How Do Cam and Follower Mechanisms Work?
Summary
TLDRThis video delves into the mechanics of cam and roller systems, which are commonly used to convert rotary motion into linear actuation in various machines, including engines and manufacturing equipment. The cam’s non-circular shape drives linear motion, while the roller follows the cam's path. The design flexibility of cams allows for organic or fluid motion patterns, but introduces trade-offs in terms of friction and complexity. The video emphasizes the importance of precision in cam and roller design, as improper design can lead to failure due to fatigue or inefficiency. A solid understanding of dynamics, such as velocity and acceleration, is essential for successful implementation.
Takeaways
- 😀 Cam and roller mechanisms are highly effective for converting rotary motion into linear actuation, used in engines, machinery, and manufacturing.
- 😀 A cam is a rotating shaft with a unique shape that induces linear motion, with types like radial and cylindrical cams that move along one or two axes.
- 😀 The roller, or follower, is a part that tracks the cam's motion and moves in a linear fashion, following a strict field of motion.
- 😀 Translating rotational motion into linear motion is challenging, but cam and roller systems do this efficiently with minimal energy loss.
- 😀 Cam designs can be organic or flowing, allowing for fluid, precise movements that provide flexibility in mechanical design.
- 😀 Radial cams offer different levels of precision, with specialized designs enabling unique mechanisms based on a simple rotational input.
- 😀 Cam and roller mechanisms have minimal friction, leading to low energy losses and smooth operation.
- 😀 There are two main types of follower contact with cams: flat-faced and roller, each with its own pros and cons in terms of precision and maintenance.
- 😀 Flat-faced interfaces resist jamming and are simple to build but are less effective for precise, organic cam designs.
- 😀 Roller interfaces fit better into complex cam shapes but are more prone to jamming and are more complicated to design and maintain.
- 😀 A well-designed cam and roller system ensures a constant velocity and acceleration throughout the cycle, which is critical for avoiding fatigue and failure in the final mechanism.
Q & A
What is the primary function of a cam and roller mechanism?
-A cam and roller mechanism is used to transform rotary motion into linear actuation, which is widely applied in engines, repetitive machinery, and manufacturing systems.
How do radial and cylindrical cams differ in terms of motion translation?
-Radial cams translate motion along one axis, whereas cylindrical cams can translate motion along two axes, providing more complex motion control.
What role does the roller, or follower, play in the cam and roller mechanism?
-The roller, or follower, follows the cam’s motion and is typically restricted to linear movement, working in coordination with the cam to achieve the desired actuation.
Why is translating rotational motion into linear motion challenging in machine design?
-Translating rotational motion into linear motion is challenging because it requires precise control and efficiency, as this translation often involves overcoming friction and minimizing energy loss.
What are the advantages of cam and roller mechanisms over other methods of motion translation?
-Cam and roller mechanisms offer efficiency with minimal energy loss due to the small contact area, making them ideal for precise, controlled linear motion with low friction.
What types of cam shapes can be used in cam and roller mechanisms, and how does this affect performance?
-Cams can be designed with regular or organic shapes, with organic cam designs offering more fluid and precise motion, allowing for greater design freedom and better performance in certain applications.
What are the two main types of follower contact used in cam and roller mechanisms?
-The two main types of follower contact are flat-faced and roller interfaces. Flat-faced interfaces are simple and resistant to jamming, while roller interfaces allow for more precise cam fitting but are more prone to jamming and are complex to build and maintain.
How does the choice of follower contact type impact cam and roller mechanism design?
-The choice of follower contact type affects the precision, complexity, and durability of the design. A flat-faced follower is simpler but less precise for complex cams, while a roller follower offers precision but requires careful design to avoid jamming.
What are some critical physical factors to consider when designing a cam and roller mechanism?
-Key physical factors include velocity, acceleration, and jerk. Proper consideration of these elements ensures smooth and precise motion, avoiding design failures due to fatigue or inefficiency.
What could happen if the design of a cam and roller mechanism is not precise?
-If the design is not precise, the mechanism may experience early failure due to fatigue or malfunction, possibly resulting in poor performance or complete breakdown.
