Role of QA and QC quality department functions
Summary
TLDRThis video explores the roles of Quality Assurance (QA) and Quality Control (QC) within operations, explaining how both functions ensure product quality through monitoring processes and validating output. It highlights the similarities and distinctions between QA and QC and their vital contribution to continuous improvement (CI) practices. By emphasizing collaboration between the quality and continuous improvement teams, the video advocates for integrating quality professionals into CI projects to optimize processes. Ultimately, the video underscores the importance of aligning quality management with continuous improvement efforts for enhanced operational efficiency and product consistency.
Takeaways
- 😀 Quality is everyone's responsibility, not just the Quality Department's role in an organization.
- 😀 Quality Assurance (QA) focuses on setting up systems and standards to maintain quality, while Quality Control (QC) checks the actual product to ensure it meets those standards.
- 😀 Both QA and QC are essential parts of the broader Quality Management System (QMS) that ensures product quality from start to finish.
- 😀 Continuous Improvement (CI) and Quality Management share the same goals: optimizing processes and ensuring high-quality outcomes.
- 😀 QA and CI teams are natural allies, but their roles often overlap, especially when it comes to ensuring quality in process improvement initiatives.
- 😀 Quality professionals should be involved in problem-solving and process improvement activities to prevent compromising quality during CI efforts.
- 😀 Quality Assurance professionals act as the conscience of the organization, reminding others to maintain quality standards even during improvements and changes.
- 😀 The quality department is often overloaded, which can limit its ability to actively participate in Continuous Improvement projects, requiring balance in workload distribution.
- 😀 Integrating quality control professionals into the CI team is important since they are the ones most familiar with the product and processes on the ground.
- 😀 Quality Assurance and Continuous Improvement are intertwined; improving one often means improving the other, creating synergies across departments.
- 😀 To expand their expertise, quality professionals can take temporary roles in CI teams to gain valuable experience and foster better alignment between CI and quality management.
Q & A
What is the role of the quality department in an industrial operation?
-The quality department ensures that both inputs (materials) and outputs (finished products) meet defined specifications, ensuring the delivery of a qualitative product to customers. This includes quality checks on raw materials, suppliers, processes, and the final product.
What is the difference between quality assurance (QA) and quality control (QC)?
-Quality assurance (QA) is focused on creating and maintaining the quality management system, which ensures processes are in place to produce quality products. Quality control (QC), on the other hand, is about inspecting and testing the product and processes to ensure they meet the established quality standards.
How does quality assurance contribute to continuous improvement?
-Quality assurance is essential to continuous improvement because it sets up and guides the quality management system, ensuring that changes made during improvement initiatives align with quality standards. QA teams help identify areas for improvement while maintaining compliance with quality specifications.
How does quality control support the quality management system?
-Quality control supports the quality management system by ensuring that processes are being followed and products meet predefined specifications. QC is involved in inspecting, testing, and documenting results, ensuring that any deviations are identified and corrected.
Why is it important for quality professionals to be involved in continuous improvement efforts?
-It is important for quality professionals to be involved in continuous improvement because they have a deep understanding of the systems, standards, and control points necessary to maintain product quality. Their insights ensure that process improvements do not compromise quality and help identify potential risks during changes.
What challenges do quality departments often face in the context of continuous improvement?
-Quality departments often face overload due to external audits, regulatory compliance tasks, and managing the quality management system. This workload can slow down their involvement in continuous improvement initiatives, making it difficult to fully contribute to process optimizations.
What role does quality assurance play in process changes within an operation?
-Quality assurance plays a crucial role in guiding process changes to ensure that they align with quality standards. QA teams act as the conscience of the organization, ensuring that any changes made do not compromise product quality, such as reducing important quality steps like frying time.
How can quality control teams contribute to problem-solving and process improvement?
-Quality control teams are often closest to the product and its processes. They possess detailed knowledge of the system and are crucial in problem-solving and process improvements. Their role in inspecting and testing products makes them highly effective in identifying root causes and suggesting practical solutions.
What is the connection between quality management systems and lean or Six Sigma practices?
