Technology Development Airframe Inovation KRTI 2023 | SRI SERINDIT
Summary
TLDRThe video script introduces Sri Srided Universitas Riau's development of a vertical take-off and landing (VTOL) unmanned aerial vehicle (UAV) with foldable wings for efficient and stable flight. The UAV, named Wahana, is designed for efficient aerodynamics, with a drag coefficient of 0.037 when the propulsion system is open and 0.031 when closed. It is intended for surveillance and monitoring in challenging areas, being portable and requiring minimal space for takeoff and landing. The development process includes designing with SolidWorks 2020, manufacturing using composite materials, and 3D printing parts. The UAV is tested for maximum speed and maneuverability, with future plans to incorporate a folding arm mechanism made from hybrid composite materials.
Takeaways
- 😀 The team from Sri Srided Universitas Riau introduces their development project, showcasing advancements in the petik swing environment.
- 🚀 The project features a vertical take-off and landing (VTOL) capability with a foldable system, enhancing the branding and aerodynamics of the aircraft.
- 💡 The design is backed by the success of the Fitovic swing in 2021, which used four motors to improve thrust and reduce drag during cruise or navigation modes.
- ✈️ The aircraft's aerodynamic efficiency is demonstrated through simulations using ANSYS R1 software, achieving a drag coefficient (CD) of 0.037 with the propulsion system open and 0.031 when closed.
- 🌍 The VTOL aircraft is intended for efficient and stable flight, suitable for monitoring and surveillance in challenging areas, making it a portable option for air service providers.
- 🛠️ The aircraft's design was created using SolidWorks 2020, and its parts were manufactured using advanced composite materials and 3D printing techniques.
- 🔧 The wing and tail components were produced using a combination of fiberglass and harform composites, while the folding mechanism was 3D printed.
- 🔩 The folding arm mechanism is made of full carbon layers to ensure strength, and the aircraft's electronics are integrated into its body.
- 🛫 Flight tests were conducted to evaluate the aircraft's maximum speed, maneuverability, and vertical stability during takeoff and landing.
- 🔄 The next phase of development will focus on enhancing the folding mechanism with hybrid composite materials, aiming for improved efficiency and functionality.
Q & A
What is the name of the development team mentioned in the script?
-The development team mentioned in the script is from Sri Sri University Riau's Technology Development and Prime Division.
What is the main topic discussed in the script?
-The main topic discussed in the script is the development of a vertical take-off and landing (VTOL) unmanned aerial vehicle (UAV) called 'Wahana Sri'.
What was the inspiration behind the 'Wahana Sri' design?
-The 'Wahana Sri' design was inspired by the 'Wahana Fitovic Swing' from the 2021 KRT, which used a propulsion system with four motors to enhance lift and reduce drag during cruise or navigation mode.
What is the purpose of the foldable system in the 'Wahana Sri'?
-The foldable system in the 'Wahana Sri' is designed to allow the UAV to be compact and portable, making it easier to transport and launch without requiring a large area for takeoff and landing.
How does the foldable system contribute to the aerodynamics of the 'Wahana Sri'?
-The foldable system, when closed, reduces the drag force, which is beneficial for more efficient and stable flight. This is achieved through aerodynamic simulations using software like ANSYS R1.
What is the significance of the coefficient of drag (CD) values mentioned in the script?
-The coefficient of drag (CD) values of 0.037 when the propulsion system is open and 0.031 when it is closed indicate the efficiency of the 'Wahana Sri' in reducing drag, which is crucial for its flight performance.
What is the intended use for the 'Wahana Sri' UAV?
-The 'Wahana Sri' is intended to be used as a center for surveillance and monitoring in areas for air service providers, particularly in difficult-to-reach regions.
What materials and manufacturing techniques were used in the construction of the 'Wahana Sri'?
-The 'Wahana Sri' was constructed using SolidWorks 2020 for design, form Core composite with fiberglass coating and liquid resin using the hand layup method for the main body, 3D printing for the folding mechanism parts, and full carbon layers for the folding arms.
What software and hardware are used for the setup and flight control of the 'Wahana Sri'?
-The setup and flight control of the 'Wahana Sri' are managed using the Mission Planner application and Pixhawk controller, which involves setup configuration, vital plan, and calibration stages.
What kind of flight tests were conducted for the 'Wahana Sri'?
