Kaizen y TPM Ejemplo de un Caso Exitoso
Summary
TLDREl proyecto implementado por el equipo de Fuerzas Especiales en la planta de Cormet se centró en mejorar la eficiencia operativa mediante la metodología Kaizen. Se utilizó el mantenimiento productivo total (TPM) para optimizar el rendimiento de una máquina de sellado, lo que resultó en una mejora del 93% en la efectividad global del equipo (OEE), reducción del 1% en scrap y un aumento en el tiempo medio entre fallas (MTBF). La integración de mantenimiento autónomo y predictivo, junto con la colaboración de un equipo multidisciplinario, permitió alcanzar los objetivos de reducción de costos y mejora en la calidad del trabajo.
Takeaways
- 😀 **Fuerzas Especiales** es un equipo multidisciplinario encargado de la implementación de mejoras en equipos de producción mediante la metodología Kaizen.
- 😀 **Cormet** es una empresa líder en el diseño y manufactura de equipos médicos, fundada en 1973 en Nueva York y con plantas en EE.UU. y Chihuahua, México.
- 😀 El proyecto Kaizen busca mejorar el desempeño de los equipos, reducir costos de mantenimiento y mejorar la calidad de los productos.
- 😀 El equipo sigue la metodología Kaizen en tres etapas: **Precisión, Evento Kaizen y Sostenimiento Post-Kaizen**.
- 😀 En la etapa de **Precisión**, se definen las áreas de mejora, se recogen datos y se fijan objetivos para optimizar el desempeño y la eficiencia del equipo.
- 😀 La **segunda etapa (Evento Kaizen)** incluye capacitación, observación en el sitio de trabajo, implementación de mejoras y validación de los resultados obtenidos.
- 😀 En la **tercera etapa (Sostenimiento Post-Kaizen)**, se realizan reuniones de seguimiento y se mantiene la mejora implementada a largo plazo.
- 😀 El OEE (Eficiencia Global del Equipo) y el MTBF (Tiempo Medio Entre Fallas) son métricas clave para medir el éxito del proyecto y monitorear el rendimiento del equipo.
- 😀 Las **seis grandes pérdidas** que se identifican son: averías, cambio de modelo, paros menores, pérdida de velocidad, defectos y retrabajos, y pérdidas por ajustes.
- 😀 Se implementan **mantenimiento autónomo, preventivo y predictivo**, con la participación activa de los operadores en el mantenimiento de las máquinas y la mejora de los procesos.
- 😀 Los resultados obtenidos incluyen un aumento del OEE al 93%, reducción del scrap al 1%, y una mejora en la seguridad y la eficiencia del equipo de sellado.
- 😀 La lección principal es que el trabajo en equipo multidisciplinario y la implementación de rutinas de mantenimiento estandarizadas generan mejoras sostenibles en los procesos de producción.
Q & A
¿Qué es la empresa Cormet y cuál es su especialización?
-Cormet es una corporación líder en el diseño, manufactura y distribución de equipos y dispositivos médicos, especializados en áreas como endocirugía, electrocirugía, artroscopía y cuidados del paciente. Fue fundada en 1973 en Nueva York y tiene plantas en Estados Unidos y Chihuahua, México.
¿Qué metodología utiliza el equipo de Fuerzas Especiales en sus proyectos?
-El equipo de Fuerzas Especiales utiliza la metodología Kaizen, específicamente enfocada en el mantenimiento productivo total (TPM). Esta metodología se estructura en tres etapas: precisión, evento Kaizen, y sostenimiento post-Caizen.
¿Cuáles son las tres etapas principales del proceso Kaizen aplicado por Fuerzas Especiales?
