How America's Largest Cast Iron Pan Factory Makes Almost Two Million Pans per Month — Dan Does
Summary
TLDRThe video takes viewers inside Lodge Cast Iron's factory in South Pittsburg, Tennessee, to explore the meticulous process behind creating their iconic cast iron cookware. From melting raw materials like pig iron and steel to molding and seasoning the pans, the video showcases the intricate craftsmanship and attention to detail involved. Through its rich history, Lodge's dedication to quality and sustainability is highlighted, as they recycle scrap metal and maintain high standards in production. The journey ends with the finished products being sent to a massive distribution center, demonstrating the immense scale and tradition behind each skillet.
Takeaways
- 😀 Cast iron pans are considered essential for cooking steaks due to their ability to create a great sear.
- 😀 Cast iron cookware has regained popularity in the U.S. over the last few decades, with Lodge Cast Iron being a leading manufacturer.
- 😀 Lodge Cast Iron, a family-owned business, has been producing cast iron cookware since the 1800s and is known for its affordability and consistency.
- 😀 The primary materials used in Lodge pans are pig iron for heat retention, steel for malleability, and scrap pans from the factory for recycling.
- 😀 Scraps and defective pans are recycled by being melted down and reused in the production process to minimize waste.
- 😀 The molten metal used for casting pans reaches temperatures of 2,800°F and undergoes two rounds of impurity removal (slagging).
- 😀 Sand molds, which are resistant to the molten metal's high temperature, are used to shape the pans. Sand is continuously recycled and remolded.
- 😀 Lodge uses a special type of sand mixed with clay and water to make molds. The sand is soft but becomes dense and hard when shaped into molds.
- 😀 Once the sand molds are created, molten metal is poured into them to form the cast iron pans, which cool and solidify into shape.
- 😀 After casting, pans are cleaned using a shot-blasting method to remove excess sand and debris, preparing them for further processing.
- 😀 Pans are then washed in an aggressive bath of soap, water, and steel beads before going through a seasoning process, which coats them with oil for better cooking performance.
- 😀 The seasoning process uses soybean oil, and the pans are heated in an oven for about 15 minutes to create a protective coating.
- 😀 Quality control involves inspecting pans for defects before they are packaged for sale. Rejects are returned to the melting process for reuse.
- 😀 Lodge Cast Iron has an extensive distribution center, shipping products directly to consumers and handling large volumes of orders.
- 😀 The legacy and dedication of past and present workers at Lodge have been crucial in the company's success, with many employees contributing to its growth over the years.
Q & A
What materials are used in the production of Lodge Cast Iron pans?
-Lodge Cast Iron pans are made from three key components: pig iron for heat retention, steel for malleability, and scraps or reject pans from the factory to minimize waste.
How does Lodge ensure that no materials go to waste during production?
-Lodge ensures that no materials go to waste by remelting defective pans and scrap metal, sending them back into the production process to be reused in future products.
Why is sand used in the molding process of Lodge Cast Iron pans?
-Sand is used in the molding process because it can withstand the high temperatures (up to 2,500 degrees Fahrenheit) required for casting molten iron. Sand also doesn't melt at these temperatures, allowing it to be reused multiple times.
How does the molding machine at Lodge Cast Iron work?
-The molding machine at Lodge uses two tools, a ram and a swing, to blow and squeeze sand into molds. These molds form the shape of the pans by creating impressions that are then filled with molten metal.
What happens to the sand after it is used for molding?
-After the sand is used for molding, it is constantly remolded and replenished with new sand. The used sand is cleaned, and the mixture of clay and water in it is maintained to ensure it remains effective for future molds.
How does the seasoning process work at Lodge?
-Lodge applies soybean oil to the pans and heats them in an oven for about 15 minutes at high temperatures to season them. This process used to involve dipping pans in wax, but now the company applies the oil directly to ensure even seasoning.
Why does Lodge use a special type of sand for molding?
-Lodge uses a specially made sand, finer than traditional foundry sand, designed specifically for their castings. This sand allows for more precise molding and is better suited to the high temperatures involved in the casting process.
