TAHAPAN PEMBUATAN BATIK TULIS SEBAGAI WARISAN BUDAYA INDONESIA
Summary
TLDRThe script outlines the intricate process of creating traditional Indonesian batik, a cultural art form. It involves 12 stages: Nyungging (designing), Njaplak (transferring design to fabric), Nglowong (applying wax with a 'canting'), Ngiseni (filling in motifs), Nyolet (coloring), Mopok (covering with wax), Ngelir (thorough coloring), Nglorod (first wax removal), Ngrentesi (detailing with wax), Nyumri (re-waxing), Nyoja (dipping in traditional colors), and final Nglorod (final wax removal). This craft is typically a cottage industry, reflecting the community's significant role in preserving this heritage.
Takeaways
- 🖌️ Written batik is created using a canting, a tool resembling a pen, for drawing and writing on the fabric.
- 🕯️ Canting is dipped into wax, which serves as ink for creating designs on the fabric.
- 🏠 Written batik production often involves 4-5 artisans and is usually done in cottage industries rather than factories.
- 🎨 The first stage, Nyungging, involves drawing the batik motif, which requires specialized skills.
- 📄 The second stage, Njaplak or Jiplak, is transferring the motif design from paper onto the fabric.
- 🖋️ Nglowong, the third stage, involves applying wax onto the fabric using canting to reveal the batik motif.
- 🌀 In the fourth stage, Ngiseni, the artisans fill in the motif details on the fabric using canting.
- 🌸 The fifth stage, Nyolet, focuses on coloring visible motif areas, such as flowers.
- 🧵 Mopok, the sixth stage, involves covering certain parts of the motif with wax to prevent coloring in those areas.
- 🌈 The seventh stage, Ngelir, is the process of dyeing the fabric in one color.
Q & A
What is written batik and how is it made?
-Written batik is a form of batik where canting, a tool resembling a pen, is used to draw patterns on fabric. The tip of the canting is dipped into wax, which is then applied to the fabric to create intricate designs.
What materials are used to make the canting?
-The canting typically has a wooden tip and a handle made of brass or zinc. It is used to apply hot wax to the fabric in the batik-making process.
Is written batik typically produced in factories?
-No, written batik is usually produced in cottage industries rather than large factories, and it often involves multiple artisans working together.
