O básico do processo de injeção de plásticos
Summary
TLDRThis video provides an in-depth look at the plastic injection molding process, explaining its history, key components, and how the technology works. The process involves feeding plastic into a machine, where it is melted, injected into a mold, and then cooled to create a solid part. Key machine components include the hopper, screw, heating zones, and cooling system. The video explores the importance of temperature control, pressure, and timing, highlighting the benefits of injection molding for mass production of complex plastic parts. It also discusses the significant role of the plastic industry in manufacturing, with a focus on the demand for skilled professionals.
Takeaways
- 😀 Injection molding is a crucial process used worldwide to manufacture plastic parts, such as casings, keyboard buttons, eyeglass frames, and many other items.
- 😀 The process involves melting plastic and injecting it into a mold cavity, where it cools and solidifies into the desired shape.
- 😀 Injection molding has evolved from basic methods to advanced systems with screw-driven machines, heaters, and precise control over material flow.
- 😀 The primary components of an injection molding machine include the injection unit, the mold clamping unit, and a heating system to ensure material melts correctly.
- 😀 The material used in injection molding can be pellets or granules, which are fed into the machine's hopper, melted, and then injected into the mold.
- 😀 Heating zones within the injection molding machine are crucial to ensure the plastic reaches the correct temperature for efficient molding.
- 😀 The molding machine works by using a rotating screw to push the molten material into the mold cavity, where it fills and takes shape.
- 😀 Cooling is a critical step in injection molding; the mold has cooling channels to remove excess heat and solidify the molded plastic efficiently.
- 😀 The injection process includes steps like 'packing' or 'recalque' to compensate for material shrinkage during cooling and ensure uniform filling of the mold.
- 😀 Injection molding is widely used in industries that require mass production of plastic parts, offering a high level of automation and precision.
- 😀 The process requires careful monitoring and adjustment of parameters such as temperature, pressure, and mold design to produce high-quality parts.
Q & A
What is injection molding, and why is it widely used?
-Injection molding is a manufacturing process where molten plastic is injected into a mold cavity to create parts. It is widely used due to its efficiency, versatility, and ability to produce precise, complex shapes for a variety of industries, including electronics, automotive, and consumer goods.
What are some everyday products made using the injection molding process?
-Everyday products made using injection molding include charger casings, keyboard buttons, eyeglass frames, and various plastic containers and parts in appliances and cars.
How does the injection molding process work?
-The process begins by feeding plastic material into a heated barrel, where it is melted. A screw or piston then injects the molten plastic into a mold. After cooling, the plastic solidifies in the shape of the mold and is ejected as a finished part.
What are the key components of an injection molding machine?
-The key components include the injection unit (for heating and injecting the material), the clamping unit (to hold the mold in place), and the cooling system (to solidify the part). The machine also includes a heating system to melt the plastic and sometimes a hydraulic or electric system for movement.
What is the difference between hydraulic, electric, and hybrid injection molding machines?
-Hydraulic machines use fluid power to operate the injection and clamping units, are widely used, and are cost-effective. Electric machines use servo motors for more precise and energy-efficient operation, offering faster cycles. Hybrid machines combine both hydraulic and electric elements for balanced performance.
What role does the plastification screw play in the injection molding process?
-The plastification screw transports the plastic material from the hopper to the mold while also melting it through friction and external heating. It ensures the plastic reaches the proper temperature and consistency before injection.
Why is temperature control crucial in injection molding?
-Temperature control is vital because it ensures that the plastic melts evenly and reaches the correct viscosity for injection. Proper temperature also helps prevent defects such as warping or incomplete filling of the mold.
What is 'packing' in injection molding, and why is it important?
-Packing is the process of adding extra material into the mold after the initial injection to compensate for material shrinkage as it cools. It ensures that the part remains filled and that there are no gaps or defects in the finished product.
What is the function of the cooling system in injection molding?
-The cooling system in the mold removes heat from the injected plastic, allowing it to solidify into the correct shape. Efficient cooling is necessary to ensure the part doesn't warp or degrade due to residual heat.
What are some common defects that can occur during the injection molding process?
-Common defects include warping, sink marks, air pockets, or incomplete filling of the mold. These issues can arise from improper temperature settings, incorrect material flow, or insufficient cooling.
