From Start to Finish: How The Boeing 787 Is Made
Summary
TLDRThe Boeing 787 Dreamliner, launched in 2009, revolutionized aviation with its composite construction and fuel efficiency, despite facing design and production challenges. It marked a shift towards smaller, more efficient aircraft, influencing Airbus to develop the A350. The 787's production is globally dispersed, with final assembly centralized in North Charleston, South Carolina. The aircraft's innovative use of composite materials reduced weight and maintenance needs, but quality control issues have impacted production rates and deliveries.
Takeaways
- 🛫 The Boeing 787 Dreamliner, first flown in 2009, revolutionized widebody aircraft with its composite construction and increased efficiency.
- 🌏 The 787's production involves a global supply chain with key components manufactured by suppliers in various countries and assembled in the US.
- 🏗️ Despite initial design and construction issues, the 787 remains a successful and popular aircraft, continuing Boeing's legacy of innovative widebody planes.
- 📈 The 787 was designed to be around 20% more efficient than the 767, with a focus on lower operating costs and reduced environmental impact.
- 🔧 Major design changes for efficiency included composite fuselage construction, aerodynamic improvements like raked wingtips, and new, more efficient engines from General Electric or Rolls-Royce.
- 💼 The 787 project, initially called 7E7, emphasized 'efficiency' and was launched in 2003, with the first customer order in 2004.
- 💰 The development cost for the 787 was over $32 billion, reflecting the high expenses of creating a new clean-sheet aircraft design.
- 🌍 The 787's ambitious 'Dream Tour' in 2011-2012 showcased the aircraft globally, highlighting Boeing's marketing efforts post-launch.
- 🤝 The 787 and Airbus A350 exemplify the competitive dynamic between Boeing and Airbus, with each company learning from the other's strategies.
- 🚀 The 787's production process is highly outsourced, with major components like wings, fuselage sections, and landing gear built by third-party companies worldwide.
- 📚 The consolidation of 787 production to Boeing's North Charleston facility in 2021 reflects adjustments to demand and production rate changes in the industry.
Q & A
When did the Boeing 787 Dreamliner first fly?
-The Boeing 787 Dreamliner first flew in 2009.
What was the main goal of the 787 Dreamliner's design?
-The main goal of the 787 Dreamliner's design was to create a more efficient widebody aircraft with lower operating costs and a reduced environmental impact.
Which engine manufacturers' engines can the 787 Dreamliner use?
-The 787 Dreamliner can use engines from either General Electric GEnx or Rolls-Royce Trent 1000.
What was the initial project name for the 787 before it was branded as the Dreamliner?
-The initial project name for the 787 was 7E7, with the 'E' standing for 'efficiency'.
What was the estimated total development cost for the 787 Dreamliner?
-The total development cost for the 787 Dreamliner was estimated at over $32 billion.
When did the 787 Dreamliner enter service?
-The 787 Dreamliner entered service in October 2011 with All Nippon Airways (ANA).
How does the 787 Dreamliner's composite construction contribute to its efficiency?
-The 787 Dreamliner's composite construction, using carbon fiber composite components, makes the aircraft lighter and stronger, contributing to a 20% weight reduction and lower maintenance requirements.
What is the significance of the Dreamlifter in the production of the 787 Dreamliner?
-The Dreamlifter, developed from the 747-400, is used to efficiently transport aircraft components from various locations to the final assembly factories in South Carolina and Washington.
Why was a second assembly line added for the 787 Dreamliner in North Charleston?
-A second assembly line was added in North Charleston in 2011 to handle the increased production rate of the 787 Dreamliner.
What are some of the key components and their respective manufacturers for the 787 Dreamliner?
-Key components and their manufacturers include the main wings by Mitsubishi Heavy Industries in Japan, the wingtips by Korean Air in Korea, and the aft fuselage section by Boeing itself.
What challenges did the 787 Dreamliner face in terms of production and quality control?
-The 787 Dreamliner faced several production and quality control issues, including problems with shims used to fill gaps in the fuselage, wider than allowable gaps in the horizontal stabilizer, and issues with decompression panels.
How has the COVID-19 pandemic affected the production rate of the 787 Dreamliner?
-The COVID-19 pandemic, along with quality control issues, significantly slowed the production rate of the 787 Dreamliner, falling from 14 aircraft per month in 2019 to five per month by the end of 2020.
