Marine Boiler (a repost)
Summary
TLDRThis video script discusses the critical aspects of boiler operation and maintenance on marine vessels, focusing on the importance of water quality and chemical treatment to prevent disasters like explosions and corrosion. It covers various boiler types, the role of makeup water, and the significance of monitoring and treating boiler water to maintain safety and efficiency. The script also addresses the challenges of low and high-pressure boilers, waste heat recovery systems, and the storage and handling of chemicals, emphasizing the need for rigorous adherence to operating parameters and good water management.
Takeaways
- ⚠️ Boiler explosions and failures can occur due to incorrect chemical treatment and impurities, leading to scale formation or corrosion.
- 🛠️ Marine engineers must maintain boiler operating parameters and good water management to ensure safe and cost-effective steam generation.
- 💧 Water quality is critical in boiler operation, as impurities can cause reduced heat transfer efficiency and dangerous conditions.
- 🔍 Continuous monitoring and accurate recording of makeup water consumption are essential to detect and address contamination in boiler systems.
- 🧪 Chemical treatments are necessary to reduce impurities in boiler water to recommended levels, preventing scale and corrosion.
- 🚫 Immediate action is required to address oil contamination in boiler systems, as it can severely reduce heat transfer and damage the boiler.
- 🔥 Waste heat recovery boilers and economizers can encourage sludge deposition and require special care to avoid high sediment precipitation.
- 🛑 During shutdown, boilers are susceptible to corrosion due to oxygen contamination, necessitating the use of oxygen scavengers and maintaining high pH levels.
- 💦 High-pressure water tube boilers require even more stringent chemical treatment and monitoring due to their close operational limits and high purity requirements.
- 📚 Accurate testing and treatment of boiler water are crucial, and safety procedures must be followed when handling and storing chemical treatments and reagents.
Q & A
What caused the explosion on the 10,000-ton motorship?
-The explosion was caused by a furnace collapse in a fire tube boiler due to incorrect chemical treatment, which failed to prevent scale formation.
Why did the VLCC experience a stoppage at sea?
-The VLCC experienced a stoppage at sea due to tube failure in a high-pressure boiler caused by corrosion.
What is the primary function of a boiler on board a ship?
-The primary function of a boiler on board a ship is to generate steam from water by applying heat to it.
Why is water quality critical in boiler operation?
-Water quality is critical because impurities in water can reduce heat transfer efficiency, cause scale formation, or lead to corrosion, which can weaken the boiler tube walls and lead to dangerous conditions.
What is the significance of makeup water consumption in boiler operation?
-The consumption of makeup water is a vital indication of the degree of contamination introduced into the boiler. Monitoring and recording this consumption accurately is crucial for maintaining boiler efficiency and safety.
How should boiler water be treated to prevent scale formation and corrosion?
-Boiler water should be treated with a combination of phosphate alkaline treatment to combat both acidic corrosion and scale formation. The dosage of chemicals depends on the impurities in the feed water and the results of regular boiler water tests.
What is the recommended makeup water quality for low-pressure boilers operating below 30 kg per square cm?
-For low-pressure boilers, makeup water should have impurity levels below four parts per million, which can be achieved by using evaporated seawater or fresh water.
Why is it important to monitor boiler water conditions regularly?
-Regular monitoring of boiler water conditions is important to maintain the recommended levels of chemical reserves and to ensure the boiler operates at optimum efficiency and safety.
What should be done if oil contamination is found in the boiler water?
-Immediate action must be taken to eliminate the source of contamination. The boiler should be cleaned thoroughly, refilled with distilled water, and the system should be treated with chemicals recommended by the manufacturers.
How should high-pressure water tube boilers be treated differently from low-pressure boilers?
-High-pressure water tube boilers require makeup water with less than two parts per million impurities and must be deaerated to eliminate dissolved oxygen and other gases before feeding into the boiler. They also require more accurate monitoring and treatment with an approved oxygen scavenger and a volatile amine to maintain the desired pH level.
