HOW RACKET IT'S MADE...VICTOR RACKET....
Summary
TLDRThe video script details the meticulous process of crafting badminton rackets with carbon fiber shafts. It begins with wrapping prepreg fabric around a metal cylinder, followed by heating to form a solid, lightweight material. Workers then mold the shaft and frame using various prepregs, ensuring uniformity. The rackets undergo quality checks for durability and are assembled with wooden handles. The final steps include painting, decal application, and stringing preparation. The manufacturer produces rackets in different sizes for all skill levels.
Takeaways
- 🏸 The game of badminton is considered faster and more intense than tennis by its fans in India.
- 🛠️ The production of badminton rackets involves meticulous steps, starting with wrapping carbon fiber fabric called prepreg around a metal cylinder.
- 🔥 The prepreg is then heated in an oven to transform it into a solid, lightweight, and super-strong carbon fiber material.
- 📐 A specialized device is used to remove the metal cylinder, leaving a hollow shaft which is a crucial part of the racket.
- 🎨 The racket frame is manufactured using a different formulation of prepreg material, which is folded into thin strips and wrapped around a mold to shape the frame.
- 🔩 The carbon fiber shaft is introduced into the mold, and another piece of carbon fiber forms the joint between the frame and the shaft.
- 🔨 The shaping machine heats and cools the prepreg to form the racket frame, which is then removed with excess resin that needs to be expelled and cleaned.
- 🔩 Drilling is done to create holes in an offset pattern for stringing the racket, with larger holes to prevent two strings from passing through.
- 🛡️ Quality control involves testing the racket frame's durability to ensure it can withstand a certain amount of pressure before breaking.
- 🎨 The rackets are painted with a base coat and then meticulously decorated with decals, which are soaked in water for easier application.
- 🔩 Grommets are nailed into the holes of the racket, ensuring they are the correct length and then smoothed out with a pressing machine.
- 🔗 The wooden handle and cap are attached to the shaft, and the components are assembled to complete the racket.
- 📏 A precision device measures the weight, swing weight, and balance point of the racket with high accuracy, ensuring performance standards are met.
Q & A
What material is used to create the carbon fiber shafts of badminton rackets?
-The carbon fiber shafts of badminton rackets are created using a material called prepreg, which is a carbon fiber fabric.
How is the prepreg material initially shaped around the metal cylinder?
-The prepreg material is tightly wrapped multiple times around a metal cylinder by a worker, and then encased in plastic to hold it in place.
What happens to the prepreg during the heating process in the oven?
-The heating process in the oven transforms the wrapped prepreg into a solid, lightweight, and super strong carbon fiber material.
What is the purpose of the specialized device used after the heating process?
-The specialized device is used to remove the metal cylinder from the carbon fiber, leaving behind a hollow shaft.
How is the racket frame initiated in the manufacturing process?
-The racket frame is initiated by a worker using a different formulation of prepreg material, which is folded into thin strips.
What is the importance of ensuring each strip of prepreg material is identical?
-Ensuring each strip is identical is crucial for maintaining uniformity and quality in the final racket frame shape.
How is the shape of the racket frame created?
