MICRONAS - Micronas Backend Overview
Summary
TLDRThe video script details the backend production process at Micronus, focusing on the meticulous testing and assembly of integrated circuits. It showcases the use of special equipment for parameter testing, probe cards for individual die testing, and the precise placement of components. The process includes dicing silicon wafers, bonding dice onto lead frames, and wire bonding. Quality control measures such as mechanical tests and statistical process control ensure reliability. The components are then molded, trimmed, and inspected, with final checks at extreme temperatures to simulate real-world applications. Each component is marked with a laser for identification, ensuring high-quality standards from Micronus.
Takeaways
- π¦ Silicon wafers are transported in dust-type boxes from the wafer fabrication facility to the backend production area.
- π¬ A comprehensive testing process includes a parameter test to ensure the integrated circuit properties meet specifications.
- π Individual die testing uses probe cards with up to 130 needles, precisely aligned to aluminum contact openings.
- π¨ Defective ICs are marked with a small colored dot for later elimination.
- π Both digital and analog circuits are tested, with up to 500 tests required for a typical IC.
- βοΈ The assembly area involves dividing tested wafers into individual dice using a dicing process with diamond-bladed saws.
- π§² Dice are bonded onto copper lead frames using an epoxy resin adhesive, which hardens in a furnace at 145Β°C.
- π Multi-chip assemblies require precise bonding and wire connections, with 276 individual wire connections applied in under 50 seconds.
- π¬ Extensive quality inspections and statistical process control are used to maintain process parameters within specification limits.
- π‘οΈ Components are molded with a plastic compound containing ultrafine glass particles to protect sensitive wire connections and prevent corrosion.
- π Post-molding, components undergo X-ray inspection to ensure the integrity of the gold wires and positioning.
- π·οΈ Each component is marked with a laser beam, including type, manufacturing date, and batch number for traceability and quality control.
Q & A
What is the first test conducted on the silicon wafers in the backend production process?
-The first test conducted on the silicon wafers is the parameter test, which ensures that the properties of the integrated circuit, such as specific transistor characteristics, comply precisely with the specifications.
How are the individual needles of the probe card positioned during testing?
-The individual needles of the probe card have to be accurately positioned on the aluminium contact openings, which are only about 100 micrometers in size.
What is done to mark defective integrated circuits during the testing phase?
-Defective integrated circuits are marked with a small colored dot on the wafer, which allows for their elimination at a later stage.
How many tests are typically necessary to check the digital and analog circuits in a micronus IC?
-In a typical case, 500 tests are necessary to check the digital and analog circuits in a micronus IC.
What is the purpose of the adhesive film used when mounting the wafers in a metal frame?
-The adhesive film ensures that the dice remain in their original position even after they've been sawn apart and that the wafer can be further processed in a reliable manner.
What is the width of the saw blades used in the dicing process?
-The saw blades used in the dicing process are fitted with minute diamonds and are only 30 micrometers wide.
How are the individual dice picked up after the dicing process?
-The individual dice are picked up by fully automatic machines with an integrated imaging system, which corrects any positioning errors.
What is the role of the copper strips in the assembly area?
-The copper strips, also known as lead frames, form the electric contact with the printed circuit board and are bonded onto the dice with an epoxy resin adhesive.
How is the electric contact between the aluminium contact surfaces on the dice and the fingers of the copper lead frame achieved?
-The electric contact is achieved through a thin gold wire, which is welded on by fully automatic wire bonders at a temperature of 200Β° C with the aid of pressure and ultrasonic energy.
What is the purpose of the plasma cleaning operation after the silver conducting adhesive has been hardened?
-The plasma cleaning operation serves to remove any organic contamination on the contact surfaces of the printed circuit board or the dice.
How is the quality of the components ensured during the molding process?
-Quality is ensured through extensive quality inspections, such as mechanical pull tests and statistical process control, which keeps individual parameters within specification limits.