Outlines
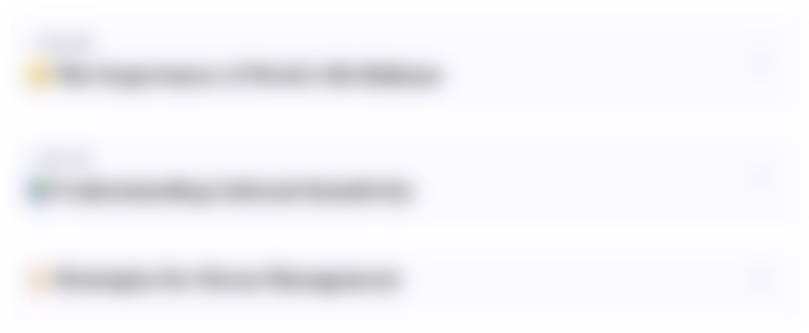
このセクションは有料ユーザー限定です。 アクセスするには、アップグレードをお願いします。
今すぐアップグレードMindmap
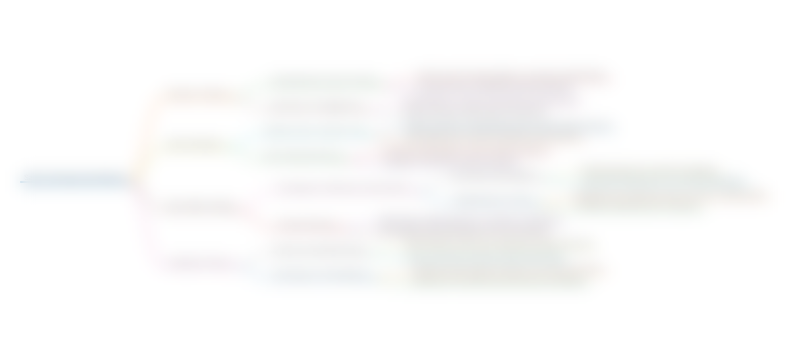
このセクションは有料ユーザー限定です。 アクセスするには、アップグレードをお願いします。
今すぐアップグレードKeywords
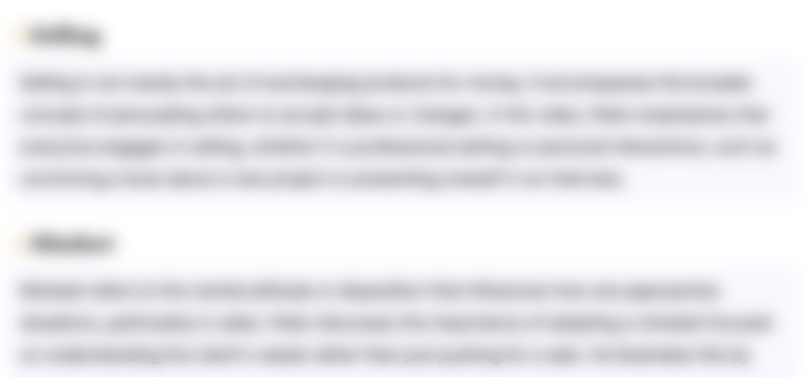
このセクションは有料ユーザー限定です。 アクセスするには、アップグレードをお願いします。
今すぐアップグレードHighlights
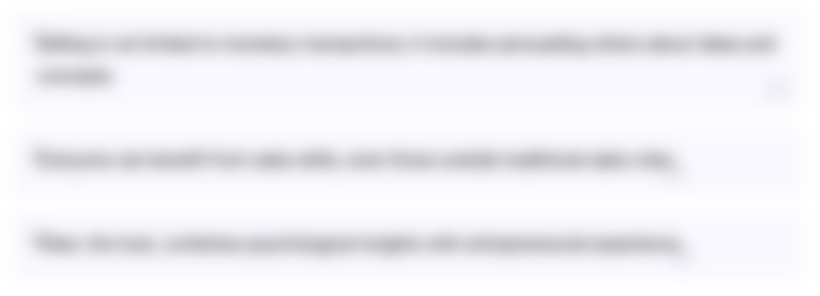
このセクションは有料ユーザー限定です。 アクセスするには、アップグレードをお願いします。
今すぐアップグレードTranscripts
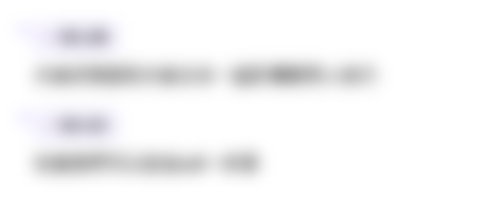
このセクションは有料ユーザー限定です。 アクセスするには、アップグレードをお願いします。
今すぐアップグレード関連動画をさらに表示
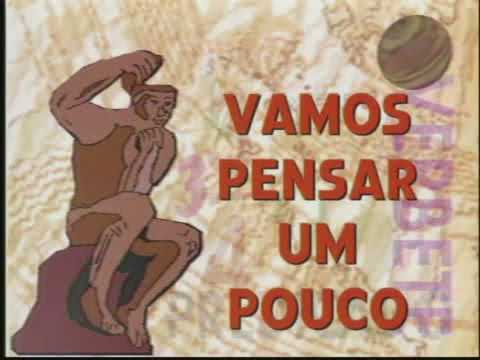