What is the Nyungging stage in the batik-making process?
-Nyungging is the first stage of making written batik, where an artist skilled in drawing batik motifs creates the initial design.
What happens in the Njaplak (Jiplak) stage?
-In the Njaplak stage, the batik design is transferred from paper to the fabric that will be used to make the batik.
What role does the canting play in the Nglowong stage?
-In the Nglowong stage, the canting is used to apply wax to the fabric, which allows the batik motif to start becoming visible on the cloth.
What is the purpose of the Ngiseni stage?
-Ngiseni is the stage where the artist fills in the motifs on the fabric according to the original design, using canting to apply wax in detailed areas.
How is color added to the batik during the Nyolet stage?
-In the Nyolet stage, the artist adds color to certain parts of the design, such as flowers, using dyes to highlight specific motifs.
What is the Nglorod stage in the batik-making process?
-Nglorod is the stage where the wax applied earlier is removed by soaking the fabric in boiling water, revealing the batik pattern underneath.
What happens in the final stages, Nyoja and Nglorod?
-In Nyoja, the fabric is dipped into a sogan or brown dye, a traditional color for batik from Jogja or Solo. In the final Nglorod stage, any remaining wax is removed using boiling water, completing the batik design.
Outlines
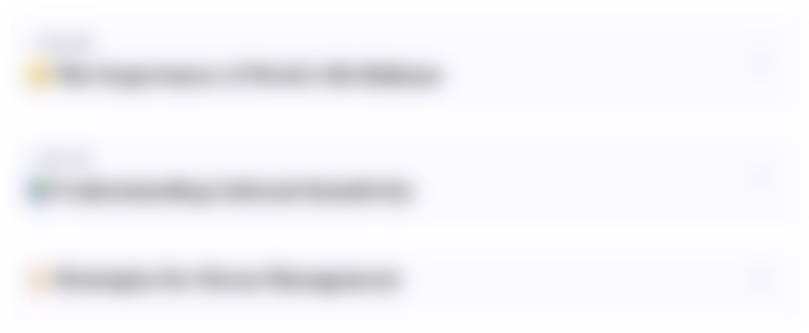
Этот раздел доступен только подписчикам платных тарифов. Пожалуйста, перейдите на платный тариф для доступа.
Перейти на платный тарифMindmap
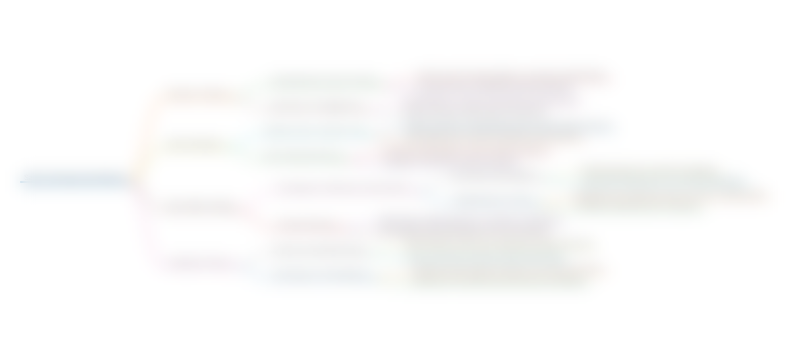
Этот раздел доступен только подписчикам платных тарифов. Пожалуйста, перейдите на платный тариф для доступа.
Перейти на платный тарифKeywords
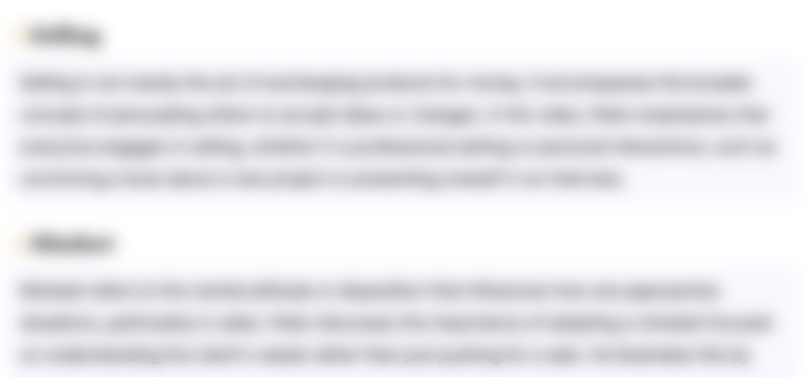
Этот раздел доступен только подписчикам платных тарифов. Пожалуйста, перейдите на платный тариф для доступа.
Перейти на платный тарифHighlights
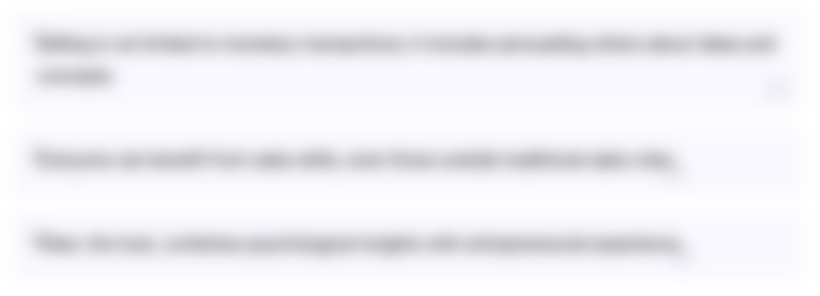
Этот раздел доступен только подписчикам платных тарифов. Пожалуйста, перейдите на платный тариф для доступа.
Перейти на платный тарифTranscripts
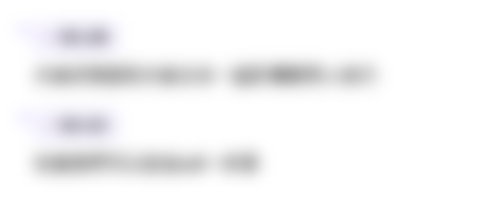
Этот раздел доступен только подписчикам платных тарифов. Пожалуйста, перейдите на платный тариф для доступа.
Перейти на платный тарифПосмотреть больше похожих видео