-The flight tests conducted for the 'Wahana Sri' included maximum speed tests and maneuverability tests in the air, as well as vertical stability evaluations during takeoff and landing.
What are the future developments planned for the 'Wahana Sri'?
-Future developments for the 'Wahana Sri' include the implementation of a folding arm system using hybrid composite materials or a combination of carbon fiber and fiberglass.
Outlines
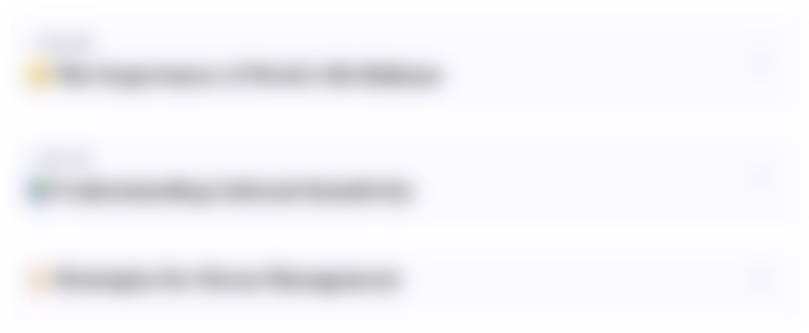
This section is available to paid users only. Please upgrade to access this part.
Upgrade NowMindmap
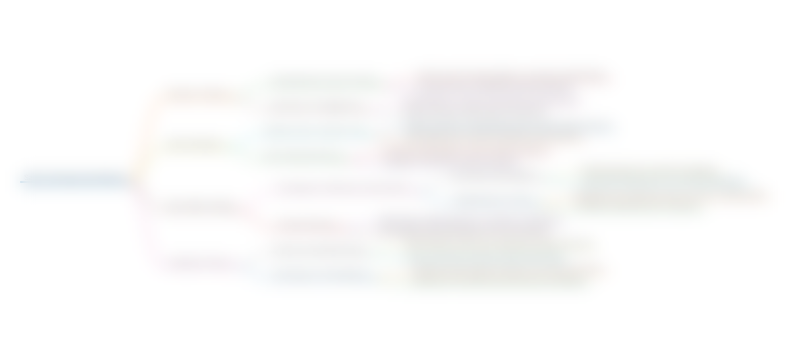
This section is available to paid users only. Please upgrade to access this part.
Upgrade NowKeywords
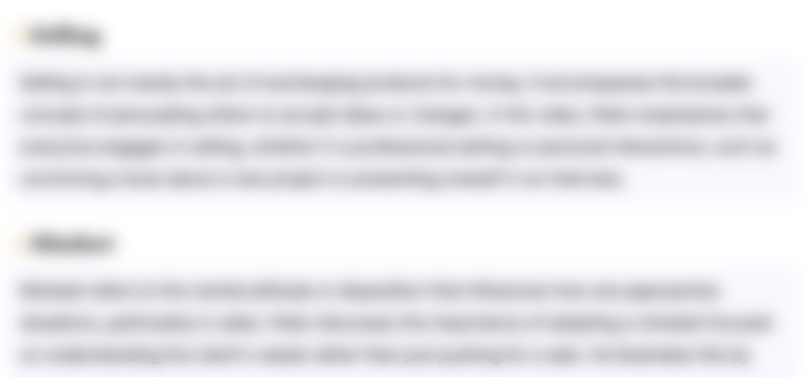
This section is available to paid users only. Please upgrade to access this part.
Upgrade NowHighlights
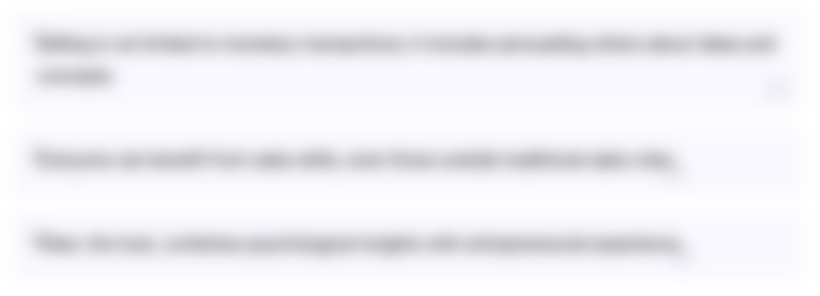
This section is available to paid users only. Please upgrade to access this part.