Outlines
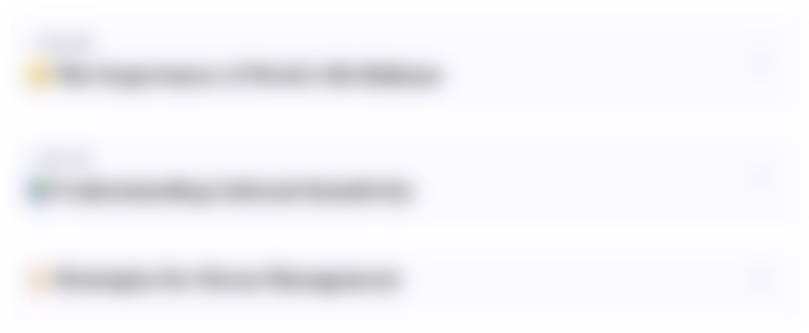
このセクションは有料ユーザー限定です。 アクセスするには、アップグレードをお願いします。
今すぐアップグレードMindmap
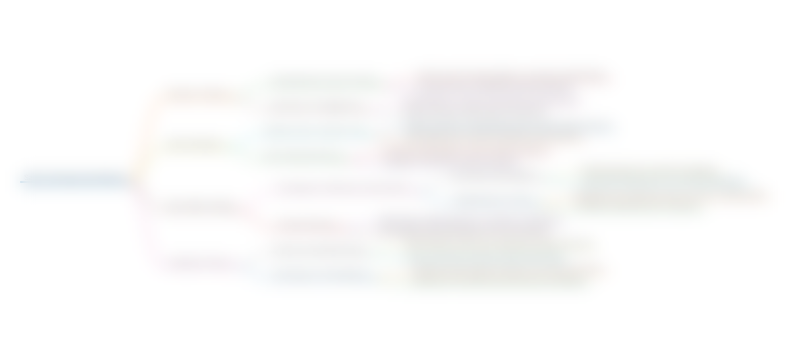
このセクションは有料ユーザー限定です。 アクセスするには、アップグレードをお願いします。
今すぐアップグレードKeywords
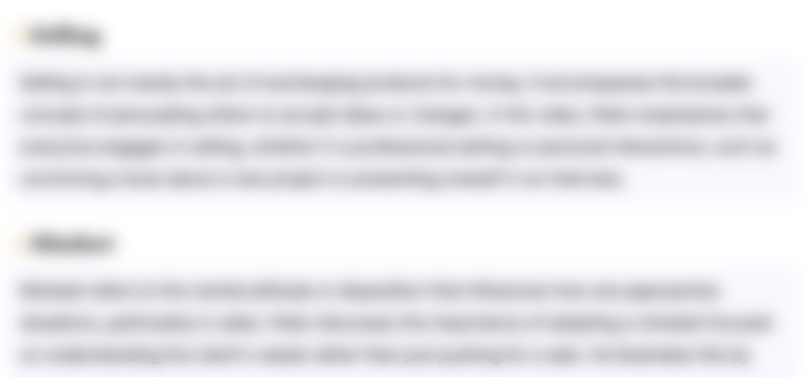
