Process of Making Ball Bearings. A Mechanical Parts Manufacturing Factory in Korea.
Summary
TLDRYH System, based in Gimpo, Korea, specializes in the production of precise mechanical parts, including ball bearings. The process starts with raw iron material, which undergoes a series of steps: sawing, heating, heat forging, and detailed inspections. Advanced techniques like fine cutting, 3D measuring, and heat treatment ensure precision. The ball bearings are then plated, laser-marked, and finely ground before being assembled, injected with grease, and sealed. The entire process is focused on achieving high-quality, durable bearings for various applications.
Takeaways
- 😀 The ball bearing production starts with selecting iron as the raw material.
- 😀 The first step in manufacturing involves cutting the raw iron material into the required size using a sawing process.
- 😀 The material is then heated to prepare it for shaping and further processing.
- 😀 Heat forging is used to shape the material under high pressure and temperature, improving its structure.
- 😀 After the forging process, the material undergoes a thorough inspection to check its quality before moving forward.
- 😀 A fine cutting process is employed to achieve precise shaping of the components.
- 😀 The use of a 3D measuring machine ensures accuracy and precision in the material's dimensions.
- 😀 The bearing material undergoes a hardening heat treatment to enhance its strength and durability.
- 😀 After hardening, another inspection is conducted to ensure the material has undergone the heat treatment process correctly.
- 😀 The bearings undergo a plating process, which may involve coating for corrosion resistance or other properties.
- 😀 Laser marking is applied to the bearings for identification, branding, and serialization purposes.
- 😀 A fine grinding process is used to smooth the components and achieve the required level of precision.
- 😀 The individual bearing parts are assembled carefully to form the final product.
- 😀 A grease injection process is used to fill the bearings, reducing friction and enhancing smooth performance.
- 😀 The bearings are sealed to protect the internal components and grease from contamination.
Q & A
What is YH System, and where is it located?
-YH System is a company based in Gimpo, Korea, that specializes in producing precise mechanical parts, specifically ball bearings.
What is the primary raw material used in the production of ball bearings?
-The primary raw material for manufacturing ball bearings is iron.
What is the first step in the ball bearing manufacturing process?
-The first step in the manufacturing process is the sawing of the raw material, which is the iron.
What happens during the heat forging process in ball bearing production?
-During the heat forging process, the material is heated to a high temperature, making it malleable for further shaping and forming.
Why is material inspection done after receiving the material?
-Material inspection is conducted to ensure that the raw material meets the required quality standards before it proceeds to the next stages of production.
What is the purpose of the fine cutting process?
-The fine cutting process is used to refine the shape and dimensions of the bearing parts to ensure precision and accuracy.
What role does the 3D measuring machine play in the inspection process?
-The 3D measuring machine is used for precise inspection of the parts to ensure they meet the correct specifications and tolerances.
What is hardening heat treatment, and why is it important in ball bearing production?
-Hardening heat treatment involves heating the material to a high temperature and then cooling it rapidly to increase its hardness and durability, making the bearing stronger and more reliable.
What is the plating process used for in ball bearing production?
-The plating process is used to apply a protective coating to the ball bearings, which helps prevent rust and enhances their durability.
What is the purpose of laser marking in the ball bearing manufacturing process?
-Laser marking is used for precise identification and branding of the ball bearings, ensuring traceability and quality control throughout the production process.
How are the final ball bearing parts assembled?
-The final ball bearing parts are carefully assembled, with the addition of a grease injector for lubrication and sealing to ensure the bearing functions smoothly and remains protected from contaminants.
Outlines
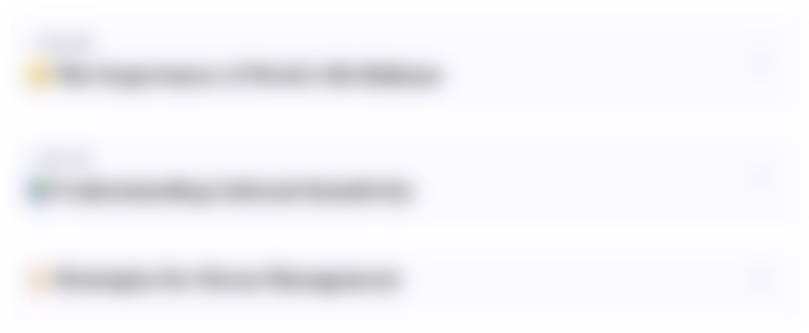
Этот раздел доступен только подписчикам платных тарифов. Пожалуйста, перейдите на платный тариф для доступа.
