Precificação - Critérios de Rateio
Summary
TLDRClaudio, the director of Pactum Softwares, discusses the crucial topic of cost distribution in the management of a manufacturing industry. In this fifth video of a series, he explains how to allocate direct and indirect costs, including fixed expenses, to the selling price of each product. Using practical examples, Claudio highlights the importance of understanding how each product absorbs costs proportionally and introduces the most common allocation criteria, such as hours worked. He emphasizes the need for a fair distribution of indirect costs and fixed expenses, suggesting various criteria like weight, square meterage, or units produced, with a preference for the hours worked method. The video series aims to guide viewers on best practices for pricing strategies in business management.
Takeaways
- 😀 Claudio is the director of Pactum Softwares and the video is part of a series on an important topic in business management for the framing industry: the formation of the selling price.
- 📝 The video discusses how direct and indirect costs, as well as fixed expenses, should be distributed in the selling price of each manufactured product.
- 🔍 An example is provided to illustrate the distribution of indirect costs, emphasizing the importance of understanding cost absorption proportionally among products.
- 🕒 The most commonly used criterion for cost allocation is the 'criterion of worked hours', which considers the number of hours worked to produce a product in relation to the total number of hours worked by the factory staff.
- ⏱️ The example given calculates the indirect cost per hour as R$26 by dividing the total indirect cost of R$1800 by the total working hours of the month, which is 800 hours.
- 🚪 For a product like a door that takes one hour to manufacture, the indirect cost would be R$26, while a simpler product like a Maxim, which takes 30 minutes, would have half the indirect cost.
- 🕵️♂️ It is necessary to conduct a time study to determine the average manufacturing time for each item in the portfolio to perform this calculation accurately.
- 📐 Other criteria for cost allocation include the weight produced, square footage of the framing, or the number of units manufactured, but the hour worked is given priority.
- 💼 The video also covers the allocation of fixed expenses using the same method as for indirect costs, with the example using worked hours to calculate the cost per hour easily.
- 💼 The total fixed expenses, including administrative salaries, commercial salaries, utilities, and other costs, amount to R$1850 per month.
- 📊 The final video in the series will show how to calculate the selling price to achieve the desired profit margins, ensuring a comprehensive understanding of pricing best practices.
Q & A
What is the main topic of the video series by Claudio Cresci?
-The main topic of the video series is the management of pricing in the industry of manufacturing and selling frames, specifically focusing on how to distribute direct and indirect costs and fixed expenses in the selling price formation of each manufactured product.
What is the role of Claudio Cresci in the video?
-Claudio Cresci is the director of Pactum Softwares and the presenter of the video series, discussing important business management topics related to pricing strategies in the manufacturing industry.
What is the importance of understanding indirect costs in the pricing strategy of a manufacturing company?
-Understanding indirect costs is crucial for a manufacturing company to allocate these costs proportionally among the products manufactured and sold during the same period, ensuring a fair distribution of expenses and accurate pricing.
What is the most commonly used criterion for allocating indirect costs in the manufacturing industry according to the script?
-The most commonly used criterion for allocating indirect costs is based on the labor hours worked, considering the number of hours worked to produce a product in relation to the total number of hours worked by the factory staff.
How does the script suggest calculating the indirect cost per hour for a product?
-The script suggests dividing the total indirect cost by the total number of hours worked in a month to arrive at the indirect cost per hour, which can then be applied to individual products based on the hours they take to produce.
What is an example of how the indirect cost per hour is applied to a specific product in the script?
-In the script, if a door takes one hour to produce, it would have an indirect cost of R$26. For a simpler frame that takes 30 minutes to produce, the indirect cost would be R$13, which is half the cost of an hour.
Why is it important to perform a time study for each product in the manufacturing process?
-A time study is important to determine the average manufacturing time for each product in the portfolio, which helps in dividing the direct and indirect costs more fairly and accurately during the pricing formation.
What are some alternative criteria for allocating indirect costs other than labor hours mentioned in the script?
-Other criteria for allocating indirect costs include the average weight produced in a month, the square footage of the frames, or the number of units manufactured.
How does the script explain the distribution of fixed expenses in the pricing strategy?
-The script explains that fixed expenses should be distributed using the same method as indirect costs, such as labor hours, to find the value of fixed expenses per hour, weight, or any other chosen method, ensuring a fair allocation of these costs.
What is the total amount of fixed expenses mentioned in the script for the hypothetical company?
-The total amount of fixed expenses mentioned in the script for the hypothetical company is R$53,185 per month.
What will be the focus of the final video in the series according to the script?
-The final video in the series will focus on how the pricing calculation should be performed to determine the selling price, considering the margins to be achieved and providing a comprehensive understanding of the best pricing practices.
