Toyota Rumo ao Topo 1-6
Summary
TLDRThis video showcases Toyota's innovative employee training program at their new plant in San Antonio, Texas, where local workers are trained in manufacturing using a hands-on approach with toy trucks. The program, rooted in Toyota’s principles of Kaizen (continuous improvement), helps employees with limited manufacturing experience develop efficiency through teamwork and problem-solving. As Toyota expands globally, it faces the challenge of training local, non-Japanese workers, and this program exemplifies how they integrate local communities into their manufacturing processes, ensuring both skill development and a strong connection to the Toyota culture.
Takeaways
- 😀 Toyota uses a unique hands-on training method involving toy trucks to teach new employees manufacturing basics.
- 😀 Most trainees at Toyota’s San Antonio plant have no prior manufacturing experience, highlighting the need for specialized training.
- 😀 The training method incorporates Toyota’s core principles, such as Kaizen (continuous improvement), which helps workers optimize their workflow.
- 😀 Local hiring is a key strategy for Toyota, with 55% of employees at the San Antonio plant being Hispanic Americans, a group with historically lower employment opportunities in manufacturing.
- 😀 Toyota’s plant in San Antonio, Texas, is the company’s largest in the U.S. and spans 2,000 acres, emphasizing the company’s significant investment in the region.
- 😀 Trainees are taught to identify inefficiencies and suggest improvements in the assembly line process, fostering problem-solving and team collaboration.
- 😀 The training involves a competitive element, where two teams race to build toy trucks as efficiently as possible in four minutes, promoting teamwork and speed.
- 😀 Despite early struggles, trainees learn to improve by adjusting their methods, such as organizing their parts and balancing workloads for better efficiency.
- 😀 Toyota’s training not only teaches technical skills but also aims to instill pride and satisfaction in the work, encouraging employees to take ownership of their tasks.
- 😀 Toyota’s commitment to local hiring and training is part of a broader strategy to integrate into local communities while maintaining its global standards of production.
Q & A
What is the main focus of the training session in the Toyota plant?
-The main focus of the training session is to teach new employees the basics of manufacturing using a hands-on approach. The training involves assembling toy trucks on a simulated assembly line to instill concepts like teamwork, Kaizen (continuous improvement), and efficiency.
Why does Toyota employ local workers in their San Antonio plant?
-Toyota employs local workers to integrate better with the community in San Antonio, where the population has a higher rate of unemployment and fewer educational opportunities. By hiring local workers, Toyota aims to support the region while building a strong workforce.
How does Toyota's training program incorporate the Kaizen philosophy?
-Toyota's training program emphasizes the Kaizen philosophy by encouraging trainees to identify inefficiencies in their work processes and continuously seek ways to improve. In the toy truck assembly exercise, workers were prompted to find solutions to improve the speed and accuracy of their tasks.
What specific challenges do new workers face at Toyota’s San Antonio plant?
-New workers, many of whom have no prior manufacturing experience, face challenges like learning basic manufacturing skills, understanding assembly line work, and adapting to the company’s strict quality and efficiency standards.
How does Toyota's manufacturing method differ in the US compared to Japan?
-In the US, Toyota faces unique challenges like the need to employ a workforce that is less experienced in manufacturing. To overcome this, they use local trainers and implement training programs designed to adapt their Japanese manufacturing methods to a diverse, local workforce.
What is the significance of using toy trucks in the training process?
-Toy trucks are used in the training process as a simple, hands-on tool to simulate the assembly line experience. This helps new employees understand the mechanics of the job and allows them to practice teamwork, task division, and problem-solving without the complexity of real vehicles.
How did the trainees improve their efficiency during the assembly process?
-Trainees improved their efficiency by discussing and implementing solutions like grouping the tires in sets of four to simplify the process of attaching them to the trucks. This allowed them to reduce time and avoid errors during the assembly.
What role does teamwork play in the Toyota training program?
-Teamwork is central to the training program, as workers are encouraged to collaborate, share tasks, and support each other to improve efficiency. This aligns with Toyota’s philosophy of mutual respect and collective problem-solving, essential for effective manufacturing.
What are some of the benefits of the Toyota training program for new workers?
-The training program helps new workers gain critical manufacturing skills, learn problem-solving techniques, and foster a sense of job satisfaction. Workers also experience the joy of building something tangible, which increases their engagement and motivation to continue learning.
How does Toyota address the lack of experienced trainers in international plants like Thailand?
-In places like Thailand, where there is a shortage of experienced Japanese trainers, Toyota has adopted a new approach by using non-Japanese trainers to teach local workers. This helps ensure that training continues to scale with the company’s rapid international expansion.
