#234 ANODIZZARE ALLUMINIO COLORATO FAI DA TE - How to ANODIZE and COLOR ALUMINIUM DIY [SUB ENG]
Summary
TLDRIn this video, the process of anodizing aluminum is explained step by step, focusing on creating a protective layer of aluminum oxide. This layer increases hardness, provides resistance to wear and atmospheric agents, and allows for coloring the metal. The presenter demonstrates the entire procedure, from cleaning and preparing the aluminum to calculating the correct current for anodizing and applying dyes for vibrant colors. Key safety precautions, such as working with chemicals like sulfuric acid, are highlighted. Viewers are encouraged to try anodizing at home using easily accessible tools.
Takeaways
- 🔧 Anodizing is a chemical/electrochemical treatment for aluminum, creating a hard aluminum oxide layer (alumina) that protects the surface.
- 🔬 The anodized layer has a hardness of 9 on the Mohs scale, similar to corundum, offering excellent protection against wear and atmospheric agents.
- 🎨 Anodizing allows for coloring aluminum in various colors like red, blue, green, and purple by introducing dyes into the porous oxide layer.
- 🧪 Anodizing involves creating deep pores in the surface oxide layer of aluminum, which can be used to hold dye, resulting in a colorful, durable finish.
- ⚙️ Sodium hydroxide (10g per 100ml) is used to pickle and clean the aluminum surface before anodizing, ensuring better adherence of the anodized layer.
- 🔌 The current applied during anodizing affects pore size, with tighter pores resulting in more resistance and looser pores allowing for better coloring.
- ⚗️ A sulfuric acid solution (170g per liter) is used for anodizing, and it's critical to maintain the solution below 21°C to prevent degradation of the oxide layer.
- 📏 The formula for calculating current density during anodizing is 0.03 x time (in minutes) x current density (mA per cm²), controlling the thickness of the oxide layer.
- 🎨 Jet printer ink is recommended for more consistent and precise color results, compared to food or clothing dyes, allowing for custom color mixes.
- 💧 After dyeing the anodized piece, it is sealed in boiling water or steam to close the pores and lock in the dye, making the color permanent.
Q & A
What is anodizing, and why is it done?
-Anodizing is a chemical or electrochemical treatment primarily used on aluminum at an industrial level. It creates a protective layer of aluminum oxide (alumina), which is very hard and helps strengthen the external surface, protecting it from atmospheric agents and wear.
How does anodizing enhance the surface of aluminum?
-Anodizing creates a thick layer of aluminum oxide that increases surface hardness (9 on the Mohs scale, similar to corundum), which makes the material more resistant to wear and environmental damage. Additionally, anodizing allows for coloring the material by introducing dyes into the pores of the oxide layer.
What is the process of preparing aluminum for anodizing?
-The aluminum part must first be mechanically cleaned and degreased to avoid stains. Then, it is treated with a sodium hydroxide solution to pickle the surface, removing any pre-existing anodizing or impurities.
How does the oxide layer formed by anodizing enable the coloring process?
-Anodizing creates pores on the aluminum surface that deepen into the metal, forming a honeycomb structure. These pores allow the introduction of dye, and their size can be controlled by adjusting the current during the anodizing process, affecting both surface strength and coloring quality.
What are the different thicknesses of anodizing, and what applications are they suitable for?
-Anodizing thickness can range from 5 microns for aesthetic purposes to 25 microns for architectural structures. Thicker anodizing layers offer greater protection, with 10 microns for indoor applications, 15 microns for outdoor use, and up to 25 microns for highly corrosive environments like those near the sea.
How is the current for anodizing calculated?
-The current density is calculated using the formula: (oxide thickness in microns) / (0.03 * treatment time in minutes). For example, to achieve 10 microns of oxide in 50 minutes, the current density would be 6.6 milliamps per square centimeter, which is then multiplied by the part’s surface area.
Why is temperature control important during anodizing?
-Temperature control is crucial because excessive heat can degrade the oxide layer being formed. The electrolyte solution should remain below 21°C, and for larger parts, a cooling system may be needed to maintain this temperature.
What are the advantages of using inkjet printer ink for coloring anodized parts?