Outlines
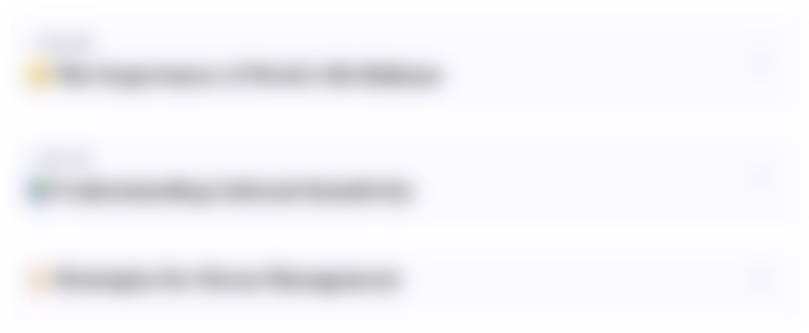
Этот раздел доступен только подписчикам платных тарифов. Пожалуйста, перейдите на платный тариф для доступа.
Перейти на платный тарифMindmap
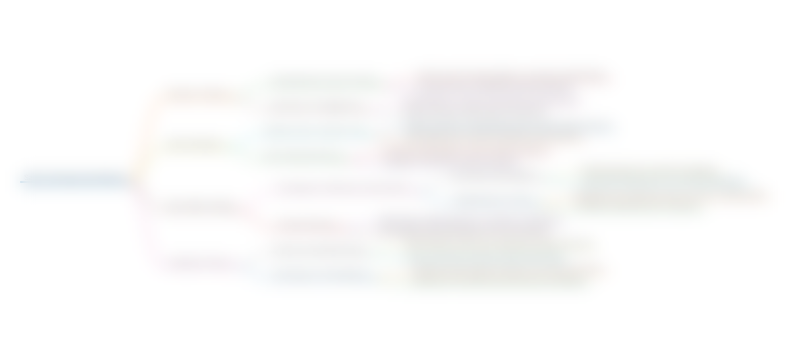
Этот раздел доступен только подписчикам платных тарифов. Пожалуйста, перейдите на платный тариф для доступа.
Перейти на платный тарифKeywords
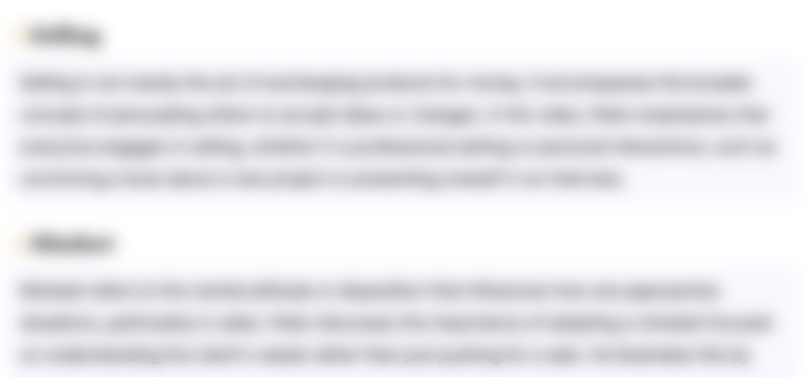
Этот раздел доступен только подписчикам платных тарифов. Пожалуйста, перейдите на платный тариф для доступа.
Перейти на платный тарифHighlights
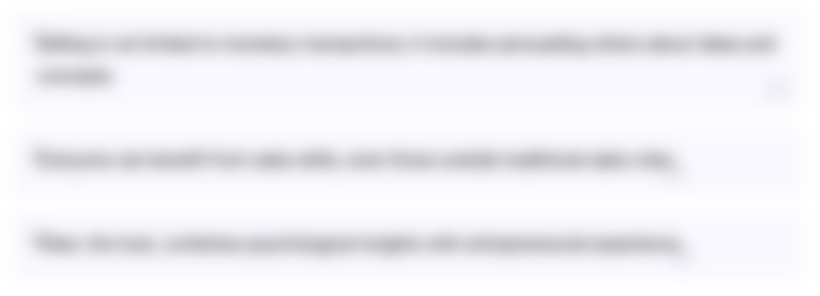
Этот раздел доступен только подписчикам платных тарифов. Пожалуйста, перейдите на платный тариф для доступа.