Outlines
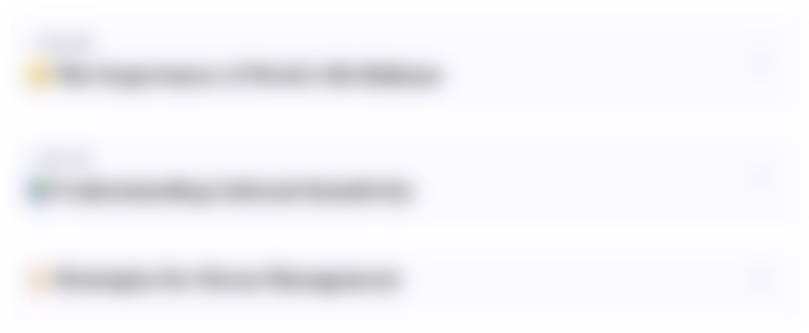
This section is available to paid users only. Please upgrade to access this part.
Upgrade NowMindmap
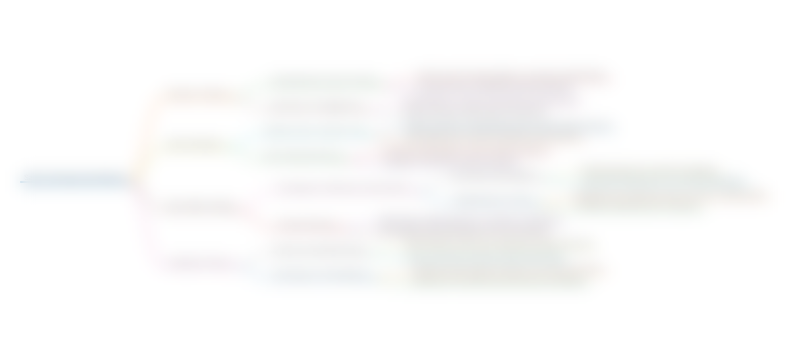
This section is available to paid users only. Please upgrade to access this part.
Upgrade NowKeywords
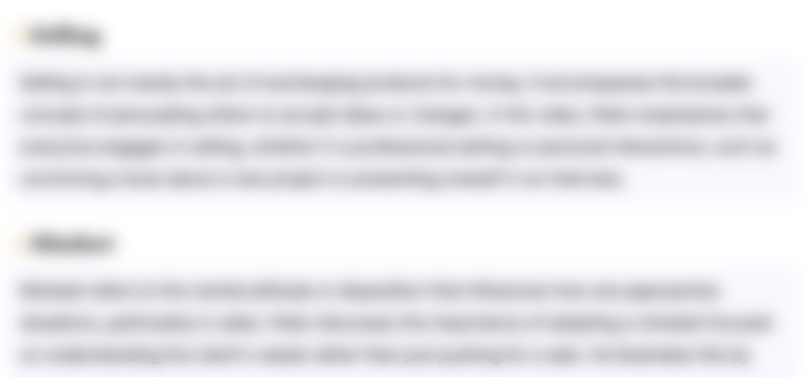
This section is available to paid users only. Please upgrade to access this part.
Upgrade NowHighlights
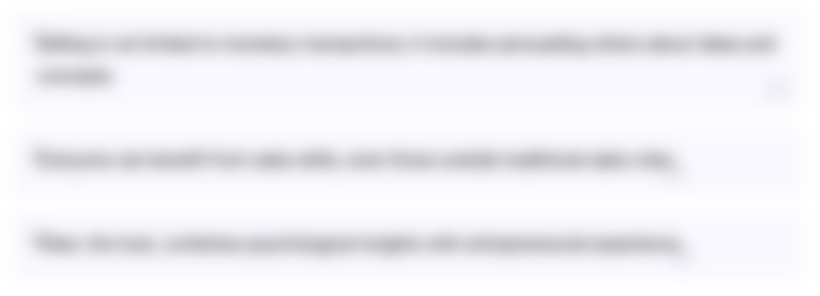
This section is available to paid users only. Please upgrade to access this part.
Upgrade NowTranscripts
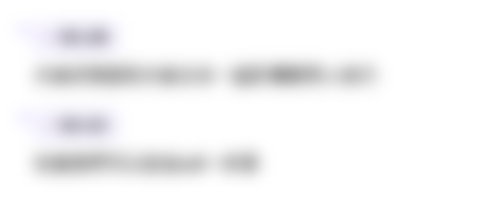
This section is available to paid users only. Please upgrade to access this part.