-Quality management systems (QMS) and lean or Six Sigma practices share similar goals of improving process efficiency while maintaining quality. While QMS focuses on compliance and standardization, lean and Six Sigma aim to eliminate waste and reduce defects, making them complementary in driving continuous improvement.
Why should organizations consider temporary roles for quality professionals within continuous improvement teams?
-Organizations should consider placing quality professionals in temporary continuous improvement roles because it broadens their experience, allowing them to integrate quality standards with lean or Six Sigma methods. This cross-functional experience can enhance the overall quality management system by making it more adaptable and effective in addressing operational challenges.
Outlines
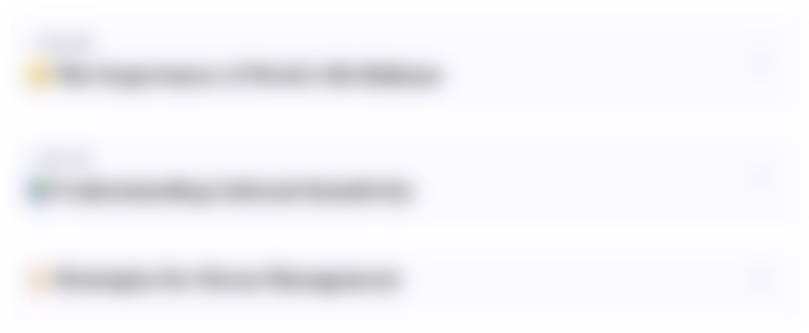
Этот раздел доступен только подписчикам платных тарифов. Пожалуйста, перейдите на платный тариф для доступа.
Перейти на платный тарифMindmap
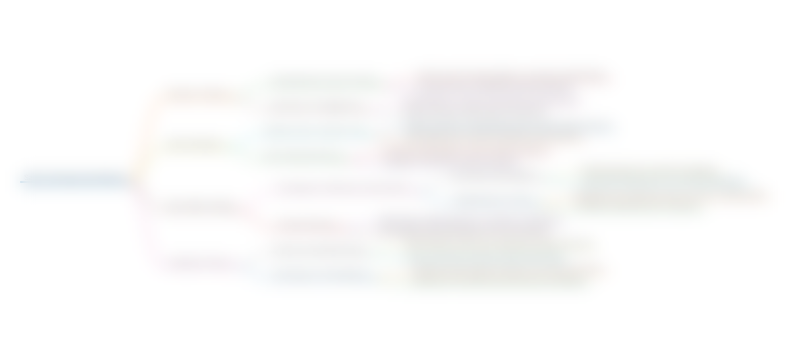
Этот раздел доступен только подписчикам платных тарифов. Пожалуйста, перейдите на платный тариф для доступа.
Перейти на платный тарифKeywords
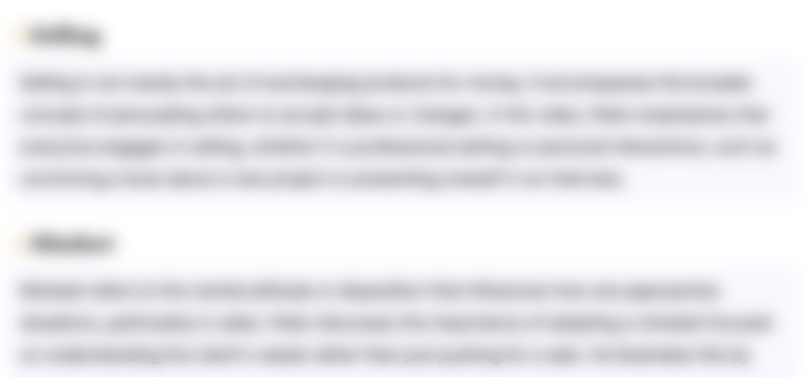
Этот раздел доступен только подписчикам платных тарифов. Пожалуйста, перейдите на платный тариф для доступа.
