Industrial 3D Printing with Multi Jet Fusion (MJF)
Summary
TLDRMultijet Fusion is a 3D printing technique using nylon powder, similar to SLS but with ink agents for part centering instead of a laser. It offers a smoother surface finish, finer feature resolution, and consistent mechanical properties in all directions. The process is faster and more economical, ideal for applications requiring strength and temperature resistance, such as engine components and manufacturing jigs and fixtures.
Takeaways
- π Multijet Fusion is a 3D printing process that builds objects layer by layer.
- π§ͺ The process uses nylon powder as its base material, similar to Selective Laser Sintering (SLS).
- π¨ Instead of a laser, Multijet Fusion uses ink agents to promote sintering, leading to better part quality.
- π A carriage with multiple ink heads disperses a fusing agent to promote energy absorption and sintering, along with detailing agents to create fine surface areas.
- β¨ Multijet Fusion provides a smoother surface finish compared to SLS technology.
- π The process allows for finer feature resolution and more consistent mechanical properties in all directions (X, Y, Z).
- β© It offers faster build speeds, making it a more economical choice.
- βοΈ As it uses engineering-grade nylon powders, the technology is expected to be used in similar applications as SLS, especially where strength or higher temperature resistance is needed.
- π Ideal applications include engine components like housings, bellows, baffles, and manufacturing tools like jigs and fixtures.
- π‘οΈ The technology is well-suited for applications requiring higher temperature resistance and mechanical strength.
Q & A
What is multi-jet fusion 3D printing?
-Multi-jet fusion is a 3D printing process that uses nylon powder as its base material and ink agents to promote sintering, similar to selective laser sintering but without the use of a laser.
How does the multi-jet fusion process differ from selective laser sintering?
-The major difference is that multi-jet fusion uses ink agents instead of a laser to promote the sintering of the nylon powder, with a carriage that disperses both a fusing agent and detailing agents across the part bed.
What are the key components of the multi-jet fusion process?
-The key components include a carriage with ink heads that disperse a fusing agent for energy absorption and sintering, as well as detailing agents at the bounding edge to create a fine surface area.
What benefits does multi-jet fusion offer over traditional SLS technology?
-Multi-jet fusion offers smoother surface finish, finer feature resolution, more consistent mechanical properties in all directions, and faster overall build speeds, making it a more economical process.
What type of materials are used in multi-jet fusion 3D printing?
-Multi-jet fusion uses nylon powders, which are engineering-grade materials suitable for various applications requiring strength and temperature resistance.
How does the detailing agent contribute to the quality of the printed parts?
-The detailing agent helps create a fine surface area at the bounding edge of the part, which contributes to better overall part quality.
What are some applications where multi-jet fusion technology is particularly advantageous?
-It is advantageous in applications requiring strength or higher temperature resistance, such as engine components like housings, bellows, or baffles, and in manufacturing jigs and fixtures.
How does the surface finish of parts produced by multi-jet fusion compare to SLS?
-The surface finish of parts produced by multi-jet fusion is smoother compared to those made by SLS technology.
What does the carriage in a multi-jet fusion printer do?
-The carriage in a multi-jet fusion printer passes back and forth over the entire part bed, dispersing ink agents that promote sintering and detailing.
How does the use of ink agents in multi-jet fusion affect the build speed?
-The use of ink agents allows for faster build speeds due to the promotion of energy absorption and sintering of the nylon powder.
What are the mechanical property advantages of multi-jet fusion over SLS in the X, Y, and Z directions?
-Multi-jet fusion provides more consistent mechanical properties across all directions, which can be beneficial for parts that require uniform strength and durability.
Outlines
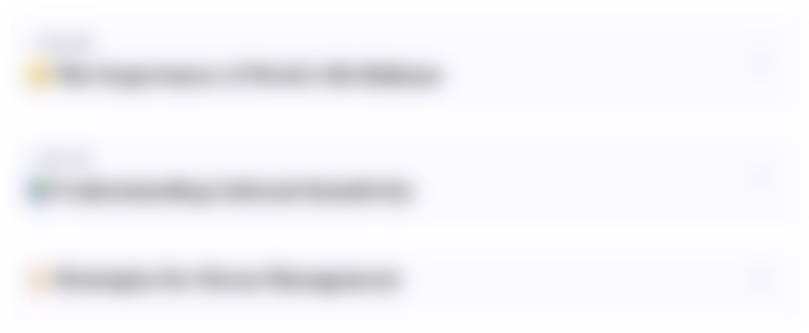
This section is available to paid users only. Please upgrade to access this part.