Перейти на платный тарифTranscripts
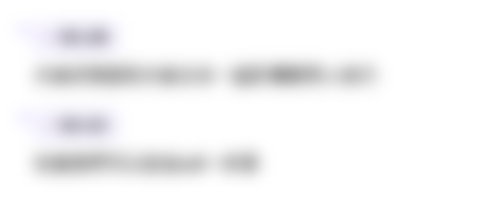
Этот раздел доступен только подписчикам платных тарифов. Пожалуйста, перейдите на платный тариф для доступа.
Перейти на платный тарифПосмотреть больше похожих видео
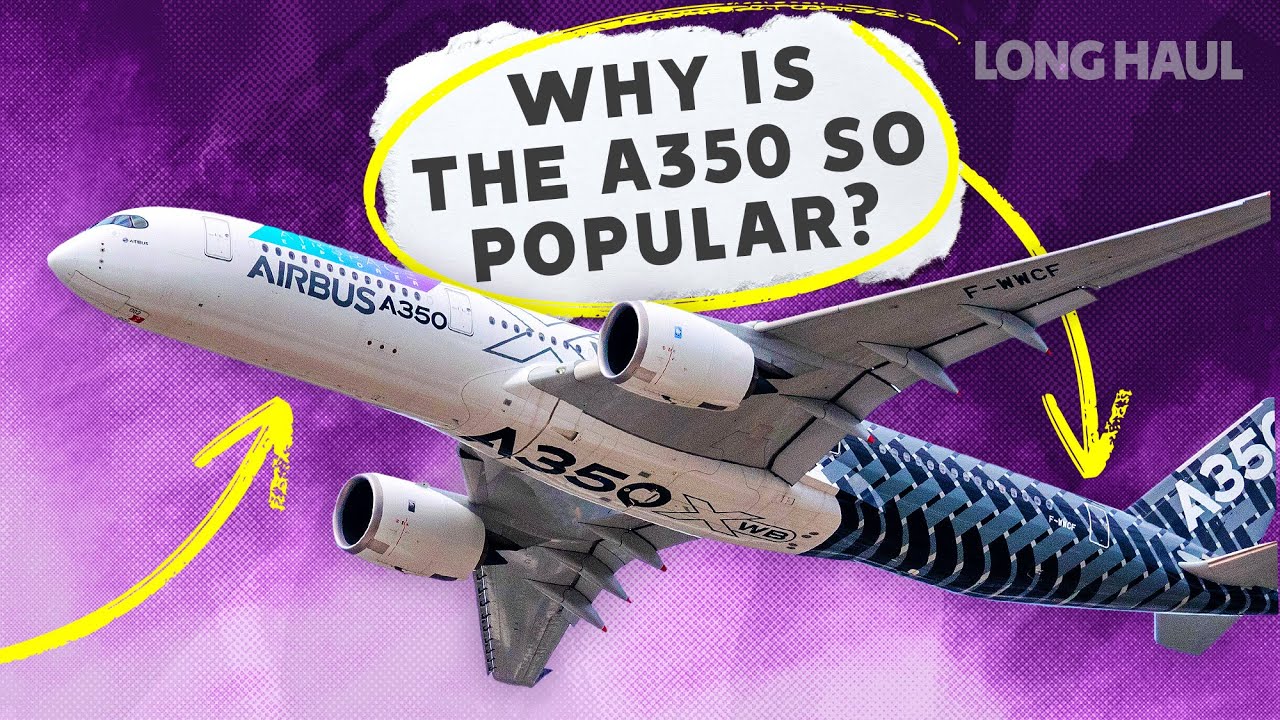
