Layout dan Proses Produksi Eps 4
Summary
TLDRThe transcript discusses the importance of standardization in production processes, highlighting the need for skilled labor to enhance efficiency while keeping costs low. It notes that a product layout is crucial for facilitating smooth production flow and long-term operational efficiency. The text emphasizes the potential downsides, including low flexibility and high maintenance costs if equipment fails. It advocates for preventive maintenance and quick repair systems to address production disruptions. In automotive manufacturing, the layout, often referred to as SMD Line, is optimized for assembly tasks, aiming for maximum efficiency and swift workflow, despite the high initial investment in equipment and technology.
Takeaways
- 🏭 Standard products require a workforce with low skill levels, which increases production efficiency.
- 📉 Production processes have higher efficiency and lower costs per unit but lack flexibility.
- ⚙️ High repair costs arise if equipment malfunctions due to the standardization of products.
- 📏 The product layout is crucial for efficient production flow and requires significant investment.
- 🔄 Errors in layout design are challenging to rectify and can affect operational costs and efficiency.
- 🚗 In automotive production, the product layout, known as SMD Line, is arranged based on assembly task sequences.
- 🛠️ Tasks are standardized according to worker and equipment specialization, leading to minimal item production.
- 🔗 Technology connects workstations, optimizing workforce and equipment usage while compensating for high equipment costs.
- ⚡ Rapid job transitions may overload the system, making it vulnerable to disruptions.
- 🔧 Preventive maintenance systems are essential for addressing equipment wear and ensuring production continuity.
Q & A
What is the primary advantage of using a standardized product in production?
-The primary advantage is achieving a higher efficiency level and lower cost per unit in the production process.
What are the drawbacks of a standardized production model?
-The drawbacks include low flexibility and high maintenance costs if the equipment stops functioning.
How does the concept of product layout relate to production efficiency?
-Product layout refers to the arrangement of production facilities that considers work movement, which is essential for maintaining a smooth and fast production flow, especially in high-volume manufacturing.
What is the significance of layout selection in production?
-Layout selection is critical because it requires significant investment and effort, and any errors can lead to long-term impacts on costs and operational efficiency.
What is an SMD Line in the context of automotive production?
-An SMD Line is a specific type of product layout in automotive manufacturing, organized based on the sequence of assembly tasks, tailored to the specialization of labor and equipment.
Why is technology important in product layout?
-Technology is crucial as it connects workstations and maximizes the use of labor and equipment, helping to compensate for high equipment costs and facilitating rapid job transfers between workstations.
What potential issues can arise from high system loads in production?
-High system loads can lead to disruptions or halts in production processes, necessitating a quick response to mitigate these problems.
What is preventive maintenance and why is it necessary?
-Preventive maintenance involves regular checks and replacements of damaged or outdated equipment, which is necessary to prevent production stoppages and ensure smooth operations.
How can quick repair systems help in production?
-Quick repair systems are designed to address potential issues rapidly, thereby minimizing downtime and maintaining production flow.
What challenges does high standardization pose in production?
-High standardization can limit flexibility and responsiveness to changes in production demands, making it difficult to adapt to new processes or product variations.
Outlines
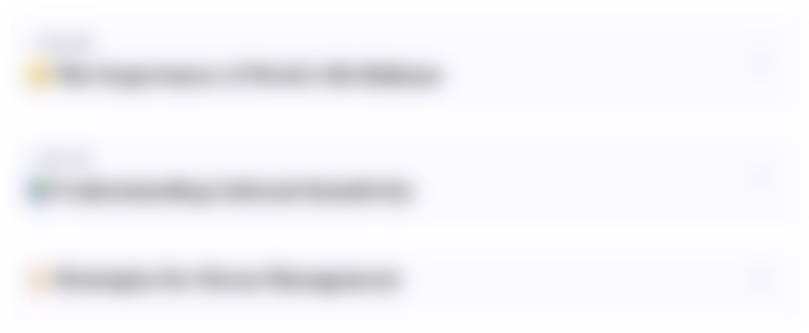
Этот раздел доступен только подписчикам платных тарифов. Пожалуйста, перейдите на платный тариф для доступа.