Upgrade NowMindmap
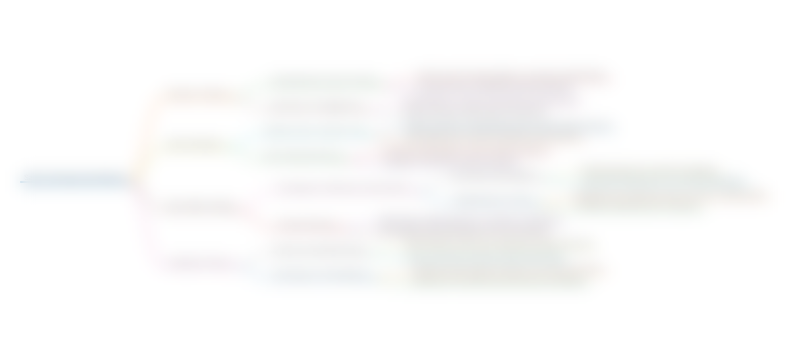
This section is available to paid users only. Please upgrade to access this part.
Upgrade NowKeywords
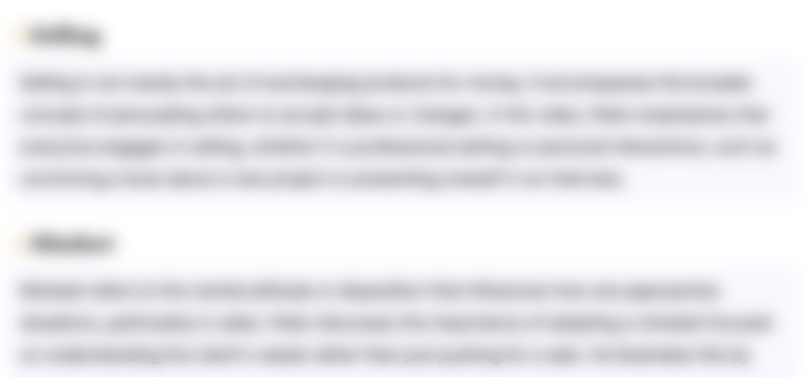
This section is available to paid users only. Please upgrade to access this part.
Upgrade NowHighlights
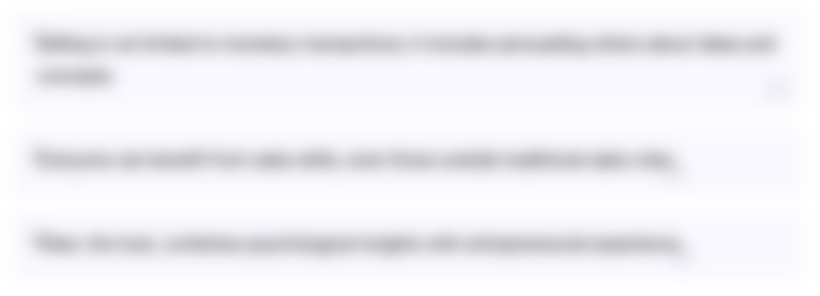
This section is available to paid users only. Please upgrade to access this part.
Upgrade NowTranscripts
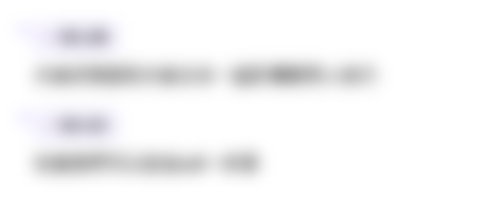
This section is available to paid users only. Please upgrade to access this part.