Outlines
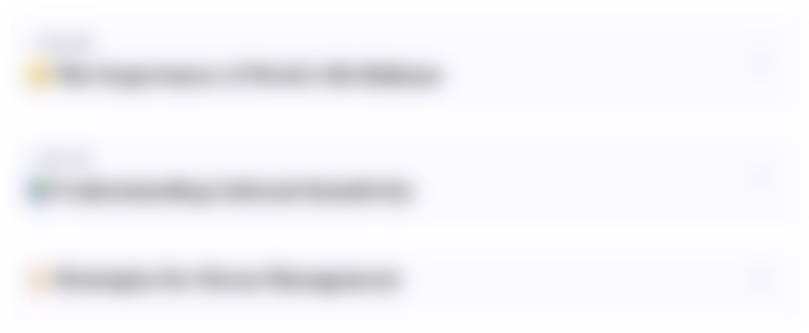
このセクションは有料ユーザー限定です。 アクセスするには、アップグレードをお願いします。
今すぐアップグレードMindmap
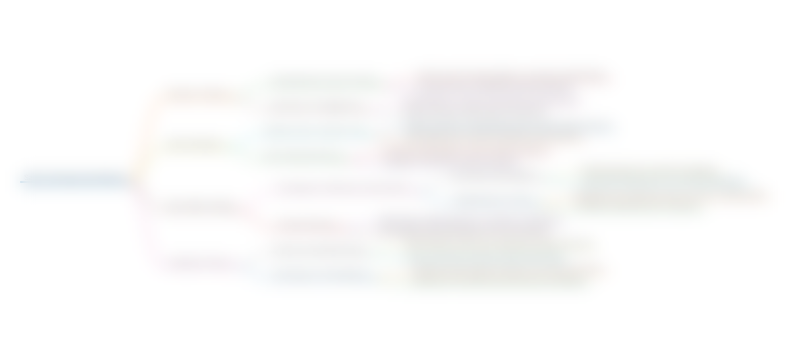
このセクションは有料ユーザー限定です。 アクセスするには、アップグレードをお願いします。
今すぐアップグレードKeywords
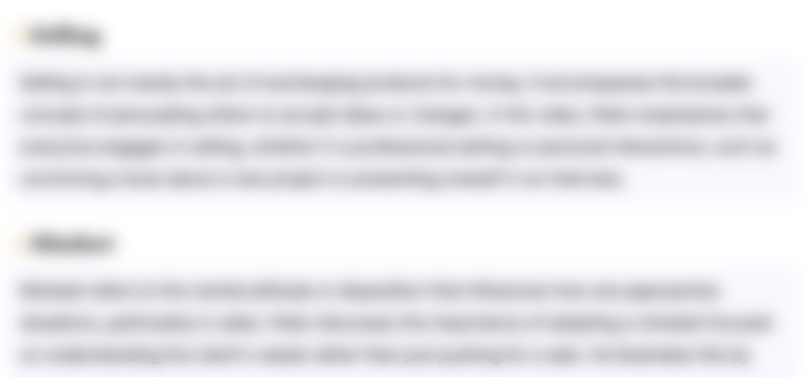
このセクションは有料ユーザー限定です。 アクセスするには、アップグレードをお願いします。
今すぐアップグレードHighlights
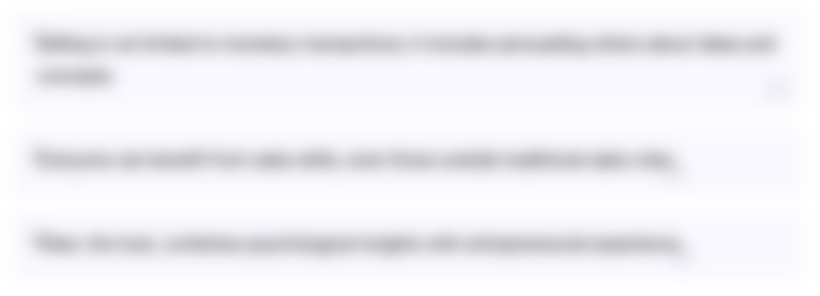
このセクションは有料ユーザー限定です。 アクセスするには、アップグレードをお願いします。
今すぐアップグレードTranscripts
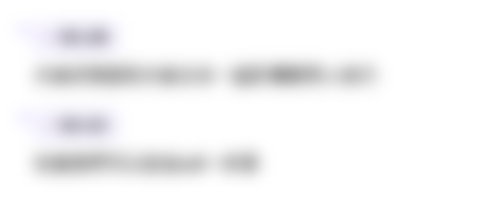
このセクションは有料ユーザー限定です。 アクセスするには、アップグレードをお願いします。
今すぐアップグレード5.0 / 5 (0 votes)