Перейти на платный тарифMindmap
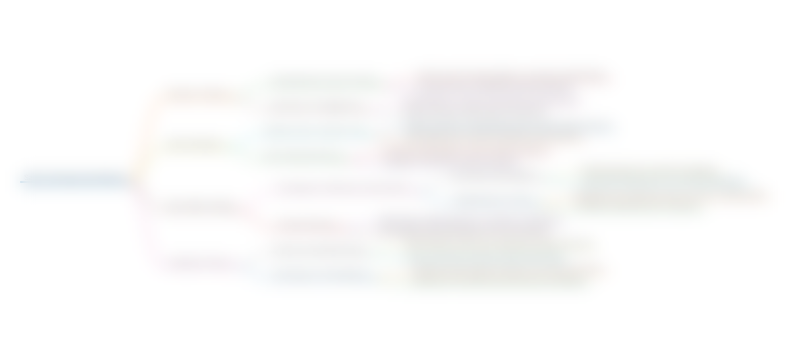
Этот раздел доступен только подписчикам платных тарифов. Пожалуйста, перейдите на платный тариф для доступа.
Перейти на платный тарифKeywords
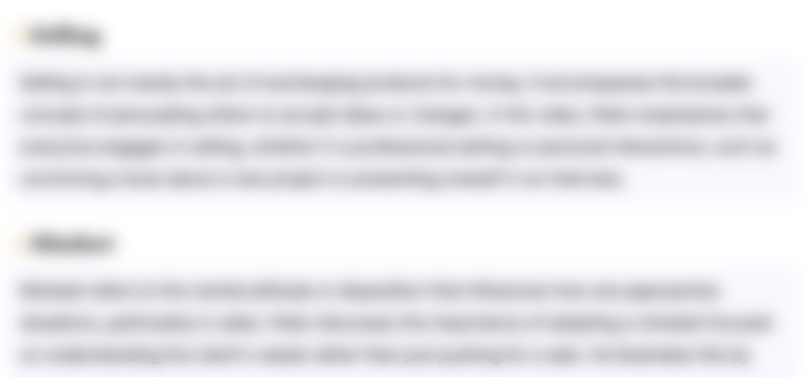
Этот раздел доступен только подписчикам платных тарифов. Пожалуйста, перейдите на платный тариф для доступа.
Перейти на платный тарифHighlights
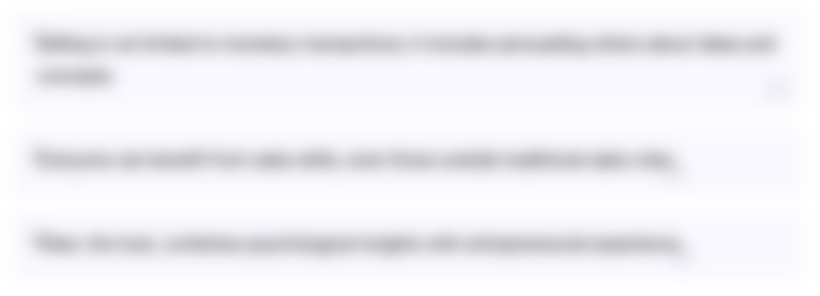
Этот раздел доступен только подписчикам платных тарифов. Пожалуйста, перейдите на платный тариф для доступа.
Перейти на платный тарифTranscripts
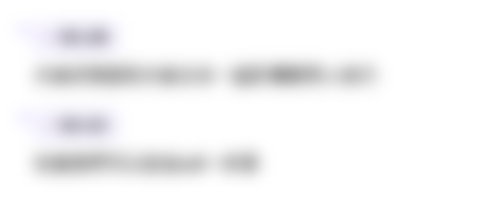
Этот раздел доступен только подписчикам платных тарифов. Пожалуйста, перейдите на платный тариф для доступа.
Перейти на платный тариф5.0 / 5 (0 votes)