Upgrade NowBrowse More Related Video
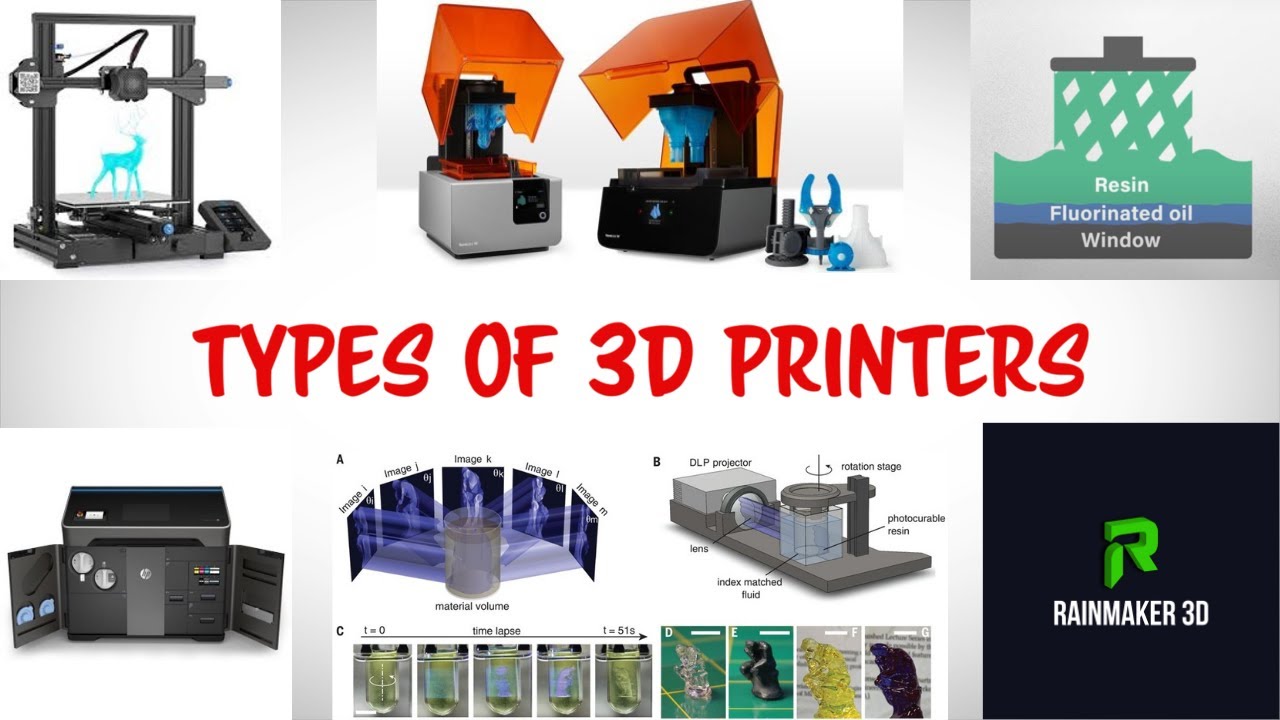
Types of 3D Printers - 11 Different Types of 3D Printers - Introduction to 3D Printing
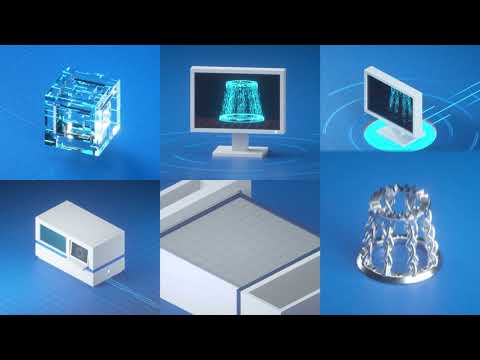
What is additive manufacturing? | GE Additive

Is 3D Printed Food the Future?
