Construction & System Operation - Aircraft Brakes - Airframes & Aircraft Systems #22
Summary
TLDRThe video script delves into the intricacies of aircraft wheel brakes, highlighting the challenge of heat dissipation due to the immense energy conversion during braking. It outlines the evolution from simple to complex hydraulic systems, the shift from steel to carbon in brake manufacturing for better heat management, and the importance of monitoring brake lining material to prevent brake fade and potential fires. The script also discusses the role of technological advancements in enhancing brake efficiency and the mechanisms of automatic brake wear adjusters.
Takeaways
- ✈️ Aircraft wheel brakes function by converting kinetic energy into heat through friction between a fixed and a moving surface.
- 🔥 The amount of heat generated when stopping large modern aircraft is enormous, presenting a significant challenge for heat dissipation.
- 🛫 Technological advancements like reverse pitch on propeller-driven aircraft and reverse thrust on jet engines, along with ground spoilers, help reduce the workload on brakes.
- 🔧 Aircraft now use plate or disc brakes operated by hydraulic systems, similar to those in cars but adapted for the unique demands of aviation.
- 🚗 Light aircraft use a braking system very similar to cars, with fixed friction pads gripping a rotating metal disc.
- 💡 The hydraulic system in larger aircraft is controlled by metering valves connected to the pilot's foot pedals, with primary and alternate hydraulic sources for redundancy.
- 🔩 Large aircraft increase braking surface area with multiple brake plates (rotors) and friction material layers (stators), improving braking ability and reducing temperatures.
- 🔄 Recent designs have segmented brake discs to improve heat dissipation, enhancing brake efficiency.
- 🏎️ Carbon is increasingly used in brake manufacturing due to its superior heat absorption and dissipation properties compared to steel, allowing for higher and longer-lasting braking performance.
- 🔍 Brake fade occurs when brakes overheat and lose their ability to slow the aircraft effectively, which is a critical safety concern.
- 🛠️ Automatic brake wear adjusters maintain a constant running clearance, compensating for wear and preventing brake drag, which can lead to excessive heat and potential brake failure.
Q & A
How do aircraft wheel brakes function?
-Aircraft wheel brakes function by using friction between a fixed surface and a moving one to bring an aircraft to rest, converting kinetic energy into heat energy.
What is the challenge faced by aircraft designers regarding brakes?
-The challenge faced by aircraft designers is dissipating the enormous amount of heat generated when stopping large modern aircraft, as the braking systems have to handle increasing speeds and weights of aircraft.
How do reverse pitch on propeller-driven aircraft and reverse thrust on jet engine aircraft assist in braking?
-They help reduce the work the brakes need to do by providing additional means of slowing down the aircraft, thus reducing the load on the wheel brakes.
What type of brakes are commonly used in aircraft?
-Aircraft now use plate or disc brakes operated by hydraulic systems as their means of slowing down or stopping.
How do hydraulic systems operate in aircraft brakes?
-On larger aircraft, hydraulic pressure controlled by metering valves connected to the foot pedals is used to operate the brakes, with a primary and an alternate hydraulic source available for redundancy.
What is the purpose of brake torque rods in aircraft undercarriage?
-Brake torque rods prevent the bogie from rotating about its pivot point during braking by counteracting the torque developed during the braking process.
Why are carbon brakes preferred in modern aircraft?
-Carbon brakes are preferred due to their superior heat absorbing and dissipating properties compared to steel, which allows for higher levels of braking and quicker turnaround times.
What is brake fade and how can it affect an aircraft?
-Brake fade is a phenomenon where brakes become too hot and are unable to absorb further energy, leading to a rapid diminishment in their ability to slow down the aircraft.
How do automatic brake wear adjusters function in aircraft braking systems?
-Automatic brake wear adjusters use springs to move the pressure plate back when the brakes are released, allowing the stator and rotor assemblies to move slightly apart, compensating for brake wear and maintaining a constant running clearance.
What is brake drag and what are its potential consequences?
-Brake drag occurs when the brakes do not release fully, which can generate excessive heat and potentially lead to brake fade or even a brake fire.
How is the remaining brake lining material checked in multiple disk brake systems?
-The most popular method is by checking the amount that the retraction pin or wear indicator pin extends from the spring housing with the brakes selected on.