Перейти на платный тарифMindmap
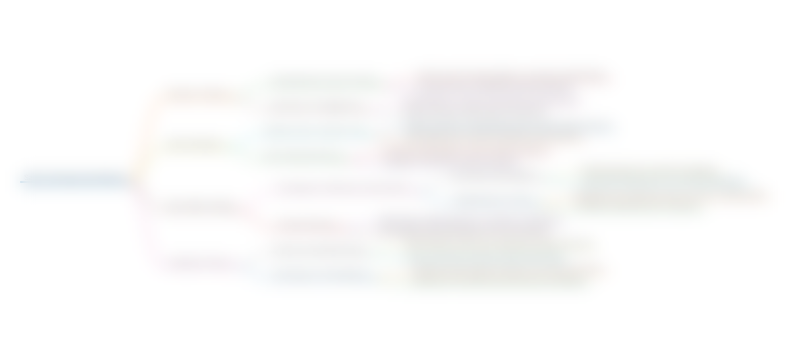
Этот раздел доступен только подписчикам платных тарифов. Пожалуйста, перейдите на платный тариф для доступа.
Перейти на платный тарифKeywords
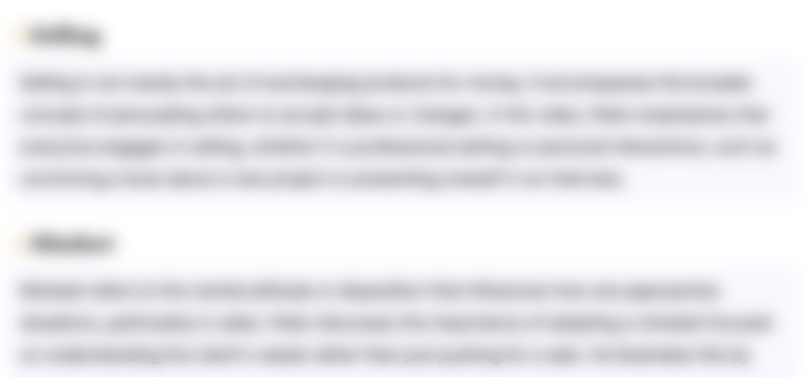
Этот раздел доступен только подписчикам платных тарифов. Пожалуйста, перейдите на платный тариф для доступа.
Перейти на платный тарифHighlights
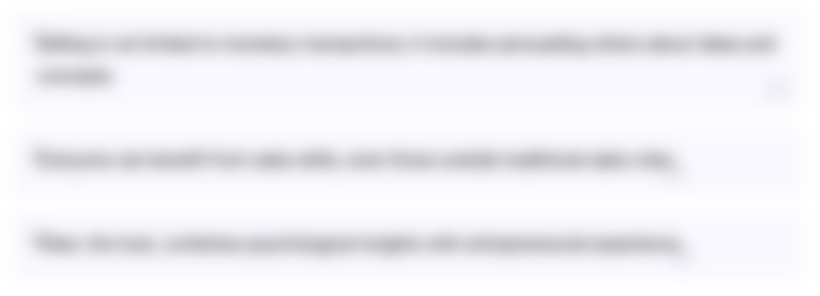
Этот раздел доступен только подписчикам платных тарифов. Пожалуйста, перейдите на платный тариф для доступа.
Перейти на платный тарифTranscripts
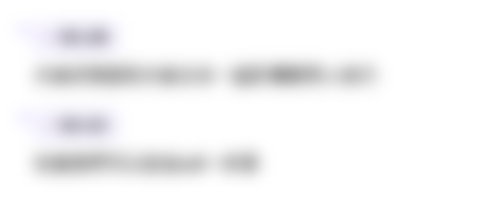
Этот раздел доступен только подписчикам платных тарифов. Пожалуйста, перейдите на платный тариф для доступа.
