23KG Chassis | Carbon Monocoques & Formula SAE [#TECHTALK]
Summary
TLDRIn this interview, Ben from University of Canterbury Motorsport walks through the fascinating process of manufacturing a carbon monocoque chassis for a Formula Student car. He explains the advantages of using carbon fiber over traditional steel, highlighting its lightweight yet highly stiff properties, crucial for torsional rigidity and suspension performance. The conversation delves into the detailed steps of manufacturing, from designing the chassis to creating molds and assembling the monocoque. Ben also compares the benefits and challenges of partial versus full carbon monocoques, offering insights into material choices and their impact on performance, weight, and heat management in combustion and electric race cars.
Takeaways
- 😀 Carbon monocoques are commonly used in high-level motorsport, but the Formula Student competition utilizes them in a unique context for student-built cars.
- 😀 The construction of a carbon monocoque involves sandwich panel construction with carbon fibre outer and inner skins, and a core made from honeycomb material for optimal stiffness-to-weight ratio.
- 😀 The use of a carbon fibre chassis offers advantages like high torsional rigidity, flexibility for attaching components, and lightweight design compared to conventional steel tube frames.
- 😀 High torsional rigidity ensures that the suspension system performs as intended, without the chassis flexing, which would otherwise compromise suspension response and handling.
- 😀 The torsional stiffness target is determined through experience and testing, using data from previous builds and considering suspension stiffness for optimal chassis-suspension interaction.
- 😀 The process of measuring torsional stiffness involves applying weight to a bar extending from the chassis and calculating the force required for rotation.
- 😀 Manufacturing a carbon monocoque involves early design work, the creation of plugs from MDF, carbon fibre moulds, and a series of curing steps to produce the final chassis.
- 😀 Carbon tooling is chosen for its ability to withstand the high temperatures of curing, preventing distortion and ensuring the precision needed for high-quality carbon fibre monocoques.
- 😀 The manufacturing timeline for a carbon monocoque is lengthy, often taking several months from design finalization to the completed build, with careful attention to quality control at every stage.
- 😀 A hybrid approach of using a partial carbon monocoque with a steel spaceframe at the rear is used in the combustion car for better heat management and easier serviceability due to engine size constraints.
- 😀 The use of a full carbon monocoque in the electric car results in significant weight savings (23 kg) while achieving impressive torsional stiffness (3800 Nm/°), showcasing the performance benefits of this approach.
Q & A
What is a carbon monocoque and why is it used in motorsport?
-A carbon monocoque is a chassis structure made from carbon fiber, often in a sandwich panel design with an outer and inner skin and a core layer. It's used in motorsport because it offers high stiffness-to-weight ratio, torsional rigidity, and greater flexibility in design compared to traditional steel spaceframes.
How does the sandwich panel construction of a carbon monocoque benefit the design?
-The sandwich panel construction provides high stiffness while keeping the weight low. The outer and inner carbon fiber skins provide strength, while the honeycomb core adds additional stiffness without significantly increasing weight.
What are the main advantages of using a carbon fiber chassis over a steel tube frame?
-The main advantages include a better stiffness-to-weight ratio, higher torsional rigidity, and design flexibility. A carbon fiber chassis also allows easier attachment of parts and eliminates the need for welding, streamlining the manufacturing process.
Why is torsional rigidity important in the design of a racing car?
-Torsional rigidity is crucial because it ensures the chassis does not flex under load, allowing the suspension to perform optimally. If the chassis is too flexible, it can distort the suspension's behavior, affecting the car's handling and performance.
How do you measure the torsional stiffness of a car's chassis?
-Torsional stiffness is measured by fixing the chassis to a table, applying a twisting force with a bar, and measuring the rotation. The force required for a specific amount of rotation is then used to calculate the torsional stiffness.
What is the process of manufacturing a carbon monocoque chassis?
-The process involves designing the car, creating MDF plugs for the tooling, and then using those plugs to produce carbon fiber molds. The carbon fiber is laid up on the molds, cured under heat and pressure, and hard points for attachments are inserted. After curing, the molds are removed, revealing the finished chassis.
Why is carbon fiber used for the tooling in the manufacturing process, despite being expensive?
