Exemplos de Lean Manufacturing, Kaizen, 5S e inclusão social em empresas japonesas
Summary
TLDRThe video showcases the application of Kaizen, a Japanese philosophy of continuous improvement, in a factory setting. It highlights how small changes, like optimizing workflows, reorganizing materials, and enhancing accessibility for workers with disabilities, lead to increased productivity, safety, and employee satisfaction. The factory's transformation, which includes innovations such as flexible screwdrivers and automated workstations, demonstrates how Kaizen not only improves efficiency but also creates an inclusive and supportive work environment. This approach is gaining global recognition for its positive impact on both worker conditions and business outcomes.
Takeaways
- 😀 Kaizen is a Japanese philosophy focused on continuous improvement in efficiency, safety, and quality in the workplace.
- 😀 Proper organization of tools and materials is key to minimizing wasted time and improving work efficiency.
- 😀 A logical pre-positioning of materials reduces unnecessary movement and collisions, improving overall workflow.
- 😀 The Kaizen approach encourages workers to always look for ways to make their work better, even in small ways.
- 😀 An example of Kaizen in action is a sandwich factory where employees reorganized their workflows to increase productivity and reduce waiting times.
- 😀 By shifting from a linear workflow to a group-based system, the factory decreased production time and boosted efficiency.
- 😀 Kaizen's benefits extend beyond productivity to include improving accessibility for employees with disabilities.
- 😀 Workstations and tools were redesigned in the sandwich factory to accommodate workers with visual impairments and physical disabilities.
- 😀 An example of a Kaizen improvement for visually impaired workers involved organizing parts with color-coded labels and tactile markers for easy identification.
- 😀 Kaizen is not about new equipment, but rather optimizing existing systems and processes for better productivity and safety.
- 😀 Kaizen has inspired companies worldwide to adopt its principles, improving both the efficiency of their operations and the well-being of their employees.
Q & A
What is the core principle behind Kaizen in Japanese manufacturing?
-The core principle of Kaizen is continuous improvement, focusing on small, incremental changes to enhance efficiency, productivity, and safety in the workplace.
How does the organization of materials contribute to efficiency in a factory setting?
-Proper organization of materials ensures that workers do not waste time searching for tools and materials. A logical pre-positioning of items reduces movement time and minimizes the risk of collisions, improving workflow efficiency.
What changes were made in the sandwich factory to improve efficiency?
-In the sandwich factory, the process was redesigned from a linear flow to a system where small groups of workers completed batches. This change improved workflow, reduced waiting times, and increased productivity.
How does Kaizen support workers with disabilities?
-Kaizen methods have been adapted to support workers with disabilities by designing workstations and tools to be more accessible, such as using assistive devices for workers with visual impairments and redesigning workstations to minimize physical strain.
What role do flexible tools play in Kaizen practices?
-Flexible tools, like the stabilizing keychains with flexible cables, help reduce unnecessary movements, thus improving worker efficiency. This is part of Kaizen's focus on eliminating waste and optimizing task performance.
How does Kaizen improve the work environment without requiring new equipment?
-Kaizen improves the work environment by reorganizing existing tools and processes to make them more efficient. For example, adjusting workstation heights or modifying layouts helps enhance productivity and worker comfort without the need for costly new equipment.
What impact does Kaizen have on worker satisfaction?
-Kaizen positively impacts worker satisfaction by empowering employees to contribute to process improvements. Workers feel a sense of accomplishment when they can create new techniques that make their tasks easier and more efficient.
How are spare parts and materials managed in a Kaizen workplace to assist workers with visual impairments?
-In a Kaizen workplace, spare parts and materials are organized in a way that supports workers with visual impairments, such as using color-coded tapes and disks that indicate when stock is low, making it easier for these workers to navigate and handle materials.
What are the benefits of redesigning workstations in the Kaizen approach?
-Redesigning workstations in the Kaizen approach enhances productivity by improving ergonomics and reducing unnecessary physical movements. This not only makes tasks easier but also reduces fatigue, which can lead to fewer mistakes and increased overall efficiency.
How has the Kaizen approach expanded beyond Japan?
-The Kaizen approach has gained followers worldwide due to its emphasis on continuous improvement and cost-effective methods. Many global companies have adopted Kaizen principles to enhance their operations, reduce waste, and improve worker satisfaction.