-Inkjet printer ink offers more precise and consistent results than fabric or food dyes, which are harder to dose. The ink percentages can be accurately measured, allowing for better control over color intensity and consistency across multiple parts.
How does sealing the anodized part in boiling water affect the final result?
-Sealing the anodized part in boiling water closes the pores in the oxide layer, trapping the dye inside. This process ensures that the color is locked in and won’t fade or wash out over time.
What safety precautions are necessary when handling sulfuric acid during anodizing?
-It is important to always add acid to water, not the other way around, to avoid heat buildup and dangerous splashes. Gloves and protective eyewear should be worn, and sturdy containers made of glass or thick plastic should be used to handle the sulfuric acid solution.
Outlines
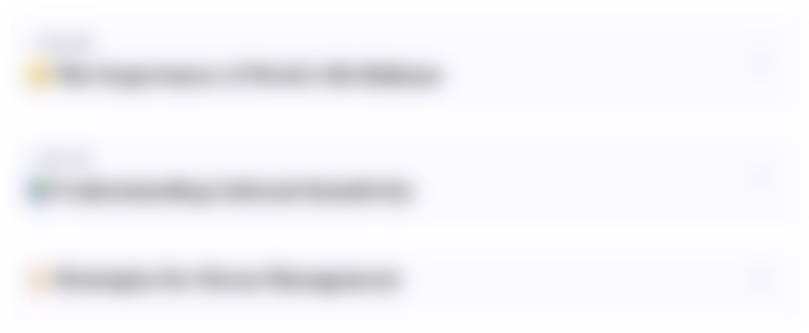
Этот раздел доступен только подписчикам платных тарифов. Пожалуйста, перейдите на платный тариф для доступа.
Перейти на платный тарифMindmap
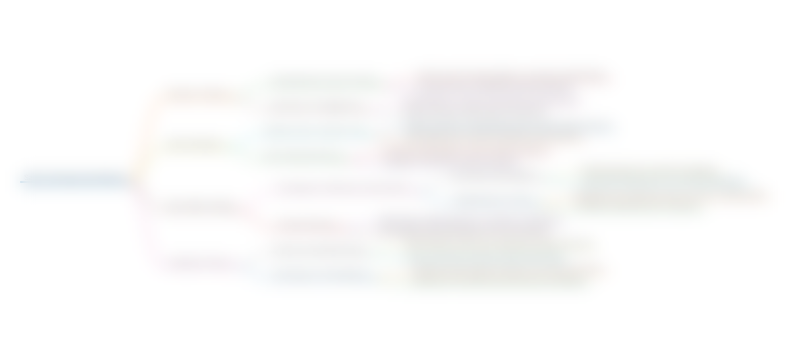
Этот раздел доступен только подписчикам платных тарифов. Пожалуйста, перейдите на платный тариф для доступа.
Перейти на платный тарифKeywords
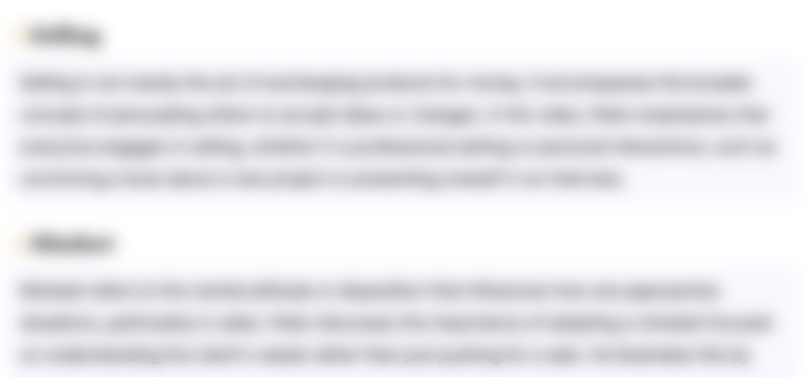
Этот раздел доступен только подписчикам платных тарифов. Пожалуйста, перейдите на платный тариф для доступа.