Outlines
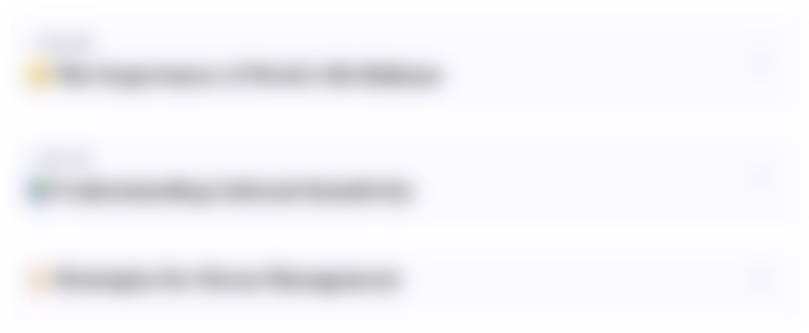
Этот раздел доступен только подписчикам платных тарифов. Пожалуйста, перейдите на платный тариф для доступа.
Перейти на платный тарифMindmap
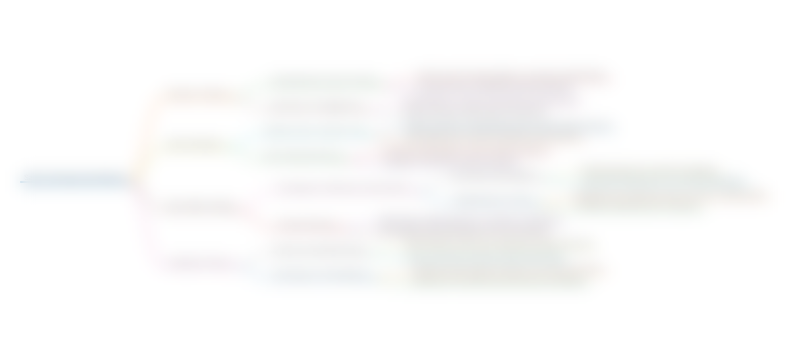
Этот раздел доступен только подписчикам платных тарифов. Пожалуйста, перейдите на платный тариф для доступа.
Перейти на платный тарифKeywords
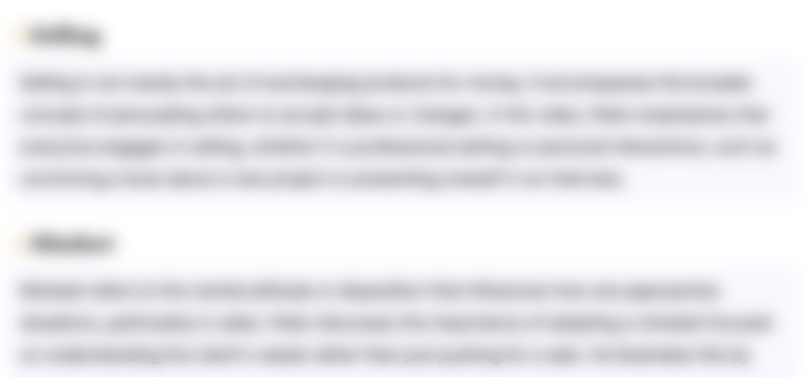
Этот раздел доступен только подписчикам платных тарифов. Пожалуйста, перейдите на платный тариф для доступа.
Перейти на платный тарифHighlights
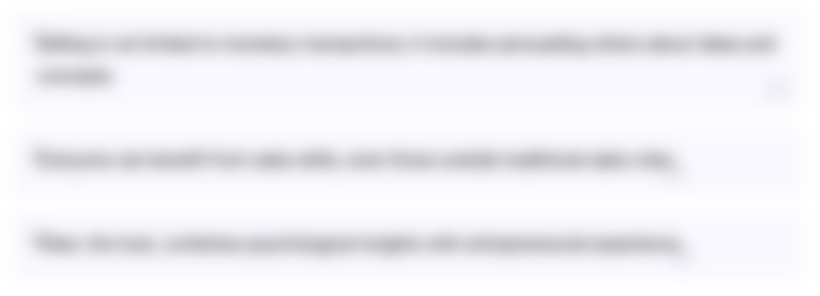
Этот раздел доступен только подписчикам платных тарифов. Пожалуйста, перейдите на платный тариф для доступа.
