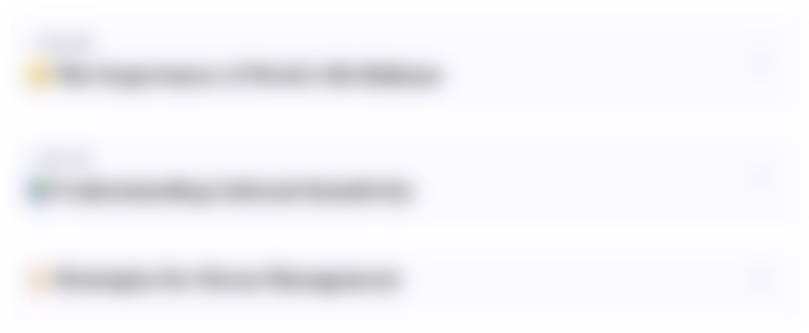
This section is available to paid users only. Please upgrade to access this part.
Upgrade NowMindmap
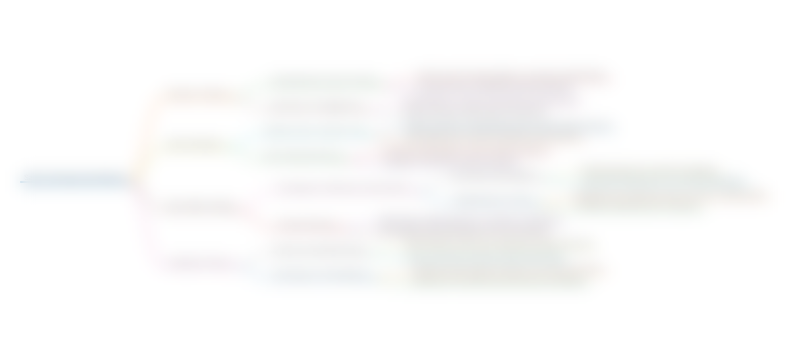
This section is available to paid users only. Please upgrade to access this part.
Upgrade NowKeywords
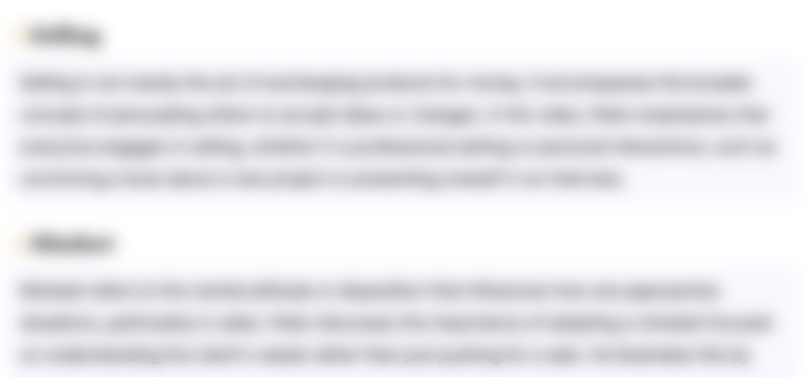
This section is available to paid users only. Please upgrade to access this part.
Upgrade NowHighlights
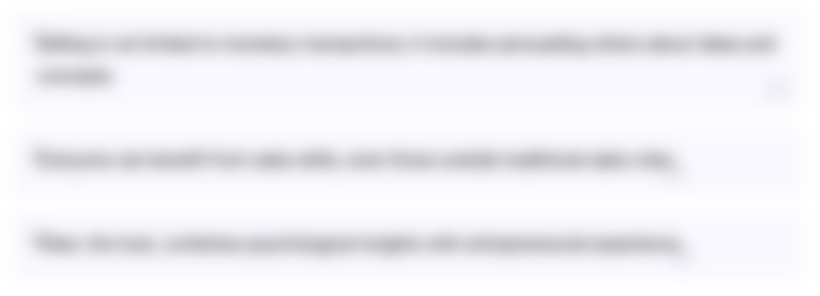
This section is available to paid users only. Please upgrade to access this part.
Upgrade NowTranscripts
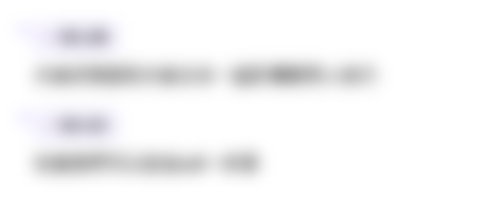
This section is available to paid users only. Please upgrade to access this part.
Upgrade Now5.0 / 5 (0 votes)