Перейти на платный тарифПосмотреть больше похожих видео
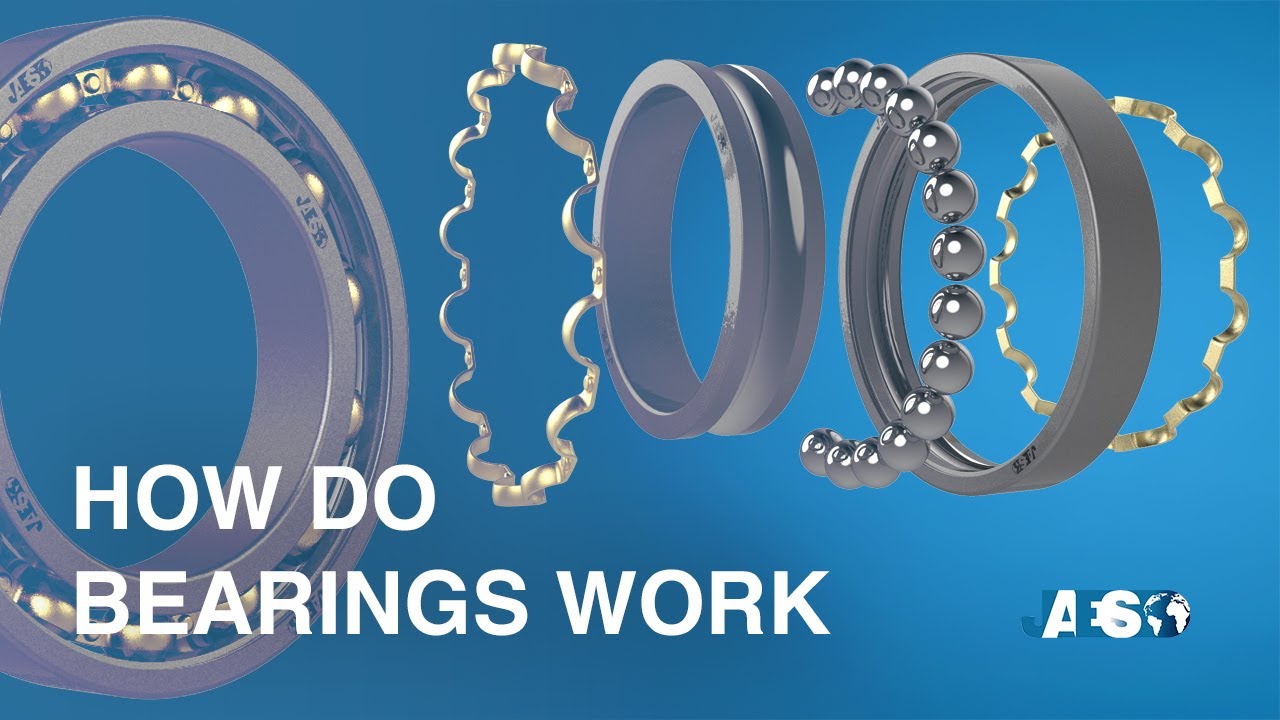
How do ball and roller bearings work? Types and durability calculation. DIN ISO 281
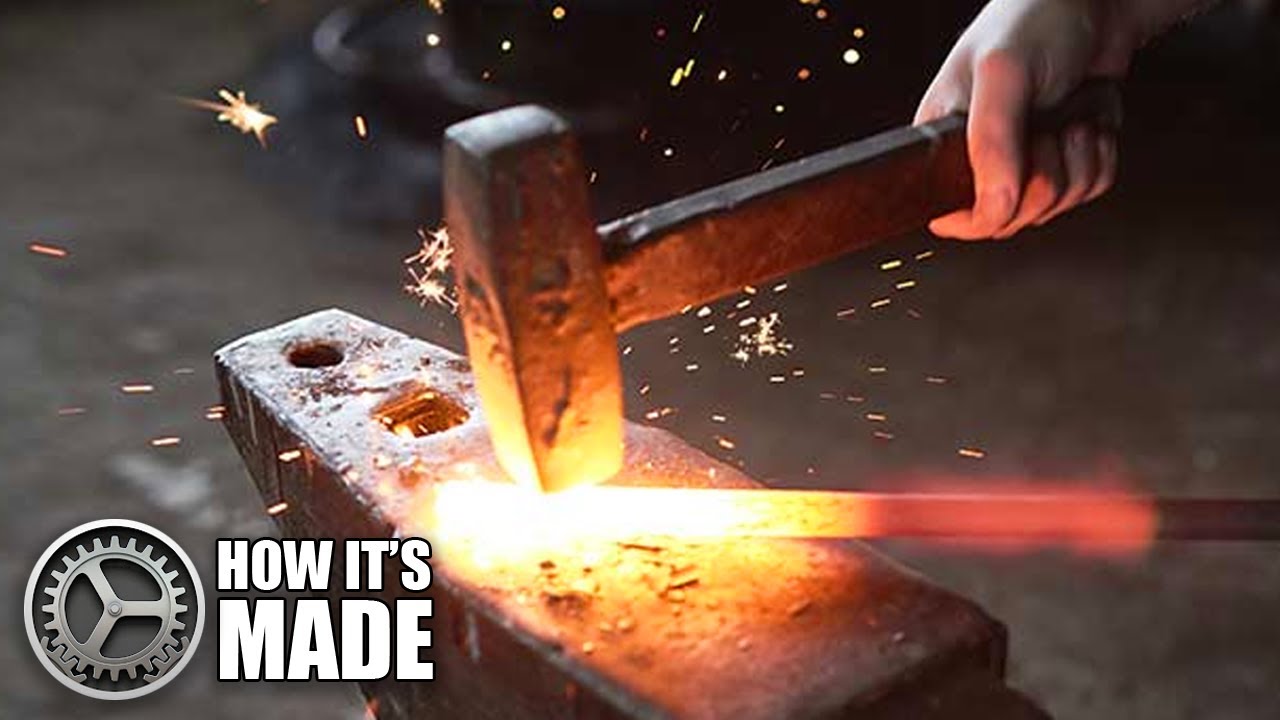
How Japanese Swords are Made