Outlines
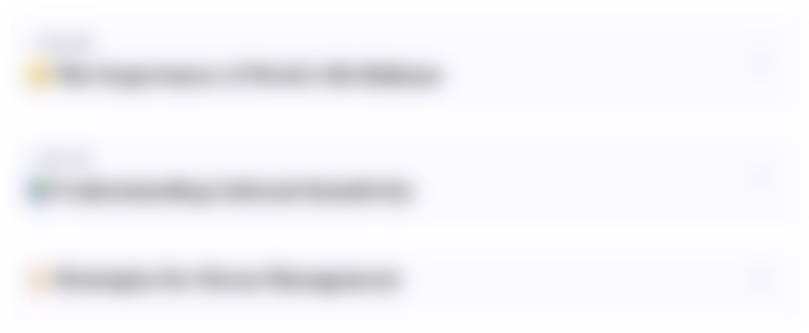
このセクションは有料ユーザー限定です。 アクセスするには、アップグレードをお願いします。
今すぐアップグレードMindmap
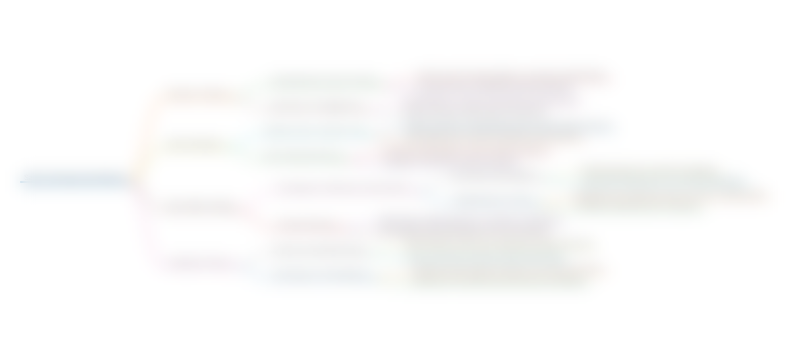
このセクションは有料ユーザー限定です。 アクセスするには、アップグレードをお願いします。
今すぐアップグレードKeywords
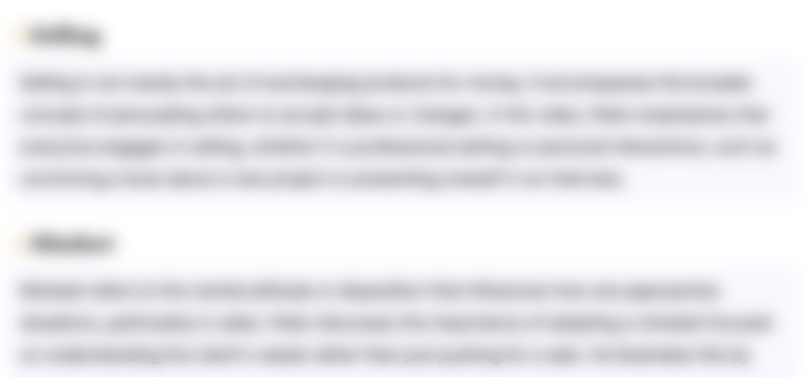
このセクションは有料ユーザー限定です。 アクセスするには、アップグレードをお願いします。
今すぐアップグレードHighlights
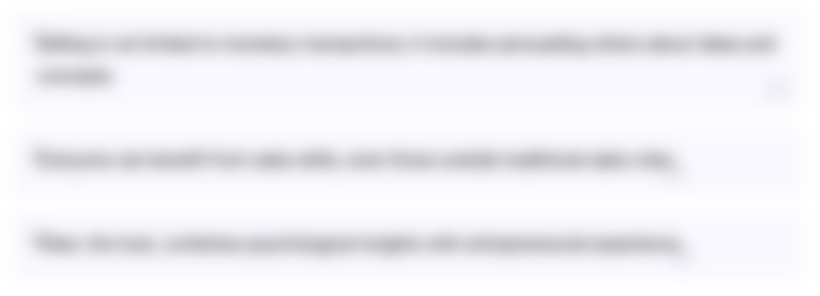
このセクションは有料ユーザー限定です。 アクセスするには、アップグレードをお願いします。
今すぐアップグレードTranscripts
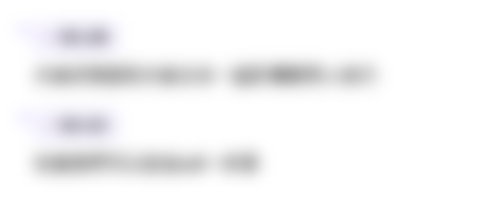
このセクションは有料ユーザー限定です。 アクセスするには、アップグレードをお願いします。
今すぐアップグレード5.0 / 5 (0 votes)