Перейти на платный тарифHighlights
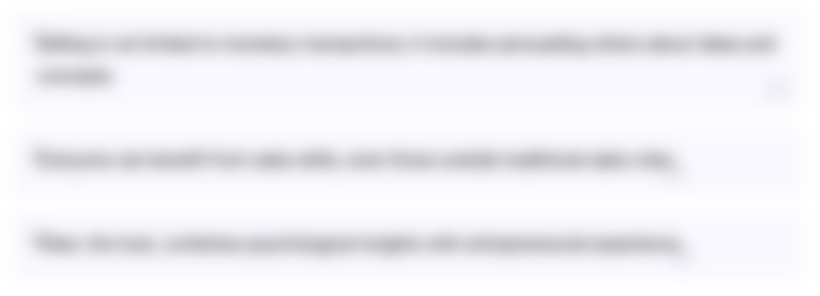
Этот раздел доступен только подписчикам платных тарифов. Пожалуйста, перейдите на платный тариф для доступа.
Перейти на платный тарифTranscripts
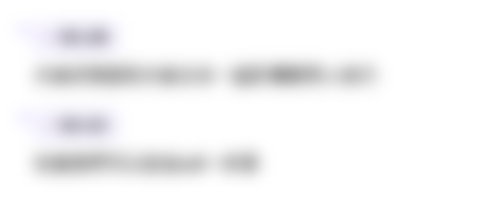
Этот раздел доступен только подписчикам платных тарифов. Пожалуйста, перейдите на платный тариф для доступа.
Перейти на платный тарифПосмотреть больше похожих видео
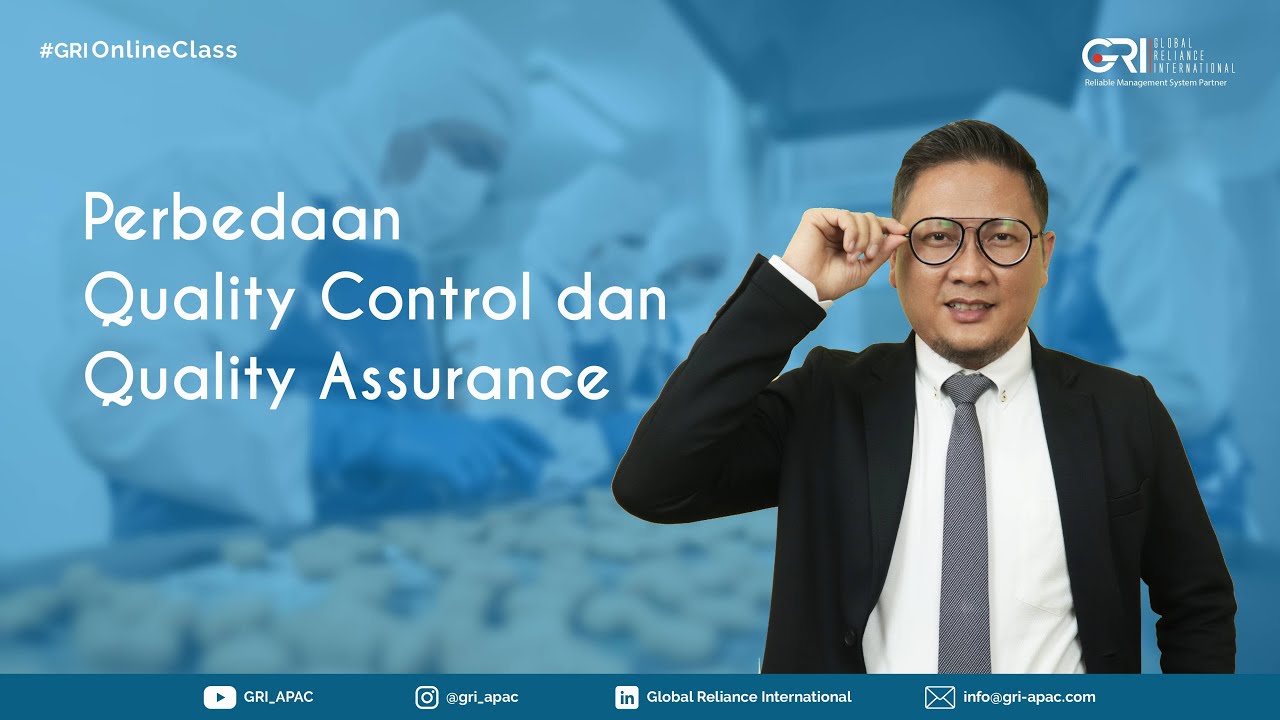
Perbedaan Quality Control dan Quality Assurance di Industri Pangan

QA vs QC: Are You Making This Common Mistake?