-Carbon fiber is used because it has the same thermal expansion properties as the carbon fiber used for the chassis. This prevents distortion during the high-temperature curing process, ensuring a high-quality finished product.
How long does it take to manufacture a carbon monocoque chassis from design to finished product?
-The process takes about three months in total. This includes around two weeks to receive the machined MDF molds, two to three weeks to prep and paint the molds, about six days for the tooling layup, and one to two weeks for curing the inner and outer skins.
Can the tooling for a carbon monocoque be reused after the first chassis is built?
-Yes, the tooling can be reused for up to eight or nine cycles before it needs resurfacing. While some repair may be necessary between uses, it remains usable for multiple chassis builds.
What are the key differences between a full carbon monocoque and a partial monocoque with a steel spaceframe?
-A full carbon monocoque provides superior stiffness and is lighter, while a partial monocoque with a steel spaceframe at the rear, like in the combustion car, allows for better heat management and easier engine fitment, especially when the engine is delivered late in the design process.
Outlines
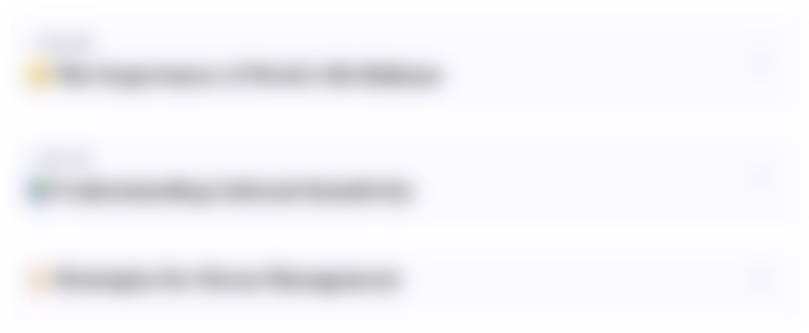
Этот раздел доступен только подписчикам платных тарифов. Пожалуйста, перейдите на платный тариф для доступа.
Перейти на платный тарифMindmap
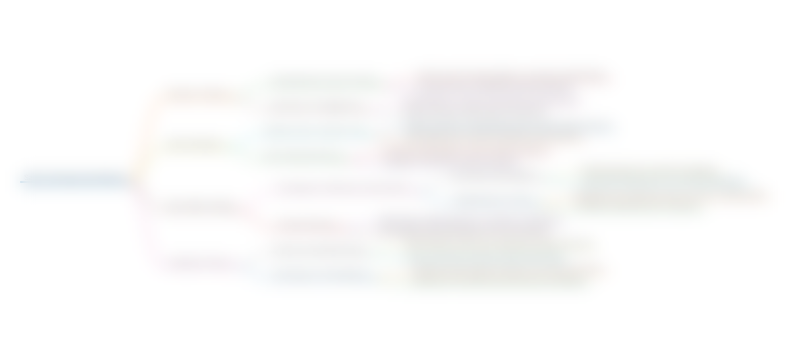
Этот раздел доступен только подписчикам платных тарифов. Пожалуйста, перейдите на платный тариф для доступа.
Перейти на платный тарифKeywords
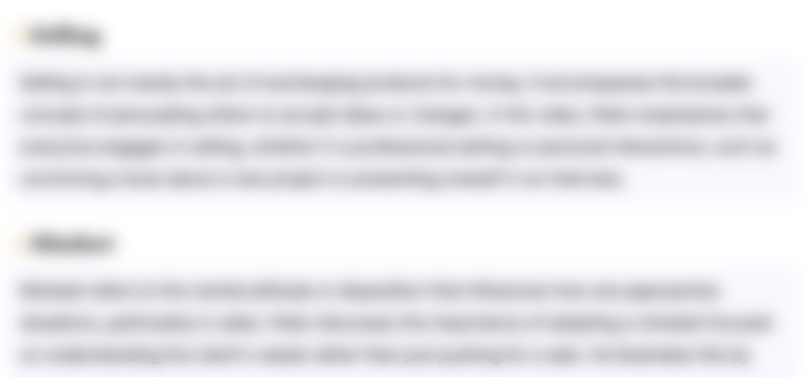
Этот раздел доступен только подписчикам платных тарифов. Пожалуйста, перейдите на платный тариф для доступа.