Outlines
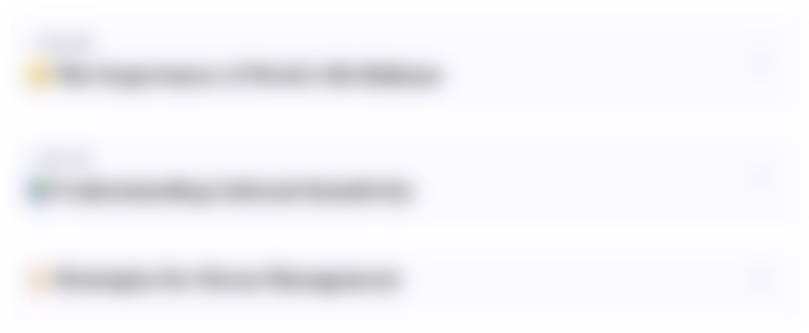
このセクションは有料ユーザー限定です。 アクセスするには、アップグレードをお願いします。
今すぐアップグレードMindmap
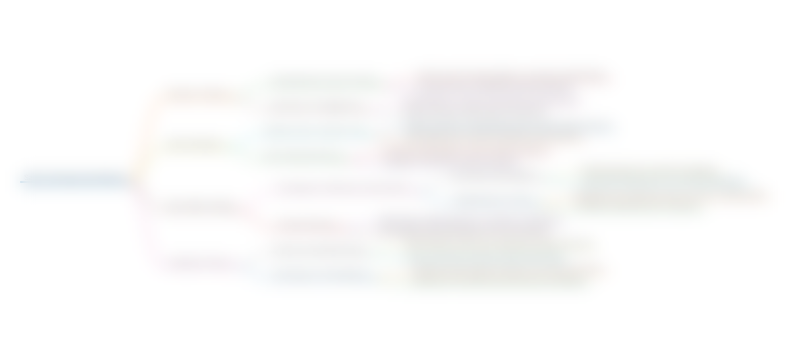
このセクションは有料ユーザー限定です。 アクセスするには、アップグレードをお願いします。
今すぐアップグレードKeywords
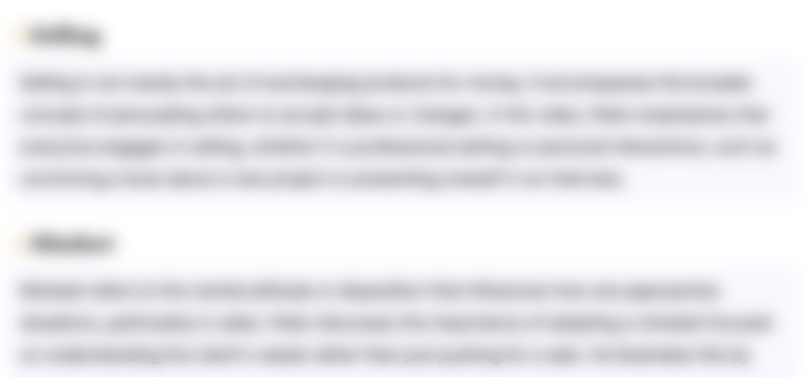
このセクションは有料ユーザー限定です。 アクセスするには、アップグレードをお願いします。
今すぐアップグレードHighlights
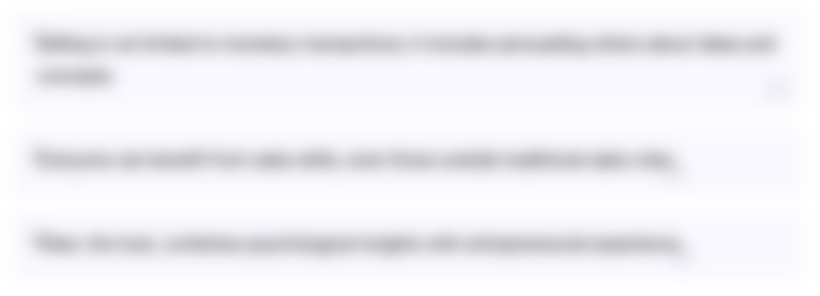
このセクションは有料ユーザー限定です。 アクセスするには、アップグレードをお願いします。
今すぐアップグレードTranscripts
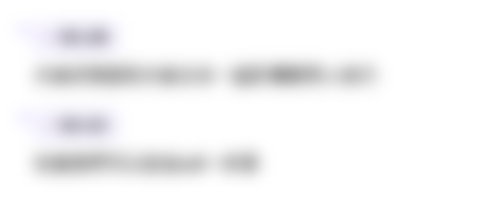
このセクションは有料ユーザー限定です。 アクセスするには、アップグレードをお願いします。
今すぐアップグレード関連動画をさらに表示
5.0 / 5 (0 votes)