Telecurso 2000 - Processos de Fabricação - 65 Metalurgia do pó

What is VAT Photopolymerization (SLA, DLP, CDLP)? | Dassault Systèmes
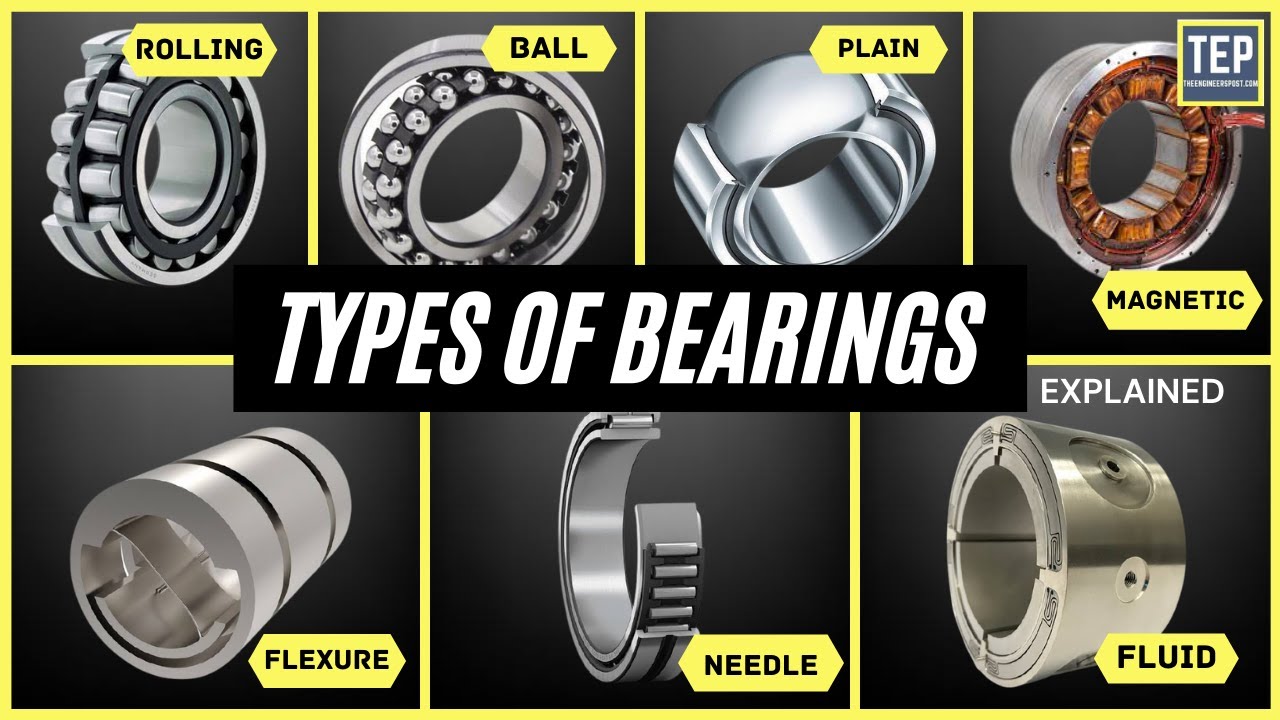
What is Bearing? Types of Bearings and How they Work?