Why The Airbus A350 Has Quickly Become A Favorite For Airlines, Pilots & Passengers
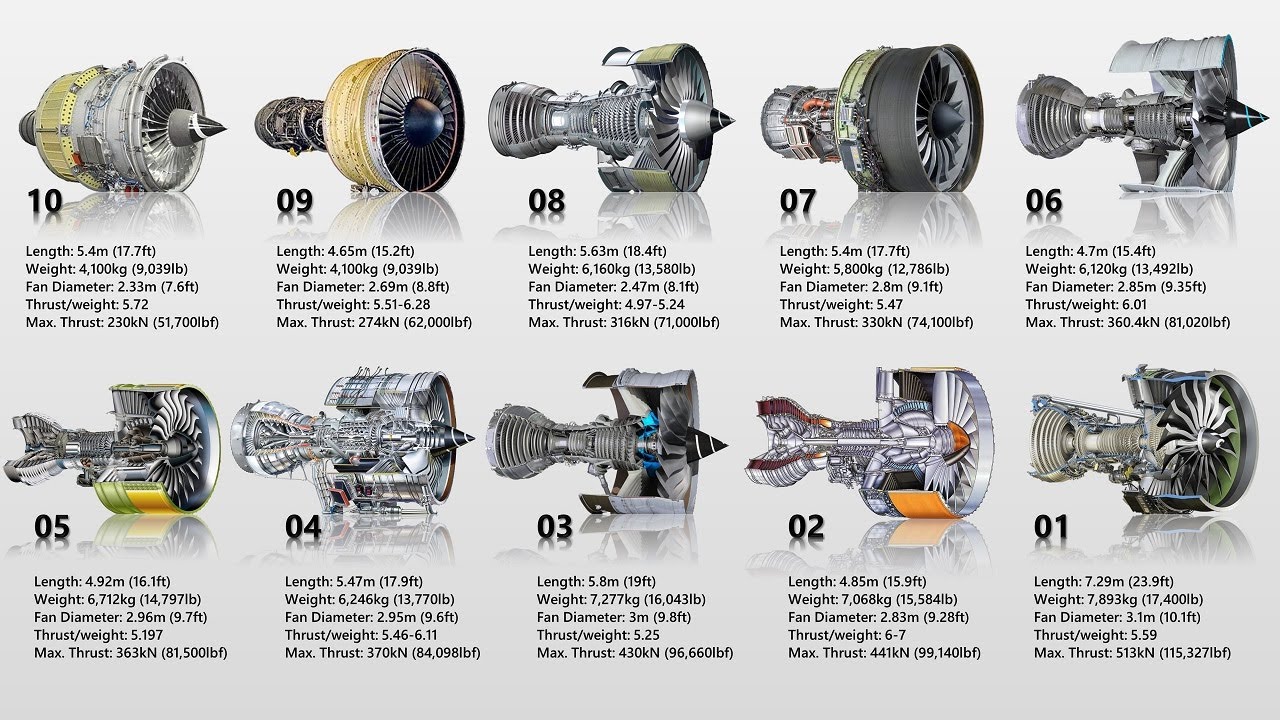
Top 10 Most Powerful Aircraft Engines In The World (2022)

Evolution Of Boeing Passenger Aircraft (1916 - 2022)