このセクションは有料ユーザー限定です。 アクセスするには、アップグレードをお願いします。
今すぐアップグレードHighlights
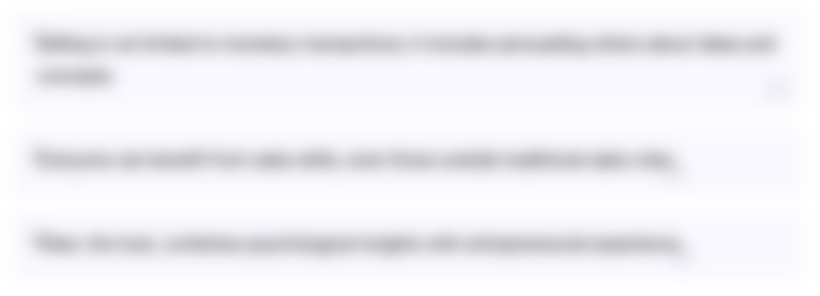
このセクションは有料ユーザー限定です。 アクセスするには、アップグレードをお願いします。
今すぐアップグレードTranscripts
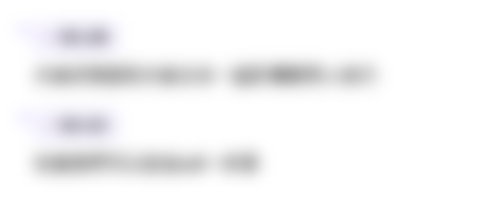
このセクションは有料ユーザー限定です。 アクセスするには、アップグレードをお願いします。