Перейти на платный тарифTranscripts
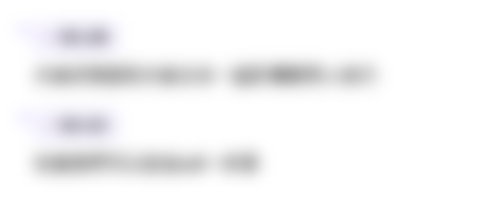
Этот раздел доступен только подписчикам платных тарифов. Пожалуйста, перейдите на платный тариф для доступа.
Перейти на платный тарифПосмотреть больше похожих видео

Components & Brake Kinetic Energy - Aircraft Brakes - Airframes & Aircraft Systems #24
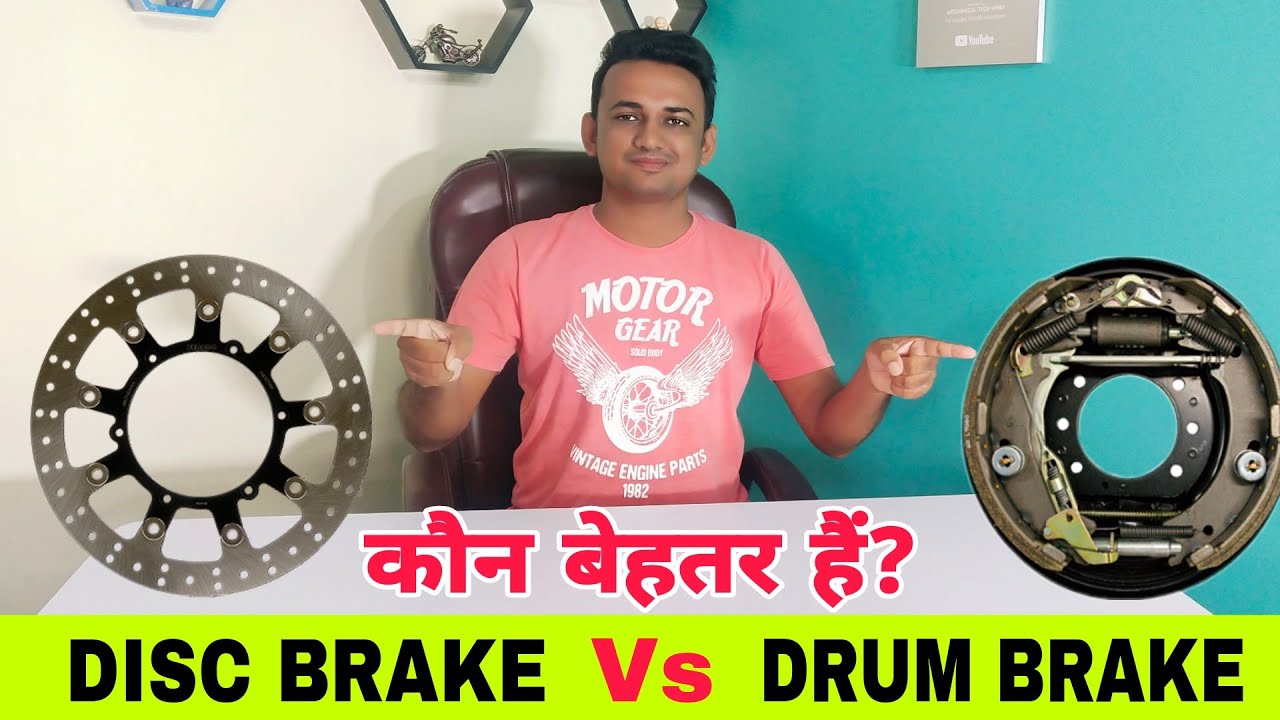
DISC BRAKE Vs DRUM BRAKE - Which Is Better? | डिस्क और ड्रम ब्रेक में कौन बेहतर हैं? | Motorcycle

Anti-Skid & Auto-Brakes - Aircraft Brakes - Airframes & Aircraft Systems #23
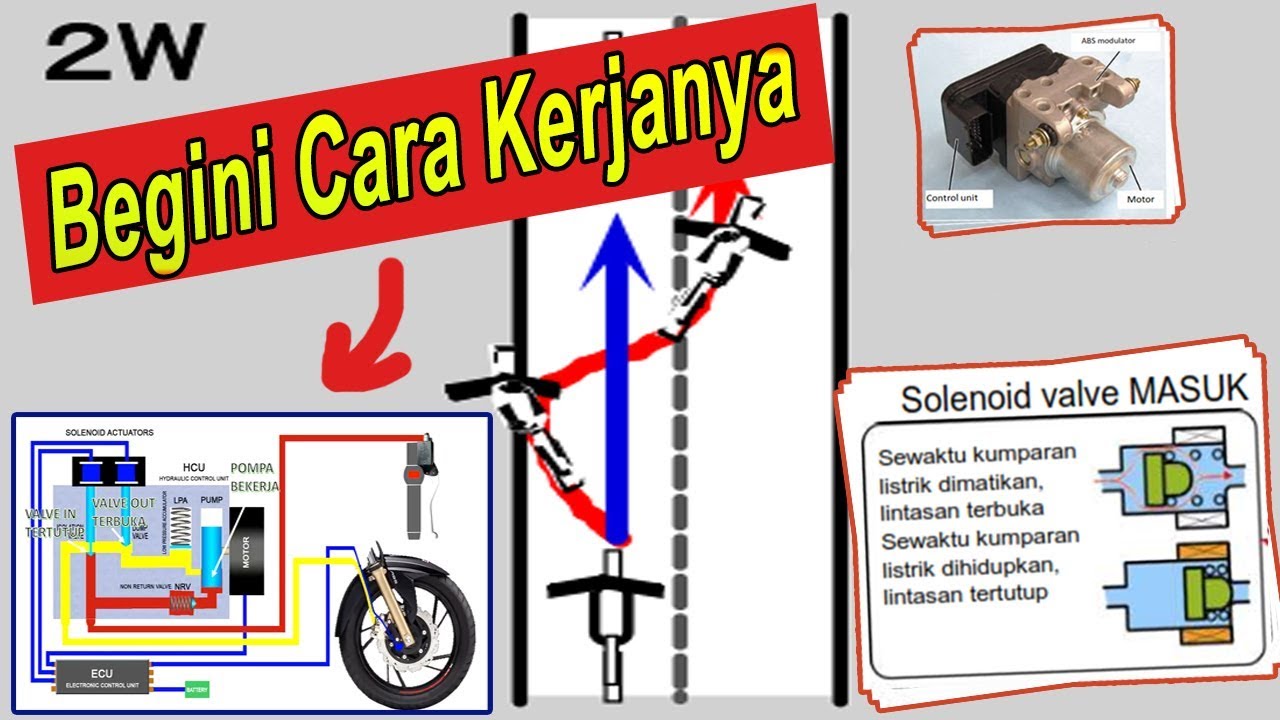