Outlines
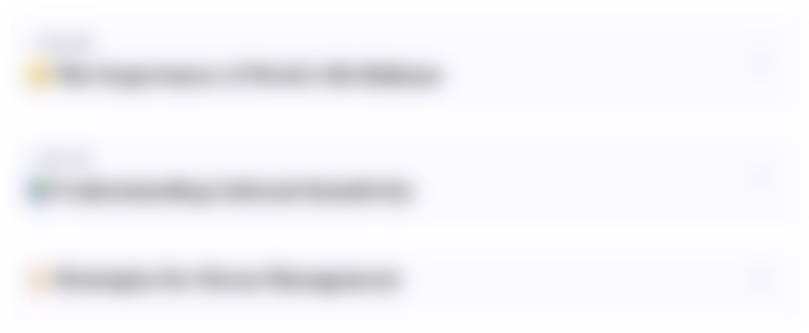
This section is available to paid users only. Please upgrade to access this part.
Upgrade NowMindmap
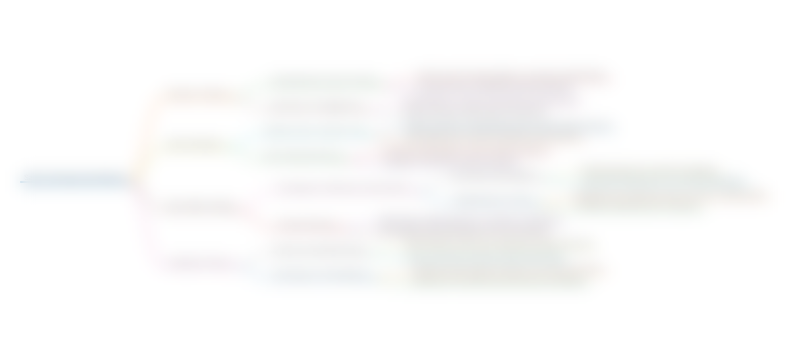
This section is available to paid users only. Please upgrade to access this part.
Upgrade NowKeywords
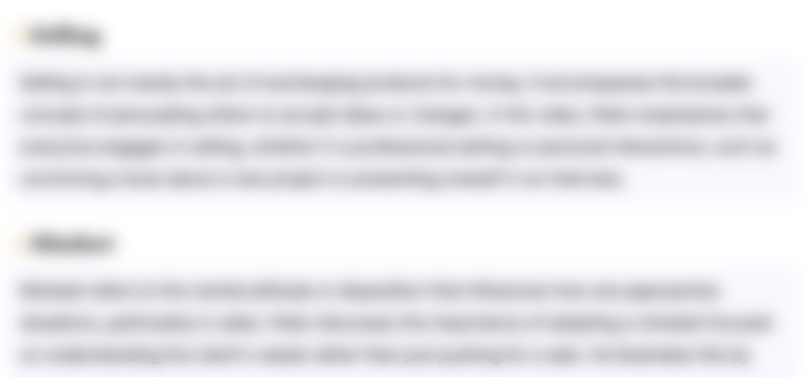
This section is available to paid users only. Please upgrade to access this part.
Upgrade NowHighlights
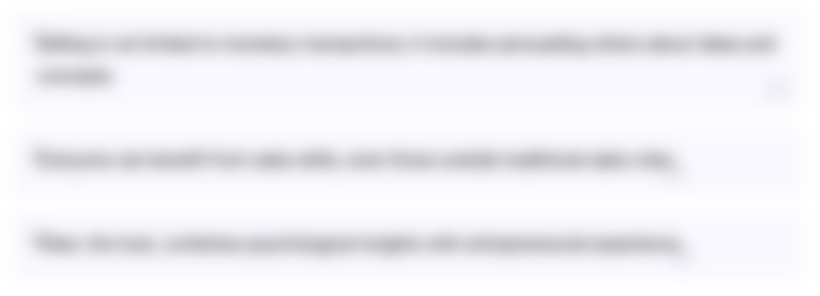
This section is available to paid users only. Please upgrade to access this part.
Upgrade NowTranscripts
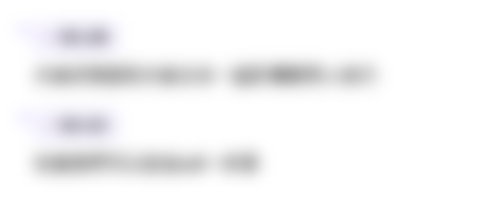
This section is available to paid users only. Please upgrade to access this part.
Upgrade NowBrowse More Related Video
5.0 / 5 (0 votes)