今すぐアップグレード関連動画をさらに表示
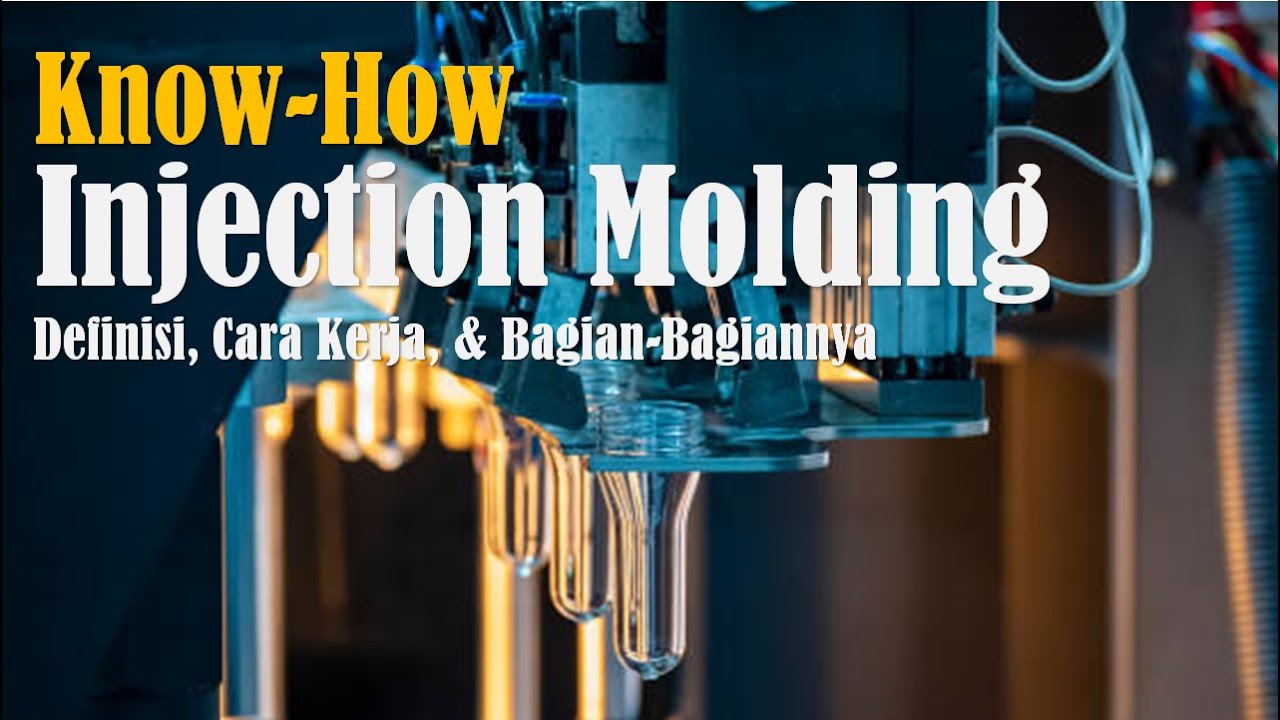
INJECTION MOLDING - DEFINISI, CARA KERJA, DAN BAGIAN-BAGIAN MESIN INJECTION MOLDING
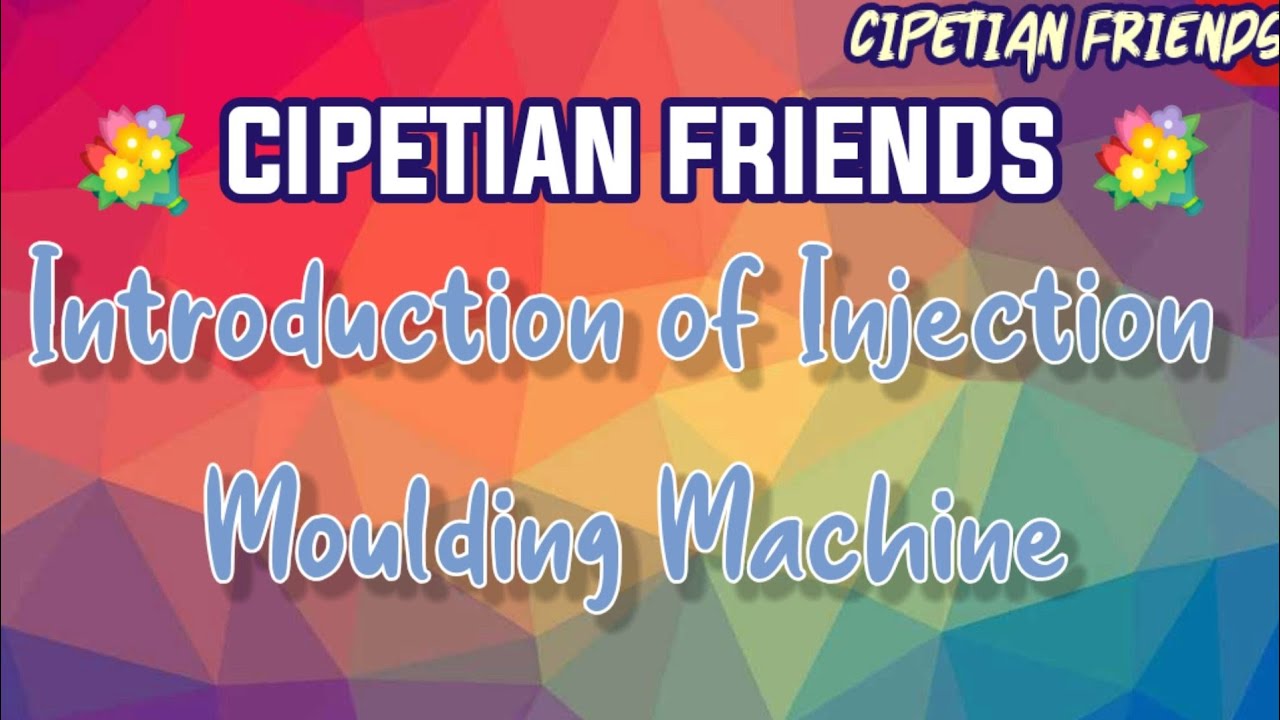
Introduction Of Injection Moulding Machine

Como funciona una inyectora de plastico