Cara Kerja Rem ABS Sepeda Motor
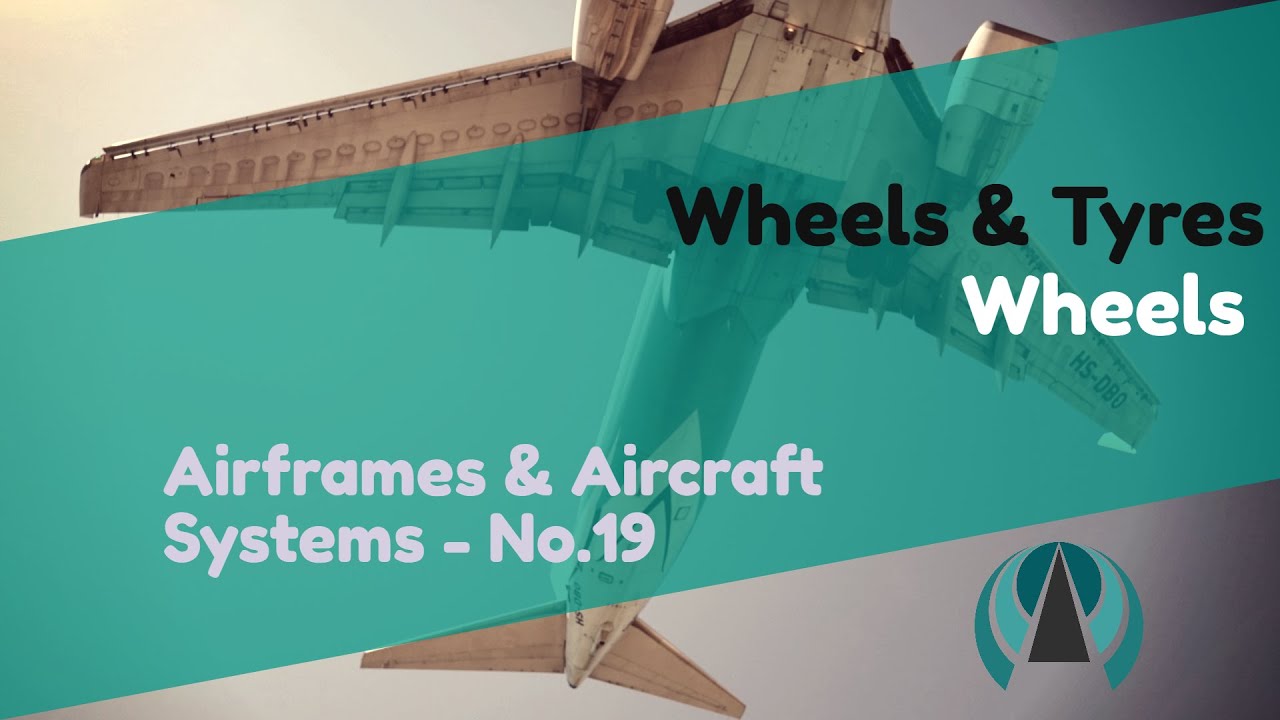
Wheels - Wheels & Tyres - Airframes & Aircraft Systems #19
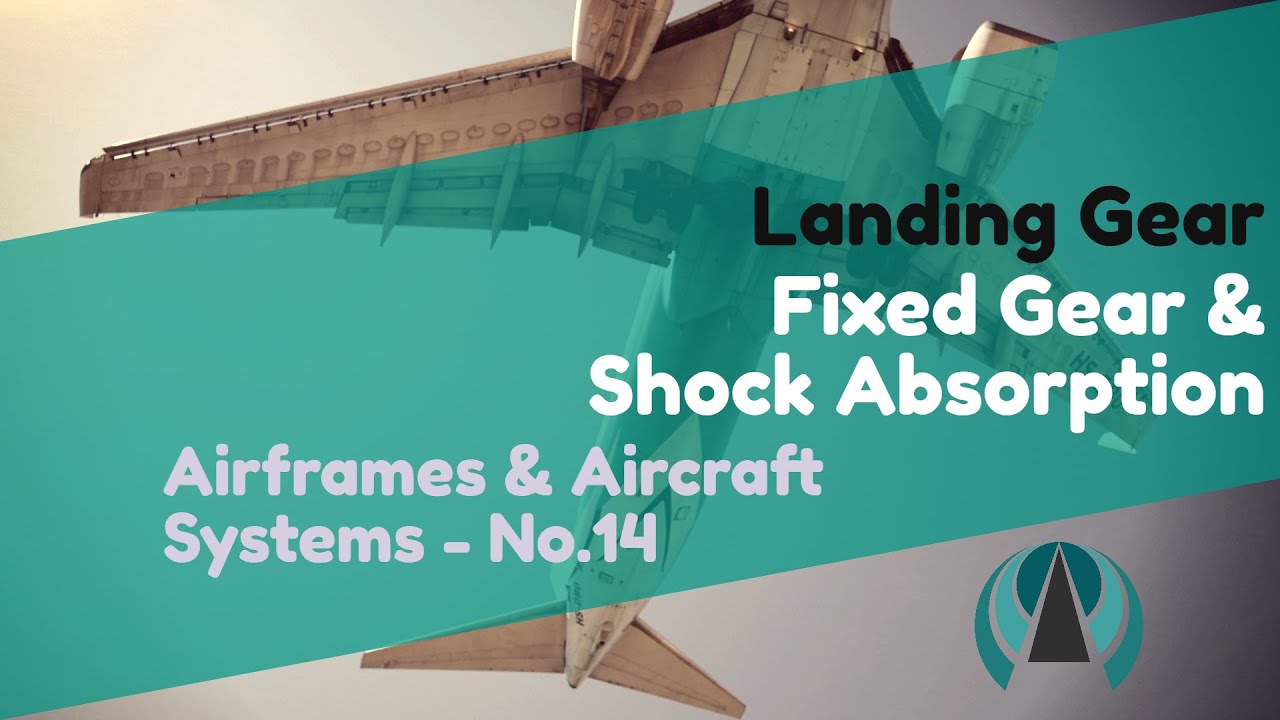
Fixed Gear & Shock Absorption - Landing Gear - Airframes & Aircraft Systems #14
5.0 / 5 (0 votes)