Перейти на платный тарифHighlights
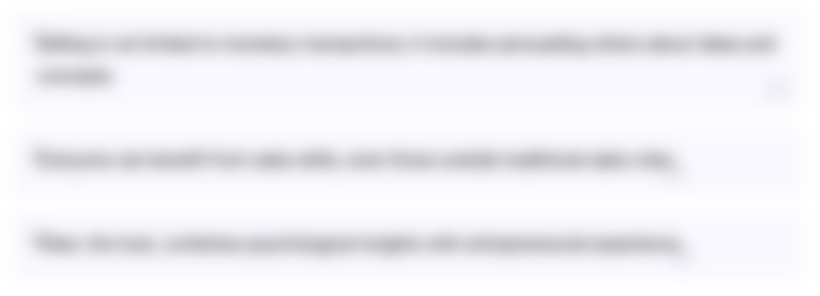
Этот раздел доступен только подписчикам платных тарифов. Пожалуйста, перейдите на платный тариф для доступа.
Перейти на платный тарифTranscripts
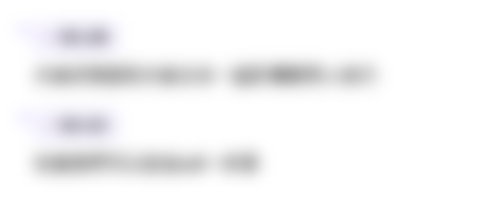
Этот раздел доступен только подписчикам платных тарифов. Пожалуйста, перейдите на платный тариф для доступа.
Перейти на платный тарифПосмотреть больше похожих видео
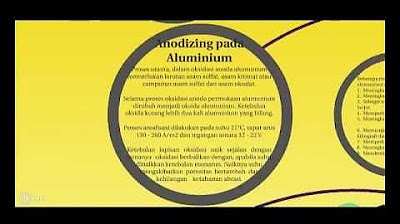