What is the significance of the rejects in the production process?
-Rejects are pans that don’t meet quality standards, and they are sent back to be remelted and reused. Only a small percentage of pans are rejected, and they are important for reducing waste in the production process.
How does Lodge ensure consistency in the quality of their castings?
-Lodge ensures consistency by using high-quality sand molds and by closely monitoring each stage of the production process. The molds are created with precise methods, and any defective pans are remelted for reuse.
How large is the Lodge distribution center, and what role does it play?
-Lodge’s distribution center is 212,000 square feet and is responsible for shipping out all the products made in the factory. It handles both direct-to-consumer orders and bulk shipments to retailers.
Outlines
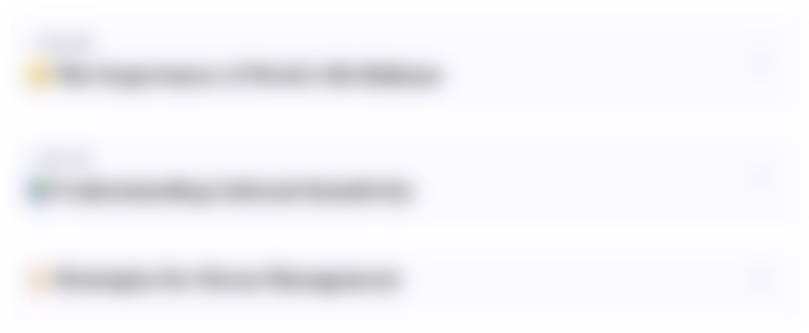
このセクションは有料ユーザー限定です。 アクセスするには、アップグレードをお願いします。
今すぐアップグレードMindmap
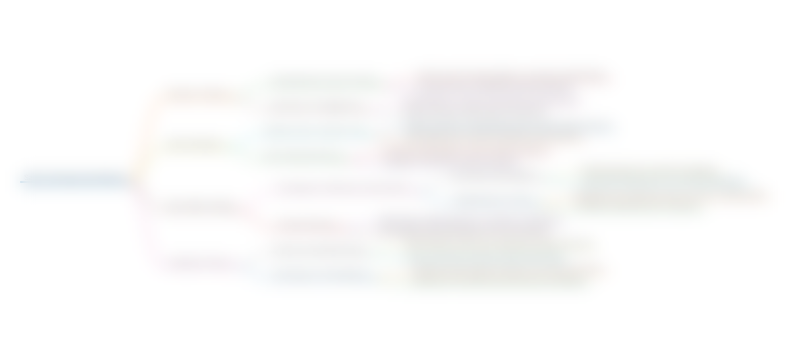
このセクションは有料ユーザー限定です。 アクセスするには、アップグレードをお願いします。
今すぐアップグレードKeywords
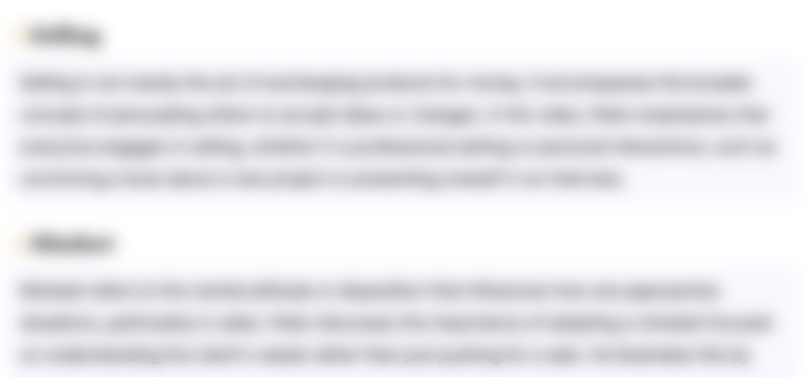
このセクションは有料ユーザー限定です。 アクセスするには、アップグレードをお願いします。
今すぐアップグレードHighlights
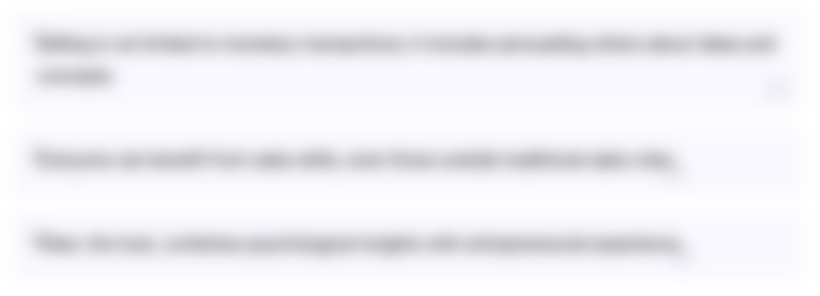
