New breakthrough claims 90% reduction in Steelmaking emissions.
Summary
TLDRThe video explores challenges in reducing carbon emissions from steelmaking, which contributes 7-8% of global CO2 emissions. While green hydrogen offers a potential long-term solution, it remains costly and impractical at scale. Researchers at the University of Birmingham have proposed a more immediate fix by introducing a perovskite material (BCNF1) to reduce CO2 emissions by 94%. This technique, which requires minimal infrastructure changes, could replace coke in blast furnaces with carbon monoxide. However, practical challenges like gas permeability and the need for costly gas cleaning may hinder its commercial viability.
Takeaways
- 😀 Steelmaking is responsible for 7-8% of global human-induced CO2 emissions, mainly due to the use of coke in blast furnaces.
- 😀 Green hydrogen has the potential to reduce steelmaking emissions by over 90%, but it remains too expensive and difficult to scale for large industrial plants.
- 😀 The University of Birmingham's team proposed a new approach to reduce CO2 emissions in steelmaking by adding a perovskite material to the process.
- 😀 The perovskite material, BCNF1, works by releasing oxygen and turning carbon dioxide into carbon monoxide when heated, which is not a greenhouse gas.
- 😀 This process could reduce CO2 emissions from steelmaking by up to 94% when integrated into existing blast furnace and basic oxygen furnace setups.
- 😀 The proposed technology would allow steel producers to retrofit existing equipment, avoiding the need for costly new infrastructure.
- 😀 The perovskite technology has been shown to convert over 10% of CO2 into carbon monoxide during trials, which could be scaled up for industrial use.
- 😀 At an electricity price of 11 pence per kWh, the perovskite process could produce carbon monoxide for just 19 pence per kilogram, making it a cost-effective solution.
- 😀 The solution allows for immediate emissions reductions once implemented, compared to waiting for green hydrogen technologies to become commercially viable in the coming decades.
- 😀 Despite the promise of the new technology, practical challenges remain, such as ensuring the stability of the process and preventing catalyst poisoning from gas impurities.
- 😀 The green hydrogen solution remains a long-term goal, but the Birmingham team's research offers a more immediate, scalable solution for decarbonizing steel production.
Q & A
What is the current contribution of the steel industry to global carbon dioxide emissions?
-The steel industry is responsible for about 8% of global human-induced carbon dioxide emissions, up from approximately 7% previously.
What is the green hydrogen steelmaking process, and why has it not been widely adopted yet?
-The green hydrogen steelmaking process aims to replace coke in blast furnaces with green hydrogen, which can significantly reduce carbon emissions. However, it has not been widely adopted because the electrolysis required to produce green hydrogen is currently much more expensive than traditional methods like steam methane reforming (SMR), which releases carbon dioxide.
What role does perovskite play in the new decarbonization approach proposed by the University of Birmingham?
-Perovskite, specifically the BCNF1 material, is used to minimize carbon dioxide production and maximize carbon monoxide production in the steelmaking process. This substitution helps reduce emissions by converting carbon dioxide into carbon monoxide, which can replace a significant portion of coke in blast furnaces.
How does the BCNF1 perovskite material function in reducing emissions?
-BCNF1 perovskite releases oxygen when heated to 700°C, creating an oxygen vacancy. At 800°C, it reacts with carbon dioxide to produce carbon monoxide, which can replace up to 90% of coke in the blast furnace. This process reduces carbon dioxide emissions by up to 94%.
What are the practical advantages of using the perovskite-based approach in steelmaking?
-The perovskite-based approach offers several advantages: it allows the continued use of existing blast furnaces and basic oxygen furnaces, preserving expensive infrastructure and jobs. Additionally, it provides a rapid reduction in emissions without waiting for decades for full-scale green hydrogen adoption.
What are the potential challenges or limitations of the BCNF1 perovskite method?
-Challenges include the fact that coke plays a crucial role in furnace stability, and replacing it with carbon monoxide could destabilize the process. Additionally, perovskite catalysts are sensitive to gas qualities and could be poisoned by impurities, necessitating costly gas cleaning procedures.
How much carbon dioxide can be reduced using the proposed BCNF1-based method compared to traditional steelmaking processes?
-The BCNF1-based method can reduce carbon dioxide emissions by 94% compared to conventional blast furnace and basic oxygen furnace steelmaking methods.
What is the significance of using carbon monoxide in place of coke in the blast furnace?
-Carbon monoxide can replace coke in the blast furnace because it serves as a reducing agent that helps to convert iron ore into molten iron. By using carbon monoxide, emissions are reduced significantly, as coke is a major source of carbon dioxide in the process.
How does the electricity price affect the cost of producing carbon monoxide using the BCNF1 perovskite method?
-The cost of producing carbon monoxide using the BCNF1 method is directly affected by electricity prices. At an electricity cost of 11 pence per kilowatt-hour, carbon monoxide production costs around 19 pence per kilogram. If electricity prices are reduced to 5 pence per kilowatt-hour, the cost drops to just 11 pence per kilogram.
What are the potential real-world obstacles to implementing the BCNF1 perovskite-based approach in steelmaking?
