What is an Encoder
Summary
TLDRIn this educational video, Henry explains the function and differences between incremental and absolute encoders. He demonstrates how encoders, used for position feedback in rotating mechanisms, work by converting optical pulses into electronic signals. Incremental encoders send a series of pulses to a controller, which counts them to determine position, but require homing after power cycles. Absolute encoders, on the other hand, maintain position information even through power cycles due to their unique addressing system for each position. The video also touches on the applications of each type of encoder, with incremental encoders suitable for systems like conveyor belts where absolute position isn't critical, and absolute encoders ideal for precise, high-dependency machinery.
Takeaways
- 😀 Encoders are used for position feedback in rotary mechanisms.
- 🔍 They can be connected to a rotating shaft to determine the position of an object.
- 🔧 Encoders have a mechanical disc inside that rotates with the shaft, which is read by an optical system to generate electrical signals.
- 💡 Incremental encoders send a series of pulses that a controller counts to determine position, but require homing after power cycles.
- 🔄 Incremental encoders can detect direction (forward or reverse) and adjust the pulse count accordingly.
- 📊 Absolute encoders have a unique address for each position, allowing them to retain position information through power cycles without homing.
- 🔗 Encoders can communicate with controllers via various methods, including specialized proprietary communications or standard Ethernet IP.
- 🏭 The choice between incremental and absolute encoders depends on application requirements, such as the need for precise positioning and whether homing is acceptable.
- 🔩 Encoders are used in various environments, from precise machinery with multiple servos to simpler applications like conveyor belts.
- 📈 The video provides practical examples, such as using an encoder on a conveyor belt to track position for robotic picking.
Q & A
What is an encoder?
-An encoder is a device used for position feedback, typically connected to a rotating shaft to provide information about the position of a rotary mechanism.
How does an encoder work?
-Encoders work by having a mechanical disc inside that is attached to the rotary mechanism. As the disc spins, it has etchings that interact with a reader on the circuitry, converting optical pulses into electronic signals that can be sent to a controller.
What is the difference between a hollow shaft encoder and a solid output shaft encoder?
-A hollow shaft encoder has a center hole where a shaft can be inserted and coupled, while a solid output shaft encoder has a continuous solid shaft. Both types have the same operating principle but differ in how they connect to the rotary mechanism.
What is an incremental encoder?
-An incremental encoder is a type of encoder that sends a series of pulses to a controller, which counts these pulses to determine the position. It does not retain position information through a power cycle and requires homing to reset the count.
What does PPR stand for in encoder terminology?
-PPR stands for Pulses Per Revolution, which indicates the number of pulses an encoder sends per complete rotation of the shaft.
How does an absolute encoder differ from an incremental encoder?
-An absolute encoder retains its position information even through a power cycle, as it has a unique address for each position on its disc. It does not require homing like an incremental encoder.
What is homing in the context of encoders?
-Homing is the process of resetting the position count to a known starting point when the system is powered on, necessary for incremental encoders because they lose position information during a power cycle.
Why would someone choose an incremental encoder over an absolute encoder?
-An incremental encoder might be chosen for applications where the cost is a factor and the system can afford to spend time homing after a power cycle, such as in a conveyor belt system where absolute position information is not critical.
What is the advantage of using an absolute encoder in a system with multiple servo motors?
-In a system with multiple servo motors that need to maintain specific alignments and positions, an absolute encoder is advantageous because it can retain position information through power cycles, avoiding the time-consuming process of homing all motors.
What is the purpose of the etchings on the encoder disc?
-The etchings on the encoder disc are used to modulate light as the disc spins, creating a pattern of light and dark that the reader on the encoder's circuitry can interpret as electrical signals representing position.
How does the communication technology differ between an incremental encoder and an absolute encoder?
-Incremental encoders typically have more wires due to the need to send multiple pulse signals for position and direction, while absolute encoders may have fewer wires because they send a unique position signal that represents the absolute position on the disc.