ANODIZING PROCESS - Proses Pelapisan Teknik Anodising

Anodisasi
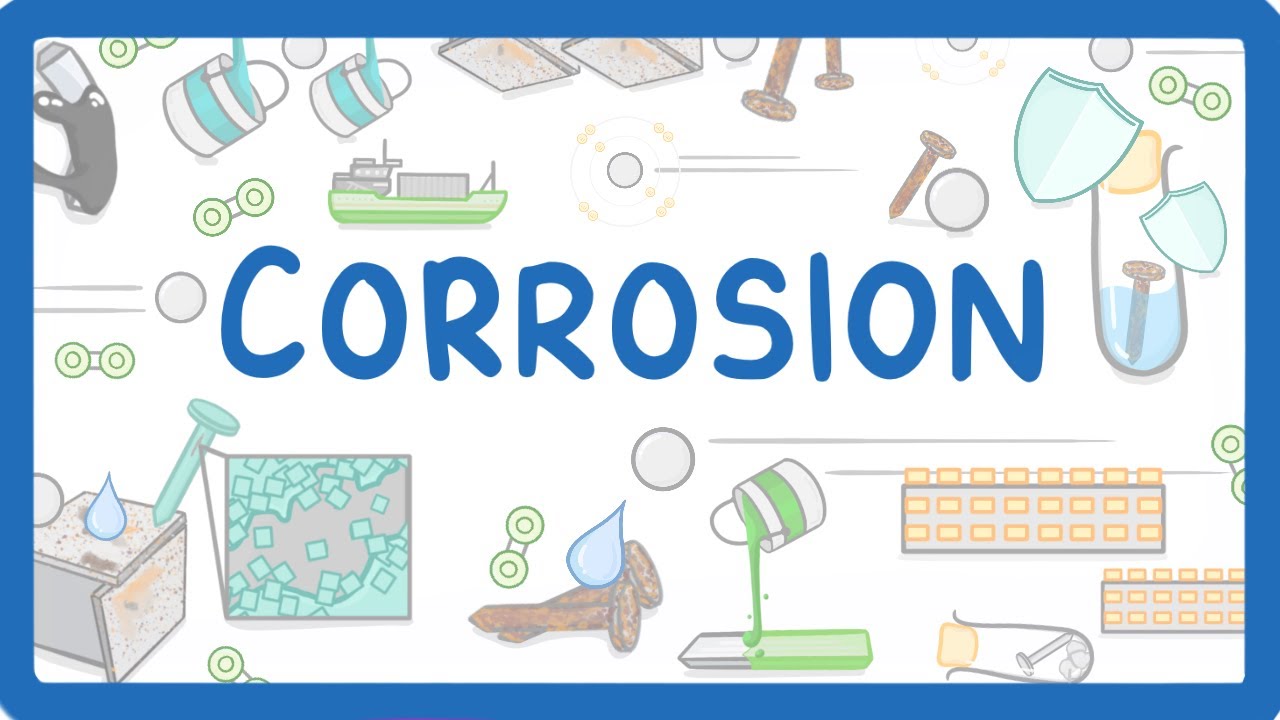
GCSE Chemistry - What is Corrosion and How to Stop it #71

PEMBUATAN LARUTAN STOK F MEDIA MS // KULTUR JARINGAN
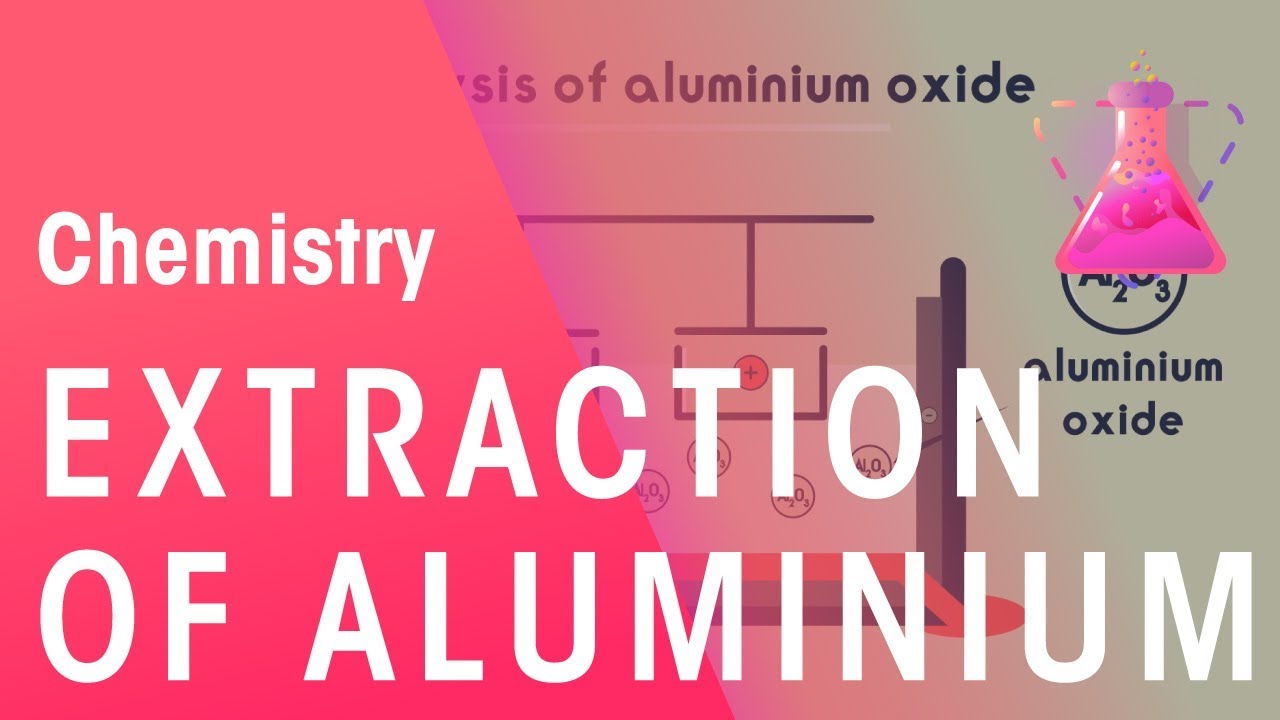
Extraction Of Aluminium Using Electrolysis | Environmental Chemistry | FuseSchool

Formulae Of Ionic Compounds & Their Names - Part 1 | Properties of Matter | Chemistry | FuseSchool
5.0 / 5 (0 votes)