-Real-world obstacles include the technical difficulties of replacing coke with carbon monoxide without destabilizing the furnace process, the need for expensive gas cleaning to maintain the effectiveness of the perovskite catalyst, and the sensitivity of perovskites to impurities in industrial gases.
Outlines
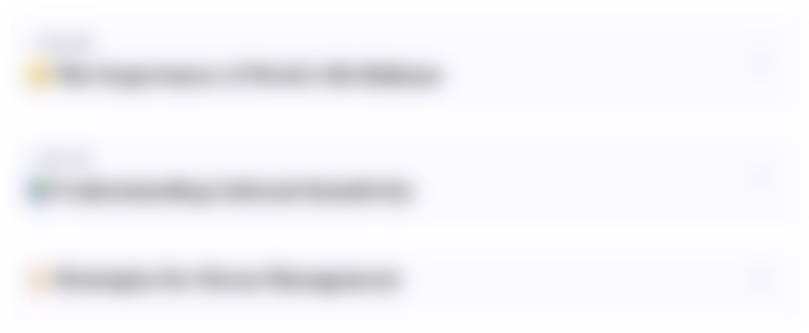
Этот раздел доступен только подписчикам платных тарифов. Пожалуйста, перейдите на платный тариф для доступа.
Перейти на платный тарифMindmap
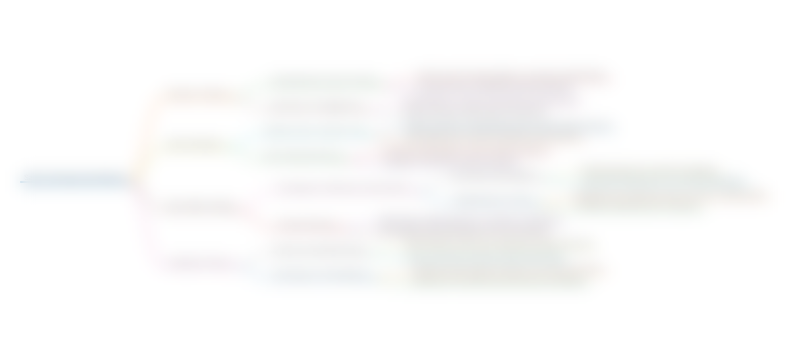
Этот раздел доступен только подписчикам платных тарифов. Пожалуйста, перейдите на платный тариф для доступа.
Перейти на платный тарифKeywords
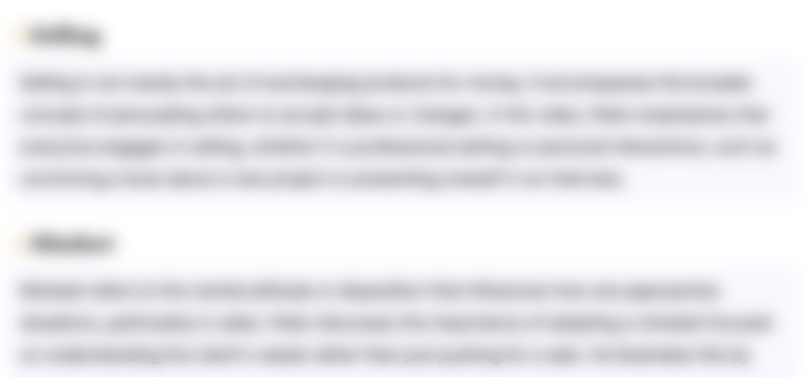
Этот раздел доступен только подписчикам платных тарифов. Пожалуйста, перейдите на платный тариф для доступа.
Перейти на платный тарифHighlights
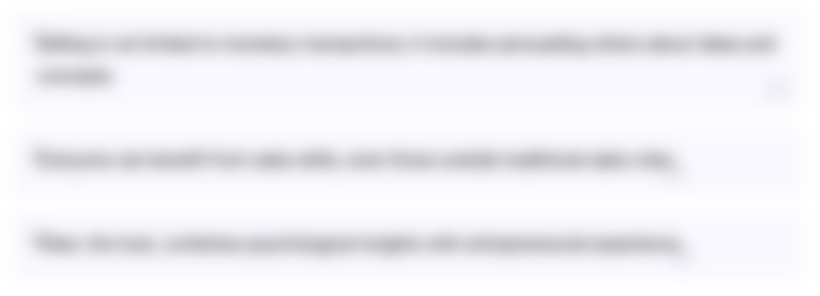
Этот раздел доступен только подписчикам платных тарифов. Пожалуйста, перейдите на платный тариф для доступа.
Перейти на платный тарифTranscripts
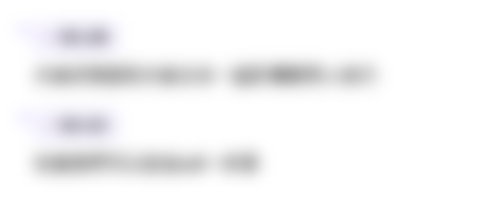
Этот раздел доступен только подписчикам платных тарифов. Пожалуйста, перейдите на платный тариф для доступа.
Перейти на платный тарифПосмотреть больше похожих видео
5.0 / 5 (0 votes)