-Las tres etapas son: 1) Precisión, donde se definen los objetivos y se recogen datos; 2) Evento Kaizen, que incluye capacitación, descubrimiento, implementación, validación y celebración; 3) Sostenimiento post-Caizen, que involucra seguimiento a las acciones y mantenimiento de mejoras.
¿Qué son las 'seis grandes pérdidas' que se deben abordar en el proceso de mejora?
-Las seis grandes pérdidas son: pérdidas por averías, pérdidas por cambio de modelo, pérdidas por paros menores, pérdidas por velocidad, pérdidas por defectos y retrabajos, y pérdidas por ajuste. Estas áreas son clave para optimizar el desempeño del equipo.
¿Cuál es la diferencia entre el mantenimiento autónomo y el mantenimiento planeado?
-El mantenimiento autónomo es realizado por los operadores de la máquina, quienes se encargan de tareas de limpieza, lubricación e inspección frecuentes. El mantenimiento planeado lo realiza el personal especializado y se divide en preventivo (inspecciones periódicas) y predictivo (diagnósticos sin desmontar la máquina).
¿Cómo se lleva a cabo la fase de 'descubrimiento' durante el evento Kaizen?
-Durante la fase de descubrimiento, el equipo realiza un recorrido por el área de producción para identificar las anormalidades y recolectar datos que sirvan como base para generar acciones de mejora. También se emplean herramientas como las tarjetas azules para registrar problemas específicos.
¿Qué son las tarjetas azules y cómo se utilizan en el proceso Kaizen?
-Las tarjetas azules son una herramienta para identificar problemas y áreas de oportunidad en las máquinas. El operador registra el problema en la tarjeta, la coloca en el equipo afectado, y el equipo de mantenimiento se encarga de hacer un seguimiento y solución del problema.
¿Qué se logró en el caso exitoso descrito en el área de 'Cleaning Broches Puerto Rico'?
-En el caso exitoso, se logró reducir los paros y microporos de la máquina selladora, aumentando el OEE (Eficiencia Global del Equipo) a un 93%, reduciendo el porcentaje de scrap a solo un 1%, y mejorando la calificación de 5S a 3.6. Además, se implementaron prácticas de mantenimiento autónomo y predictivo.
¿Qué resultados se alcanzaron después de aplicar la metodología Kaizen en el área de producción?
-Después de aplicar la metodología Kaizen, se lograron importantes mejoras en la eficiencia, tales como un OEE del 93%, una reducción del scrap a un 1%, y un tiempo promedio entre fallas (MTBF) de 3.17 horas. Además, se implementó una rutina de mantenimiento autónomo y se mejoró la seguridad y la reducción de defectos.
¿Cuál fue la lección aprendida del caso implementado en la planta?
-Una lección importante fue que, al integrar un equipo multidisciplinario, se aumenta la capacidad de identificar y aprovechar oportunidades de mejora. Además, el equipo se destacó por ser los precursores de la implementación del TPM en la planta, lo que les permitió alcanzar los objetivos de mejora establecidos.
Outlines
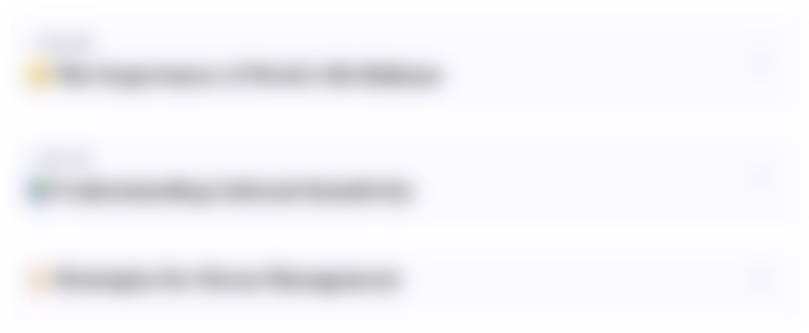
このセクションは有料ユーザー限定です。 アクセスするには、アップグレードをお願いします。
今すぐアップグレードMindmap
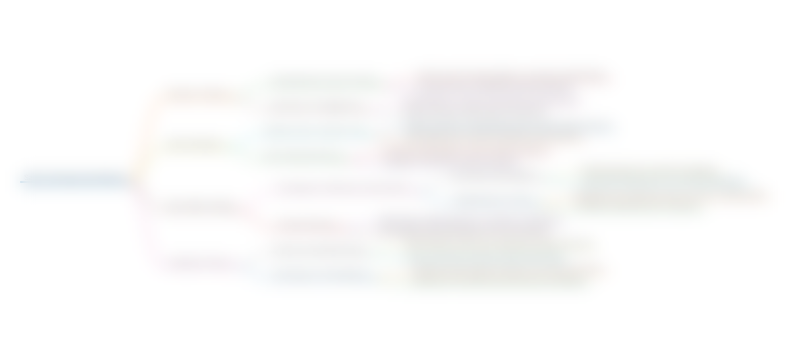
このセクションは有料ユーザー限定です。 アクセスするには、アップグレードをお願いします。
今すぐアップグレードKeywords
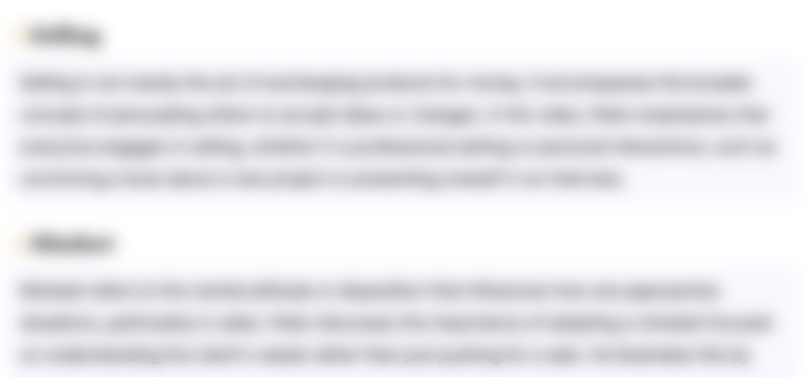
このセクションは有料ユーザー限定です。 アクセスするには、アップグレードをお願いします。
今すぐアップグレードHighlights
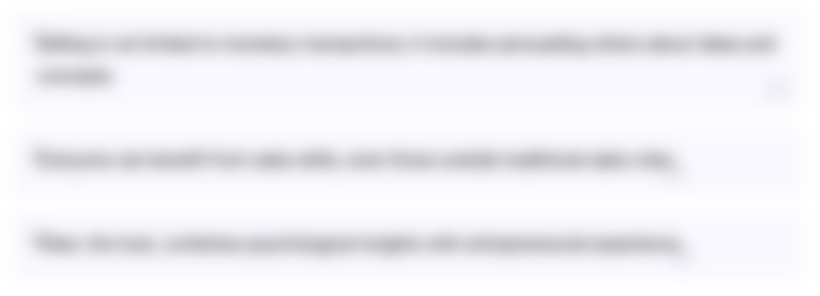
このセクションは有料ユーザー限定です。 アクセスするには、アップグレードをお願いします。
今すぐアップグレードTranscripts
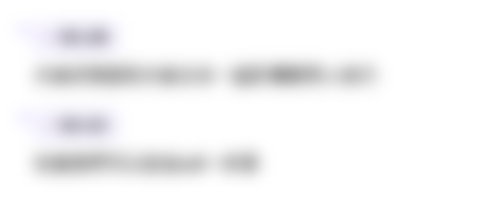
このセクションは有料ユーザー限定です。 アクセスするには、アップグレードをお願いします。
今すぐアップグレード関連動画をさらに表示