-The shape of the racket frame is created by a worker wrapping the prepreg strip around a purpose-built mold and introducing the carbon fiber shaft into it.
What is the function of the shaping machine in the production process?
-The shaping machine heats and then cools the prepreg over the course of about 30 minutes to form the fully shaped racket frame.
Why is resin removed from the racket frame after the shaping process?
-Resin is removed because it is used to hold the carbon fibers together before the curing process, and it needs to be expelled through heating.
What is the purpose of drilling holes in the racket frame?
-Holes are drilled in the racket frame to make it easier to string the racket, with different hole sizes to accommodate the strings properly.
How is the quality of the racket frame assessed before it is strung?
-Quality control inspectors randomly select a racket frame and test how much pressure it can bear before reaching the breaking point.
What is the final step in assembling the badminton racket?
-The final step in assembling the badminton racket is adding the wooden handle and cap to the shaft and putting everything together.
What is the purpose of the painting department in the racket production process?
-The painting department applies a base coat and then meticulously applies a series of decals to the rackets for aesthetic and branding purposes.
How are the grommets attached to the racket frame?
-Grommets are attached by sliding each hole over a pin at the base of a nailing machine, which then nails the specially designed grommets into the holes.
What is the role of the pressing machine in the final stages of racket production?
-The pressing machine heats and then presses the cut side of the grommets to smooth them out, ensuring a flush fit with the frame.
How is the handle wrap applied to the racket handle?
-A worker clamps the racket into a winding machine, brushes glue onto the handle, secures one end of the handle wrap at the base, and uses a foot pedal to turn the racquet while maintaining steady tension and the correct angle.
What technology is used to mark the product ID number on the racket shaft?
-A laser is used to quickly and accurately burn the product ID number into the shaft.
How is the weight, swing weight, and balance point of the racket measured?
-A precision-engineered device is used to measure the weight, swing weight, and balance point of the racket with incredible accuracy.
What variety of racket sizes does the manufacturer produce?
-The manufacturer produces rackets in different sizes suited to every level of badminton player.
Outlines
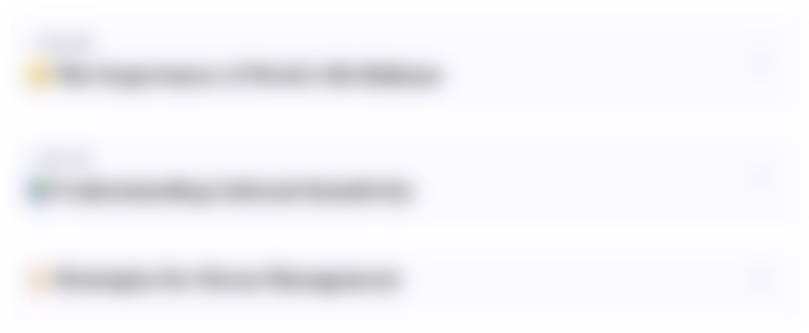
This section is available to paid users only. Please upgrade to access this part.
Upgrade NowMindmap
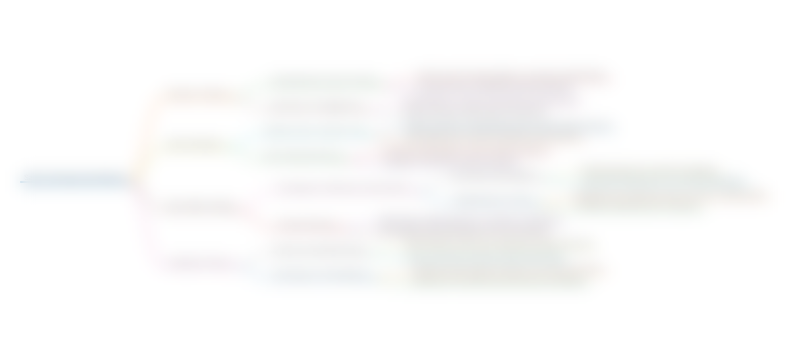
This section is available to paid users only. Please upgrade to access this part.
Upgrade NowKeywords
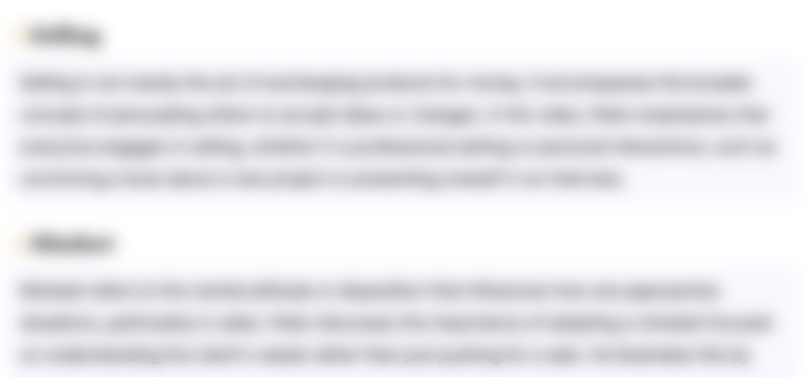
This section is available to paid users only. Please upgrade to access this part.
Upgrade NowHighlights
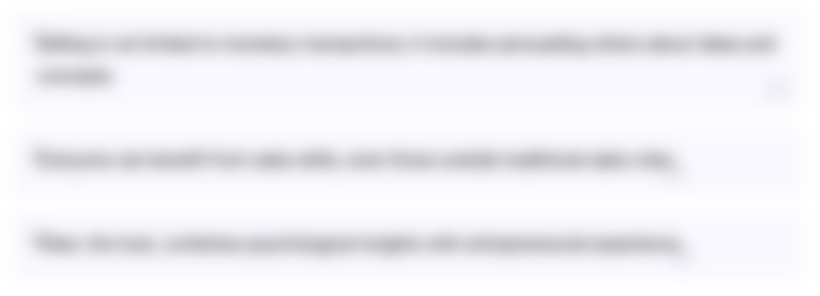
This section is available to paid users only. Please upgrade to access this part.
Upgrade NowTranscripts
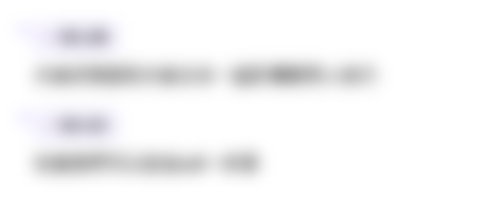
This section is available to paid users only. Please upgrade to access this part.
Upgrade NowBrowse More Related Video

รีวิว HUNDRED AEROFLASH X ATTK และ CTRL | Tai - Shan Badminton

Golf Clubs | How It's Made

Yonex Nanoflare 700 - Tour vs Game vs Play Second Gen Nanoflare Badminton Racket Comparison

VIDEO PEMBELAJARAN PJOK SD KELAS 4 - Permainan Bulutangkis
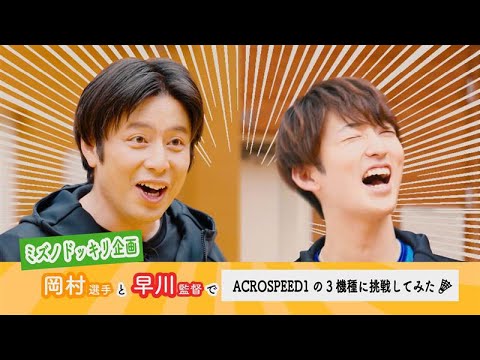
【ドッキリ試打】ACROSPEEDの3機種を早川監督と岡村選手が挑戦!

Lebih Kuat Dari Baja, Proses Pembuatan Carbon Fiber Di Pabrik
5.0 / 5 (0 votes)