Telecurso 2000 Universo da Mecânica - 03 Transmissão e transformação de movimento

What are the different types of Actuators - Hydraulic, Rotary, and Electric Linear Actuators

Inversions of Single Slider crank Mechanism in Tamil #tom #kom #mechanism

HYDRAULIC ACTUATORS VICKERS HYDRAULIC TRAINING VEDIO BY MR PAUL COOK
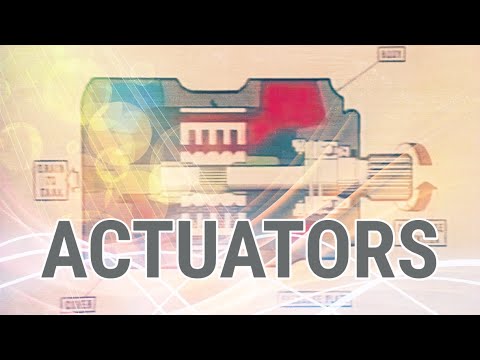
Hydraulic Training Series - Chapter 3 - Actuators
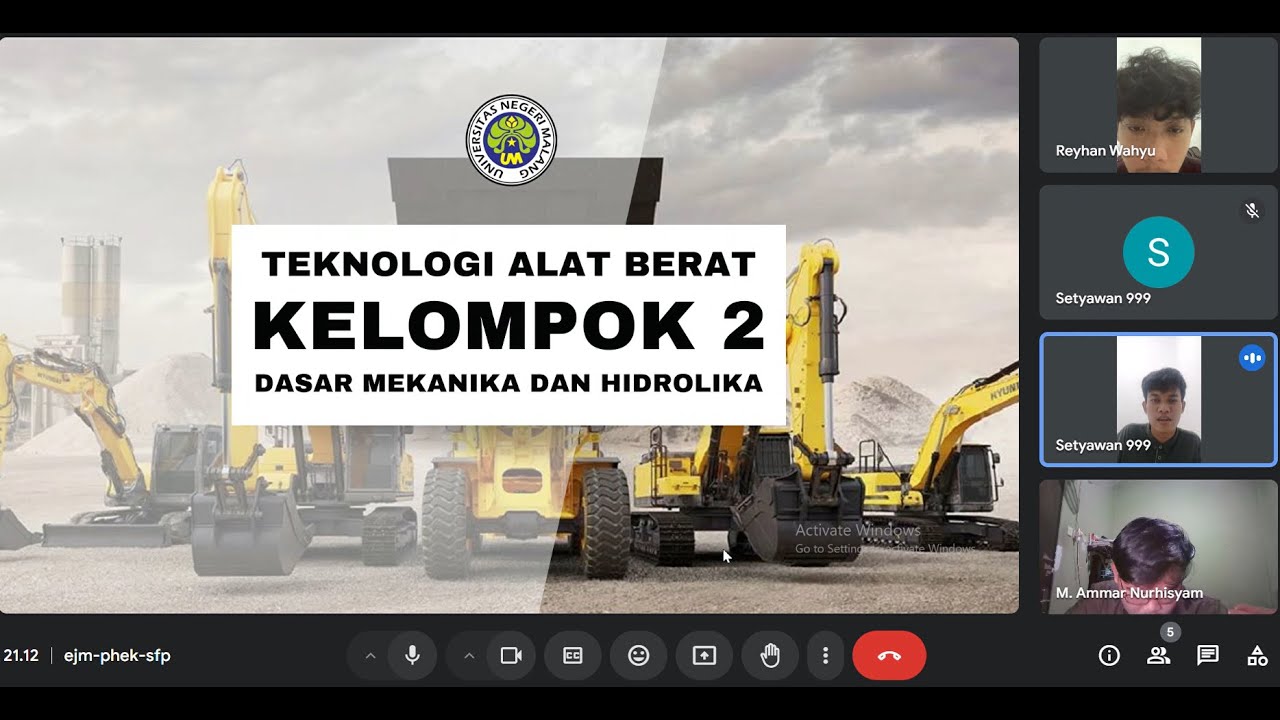
Video Presentasi Dasar Mekanika dan Hidrolika pada alat berat Kelompok 2
5.0 / 5 (0 votes)