Перейти на платный тарифHighlights
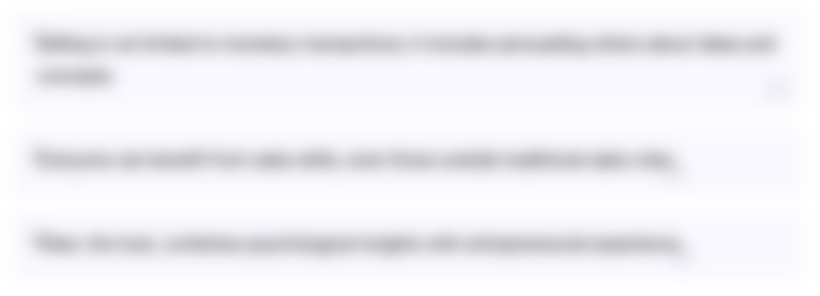
Этот раздел доступен только подписчикам платных тарифов. Пожалуйста, перейдите на платный тариф для доступа.
Перейти на платный тарифTranscripts
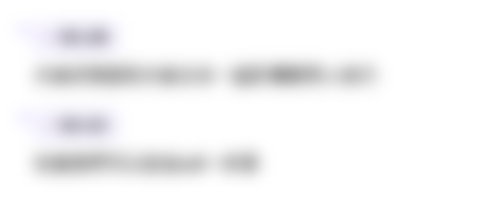
Этот раздел доступен только подписчикам платных тарифов. Пожалуйста, перейдите на платный тариф для доступа.
Перейти на платный тарифПосмотреть больше похожих видео