TUTORIAL PEMBUATAN BATIK TULIS LASEM SKB REMBANG 2022

Batik Story

Batik, Simbol Budaya dan Peradaban Bangsa#InsideIndonesia

Mengenal Batik Nusantara

PENGERTIAN BATIK - JENIS-JENIS BATIK DAN CIRI-CIRI BATIK - SELAMAT HARI BATIK
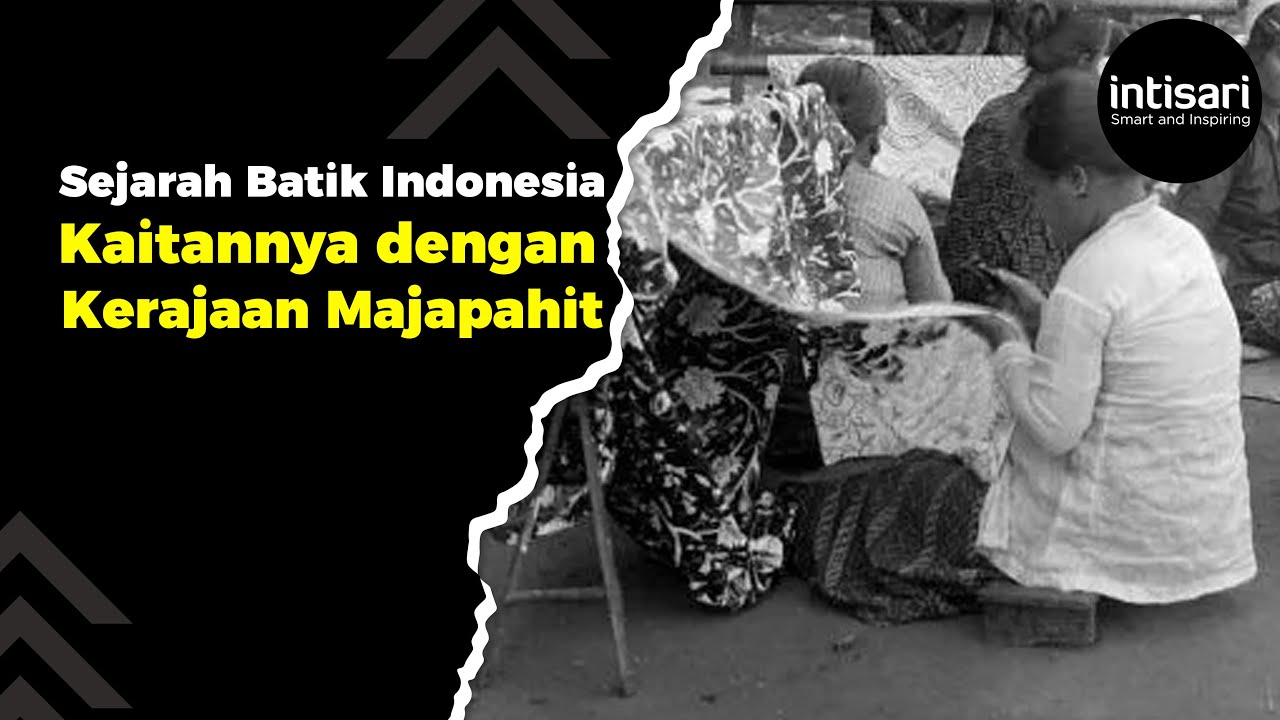
Batik Indonesia: Sejarah, Perkembangan, dan Kaitannya dengan Kerajaan Majapahit
5.0 / 5 (0 votes)