Upgrade NowBrowse More Related Video
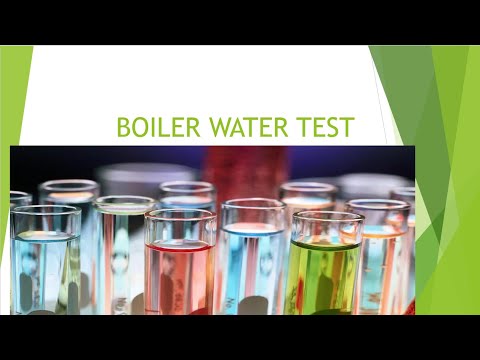
Boiler Water Treatment - Part B:MEO CLASS2 A COMPREHENSIVE GUIDE frequently asked questions included
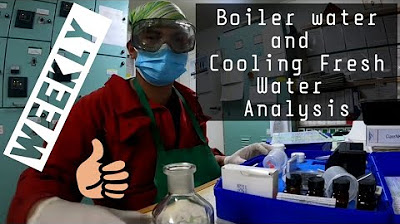
Boiler water and Cooling Fresh Water Test Onboard// Unitor Chemicals!

PENGOLAHAN AIR UMPAN KETEL (BOILER)

Without Safeguards, Pressure Vessels Can Be Deadly
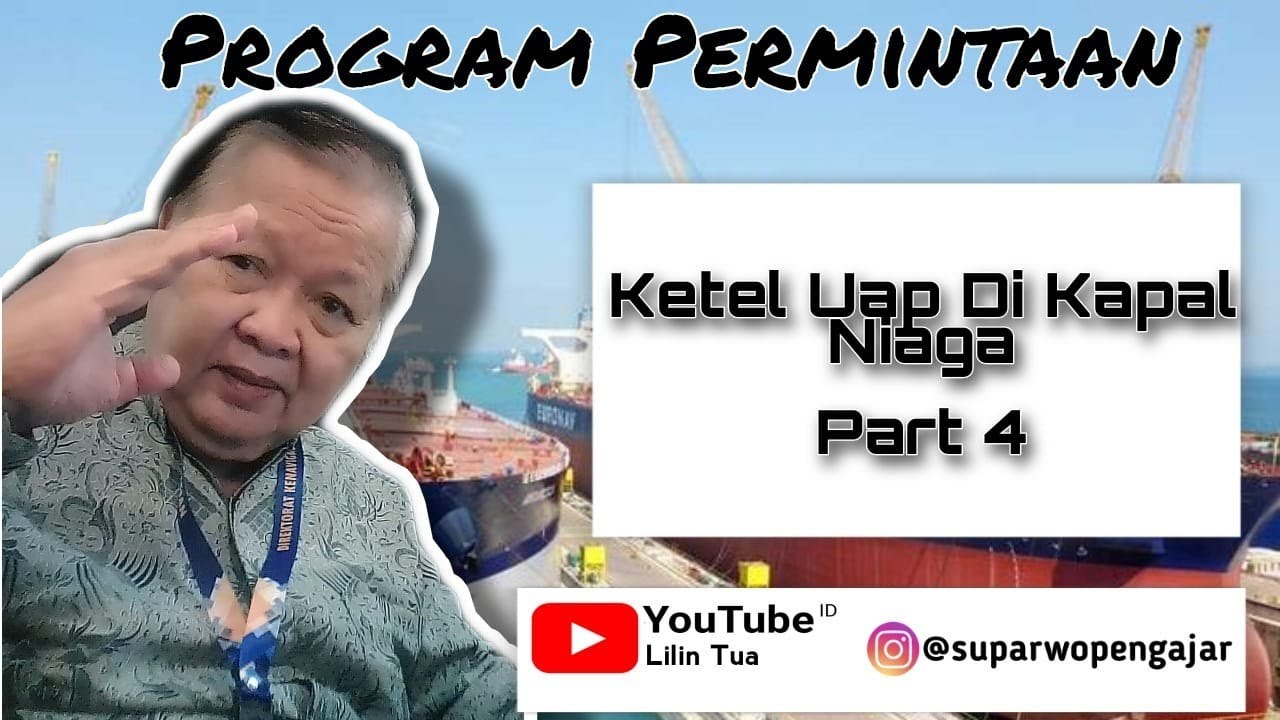
Ketel Uap di Kapal Niaga (Part 4) - Lilin Tua #belajarbersama #mesin #kapal #lilintua #engineer

Boiler water Testing and Treatment, The Unitor way! By an engine cadet
5.0 / 5 (0 votes)