Le MOTEUR de l'HYPERCAR est installé ! berceau arrière [Hypercar project #20]
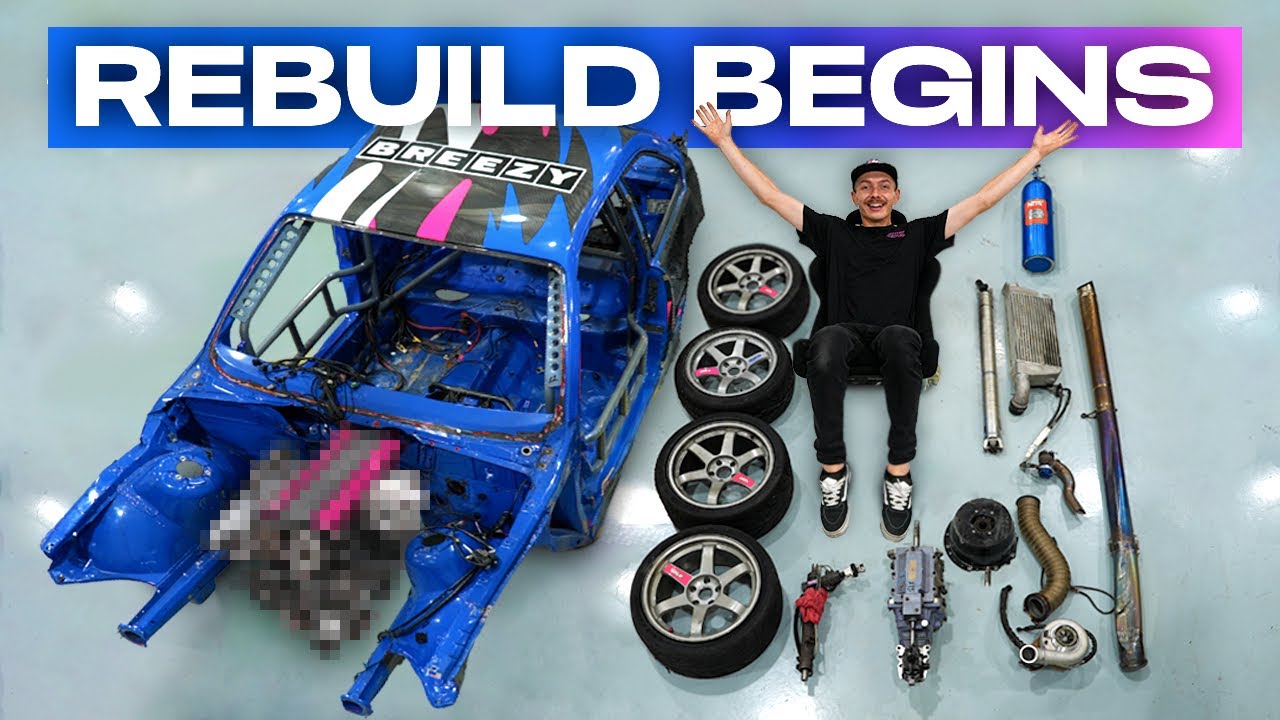
1 WEEK to rebuild my 1000HP E36 & SAVE my Formula Drift season

McLaren Tech Club - Episode 21 - How to build a carbon fibre monocoque
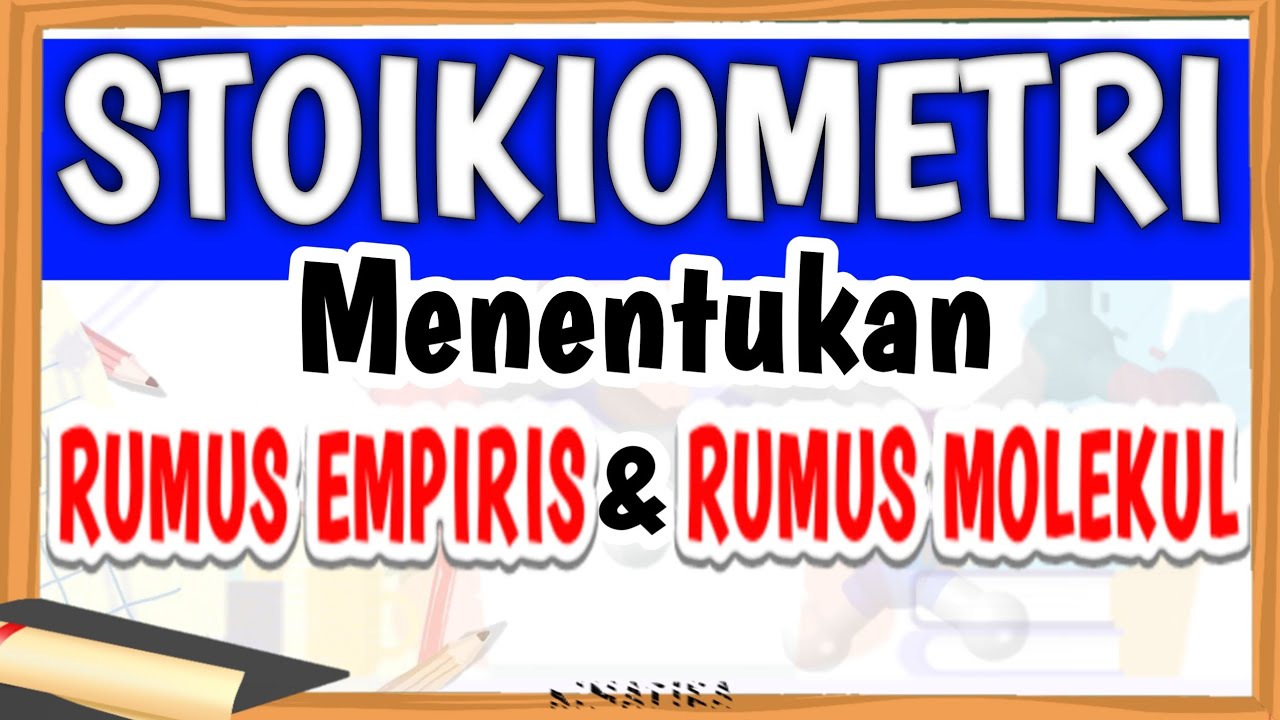
Stoikiometri (3) | Menentukan Rumus Empiris Dan Rumus Molekul | Kimia Kelas 10

☕️ Curso de Java na prática - Construtores - aula 7 - POO - Parte 2/7 #java #javase #javatutorial

priv
5.0 / 5 (0 votes)