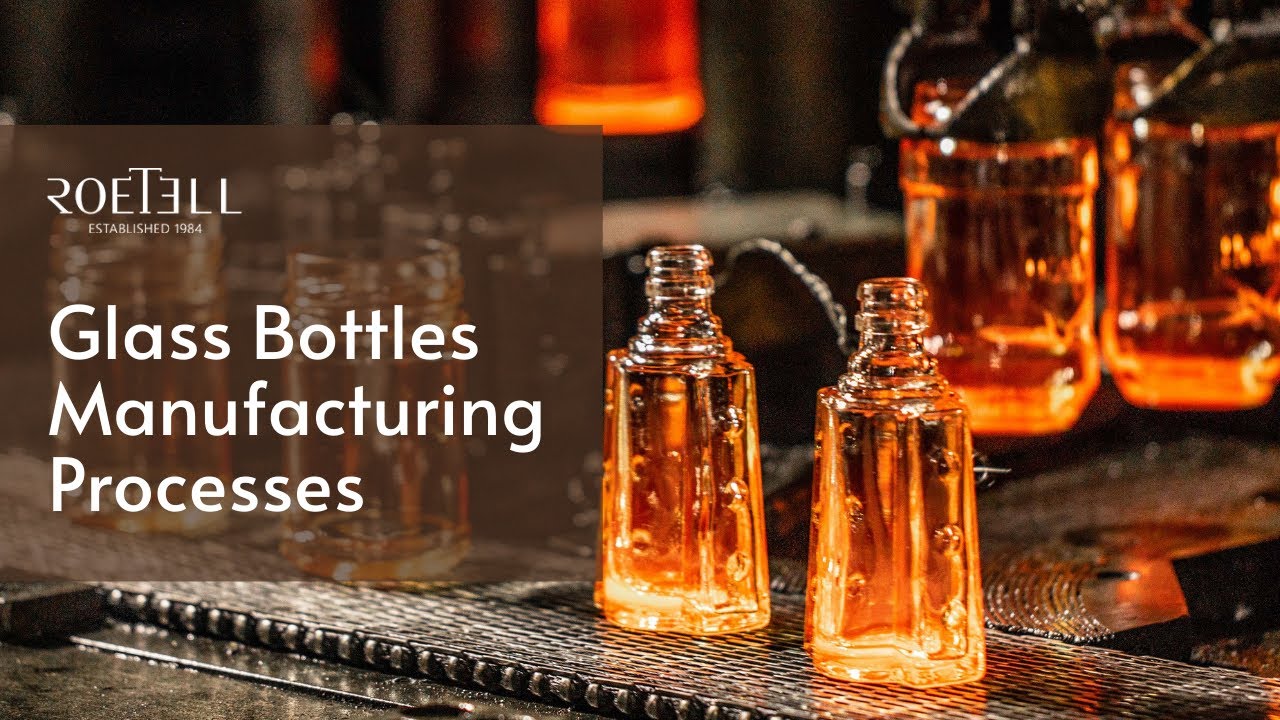
Glass Bottle Manufacturing Process (2021 Updated) - Roetell
5.0 / 5 (0 votes)