このセクションは有料ユーザー限定です。 アクセスするには、アップグレードをお願いします。
今すぐアップグレードTranscripts
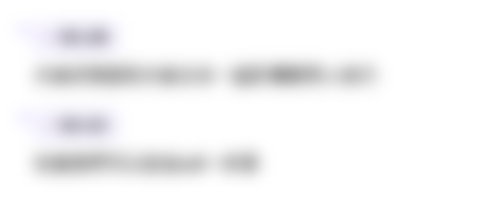
このセクションは有料ユーザー限定です。 アクセスするには、アップグレードをお願いします。
今すぐアップグレード関連動画をさらに表示

4 Tipos de Panelas Tóxicas Para Evitar e 4 Alternativas Seguras
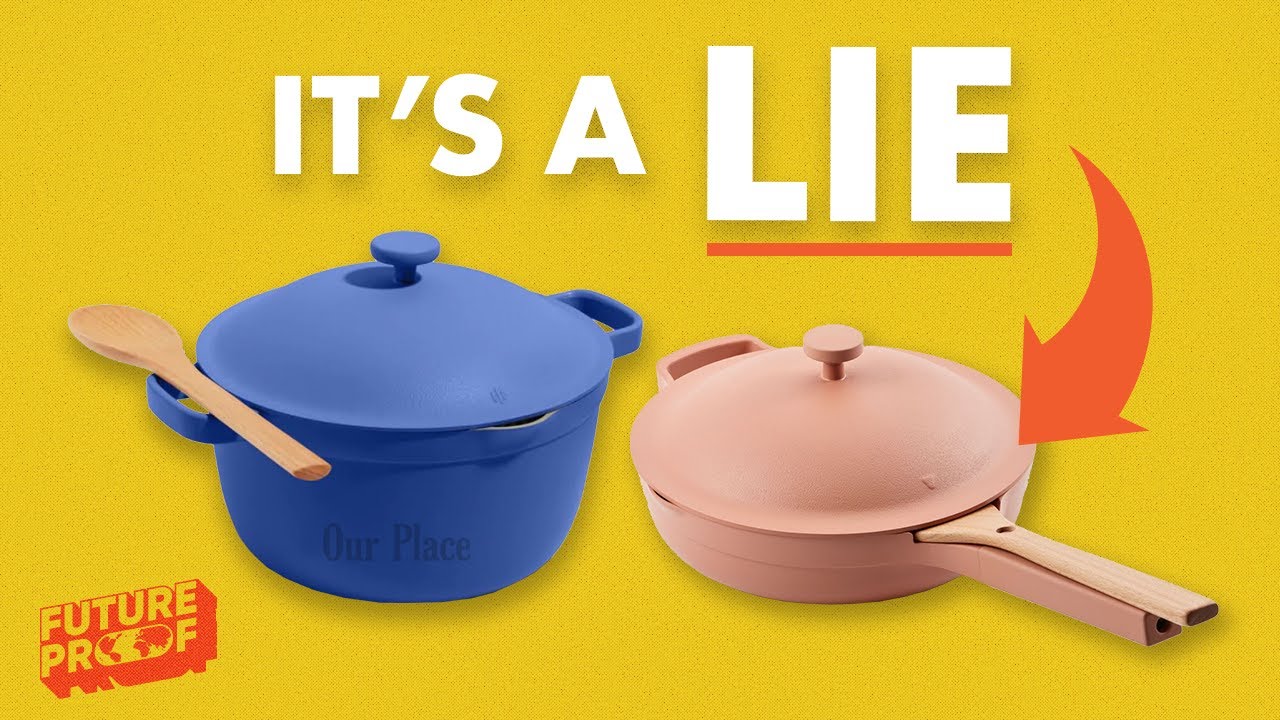
The TRUTH about Ceramic Cookware
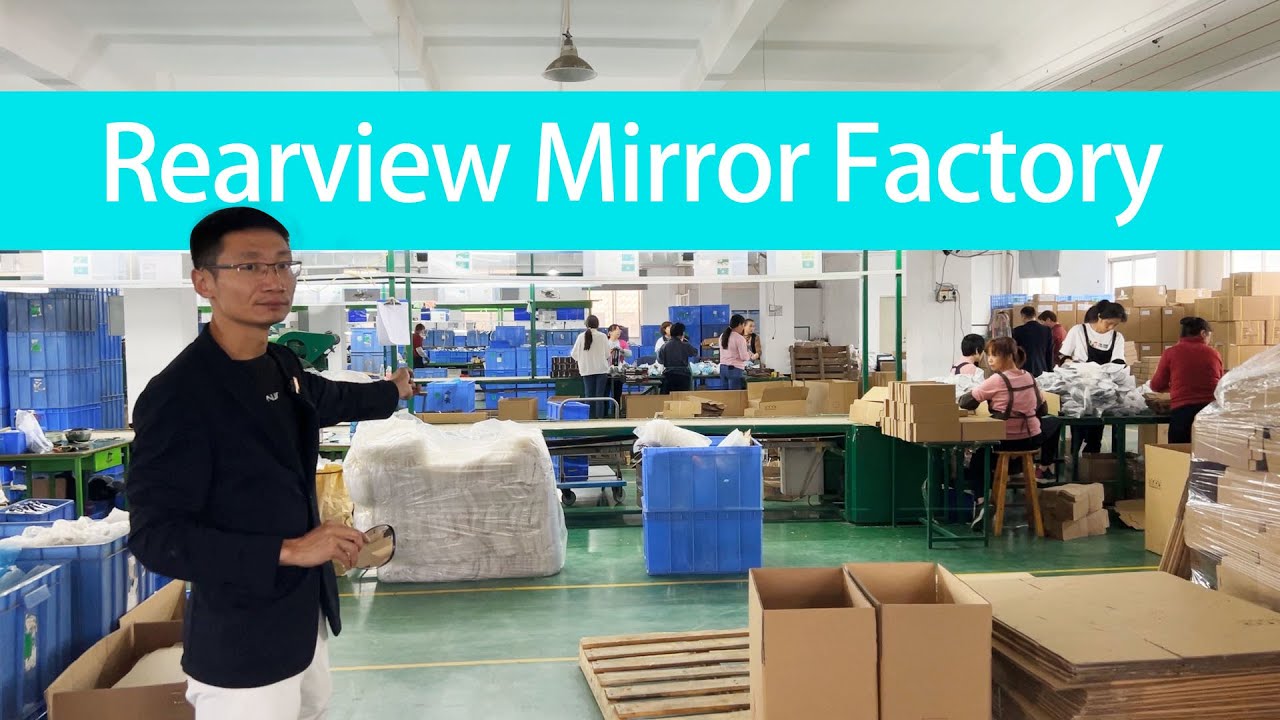
Motorcycle Rearview Mirror Factory Tour - How is Motorcycle Rearview Mirror Made?

HOW TO IMPROVE LOW IRON LEVELS (7 science-backed tips!)

How KITKAT Chocolate is Made | 7 MILLION KITKAT Chocolates EACH Day!!🍫🏭

How Chocolate is Made
5.0 / 5 (0 votes)