La estrategia de Alicorp para crecer más rápido
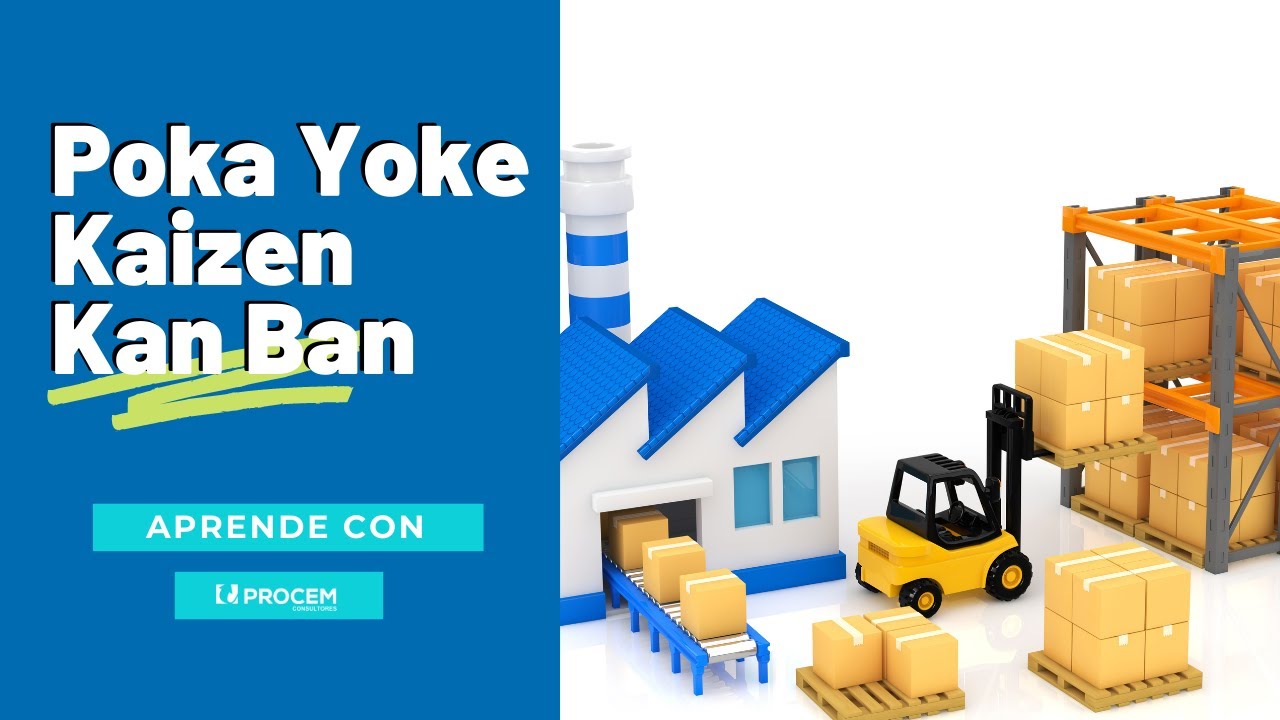
Herramientas de calidad - Poka Yoke, Kaizen y Kan Ban

Crecimiento de las plantas mediante la aplicación de cálculo integral por partes en la ing

Cómo mejorar la calidad de vida de los pacientes | Victoria Armenteros | TEDxVitoriaGasteiz

Ingeniería de planta

⚡INGENIERÍA CONCURRENTE- DEFINICIÓN Y CARACTERÍSTICAS 🏭
5.0 / 5 (0 votes)