Upgrade NowTranscripts
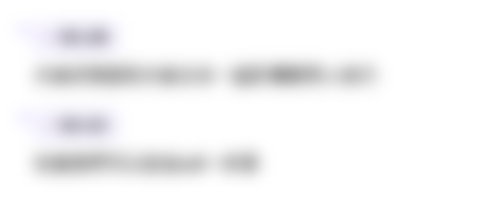
This section is available to paid users only. Please upgrade to access this part.
Upgrade NowBrowse More Related Video

CUAir: 2023 Technical Design and Flight Readiness Review
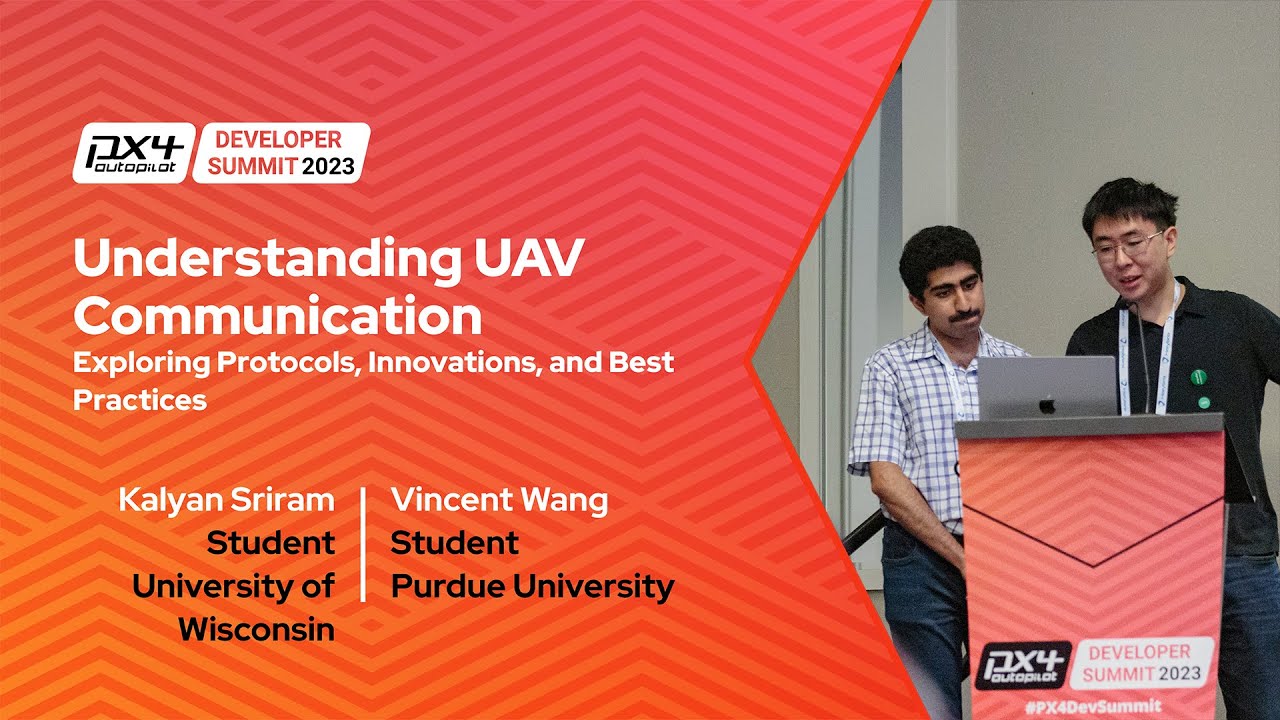
Understanding UAV Communication - Kalyan Sriram & Vincent Wang
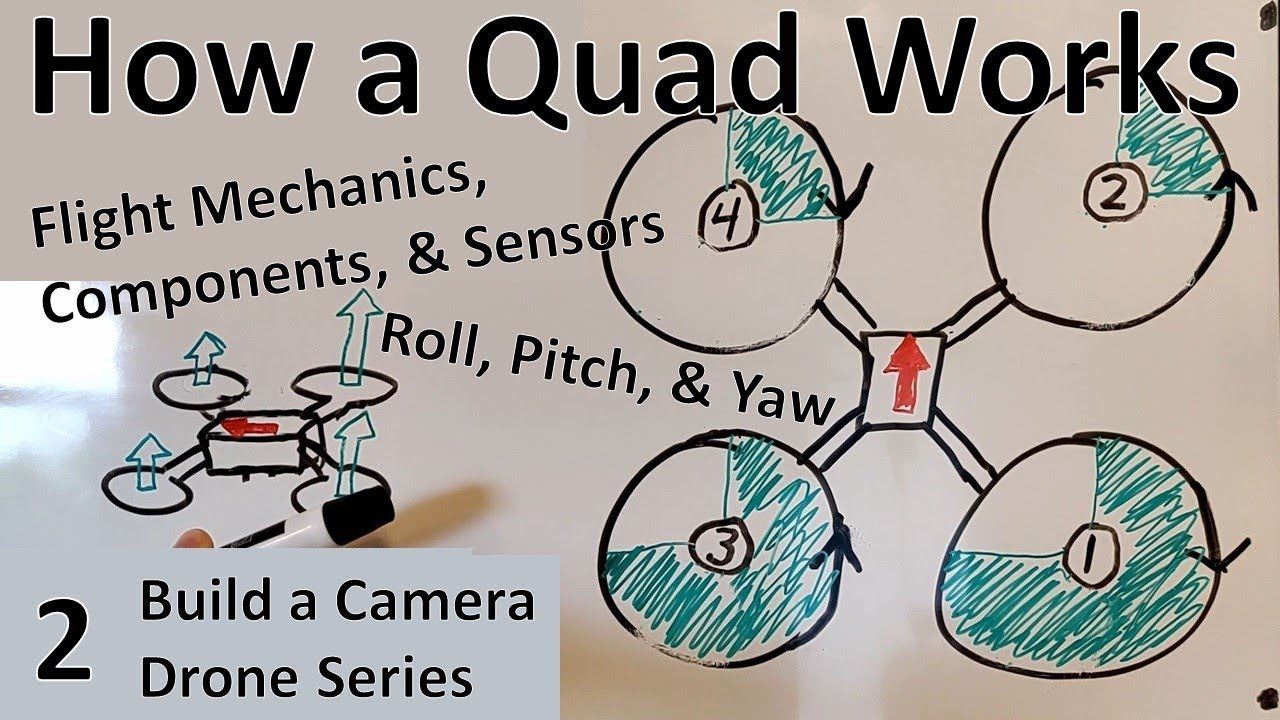
How a Quadcopter Works - Flight Mechanics, Components, & Sensors (2)