QA vs. QC: Understanding the Key Difference

Difference between quality assurance and quality control - Quality Assurance vs Quality Control
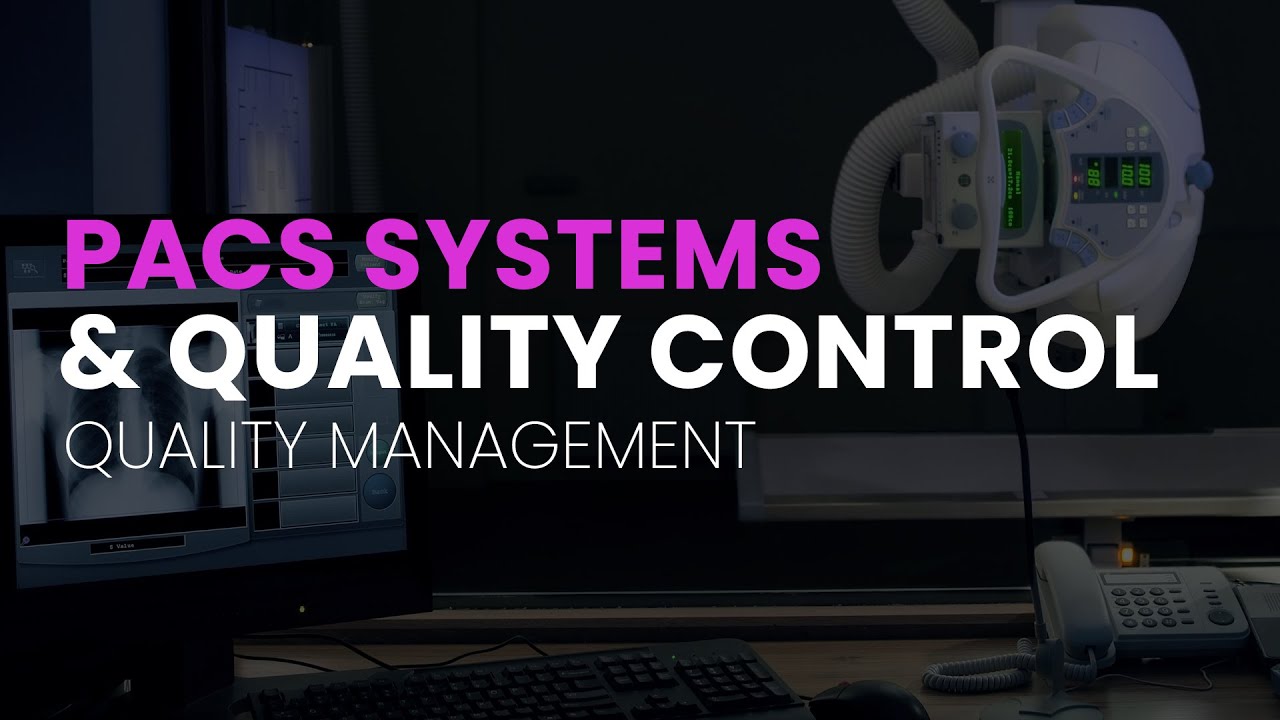
PACS Systems and Quality Control Part 3 - Quality Management
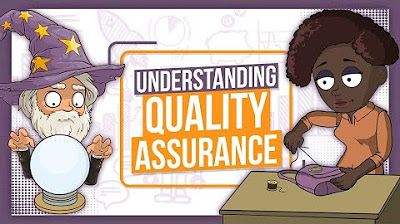
Understanding Quality Assurance - GCSE Business Studies Revision - OCR, Edexcel, AQA - BizzWizard
5.0 / 5 (0 votes)