Cara Mengoperasikan Mesin Injection Molding #polibatam #LabInjectionmolding
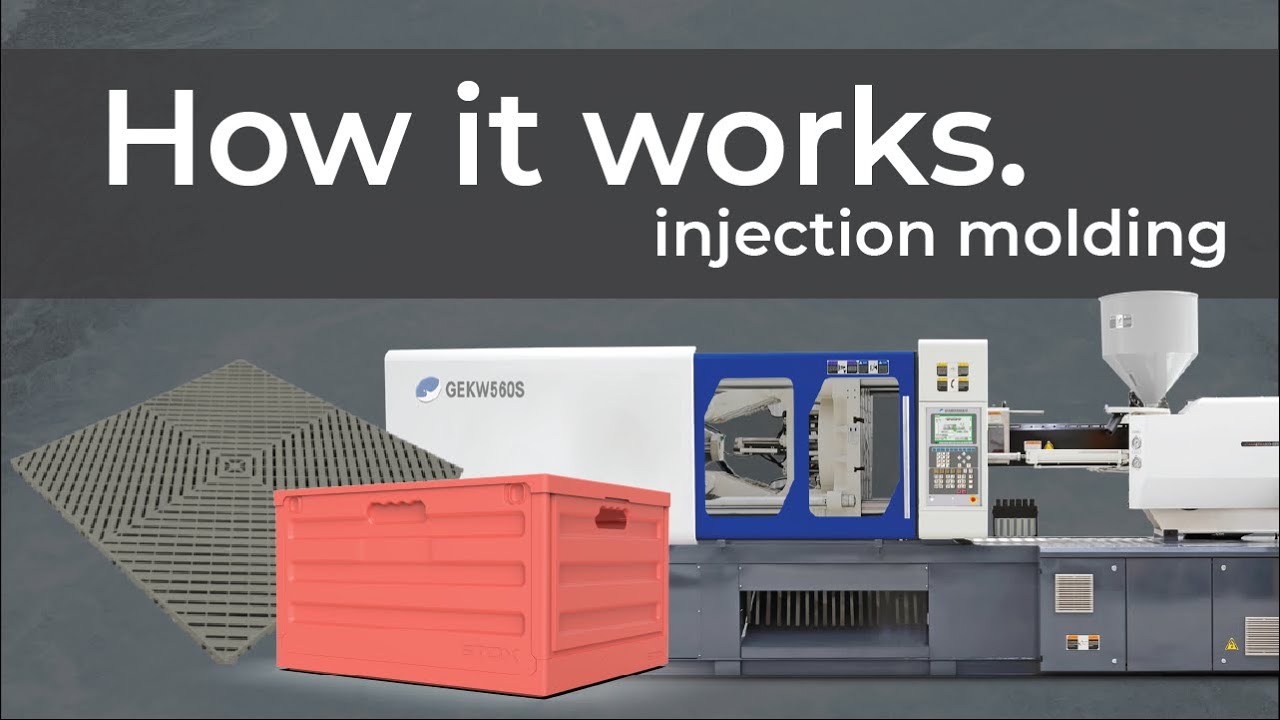
How Plastic Products are Made | The Injection Molding Process
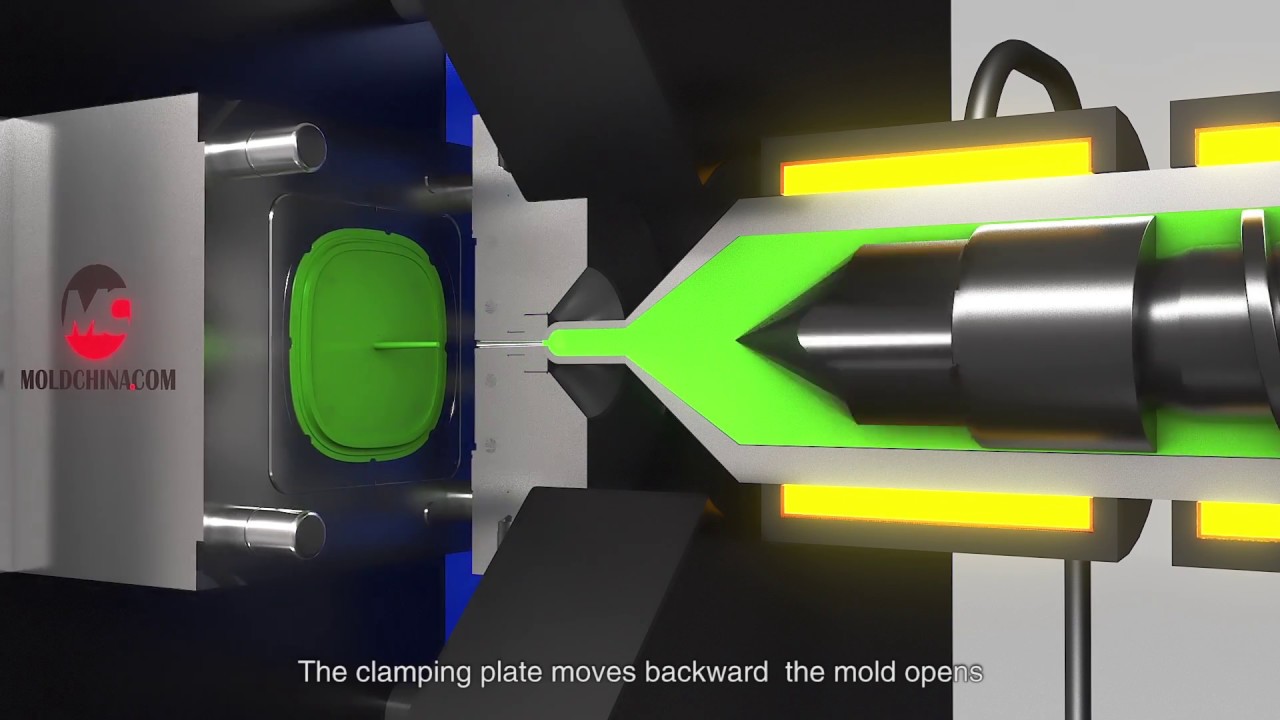
Plastic Injection Molding
5.0 / 5 (0 votes)