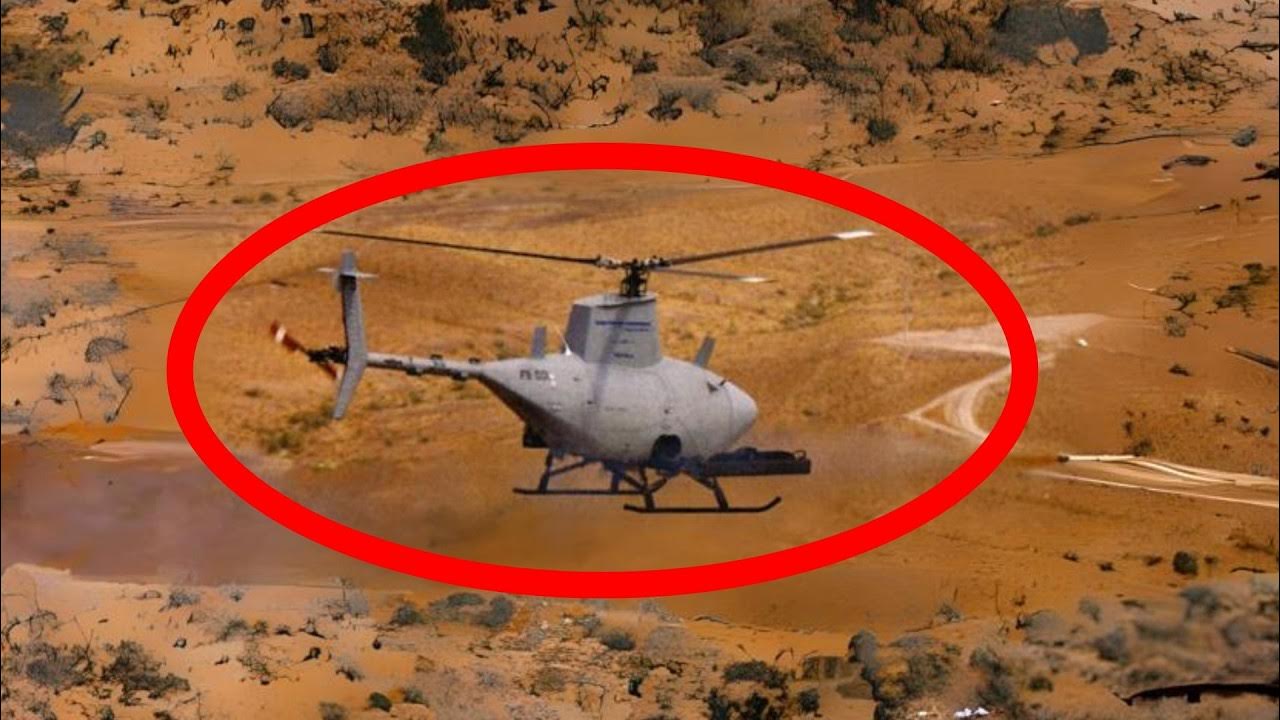
US's Surprise Flying Killer Confused with a Completely Different Aircraft
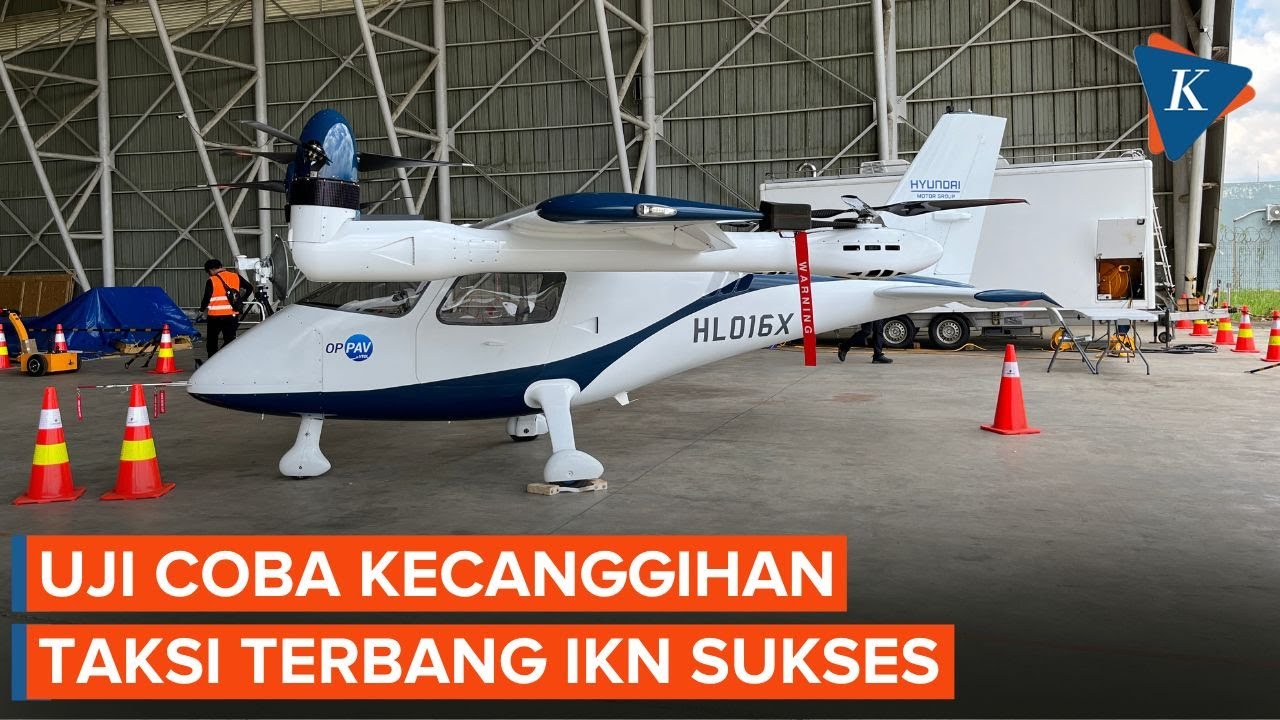
Uji Coba Taksi Terbang IKN Buatan Hyundai

Aircraft Systems - 02 - Flight Controls
5.0 / 5 (0 votes)