Outlines
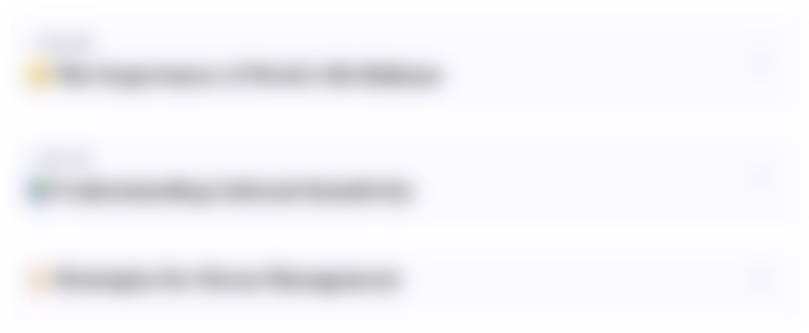
Этот раздел доступен только подписчикам платных тарифов. Пожалуйста, перейдите на платный тариф для доступа.
Перейти на платный тарифMindmap
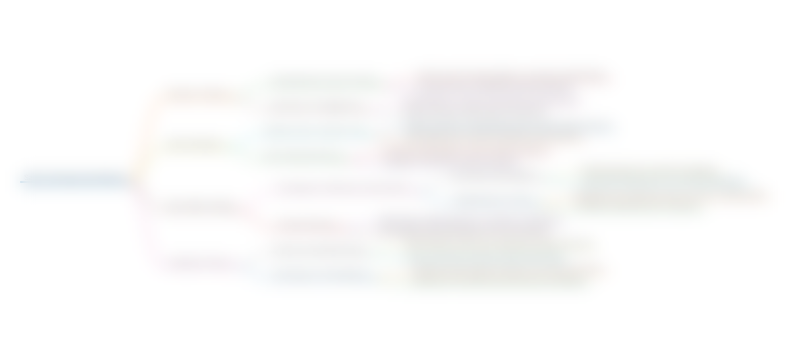
Этот раздел доступен только подписчикам платных тарифов. Пожалуйста, перейдите на платный тариф для доступа.
Перейти на платный тарифKeywords
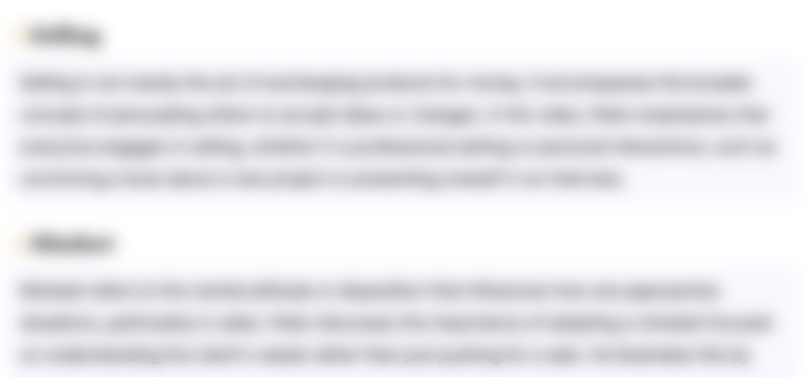
Этот раздел доступен только подписчикам платных тарифов. Пожалуйста, перейдите на платный тариф для доступа.
Перейти на платный тарифHighlights
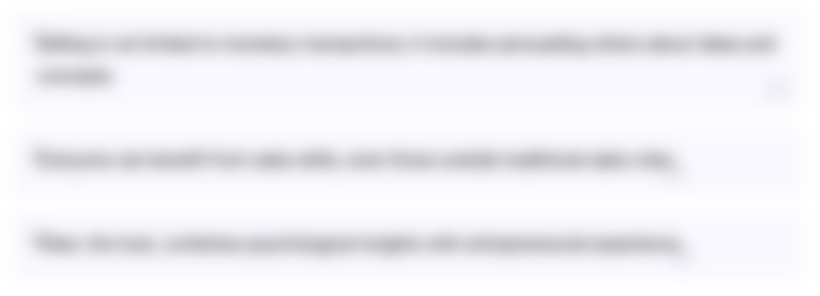
Этот раздел доступен только подписчикам платных тарифов. Пожалуйста, перейдите на платный тариф для доступа.
Перейти на платный тарифTranscripts
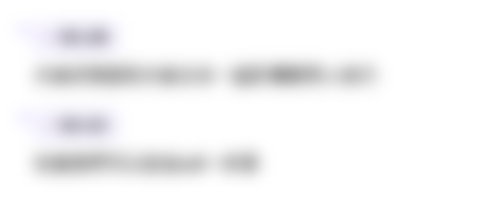
Этот раздел доступен только подписчикам платных тарифов. Пожалуйста, перейдите на платный тариф для доступа.
Перейти на платный тариф5.0 / 5 (0 votes)