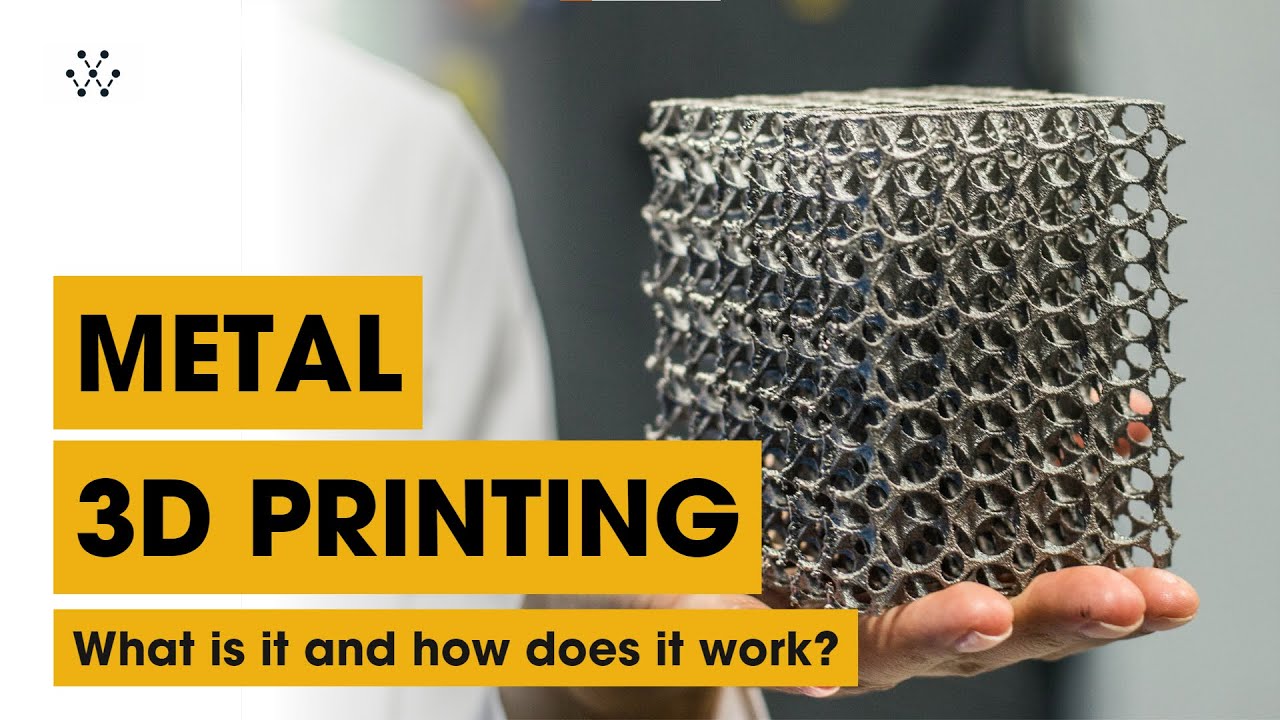
METAL 3D PRINTING | What is it and how does it work ?

Digital Light Processing DLP 3D Printing Process
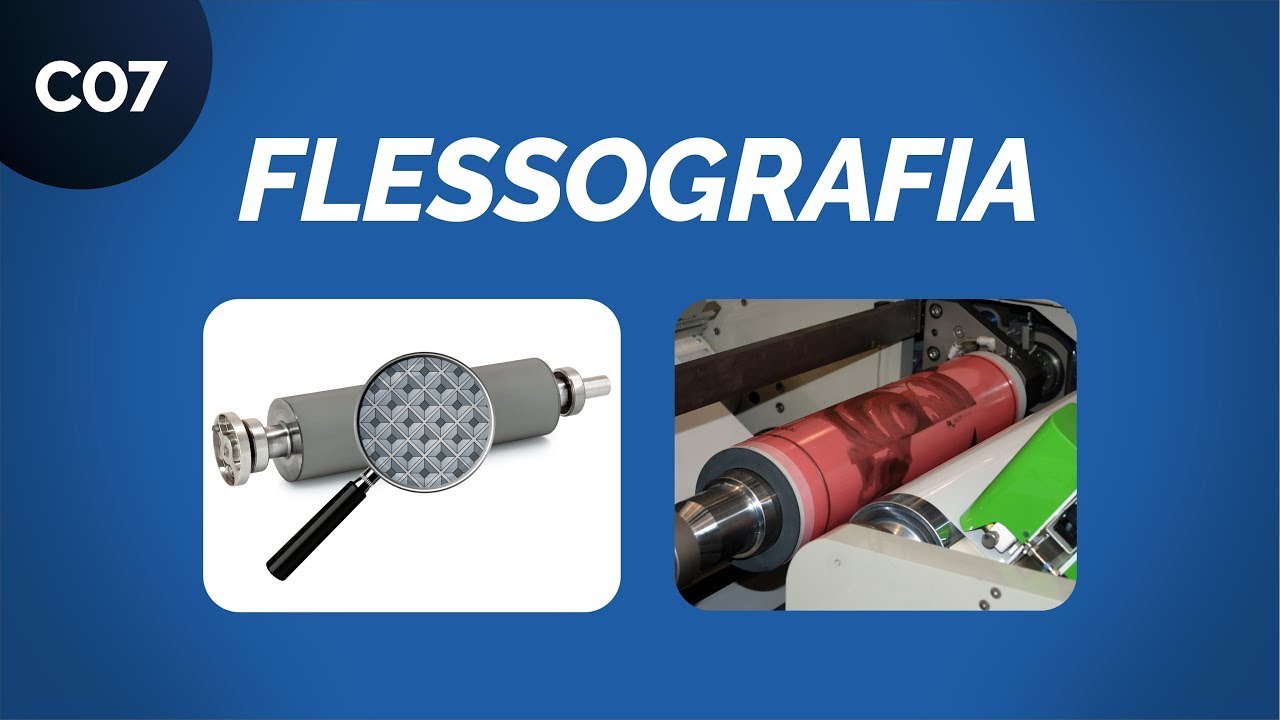
Flessografia: stampa su confezioni e imballi // Daniele Cogo
5.0 / 5 (0 votes)