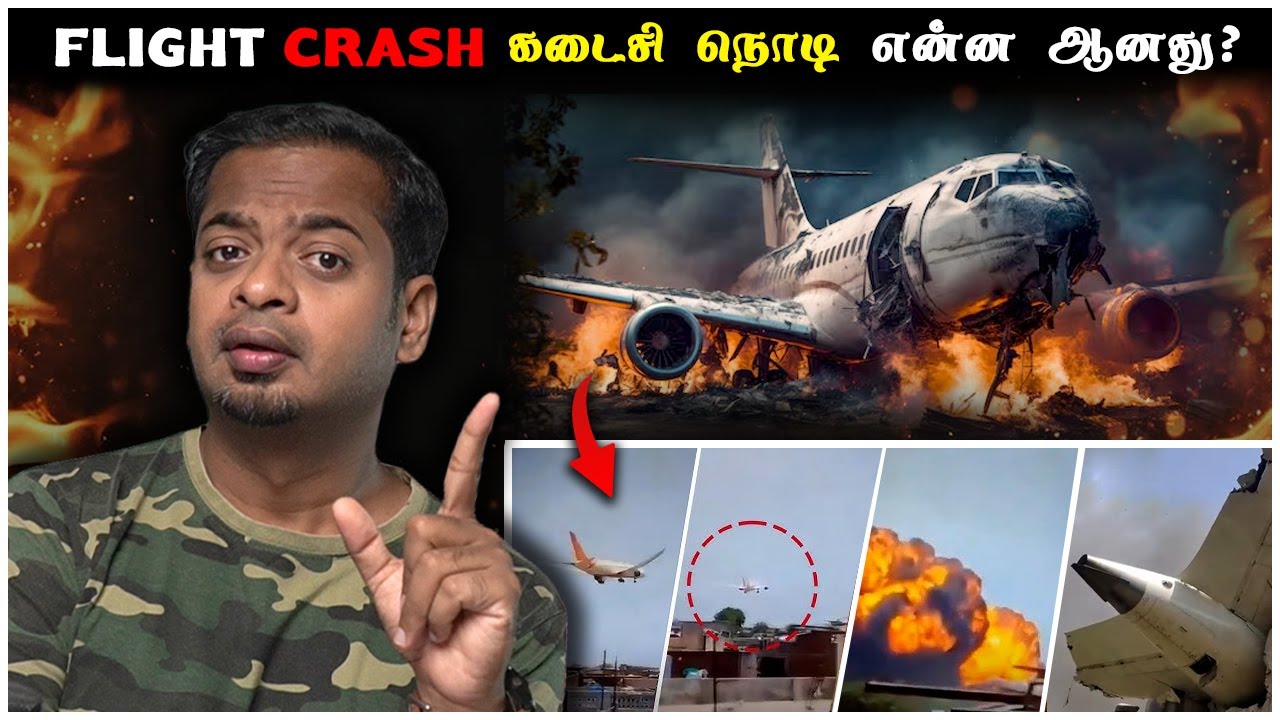
😱 WORST Flight Crash EVER 😡Ahmedabad Airport ல் உண்மையில் நடந்தது என்ன? | Mr.GK

Shocking Report OUT ; DREAMLINER FUEL SWITCH OFF? | Face to Face
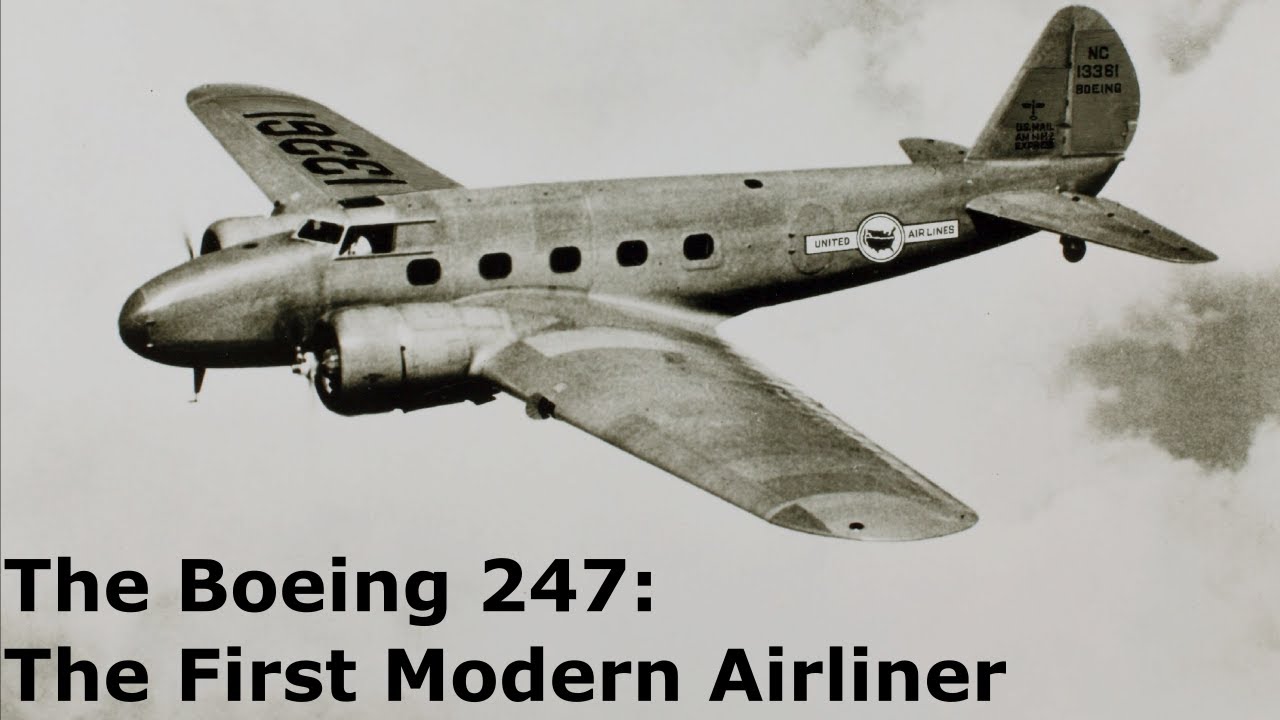
The First Modern Airliner: The Boeing 247
5.0 / 5 (0 votes)